- お役立ち記事
- Optimizing Hot Runner Systems: How to Increase Efficiency in Injection Molding
Optimizing Hot Runner Systems: How to Increase Efficiency in Injection Molding
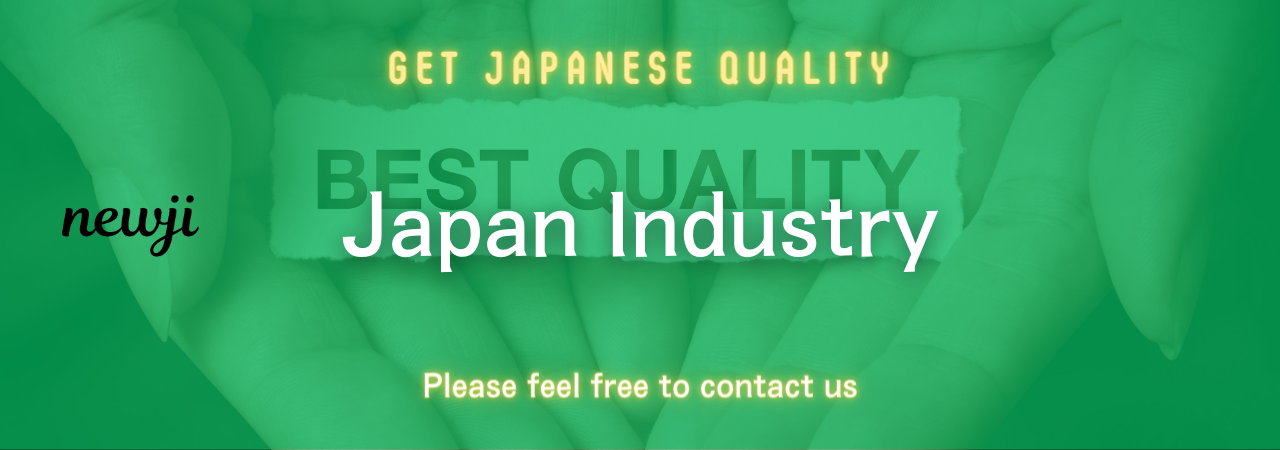
In the world of injection molding, efficiency is paramount.
Using advanced techniques like optimizing hot runner systems can make a significant difference in productivity and quality.
Enhancing these systems not only reduces waste but also improves cycle times and product consistency.
Here’s how you can increase efficiency in your injection molding process through hot runner system optimization.
目次
Understanding Hot Runner Systems
Hot runner systems are crucial components in the injection molding process.
They keep the plastic material in a molten state within the mold, allowing for continuous flow and reducing waste.
The system comprises heated components like nozzles and manifolds that ensure the material remains at the optimal temperature.
This setup contrasts with cold runner systems, where the excess material needs to be trimmed and recycled, generating waste.
Benefits of Hot Runner Systems
Hot runner systems offer several advantages over cold runner systems.
First, they reduce material waste.
Since the plastic remains molten, there’s no need to trim excess material, leading to more efficient use of resources.
Second, they improve cycle times by maintaining consistent melt flow, speeding up the injection process.
Additionally, the enhanced temperature control aids in producing more consistent and higher-quality products.
Lastly, fewer molds are required, resulting in lower maintenance and operational costs.
Key Factors for Optimizing Hot Runner Systems
To maximize the benefits of hot runner systems, several factors need consideration.
Proper design, material selection, and maintenance are critical for optimization.
System Design
Effective design is the backbone of an optimized hot runner system.
The layout of the nozzle and manifold must align precisely with the mold design to ensure uniform flow and temperature distribution.
Utilizing computer-aided design (CAD) software can help in planning an efficient system.
It’s also important to consider the thermal management capabilities of the design, as this will impact cycle times and product quality.
Material Selection
Choosing the right materials for your hot runner system is equally important.
Opt for materials that offer high thermal conductivity and durability.
This ensures that the system can withstand the operational pressures and temperatures of the injection molding process.
Advanced materials like high-grade steel or specialized alloys are often used in nozzles and manifolds for their robustness and longevity.
Regular Maintenance
Maintenance should never be overlooked.
Over time, components in hot runner systems can experience wear and tear or accumulate residue, leading to inefficiencies.
Implementing a regular maintenance schedule, including cleaning and inspecting components, can prevent unexpected downtime and extend the lifespan of the system.
Some manufacturers also offer advanced diagnostic tools to monitor the health of hot runner systems continuously.
Advanced Technologies for Enhancing Efficiency
The integration of advanced technologies can further optimize hot runner systems.
Temperature Control Systems
Precision in temperature control is pivotal for maintaining the integrity of the plastic melt.
Modern temperature control systems offer real-time monitoring and adjustments, ensuring consistent heat distribution throughout the mold.
These systems use sensors and feedback loops to correct any temperature deviations immediately, enhancing the overall efficiency of the injection molding process.
Flow Simulation Software
Flow simulation software allows engineers to visualize and analyze the flow of molten plastic within the hot runner system and mold.
By simulating different scenarios, engineers can identify potential bottlenecks or thermal imbalances before they occur in real production.
This proactive approach helps in fine-tuning the system design for optimal performance and minimizing trial-and-error during the actual molding process.
Automation and IoT Integration
Automation and the Internet of Things (IoT) are revolutionizing injection molding.
Automated systems can handle complex tasks such as mold changes, temperature adjustments, and maintenance checks with minimal human intervention.
IoT-enabled devices allow for remote monitoring and predictive maintenance, reducing downtime and improving efficiency.
The data collected from these devices can provide valuable insights into system performance, helping in making informed decisions for further optimization.
Practical Steps for Immediate Implementation
To start optimizing your hot runner systems, you don’t need to overhaul everything at once.
Here are some practical steps you can take immediately to see noticeable improvements.
Refine Existing Systems
Begin by auditing your current hot runner systems.
Identify any inefficiencies such as uneven temperature distribution or frequent maintenance issues.
Make the necessary adjustments to the system design or material components to address these problems.
Train Your Team
Investing in the training of your team can yield significant returns.
Ensure that everyone involved in the injection molding process understands the importance of hot runner systems and how to optimize them.
Provide training on new technologies and best practices.
Collaborate with Experts
Sometimes, seeking external expertise can be beneficial.
Collaborate with consultants or manufacturers specializing in hot runner systems.
They can provide insights and solutions tailored to your specific needs, helping you achieve optimal efficiency.
By focusing on these strategies, you can make the most of your hot runner systems and enhance the efficiency of your injection molding process.
With continuous improvements and the adoption of advanced technologies, you’ll be well on your way to achieving peak productivity and product quality.
資料ダウンロード
QCD調達購買管理クラウド「newji」は、調達購買部門で必要なQCD管理全てを備えた、現場特化型兼クラウド型の今世紀最高の購買管理システムとなります。
ユーザー登録
調達購買業務の効率化だけでなく、システムを導入することで、コスト削減や製品・資材のステータス可視化のほか、属人化していた購買情報の共有化による内部不正防止や統制にも役立ちます。
NEWJI DX
製造業に特化したデジタルトランスフォーメーション(DX)の実現を目指す請負開発型のコンサルティングサービスです。AI、iPaaS、および先端の技術を駆使して、製造プロセスの効率化、業務効率化、チームワーク強化、コスト削減、品質向上を実現します。このサービスは、製造業の課題を深く理解し、それに対する最適なデジタルソリューションを提供することで、企業が持続的な成長とイノベーションを達成できるようサポートします。
オンライン講座
製造業、主に購買・調達部門にお勤めの方々に向けた情報を配信しております。
新任の方やベテランの方、管理職を対象とした幅広いコンテンツをご用意しております。
お問い合わせ
コストダウンが利益に直結する術だと理解していても、なかなか前に進めることができない状況。そんな時は、newjiのコストダウン自動化機能で大きく利益貢献しよう!
(Β版非公開)