- お役立ち記事
- Optimizing Inventory Management in Manufacturing with PFEP Implementation
Optimizing Inventory Management in Manufacturing with PFEP Implementation
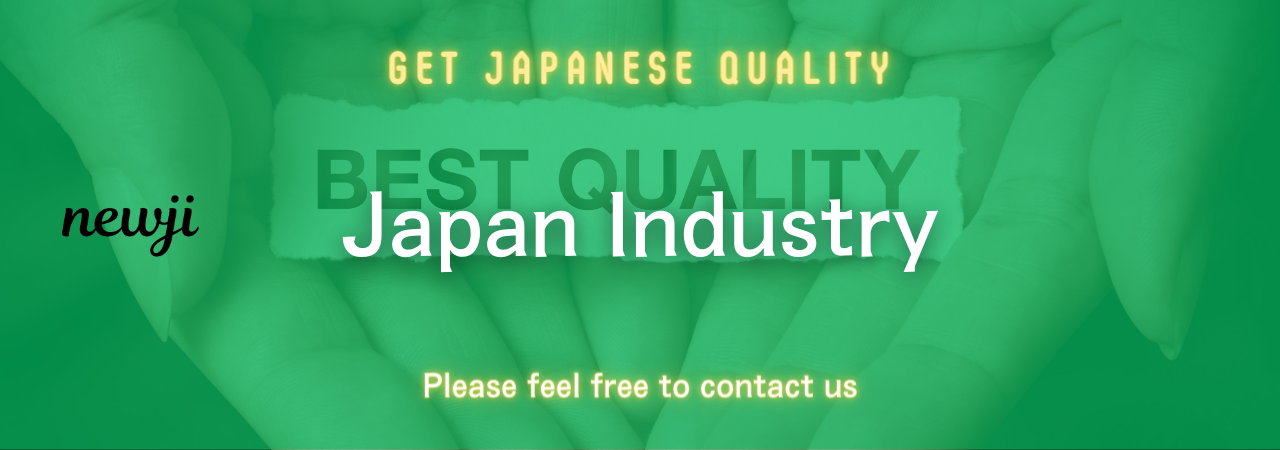
In the world of manufacturing, managing inventory efficiently is vital for maintaining smooth operations and reducing costs.
One method that has proven to be exceptionally effective for optimizing inventory management is PFEP, or Plan For Every Part.
This approach helps manufacturing companies streamline their processes by improving the accuracy and efficiency of inventory tracking, storage, and usage.
目次
What is PFEP?
Plan For Every Part, or PFEP, refers to a comprehensive and systematic approach to managing parts and materials in a manufacturing setting.
It involves creating a detailed plan for each part used in production, encompassing aspects such as storage location, quantity, ordering instructions, and usage rate.
By having a well-documented plan for each part, manufacturers can minimize waste, reduce lead times, and ensure that the right materials are available when needed.
Benefits of PFEP Implementation
Improved Inventory Accuracy
One of the most significant benefits of PFEP implementation is the improvement in inventory accuracy.
When every part has a detailed plan, tracking becomes much simpler and more precise.
This eliminates the risk of overstocking or understocking, which can lead to production delays or increased holding costs.
Improved accuracy means that the right quantity of parts is always available, ensuring smooth and uninterrupted production.
Reduced Lead Times
PFEP helps to identify the optimal ordering and replenishment schedules for each part, which can significantly reduce lead times.
By having a clear understanding of when and how much to order, manufacturers can avoid delays caused by waiting for parts to arrive.
This leads to a more efficient production process and a faster response to customer demands.
Shorter lead times can also improve customer satisfaction and give manufacturers a competitive edge.
Cost Savings
Implementing PFEP can result in substantial cost savings across various aspects of the manufacturing process.
Accurate inventory management reduces the need for excess stock, which in turn lowers storage costs and reduces the risk of obsolescence.
Additionally, better planning leads to more efficient ordering practices, allowing manufacturers to take advantage of bulk purchasing discounts and avoid expedited shipping charges.
The overall reduction in waste and inefficiencies translates to significant cost savings that can positively impact the bottom line.
Steps to Implement PFEP in Manufacturing
Identify All Parts
The first step in implementing PFEP is to identify all the parts used in the manufacturing process.
This includes raw materials, components, and finished goods.
Creating a comprehensive list of all parts involved in production is essential for developing an effective PFEP strategy.
It’s important to categorize the parts based on their type, usage, and criticality to the production process.
Gather Detailed Information
Once all parts have been identified, the next step is to gather detailed information about each one.
This includes specifics such as part number, description, supplier information, lead times, order quantities, and storage requirements.
Having complete and accurate data is crucial for creating a precise and effective PFEP.
Develop Storage and Handling Plans
With detailed information in hand, manufacturers can develop storage and handling plans for each part.
This involves determining the optimal storage location, the best method for handling and moving parts, and the appropriate storage conditions.
For example, some parts may require climate-controlled environments, while others may need special handling procedures to prevent damage.
Well-thought-out storage and handling plans ensure that parts are easily accessible and maintained in good condition.
Establish Replenishment Strategies
A key component of PFEP is establishing effective replenishment strategies.
This involves setting reorder points, defining order quantities, and determining how often orders should be placed.
The goal is to ensure that parts are reordered in a timely manner to avoid stockouts, while also avoiding excess inventory.
Replenishment strategies should be based on historical data, usage patterns, and lead times to achieve optimal inventory levels.
Implement PFEP Across the Organization
After developing detailed plans for each part, the next step is to implement PFEP across the organization.
This involves training employees on the new processes and ensuring that everyone understands and follows the established plans.
It’s important to have clear communication and documentation to support the implementation and make sure that the PFEP is integrated into daily operations.
Continuous Improvement
PFEP is not a one-time effort but an ongoing process that requires continuous improvement.
Regularly reviewing and updating plans to reflect changes in production, supplier performance, and market conditions is essential.
This ensures that the PFEP remains relevant and effective, enabling manufacturers to maintain optimal inventory management over time.
Challenges and Solutions
While the benefits of PFEP are clear, implementing it can present some challenges.
Data Accuracy
Ensuring data accuracy can be a significant challenge, as it requires meticulous record-keeping and regular updates.
To address this, manufacturers can invest in technology such as inventory management software that can automate data entry and provide real-time updates.
Regular audits and reviews can also help maintain data accuracy.
Employee Training
Another challenge is training employees and getting buy-in from the entire organization.
To overcome this, it’s crucial to have a well-structured training program that educates employees on the benefits of PFEP and how to implement it effectively.
Providing ongoing support and resources can also help ensure successful adoption.
Adapting to Change
Manufacturing environments are dynamic, and changes in production processes, supplier performance, or market conditions can impact the effectiveness of PFEP.
To mitigate this challenge, manufacturers should create a flexible PFEP that can be easily adjusted as needed.
Regularly monitoring key performance indicators and being proactive in making necessary adjustments can help maintain the effectiveness of PFEP.
In conclusion, implementing Plan For Every Part (PFEP) in manufacturing is a powerful strategy for optimizing inventory management.
By improving inventory accuracy, reducing lead times, and realizing cost savings, PFEP can significantly enhance the efficiency and profitability of manufacturing operations.
Despite the challenges, with careful planning, continuous improvement, and investment in technology and training, manufacturers can successfully implement PFEP and reap its many benefits.
資料ダウンロード
QCD調達購買管理クラウド「newji」は、調達購買部門で必要なQCD管理全てを備えた、現場特化型兼クラウド型の今世紀最高の購買管理システムとなります。
ユーザー登録
調達購買業務の効率化だけでなく、システムを導入することで、コスト削減や製品・資材のステータス可視化のほか、属人化していた購買情報の共有化による内部不正防止や統制にも役立ちます。
NEWJI DX
製造業に特化したデジタルトランスフォーメーション(DX)の実現を目指す請負開発型のコンサルティングサービスです。AI、iPaaS、および先端の技術を駆使して、製造プロセスの効率化、業務効率化、チームワーク強化、コスト削減、品質向上を実現します。このサービスは、製造業の課題を深く理解し、それに対する最適なデジタルソリューションを提供することで、企業が持続的な成長とイノベーションを達成できるようサポートします。
オンライン講座
製造業、主に購買・調達部門にお勤めの方々に向けた情報を配信しております。
新任の方やベテランの方、管理職を対象とした幅広いコンテンツをご用意しております。
お問い合わせ
コストダウンが利益に直結する術だと理解していても、なかなか前に進めることができない状況。そんな時は、newjiのコストダウン自動化機能で大きく利益貢献しよう!
(Β版非公開)