- お役立ち記事
- Optimizing Inventory Management with ABC Analysis Techniques
月間76,176名の
製造業ご担当者様が閲覧しています*
*2025年3月31日現在のGoogle Analyticsのデータより
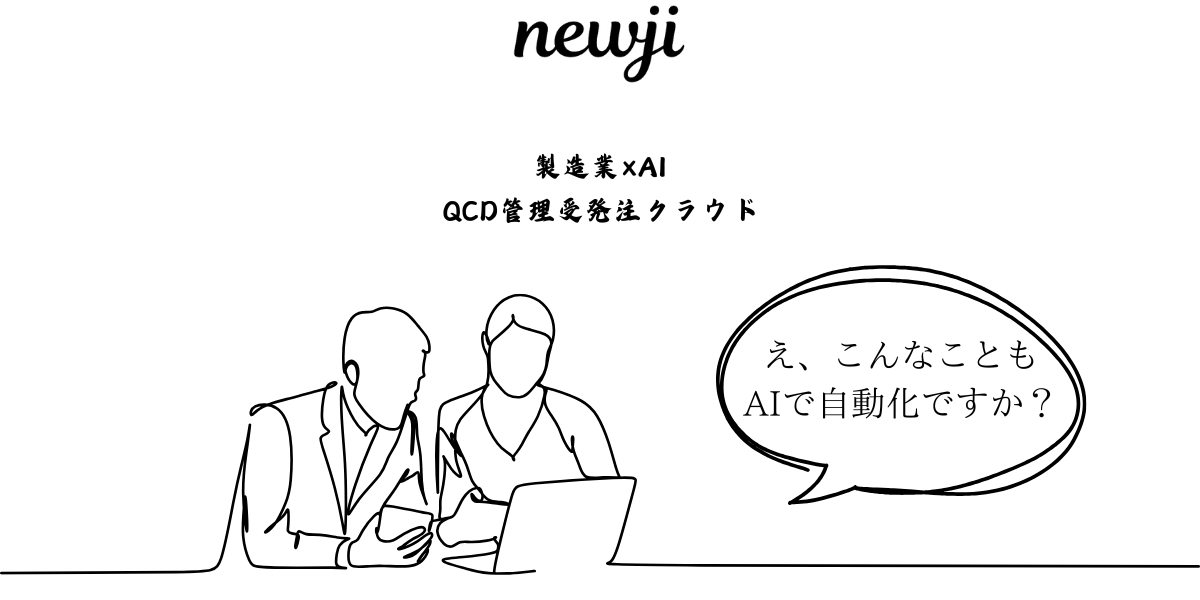
Optimizing Inventory Management with ABC Analysis Techniques
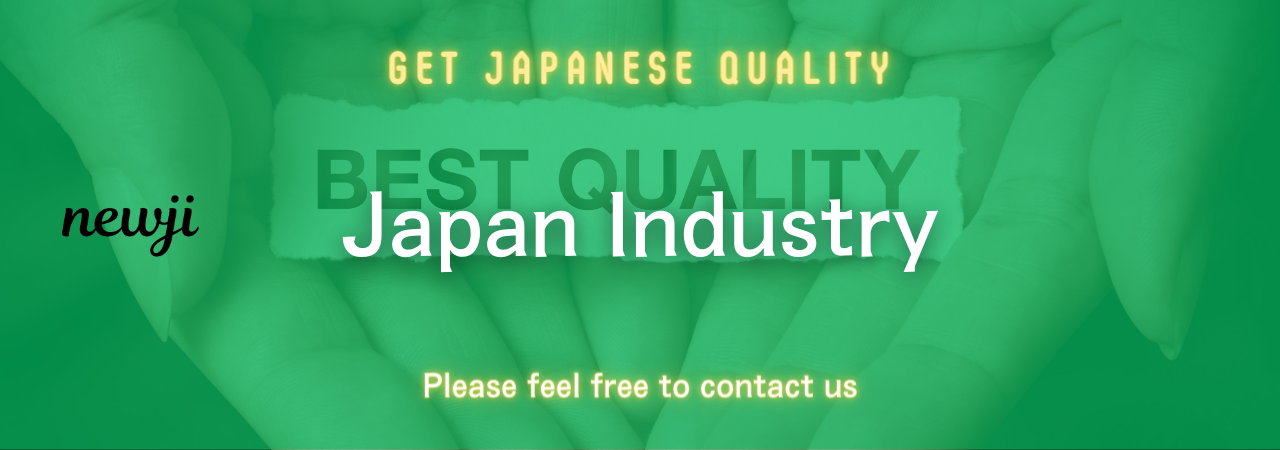
目次
Understanding ABC Analysis
Inventory management is crucial for businesses, ensuring that products are available for customers while minimizing storage costs.
One popular technique for optimizing inventory management is ABC analysis, a method that categorizes inventory items based on their importance.
ABC analysis divides items into three categories: A, B, and C.
Category A consists of items that are the most valuable and require close monitoring.
Category B includes moderately important items, while Category C contains items that are least valuable.
By focusing on the more critical inventory, businesses can streamline their operations and reduce costs.
Implementing ABC Analysis in Inventory Management
To implement ABC analysis effectively, follow these steps:
Step 1: Collect Inventory Data
Begin by gathering detailed information about each inventory item.
This data should include the item description, quantity on hand, unit cost, and annual consumption.
The goal is to understand how each item contributes to the overall inventory value.
Step 2: Calculate the Annual Consumption Value
Next, determine the annual consumption value for each item.
This is done by multiplying the unit cost by the annual usage quantity.
The sum of these calculations will give you the total consumption value for each inventory item over a year.
Step 3: Rank the Items
With the annual consumption values calculated, rank the items in descending order.
The highest consumption value items will be at the top of the list, while the lowest will be at the bottom.
This ranking will help identify which items contribute the most to the inventory value.
Step 4: Classify Inventory Items
Now, divide the ranked list into three categories: A, B, and C.
Category A should consist of the top 20% of items that account for roughly 80% of the total inventory value.
Category B should include the next 30% of items that contribute to about 15% of the value.
Finally, category C will contain the remaining 50% of items, which account for only 5% of the inventory value.
This classification helps in focusing attention on the most critical items.
Benefits of Using ABC Analysis
Implementing ABC analysis offers several benefits to businesses:
Improved Inventory Control
By focusing on the most valuable items, businesses can better manage their inventory levels.
This means ensuring that category A items are always in stock, reducing the risk of stockouts and lost sales.
For category B and C items, businesses can maintain lower inventory levels, reducing carrying costs and minimizing storage space.
Cost Reduction
Effective inventory management can lead to significant cost savings.
By prioritizing high-value items, businesses can reduce excess inventory and associated costs such as storage, handling, and obsolescence.
This allows for more efficient use of resources and improved profitability.
Enhanced Decision-Making
With a clear understanding of the importance of each inventory item, businesses can make more informed decisions.
This includes decisions related to procurement, production planning, and inventory replenishment.
ABC analysis provides valuable insights into which items require more attention and resources, ultimately leading to better operational efficiency.
Challenges of ABC Analysis
While ABC analysis offers numerous benefits, it is essential to be aware of potential challenges:
Data Accuracy
The accuracy of the collected inventory data is crucial for effective ABC analysis.
Incorrect or outdated data can lead to misclassification of items and suboptimal inventory management decisions.
Regularly updating and verifying inventory data is vital for maintaining the accuracy of the analysis.
Dynamic Inventory
Inventory levels and consumption patterns are not static.
They can change over time due to factors such as seasonality, market trends, and product lifecycle stages.
Businesses must regularly review and update their ABC analysis to reflect these changes, ensuring that inventory management practices remain relevant and effective.
Balancing Categories
Finding the right balance between categories A, B, and C can be challenging.
Over-prioritizing category A items might lead to neglecting categories B and C, resulting in potential stockouts or excess inventory for these items.
Striking the right balance is key to maximizing the benefits of ABC analysis.
Best Practices for ABC Analysis
To get the most out of ABC analysis, consider these best practices:
Regularly Review and Update ABC Classification
As inventory consumption patterns and market conditions change, it is essential to review and update the ABC classification regularly.
This ensures that the analysis remains accurate and relevant, allowing businesses to make well-informed inventory management decisions.
Integrate ABC Analysis with Other Inventory Management Techniques
While ABC analysis is a powerful tool, it is most effective when combined with other inventory management techniques.
Methods such as Just-in-Time (JIT), Economic Order Quantity (EOQ), and safety stock calculations can complement ABC analysis and enhance overall inventory control.
Utilize Inventory Management Software
Implementing inventory management software can streamline the ABC analysis process.
These tools can help automate data collection, analysis, and classification, making it easier for businesses to manage their inventory effectively.
Additionally, inventory management software can provide real-time insights, allowing for more agile and responsive decision-making.
Conclusion
ABC analysis is a valuable technique for optimizing inventory management.
By categorizing inventory items based on their importance, businesses can focus on the most critical items, reduce costs, and improve overall efficiency.
While there are challenges associated with ABC analysis, following best practices and regularly updating the analysis can help overcome these obstacles.
Implementing ABC analysis alongside other inventory management techniques and utilizing inventory management software can further enhance its effectiveness.
Ultimately, mastering ABC analysis can lead to better inventory control, cost savings, and enhanced decision-making, contributing to the overall success of a business.
資料ダウンロード
QCD管理受発注クラウド「newji」は、受発注部門で必要なQCD管理全てを備えた、現場特化型兼クラウド型の今世紀最高の受発注管理システムとなります。
ユーザー登録
受発注業務の効率化だけでなく、システムを導入することで、コスト削減や製品・資材のステータス可視化のほか、属人化していた受発注情報の共有化による内部不正防止や統制にも役立ちます。
NEWJI DX
製造業に特化したデジタルトランスフォーメーション(DX)の実現を目指す請負開発型のコンサルティングサービスです。AI、iPaaS、および先端の技術を駆使して、製造プロセスの効率化、業務効率化、チームワーク強化、コスト削減、品質向上を実現します。このサービスは、製造業の課題を深く理解し、それに対する最適なデジタルソリューションを提供することで、企業が持続的な成長とイノベーションを達成できるようサポートします。
製造業ニュース解説
製造業、主に購買・調達部門にお勤めの方々に向けた情報を配信しております。
新任の方やベテランの方、管理職を対象とした幅広いコンテンツをご用意しております。
お問い合わせ
コストダウンが利益に直結する術だと理解していても、なかなか前に進めることができない状況。そんな時は、newjiのコストダウン自動化機能で大きく利益貢献しよう!
(β版非公開)