- お役立ち記事
- Optimizing Japanese Manufacturing with Advanced AGV Control Systems
月間76,176名の
製造業ご担当者様が閲覧しています*
*2025年3月31日現在のGoogle Analyticsのデータより
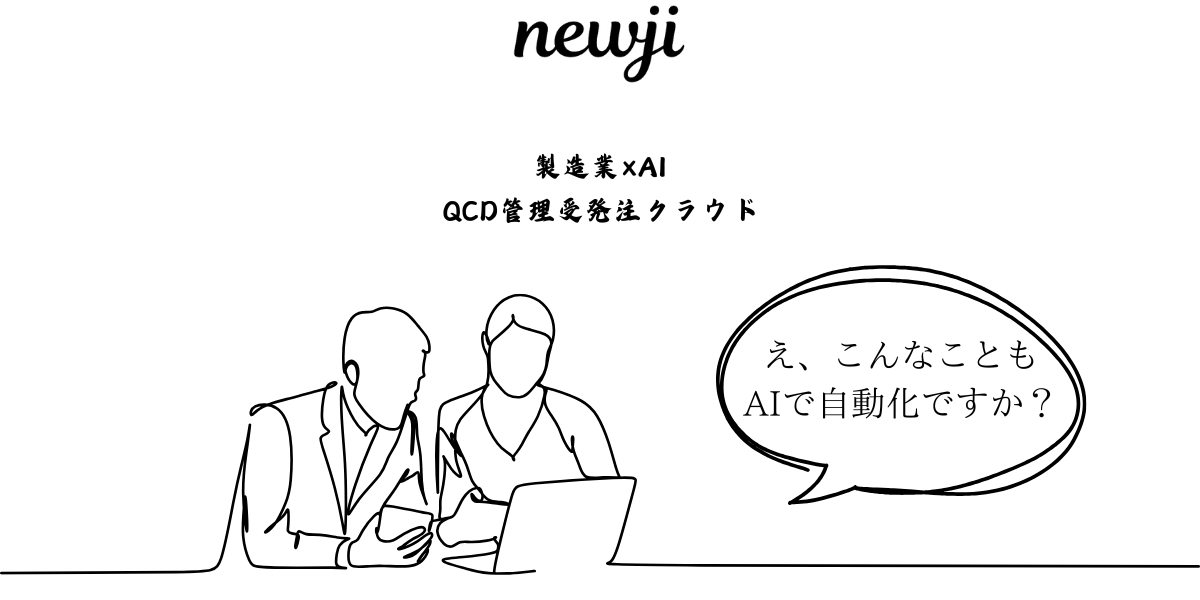
Optimizing Japanese Manufacturing with Advanced AGV Control Systems
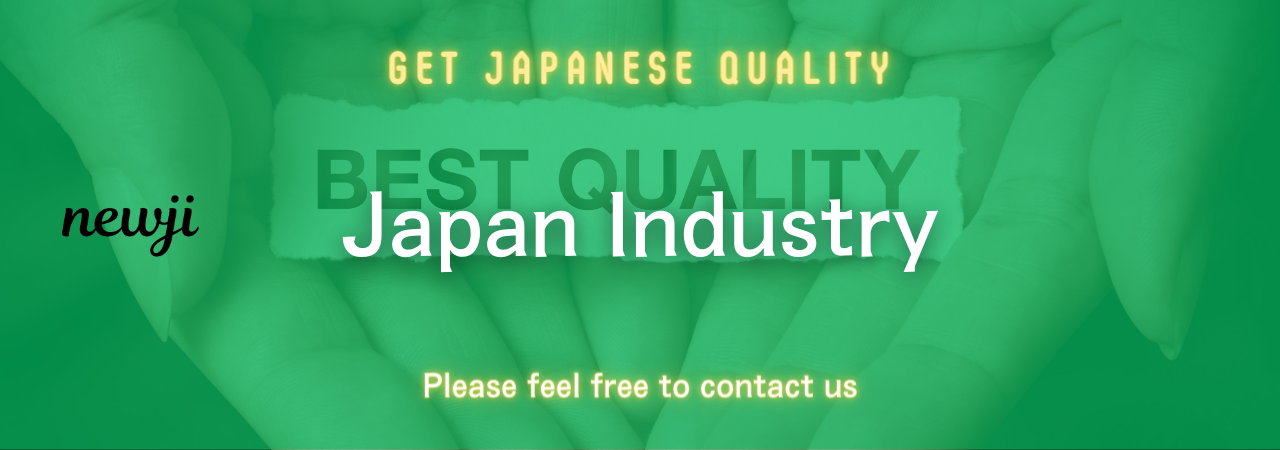
目次
Introduction to Advanced AGV Control Systems in Japanese Manufacturing
Automated Guided Vehicles (AGVs) have become a cornerstone in modern manufacturing environments.
Their integration into Japanese manufacturing processes represents a significant shift towards enhanced efficiency and productivity.
This article explores the optimization of Japanese manufacturing through the implementation of advanced AGV control systems.
We will delve into the practical aspects of procurement and purchasing, examine the advantages and disadvantages, discuss supplier negotiation techniques, assess current market conditions, and outline best practices for successful AGV integration.
The Role of AGVs in Japanese Manufacturing
Enhancing Efficiency and Productivity
AGVs are instrumental in automating material handling tasks.
In Japanese manufacturing, where precision and efficiency are paramount, AGVs contribute by reducing manual labor and minimizing human error.
They ensure consistent and timely delivery of components, thereby streamlining the production process.
The result is increased throughput and better utilization of human resources for more strategic tasks.
Supporting Lean Manufacturing Principles
Lean manufacturing is a philosophy deeply ingrained in Japanese industry.
AGVs align perfectly with lean principles by eliminating waste associated with manual material handling.
They optimize workflow, reduce inventory levels through just-in-time delivery, and enhance overall operational flexibility.
By supporting lean initiatives, AGVs help Japanese manufacturers maintain their competitive edge in the global market.
Advantages of Implementing Advanced AGV Control Systems
Improved Operational Efficiency
Advanced AGV control systems offer precise navigation and real-time tracking.
This leads to improved operational efficiency by ensuring that materials are moved accurately and promptly.
Reduced downtime and minimized bottlenecks contribute to a smoother manufacturing process.
Cost Savings
While the initial investment in AGVs can be significant, the long-term cost savings are substantial.
AGVs reduce labor costs by handling repetitive and strenuous tasks.
They also decrease the likelihood of accidents and damage to materials, leading to lower maintenance and replacement expenses.
Scalability and Flexibility
Modern AGV systems are highly scalable, allowing manufacturers to expand their operations without extensive reconfiguration.
They offer flexibility in adapting to changing production demands and can be reprogrammed to handle different tasks as needed.
This adaptability is crucial for Japanese manufacturers facing fluctuating market conditions and diverse product lines.
Enhanced Safety
Safety is a top priority in Japanese manufacturing facilities.
AGVs are equipped with advanced sensors and safety protocols to prevent collisions and ensure the safe transport of materials.
By automating hazardous tasks, AGVs reduce the risk of workplace injuries and create a safer working environment.
Disadvantages and Challenges of AGV Implementation
High Initial Investment
The upfront cost of purchasing and installing AGV systems can be a barrier for some manufacturers.
This includes expenses for the vehicles themselves, integration with existing systems, and training personnel to operate and maintain the technology.
Complex Integration
Integrating AGVs into existing manufacturing processes can be complex and time-consuming.
It requires meticulous planning to ensure compatibility with current workflows and to minimize disruptions during the transition period.
Maintenance and Downtime
AGVs require regular maintenance to operate effectively.
Any malfunctions or downtime can disrupt the production process, necessitating contingency plans to mitigate the impact on manufacturing operations.
Dependency on Technology
Reliance on AGVs introduces a dependency on advanced technology.
System failures or cyber threats could potentially halt operations, highlighting the need for robust cybersecurity measures and backup systems.
Supplier Negotiation Techniques for AGV Procurement
Thorough Market Research
Before engaging in negotiations, conduct comprehensive market research to understand the range of available AGV solutions and their pricing structures.
This knowledge empowers you to make informed decisions and identify competitive pricing.
Establishing Clear Requirements
Define your specific needs and requirements clearly.
Communicate these to potential suppliers to ensure that the AGV systems proposed align with your manufacturing objectives and operational constraints.
Leveraging Volume and Long-Term Commitments
Negotiating volumes and long-term contracts can provide leverage in achieving better pricing and favorable terms.
Suppliers are often willing to offer discounts or additional services in exchange for guaranteed business commitments.
Evaluating Supplier Reputation and Reliability
Assess the reputation and reliability of potential suppliers.
Consider factors such as their track record, customer reviews, and the quality of their after-sales support.
Favor suppliers who demonstrate a commitment to quality and customer satisfaction.
Requesting Competitive Bids
Solicit bids from multiple suppliers to encourage competitive pricing.
Analyze the proposals not just on cost but also on the value offered in terms of features, support, and flexibility.
Understanding Market Conditions for AGVs in Japan
Technological Advancements
The AGV market in Japan is characterized by rapid technological advancements.
Manufacturers are increasingly adopting smart AGV systems equipped with AI, machine learning, and IoT capabilities.
These innovations enhance the functionality and efficiency of AGVs, making them more adaptable to complex manufacturing environments.
Supply Chain Dynamics
Global supply chain disruptions have underscored the importance of automation in manufacturing.
AGVs offer a resilient solution by ensuring consistent material flow despite external challenges.
Japanese manufacturers are leveraging AGVs to mitigate supply chain vulnerabilities and maintain production continuity.
Competitive Landscape
The AGV market in Japan is highly competitive, with numerous domestic and international players.
This competition drives innovation and leads to a broader range of options for manufacturers looking to implement AGV systems.
Regulatory Environment
Compliance with safety and operational standards is critical.
Japanese regulations mandate stringent safety protocols for automated systems, which suppliers must adhere to.
Staying informed about regulatory changes is essential for successful AGV implementation.
Best Practices for Implementing AGV Control Systems
Comprehensive Planning and Assessment
Begin with a thorough assessment of your manufacturing processes to identify areas where AGVs can add value.
Develop a detailed implementation plan that outlines timelines, resource allocation, and key milestones.
Selecting the Right AGV System
Choose an AGV system that aligns with your specific operational needs.
Consider factors such as load capacity, navigation technology, and compatibility with existing systems.
Engage with suppliers to customize solutions that fit your manufacturing environment.
Training and Development
Provide extensive training for your workforce to ensure they can effectively operate and maintain the AGV systems.
Invest in continuous development programs to keep your team updated on the latest AGV technologies and best practices.
Integration with Existing Systems
Ensure seamless integration of AGVs with your current manufacturing execution systems (MES) and enterprise resource planning (ERP) software.
This integration facilitates data sharing and enables better coordination across different departments.
Continuous Monitoring and Optimization
Implement monitoring tools to track the performance of AGVs in real-time.
Use data analytics to identify areas for improvement and optimize AGV operations for maximum efficiency.
Establishing Maintenance Protocols
Develop a proactive maintenance schedule to prevent unexpected breakdowns.
Regular inspections and timely repairs ensure that AGVs operate reliably and extend their operational lifespan.
Fostering a Culture of Innovation
Encourage a culture that embraces technological advancements and continuous improvement.
Involve your team in the AGV implementation process to garner insights and foster ownership of the new systems.
Case Studies: Success Stories of AGV Implementation in Japanese Manufacturing
Toyota Motor Corporation
Toyota has successfully integrated AGV systems into its manufacturing plants to enhance assembly line efficiency.
The company’s focus on lean manufacturing principles is complemented by the automation capabilities of AGVs, leading to reduced lead times and improved product quality.
Panasonic Corporation
Panasonic employs advanced AGV control systems in its electronics manufacturing facilities.
The AGVs facilitate seamless material flow, supporting Panasonic’s commitment to innovation and high-quality production standards.
Hitachi Ltd.
Hitachi utilizes AGVs to manage complex logistics in its industrial manufacturing units.
The integration of AGVs with Hitachi’s IoT-based manufacturing systems has resulted in optimized operations and increased scalability.
Future Trends in AGV Technology and Japanese Manufacturing
Artificial Intelligence and Machine Learning
The incorporation of AI and machine learning into AGV systems is set to revolutionize automation.
These technologies enable AGVs to learn and adapt to dynamic manufacturing environments, enhancing their efficiency and decision-making capabilities.
Enhanced Connectivity through IoT
IoT-enabled AGVs can communicate seamlessly with other machines and systems within the manufacturing facility.
This connectivity facilitates real-time data exchange, predictive maintenance, and improved operational visibility.
Autonomous Navigation and Advanced Sensors
Future AGVs will feature more sophisticated autonomous navigation systems and advanced sensors.
These enhancements will allow AGVs to navigate complex environments with greater precision and safety, further reducing reliance on human intervention.
Integration with Smart Manufacturing Ecosystems
AGVs will increasingly become integral components of smart manufacturing ecosystems.
Their ability to interact with other automated systems will foster a more interconnected and efficient manufacturing process.
Conclusion
The optimization of Japanese manufacturing through advanced AGV control systems offers significant benefits in terms of operational efficiency, cost savings, scalability, and safety.
While there are challenges associated with implementation, such as high initial costs and complex integration, the long-term advantages make AGVs a valuable investment for manufacturers seeking to enhance their competitive edge.
By employing effective supplier negotiation techniques, understanding market conditions, and adhering to best practices, Japanese manufacturers can successfully integrate AGV systems into their operations.
Looking ahead, emerging technologies like AI, IoT, and autonomous navigation will further enhance the capabilities of AGVs, paving the way for smarter and more efficient manufacturing processes.
資料ダウンロード
QCD管理受発注クラウド「newji」は、受発注部門で必要なQCD管理全てを備えた、現場特化型兼クラウド型の今世紀最高の受発注管理システムとなります。
ユーザー登録
受発注業務の効率化だけでなく、システムを導入することで、コスト削減や製品・資材のステータス可視化のほか、属人化していた受発注情報の共有化による内部不正防止や統制にも役立ちます。
NEWJI DX
製造業に特化したデジタルトランスフォーメーション(DX)の実現を目指す請負開発型のコンサルティングサービスです。AI、iPaaS、および先端の技術を駆使して、製造プロセスの効率化、業務効率化、チームワーク強化、コスト削減、品質向上を実現します。このサービスは、製造業の課題を深く理解し、それに対する最適なデジタルソリューションを提供することで、企業が持続的な成長とイノベーションを達成できるようサポートします。
製造業ニュース解説
製造業、主に購買・調達部門にお勤めの方々に向けた情報を配信しております。
新任の方やベテランの方、管理職を対象とした幅広いコンテンツをご用意しております。
お問い合わせ
コストダウンが利益に直結する術だと理解していても、なかなか前に進めることができない状況。そんな時は、newjiのコストダウン自動化機能で大きく利益貢献しよう!
(β版非公開)