- お役立ち記事
- Optimizing Location Management in Manufacturing with GPS Sensors
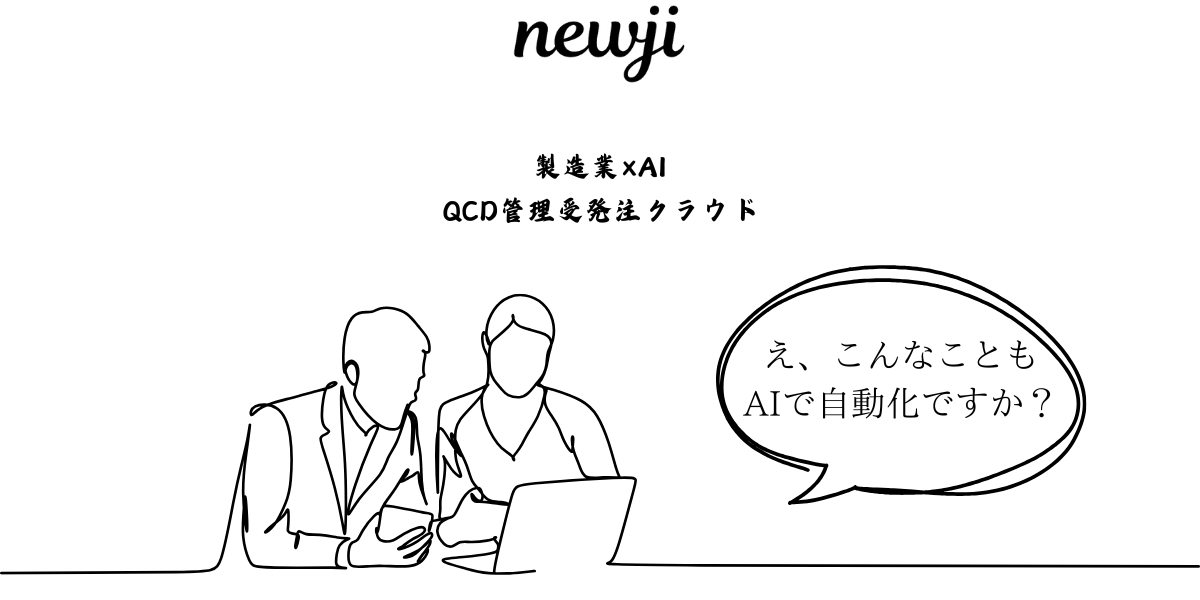
Optimizing Location Management in Manufacturing with GPS Sensors
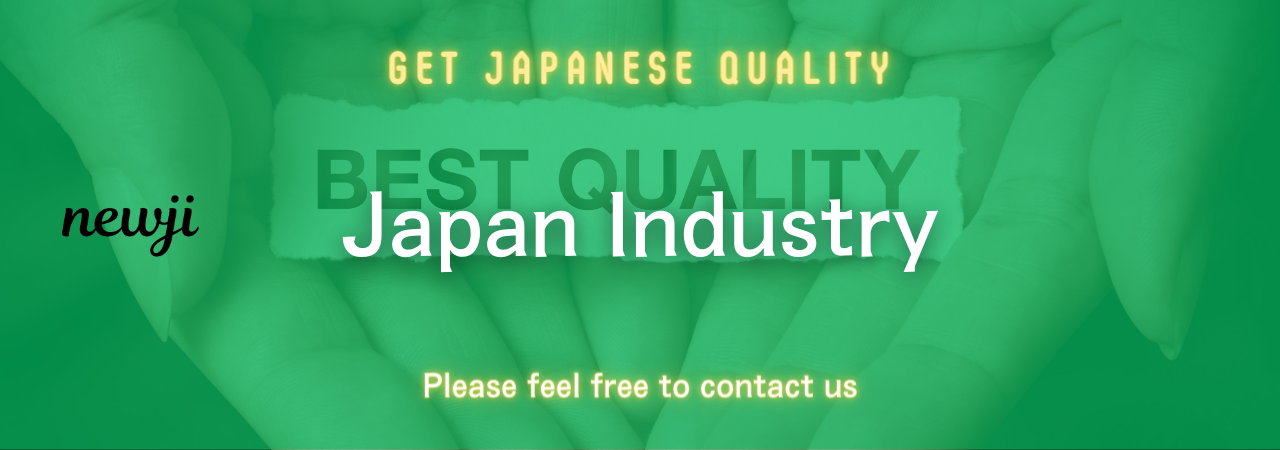
Effective location management is crucial for the success of any manufacturing operation.
Ensuring that materials, equipment, and personnel are in the right place at the right time improves efficiency and productivity.
One way to streamline this process is through the use of GPS sensors.
In this article, we will explore how GPS sensors can optimize location management in manufacturing.
目次
What Are GPS Sensors?
GPS, or Global Positioning System, is a satellite-based navigation system that allows a device to determine its exact location.
GPS sensors are devices that receive signals from satellites to pinpoint their geographical position.
They play a vital role in various industries, including transportation, logistics, and manufacturing.
The Benefits of GPS Sensors in Manufacturing
Enhanced Asset Tracking
In a busy manufacturing environment, keeping track of assets such as raw materials, machinery, and finished products is a challenging task.
GPS sensors can be attached to these assets, allowing managers to monitor their locations in real-time.
This reduces the risk of loss or misplacement and ensures that critical assets are where they need to be.
Improved Inventory Management
Efficient inventory management is essential for minimizing costs and meeting production schedules.
GPS sensors can help track the movement of raw materials and finished goods within the facility.
This enables accurate inventory counts and timely replenishment of stock.
As a result, manufacturers can avoid stockouts or overstock situations, thereby optimizing their inventory management processes.
Enhanced Worker Safety
Ensuring worker safety is a top priority in any manufacturing setting.
GPS sensors can be used to track the locations of workers within the facility.
In case of an emergency, managers can quickly locate and assist affected personnel.
Moreover, geofencing technology can be integrated with GPS sensors to define safe zones.
If a worker enters a potentially hazardous area, an alert can be triggered to notify supervisors and prevent accidents.
Optimized Workflow and Efficiency
GPS sensors allow for precise tracking of equipment and machinery movement.
This enables managers to analyze workflows and identify bottlenecks.
By understanding how materials and equipment move through the manufacturing process, managers can optimize layouts and streamline operations.
This leads to improved efficiency and reduced production time.
How GPS Sensors Work in Manufacturing
Installation and Setup
To get started with GPS sensors in a manufacturing environment, the first step is to install the sensors on the assets and equipment you wish to track.
These sensors can be affixed using brackets, adhesive, or other mounting solutions.
Integration with Software Systems
Next, the GPS sensors must be integrated with your existing software systems, such as enterprise resource planning (ERP) or manufacturing execution systems (MES).
This integration is crucial for collecting and analyzing data from the sensors.
Many GPS sensors come with dedicated software that allows for seamless data integration and analysis.
Real-Time Monitoring
Once the sensors are installed and integrated, they begin transmitting location data in real-time.
Managers can access this data through dashboards and reports, enabling them to monitor the movement and status of assets, equipment, and personnel.
Real-time monitoring allows for quick decision-making and immediate response to any issues that arise.
Data Analysis and Insights
The data collected by GPS sensors can be analyzed to gain valuable insights into the manufacturing process.
By identifying patterns and trends, managers can make informed decisions to improve operations.
For example, if data shows that certain equipment is frequently idle, it may indicate a need for maintenance or process adjustments.
Overcoming Challenges with GPS Sensors
Signal Interference
One of the main challenges with using GPS sensors in manufacturing is signal interference.
Manufacturing facilities often have structures and machinery that can block or weaken GPS signals.
To overcome this, manufacturers can use a combination of GPS and other positioning technologies, such as Wi-Fi or Bluetooth, to ensure accurate tracking.
Data Security
Protecting the data collected by GPS sensors is essential to prevent unauthorized access and security breaches.
Encryption and secure communication protocols should be implemented to safeguard the data.
Additionally, manufacturers should have a robust data management plan in place to handle the storage and analysis of GPS data.
Cost Considerations
Implementing GPS sensors can be costly, particularly for large-scale manufacturing operations.
However, the investment can be justified by the increase in efficiency and reduction in losses achieved through better location management.
Manufacturers should conduct a cost-benefit analysis to determine the potential return on investment.
Future Trends in GPS Sensors for Manufacturing
Improved Accuracy
Advancements in GPS technology are continually improving the accuracy of location tracking.
Future GPS sensors are expected to offer even higher precision, enabling more accurate management of assets and personnel within manufacturing facilities.
Integration with IoT
The Internet of Things (IoT) is transforming the manufacturing landscape.
Integrating GPS sensors with IoT devices will enable more comprehensive monitoring and control of manufacturing processes.
For example, IoT-enabled GPS sensors can communicate with other smart devices to automate workflows and enhance overall efficiency.
Predictive Maintenance
GPS sensors, combined with data analytics, can play a significant role in predictive maintenance.
By monitoring the location and usage patterns of machinery and equipment, manufacturers can predict when maintenance is needed before a breakdown occurs.
This proactive approach reduces downtime and extends the lifespan of equipment.
In conclusion, GPS sensors offer numerous benefits for optimizing location management in manufacturing.
From enhanced asset tracking and inventory management to improved worker safety and workflow efficiency, these sensors can significantly enhance operational performance.
By addressing challenges and staying abreast of future trends, manufacturers can make the most of GPS sensor technology to drive success and remain competitive in today’s fast-paced industry.
資料ダウンロード
QCD調達購買管理クラウド「newji」は、調達購買部門で必要なQCD管理全てを備えた、現場特化型兼クラウド型の今世紀最高の購買管理システムとなります。
ユーザー登録
調達購買業務の効率化だけでなく、システムを導入することで、コスト削減や製品・資材のステータス可視化のほか、属人化していた購買情報の共有化による内部不正防止や統制にも役立ちます。
NEWJI DX
製造業に特化したデジタルトランスフォーメーション(DX)の実現を目指す請負開発型のコンサルティングサービスです。AI、iPaaS、および先端の技術を駆使して、製造プロセスの効率化、業務効率化、チームワーク強化、コスト削減、品質向上を実現します。このサービスは、製造業の課題を深く理解し、それに対する最適なデジタルソリューションを提供することで、企業が持続的な成長とイノベーションを達成できるようサポートします。
オンライン講座
製造業、主に購買・調達部門にお勤めの方々に向けた情報を配信しております。
新任の方やベテランの方、管理職を対象とした幅広いコンテンツをご用意しております。
お問い合わせ
コストダウンが利益に直結する術だと理解していても、なかなか前に進めることができない状況。そんな時は、newjiのコストダウン自動化機能で大きく利益貢献しよう!
(Β版非公開)