- お役立ち記事
- Optimizing Manufacturing Networks by Understanding the OSI Reference Model
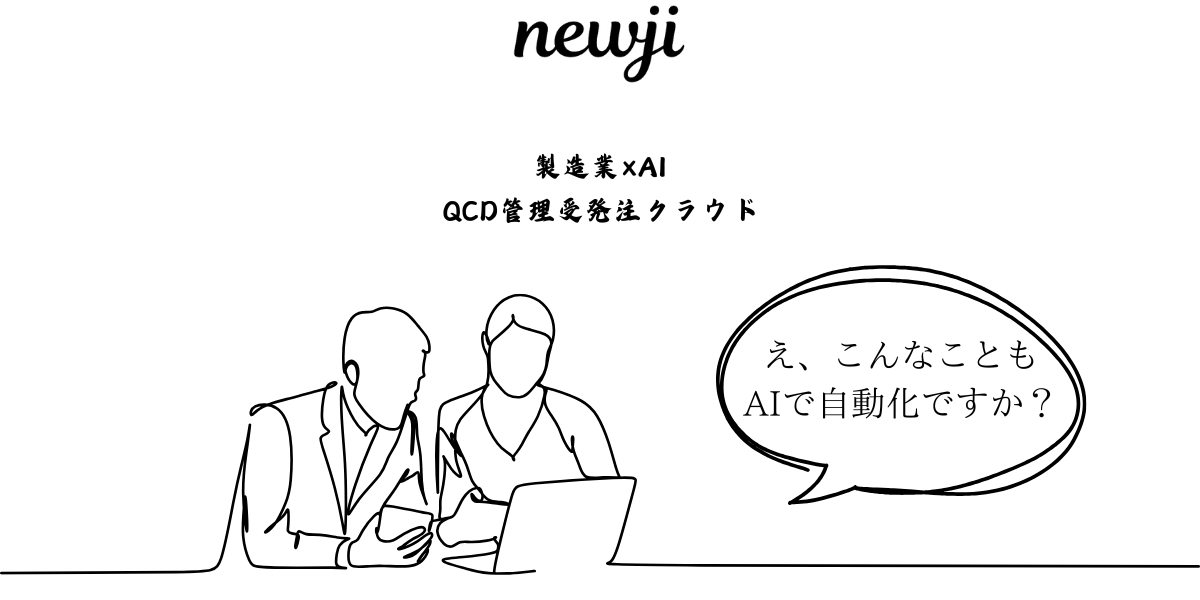
Optimizing Manufacturing Networks by Understanding the OSI Reference Model
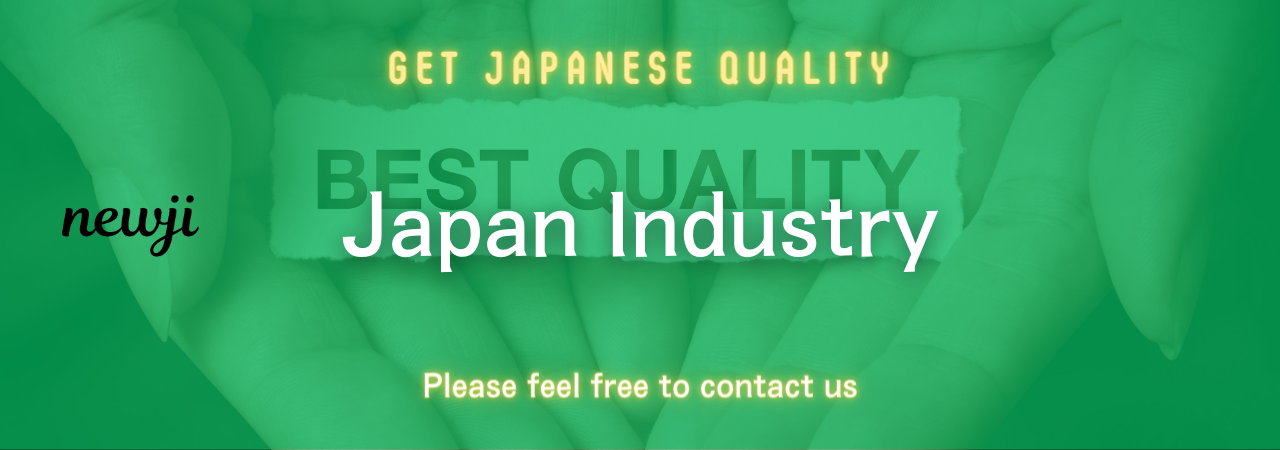
The OSI Reference Model is a concept that can seem baffling at first, especially to those not well-versed in the details of networking and data communication.
However, its fundamental principles can play a vital role in optimizing manufacturing networks and enhancing overall efficiency.
Understanding the OSI Reference Model allows manufacturers to address issues in data communication, ensuring smoother operations, and facilitating better decision-making processes.
目次
What is the OSI Reference Model?
The OSI (Open Systems Interconnection) Reference Model is a conceptual framework used to understand and implement standards for network communication between different systems.
Developed by the International Organization for Standardization (ISO), this model consists of seven layers that define specific tasks involved in data communication.
The layers are:
1. **Physical Layer**
2. **Data Link Layer**
3. **Network Layer**
4. **Transport Layer**
5. **Session Layer**
6. **Presentation Layer**
7. **Application Layer**
Each of these layers plays a unique role in managing and transmitting data between computing devices, ensuring efficient communication and interoperability.
1. Physical Layer
The Physical Layer is the first layer in the OSI Model and deals with the physical connection between devices.
This includes the hardware elements like cables, switches, and network interface cards.
In a manufacturing setting, the reliability of the physical layer can impact production efficiency, as disruptions in network connectivity can halt machinery and workflow.
2. Data Link Layer
The Data Link Layer ensures reliable transmission of data across the physical network.
It handles error detection and correction and is responsible for establishing, maintaining, and terminating the data link connection.
For manufacturers, an optimized data link layer can prevent data loss and minimize production downtimes caused by communication errors.
3. Network Layer
The Network Layer is responsible for determining the best path for data transmission.
It manages the routing of data packets from source to destination, addressing the devices on the network and ensuring that data reaches the correct recipient.
For manufacturing networks, this layer ensures that critical data, such as production metrics, reaches the appropriate system without unnecessary delays.
4. Transport Layer
The Transport Layer guarantees the complete transfer of data.
It provides error checking and ensures that data is delivered accurately and in the correct sequence.
In manufacturing, this layer ensures that instructions sent to machinery or robotics are received intact, contributing to smooth and error-free production processes.
5. Session Layer
The Session Layer manages and controls the dialogue between two computers.
It establishes, maintains, and terminates the interaction session.
For manufacturing networks, this layer is crucial for coordinating and synchronizing interactions between various systems, ensuring that processes are carried out systematically.
6. Presentation Layer
The Presentation Layer translates data between the application layer and the network.
It ensures that data is presented in a usable format and handles data encryption and compression.
In a manufacturing context, this layer can help in translating machine instructions and data formats, facilitating better communication between different machinery and systems.
7. Application Layer
The Application Layer is the topmost layer, serving as the interface between the network and end-users.
It provides network services directly to user applications.
For manufacturers, this layer supports applications that manage inventory, control machinery, and monitor production processes, enabling efficient operations and data management.
Benefits of Applying the OSI Model in Manufacturing Networks
Understanding and applying the OSI Reference Model to manufacturing networks offers several benefits:
Improved Troubleshooting and Network Management
By breaking down the networking process into distinct layers, the OSI Model makes it easier to identify and solve network issues.
Manufacturers can pinpoint problems to a specific layer, enabling quicker and more effective troubleshooting.
This level of detail helps maintain consistent production flow, minimizing downtime and enhancing productivity.
Enhanced Interoperability
The OSI Model promotes standardization, which enhances interoperability between different devices and systems.
For manufacturers, this means improved compatibility between machinery and software from different vendors.
This interoperability supports seamless communication across the production line, optimizing the overall manufacturing process.
Scalability and Flexibility
A layered network structure, as defined by the OSI Model, allows for greater scalability and flexibility.
Manufacturers can upgrade or modify one layer without affecting the others, making it easier to implement new technologies and expand operations.
This adaptability is crucial in the dynamic manufacturing industry, where technological advancements and market demands evolve rapidly.
Better Data Integrity and Security
The OSI Model emphasizes data integrity and security at each layer.
Manufacturers can implement protocols and measures at various layers to protect data against loss and unauthorized access.
Ensuring high data integrity and robust security measures are vital for protecting intellectual property and maintaining operational integrity.
Implementing the OSI Model in Manufacturing Networks
To effectively implement the OSI Model in manufacturing networks, manufacturers should follow a structured approach:
Conduct a Network Assessment
Start by assessing the current network infrastructure.
Identify the strengths and weaknesses at each OSI layer to understand where improvements are needed.
This baseline will help in prioritizing upgrades and enhancements.
Invest in Quality Hardware
Ensure that the physical layer is robust by investing in high-quality cables, switches, and networking hardware.
Reliable physical connections form the foundation of a stable manufacturing network.
Standardize Protocols and Procedures
Adopting standard protocols and procedures across the network layers will enhance compatibility and performance.
This standardization helps in maintaining coherence and stability, making the network easier to manage.
Enhance Security Measures
Implement security measures at each OSI layer to protect against data breaches and cyber threats.
Regularly update security protocols and conduct audits to ensure ongoing protection.
Train Staff and Maintenance Personnel
Provide training for staff and maintenance personnel on the principles of the OSI Model.
A deeper understanding of the model will enable them to troubleshoot more effectively and maintain the network efficiently.
In conclusion, the OSI Reference Model is a powerful framework for understanding and optimizing manufacturing networks.
By breaking down complex networking processes into manageable layers, manufacturers can enhance network reliability, interoperability, and security.
Implementing the OSI Model ensures smoother operations, better data management, and ultimately contributes to an increase in productivity and efficiency across the manufacturing landscape.
資料ダウンロード
QCD調達購買管理クラウド「newji」は、調達購買部門で必要なQCD管理全てを備えた、現場特化型兼クラウド型の今世紀最高の購買管理システムとなります。
ユーザー登録
調達購買業務の効率化だけでなく、システムを導入することで、コスト削減や製品・資材のステータス可視化のほか、属人化していた購買情報の共有化による内部不正防止や統制にも役立ちます。
NEWJI DX
製造業に特化したデジタルトランスフォーメーション(DX)の実現を目指す請負開発型のコンサルティングサービスです。AI、iPaaS、および先端の技術を駆使して、製造プロセスの効率化、業務効率化、チームワーク強化、コスト削減、品質向上を実現します。このサービスは、製造業の課題を深く理解し、それに対する最適なデジタルソリューションを提供することで、企業が持続的な成長とイノベーションを達成できるようサポートします。
オンライン講座
製造業、主に購買・調達部門にお勤めの方々に向けた情報を配信しております。
新任の方やベテランの方、管理職を対象とした幅広いコンテンツをご用意しております。
お問い合わせ
コストダウンが利益に直結する術だと理解していても、なかなか前に進めることができない状況。そんな時は、newjiのコストダウン自動化機能で大きく利益貢献しよう!
(Β版非公開)