- お役立ち記事
- Optimizing Manufacturing Processes with Advanced Simulation Technologies
Optimizing Manufacturing Processes with Advanced Simulation Technologies
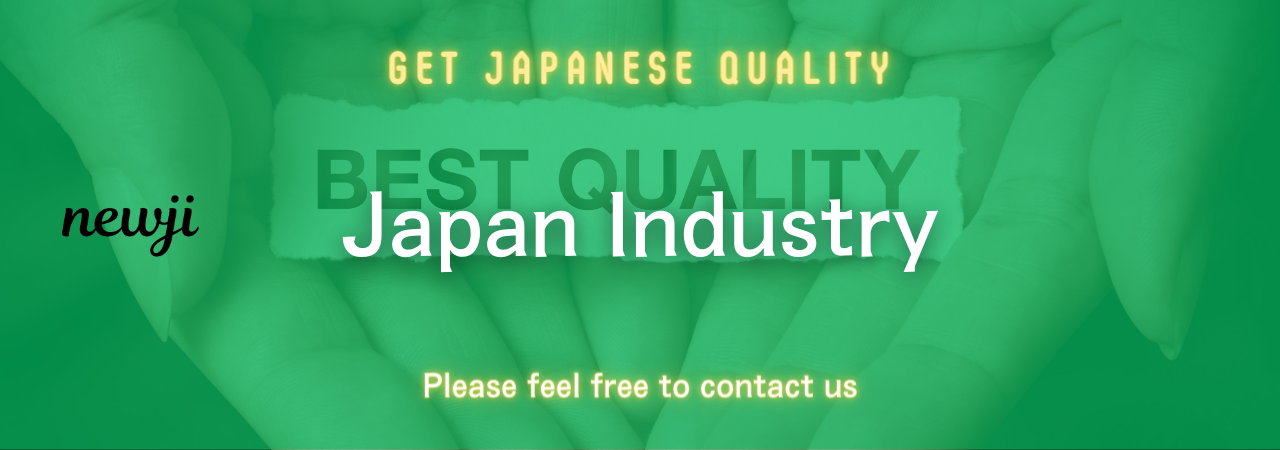
Manufacturing processes have evolved significantly over the years, primarily driven by innovations in technology.
One of the most revolutionary advancements in this field is the integration of advanced simulation technologies.
These technologies are transforming the manufacturing landscape, offering unprecedented precision, efficiency, and cost savings.
目次
What are Advanced Simulation Technologies?
Simulation technologies involve the use of computer models to replicate and analyze real-world processes.
In manufacturing, these technologies allow engineers to create virtual models of production systems, machinery, and even entire factories.
These models can be manipulated to simulate various conditions and predict outcomes without the need for physical trials.
By doing so, companies can identify potential issues, optimize processes, and improve product quality before actual implementation.
Benefits of Using Simulation in Manufacturing
Cost Reduction
One of the primary benefits of using advanced simulation technologies in manufacturing is cost reduction.
Traditional methods of trial and error can be expensive.
With simulation, manufacturers can test and refine processes in a virtual environment, thereby reducing the costs associated with materials, labor, and downtime.
Enhanced Efficiency
Simulations offer the ability to analyze the efficiency of different processes and systems.
Manufacturers can identify bottlenecks and areas of inefficiency and implement changes to improve overall throughput.
This enhanced efficiency translates into faster production times and greater output.
Risk Mitigation
Introducing new processes or equipment always carries some level of risk.
Simulation technologies help mitigate these risks by allowing manufacturers to visualize potential problems and address them proactively.
This foresight can prevent costly mistakes and ensure smoother implementation of new technologies or methods.
Improved Product Quality
Quality is a critical factor in manufacturing.
Simulation technologies enable detailed analysis of production processes, ensuring that they are optimized for the highest quality output.
Predictive analytics can highlight potential quality issues before they occur, allowing manufacturers to take corrective actions.
Flexibility and Innovation
Advanced simulation technologies provide a platform for innovation.
Manufacturers can experiment with new materials, designs, and processes in a virtual environment.
This flexibility facilitates the development of cutting-edge products and allows companies to stay ahead of the competition.
Key Simulation Technologies in Manufacturing
Finite Element Analysis (FEA)
Finite Element Analysis (FEA) is a powerful simulation technique used to predict how products will react to real-world forces, such as heat, vibration, and other physical effects.
By using FEA, manufacturers can identify and resolve potential weak points in a product’s design before it goes into production.
Computational Fluid Dynamics (CFD)
Computational Fluid Dynamics (CFD) is used to simulate fluid flow within a product.
This technology is particularly useful in industries such as automotive and aerospace, where aerodynamics and fluid behavior are critical.
CFD helps optimize designs for efficiency and performance while reducing the need for physical prototypes.
Discrete Event Simulation (DES)
Discrete Event Simulation (DES) models the operation of a system as a sequence of discrete events over time.
This type of simulation is essential for understanding complex manufacturing systems, including workflow, production schedules, and resource allocation.
DES enables manufacturers to optimize operations and improve decision-making.
Virtual Reality (VR) and Augmented Reality (AR)
Virtual Reality (VR) and Augmented Reality (AR) are increasingly being used in manufacturing simulations.
These technologies provide immersive experiences, allowing engineers to visualize and interact with virtual models of production systems.
VR and AR can be used for training, maintenance, and design review, enhancing overall productivity.
Steps to Implement Simulation Technologies in Manufacturing
Identify Objectives
The first step in implementing simulation technologies is to identify the specific objectives and challenges you want to address.
Are you looking to reduce costs, improve quality, or enhance efficiency?
Clearly define your goals to ensure that your simulation efforts are aligned with your business needs.
Select the Appropriate Simulation Software
Choosing the right simulation software is crucial.
There are numerous options available, each with its own strengths and capabilities.
Evaluate different software based on your specific requirements, such as the type of simulation needed (e.g., FEA, CFD, DES), ease of use, and scalability.
Collect Data
Accurate data is the foundation of any successful simulation.
Gather detailed information about your manufacturing processes, equipment, and materials.
This data will be used to create realistic models and ensure that your simulations provide meaningful insights.
Create and Validate Models
Once you have the necessary data, create your simulation models.
Work closely with engineers and other stakeholders to ensure that the models accurately represent your real-world processes.
Validate the models by comparing simulation results with actual performance data to ensure their accuracy.
Analyze and Optimize
With validated models in hand, you can begin running simulations and analyzing the results.
Identify areas for improvement and test different scenarios to optimize your processes.
Use the insights gained from simulations to make informed decisions and implement changes in your manufacturing operations.
Conclusion
Advanced simulation technologies are revolutionizing the manufacturing industry, offering numerous benefits ranging from cost reduction to improved product quality.
By leveraging these technologies, manufacturers can stay competitive in an increasingly dynamic market.
Implementing simulation technologies involves a series of steps, from defining objectives to optimizing processes, but the rewards are well worth the effort.
As technology continues to advance, the role of simulation in manufacturing will only grow, driving further innovation and efficiency in the industry.
資料ダウンロード
QCD調達購買管理クラウド「newji」は、調達購買部門で必要なQCD管理全てを備えた、現場特化型兼クラウド型の今世紀最高の購買管理システムとなります。
ユーザー登録
調達購買業務の効率化だけでなく、システムを導入することで、コスト削減や製品・資材のステータス可視化のほか、属人化していた購買情報の共有化による内部不正防止や統制にも役立ちます。
NEWJI DX
製造業に特化したデジタルトランスフォーメーション(DX)の実現を目指す請負開発型のコンサルティングサービスです。AI、iPaaS、および先端の技術を駆使して、製造プロセスの効率化、業務効率化、チームワーク強化、コスト削減、品質向上を実現します。このサービスは、製造業の課題を深く理解し、それに対する最適なデジタルソリューションを提供することで、企業が持続的な成長とイノベーションを達成できるようサポートします。
オンライン講座
製造業、主に購買・調達部門にお勤めの方々に向けた情報を配信しております。
新任の方やベテランの方、管理職を対象とした幅広いコンテンツをご用意しております。
お問い合わせ
コストダウンが利益に直結する術だと理解していても、なかなか前に進めることができない状況。そんな時は、newjiのコストダウン自動化機能で大きく利益貢献しよう!
(Β版非公開)