- お役立ち記事
- Optimizing Manufacturing Processes with QFD: Secrets to Efficiency and Quality Improvement
Optimizing Manufacturing Processes with QFD: Secrets to Efficiency and Quality Improvement
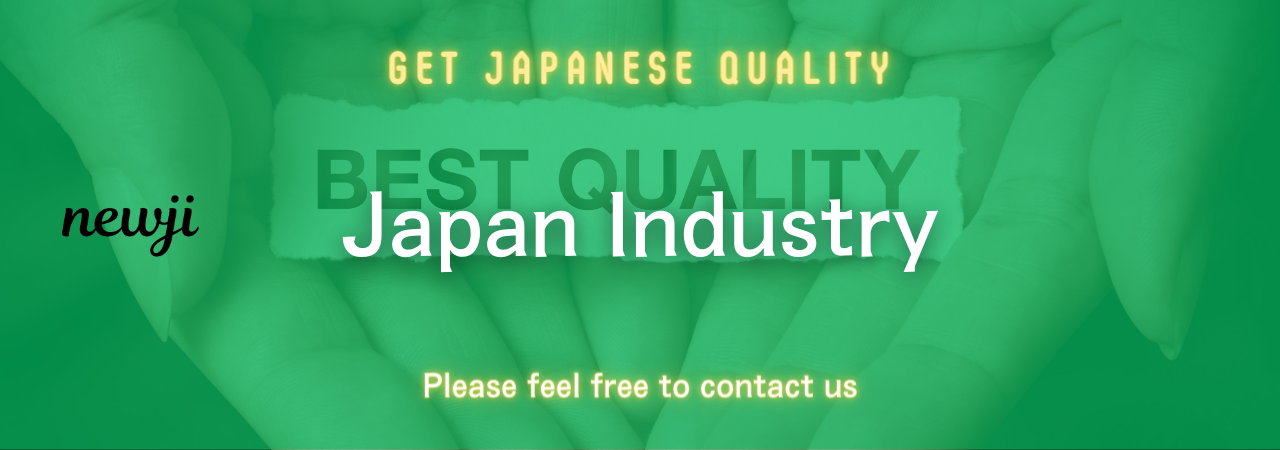
Quality Function Deployment (QFD) is a powerful tool that can help companies improve their manufacturing processes. By focusing on customer needs and translating those needs into specific technical requirements, QFD ensures that every step of the product development process is aligned with what customers truly want.
## What is Quality Function Deployment (QFD)?
Quality Function Deployment, commonly known as QFD, is a structured approach used in manufacturing and product development. It aims to capture customer requirements and translate them into technical specifications. This helps in designing products that meet customer expectations and improve overall quality and efficiency.
## Benefits of Using QFD in Manufacturing
### Better Understanding of Customer Needs
One of the primary advantages of using QFD is that it enhances the understanding of customer needs. By gathering detailed information about what customers want, manufacturers can create products that are more likely to satisfy their target audience.
### Improved Communication
QFD fosters better communication within and between teams. By visualizing the relationship between customer requirements and technical specifications, different departments can have a clearer understanding of their roles and responsibilities.
### Enhanced Efficiency
By aligning the manufacturing process with customer needs, QFD can optimize production and reduce waste. This leads to a more efficient use of resources and time, ultimately lowering costs.
### Higher Quality Products
Since QFD focuses on meeting customer requirements, the end result is often a higher quality product. This can lead to increased customer satisfaction and loyalty, which is essential for long-term success.
## The QFD Process
### Step 1: Identify Customer Requirements
The first step in QFD is to gather detailed information about customer requirements. This can be done through surveys, focus groups, interviews, and other methods. The goal is to understand what features and qualities customers value most in a product.
### Step 2: Prioritize Customer Needs
Once the customer requirements are gathered, the next step is to prioritize them. Not all requirements will have the same level of importance, so it’s essential to identify which ones are most critical to customer satisfaction.
### Step 3: Translate Requirements into Technical Specifications
After prioritizing the customer needs, the next step is to translate those needs into specific technical specifications. This involves identifying the technical features and processes that will be used to meet the customer requirements.
### Step 4: Develop a House of Quality
The House of Quality is a visual tool used in QFD to represent the relationship between customer requirements and technical specifications. It is typically presented in the form of a matrix, with customer needs listed on one axis and technical features on the other.
### Step 5: Implement and Test
Once the House of Quality is developed, the next step is to implement the changes in the manufacturing process. This involves making adjustments to ensure that the product meets the identified technical specifications. After implementation, thorough testing should be conducted to confirm that the product satisfies the customer requirements.
## Real-World Applications of QFD
### Automotive Industry
In the automotive industry, QFD is widely used to ensure that new car models meet customer expectations. By gathering feedback from potential buyers, manufacturers can design cars that offer the right combination of features, performance, and safety.
### Electronics Manufacturing
Electronics manufacturers use QFD to develop products like smartphones and laptops. By understanding what customers want in terms of functionality, design, and usability, these companies can create products that stand out in a competitive market.
### Healthcare Products
The healthcare industry also benefits from QFD by designing products that meet the specific needs of patients and healthcare providers. This can range from medical devices to pharmaceutical products, ensuring that they deliver the required performance and reliability.
## Challenges in Implementing QFD
### Time-Consuming Process
One of the main challenges of QFD is that it can be time-consuming. Gathering detailed customer requirements and translating them into technical specifications requires significant effort and resources.
### Resistance to Change
Implementing QFD may face resistance from team members who are accustomed to traditional methods. It requires a shift in mindset and may involve retraining staff to use new tools and techniques.
### Data Accuracy
The success of QFD depends on the accuracy of the customer data collected. Inaccurate or incomplete data can lead to incorrect assumptions and suboptimal product designs.
## Best Practices for Successful QFD Implementation
### Involve Cross-Functional Teams
To ensure a comprehensive understanding of customer needs, involve cross-functional teams in the QFD process. This includes representatives from marketing, design, engineering, and production.
### Use Reliable Data Sources
Collect data from multiple, reliable sources to ensure that the customer requirements are accurately captured. This includes direct feedback from customers, market research, and competitive analysis.
### Continual Improvement
QFD should not be a one-time exercise. Continually update and refine the process based on feedback and changing customer needs to ensure that products remain relevant and competitive.
### Utilize QFD Software
Consider using specialized QFD software to streamline the process. These tools can help in data collection, analysis, and visualization, making it easier to implement QFD effectively.
## Conclusion
Quality Function Deployment is a valuable methodology that can significantly enhance manufacturing processes. By focusing on customer requirements and translating them into actionable technical specifications, QFD ensures that products meet or exceed customer expectations. Despite the challenges in implementation, the benefits of improved communication, enhanced efficiency, and higher quality products make it an essential tool for any manufacturing company aiming for long-term success.
資料ダウンロード
QCD調達購買管理クラウド「newji」は、調達購買部門で必要なQCD管理全てを備えた、現場特化型兼クラウド型の今世紀最高の購買管理システムとなります。
ユーザー登録
調達購買業務の効率化だけでなく、システムを導入することで、コスト削減や製品・資材のステータス可視化のほか、属人化していた購買情報の共有化による内部不正防止や統制にも役立ちます。
NEWJI DX
製造業に特化したデジタルトランスフォーメーション(DX)の実現を目指す請負開発型のコンサルティングサービスです。AI、iPaaS、および先端の技術を駆使して、製造プロセスの効率化、業務効率化、チームワーク強化、コスト削減、品質向上を実現します。このサービスは、製造業の課題を深く理解し、それに対する最適なデジタルソリューションを提供することで、企業が持続的な成長とイノベーションを達成できるようサポートします。
オンライン講座
製造業、主に購買・調達部門にお勤めの方々に向けた情報を配信しております。
新任の方やベテランの方、管理職を対象とした幅広いコンテンツをご用意しております。
お問い合わせ
コストダウンが利益に直結する術だと理解していても、なかなか前に進めることができない状況。そんな時は、newjiのコストダウン自動化機能で大きく利益貢献しよう!
(Β版非公開)