- お役立ち記事
- Optimizing Molding Conditions to Prevent Weld Line Formation
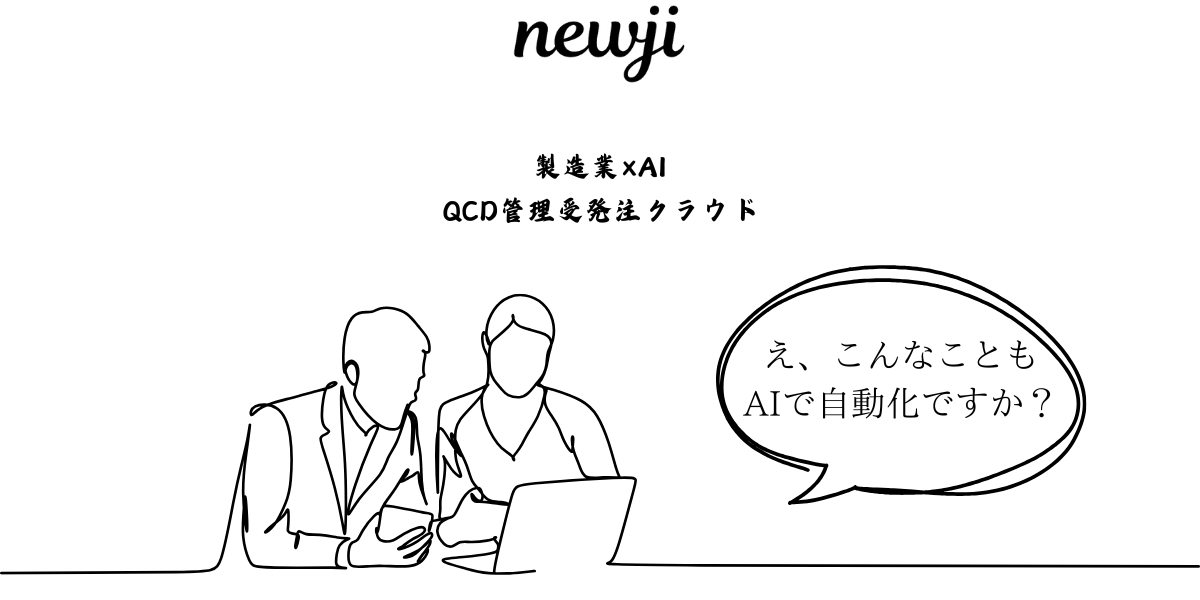
Optimizing Molding Conditions to Prevent Weld Line Formation
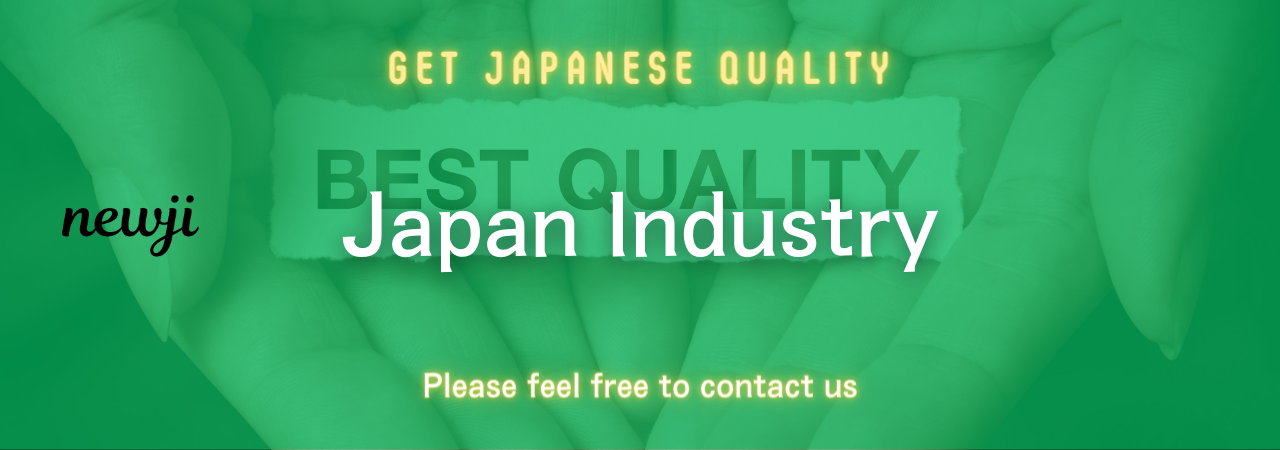
目次
Understanding Weld Lines in Injection Molding
Weld lines, sometimes referred to as knit lines, are common defects in injection molding processes.
These lines appear on the surface of a molded part, often resulting in both functional and aesthetic issues.
The formation of weld lines occurs when two or more flow fronts of molten material meet but do not bond perfectly.
This imperfect bonding can lead to weak spots in the final product, compromising structural integrity.
The presence of weld lines can also be problematic from a visual standpoint.
Parts that require a flawless finish, such as components used in consumer electronics or automotive interiors, can suffer from reduced value if weld lines are visible.
Understanding how and why weld lines form is the first step in optimizing molding conditions to mitigate this issue.
The Importance of Mold Design
One of the critical factors in preventing weld line formation is the design of the mold itself.
A well-designed mold ensures an even and consistent flow of material, reducing the likelihood of flow fronts meeting and forming weld lines.
The flow path should be carefully considered to minimize sharp angles or changes in direction, which can contribute to the formation of weld lines.
Gate location is another crucial aspect of mold design that can influence weld line formation.
Positioning gates strategically can control the flow of the material in such a way that weld lines are minimized or pushed to less critical areas of the part.
By assessing the mold design thoroughly before production begins, manufacturers can anticipate and address potential weld line issues.
Optimizing Process Parameters
In addition to mold design, optimizing process parameters is vital for preventing weld lines.
These parameters include the injection speed, pressure, and temperature of the material being molded.
Adjusting these settings can significantly impact the way material flows within the mold, helping to prevent the formation of weld lines.
For example, increasing the injection speed can help ensure that flow fronts meet with sufficient velocity to bond seamlessly.
However, it’s important to balance speed with other factors to avoid introducing new defects or complications.
Injection pressure is another critical parameter.
Increasing the pressure can help compact the material and promote better bonding at weld lines.
However, too much pressure can lead to flashing and other issues.
Material temperature plays a role as well.
Ensuring the material is at an optimal temperature promotes good flow and adequate bonding when flow fronts meet.
Finding the right combination of these parameters is key to preventing weld line formation.
Material Selection and Its Impact
The type of material used in injection molding can also influence weld line formation.
Different materials have varied flow characteristics and bonding properties, impacting how they behave within a mold.
Some materials are more prone to weld line formation due to their chemical composition or flow characteristics.
When selecting a material, consider its viscosity and melting temperature.
Materials with higher viscosity may flow less easily, leading to potential weld line issues.
Similarly, if the melting temperature is too high or low for a given process, it can affect flow and bonding.
Choosing the right material requires a thorough understanding of both the manufacturer’s needs and the material’s properties.
Collaborating with a materials engineer can provide valuable insights into selecting a material that minimizes weld line risk.
The Role of Additives
Additives play a significant role in modifying the properties of injection-molded parts, potentially influencing weld line formation.
Some additives are designed to enhance flow, improve the bonding of flow fronts, or increase the part’s overall strength.
Flow enhancers, for instance, help materials fill the mold more completely and aid proper weld line bonding.
In some cases, using an additive that promotes better bonding between flow fronts can improve the strength of weld lines, thereby mitigating their negative impact.
However, it is critical to evaluate how additives interact with the base material, as some may alter properties in undesirable ways.
Testing various formulations and additives in a controlled setting can help determine the best combination for preventing weld lines.
Continuous Improvement and Testing
Finally, preventing weld lines in molded parts requires a commitment to continuous improvement and testing.
Regularly evaluating current processes and outcomes allows manufacturers to identify areas where adjustments can be made for better results.
Implementing a testing phase for any changes in materials, mold designs, or process parameters helps predict how these factors will interact.
Conducting these tests in advance of full-scale production can help prevent costly mistakes and ensure high-quality, defect-free parts.
Incorporating feedback from production lines and operators can also provide valuable insights.
These team members often have first-hand experience with how changes affect production and can suggest practical improvements.
By leveraging both technology and team expertise, it’s possible to create a data-driven approach to optimize molding conditions, ultimately reducing or eliminating weld line formation.
Conclusion
Weld lines can pose significant challenges in injection molding, but with a comprehensive approach to mold design, process optimization, material selection, and the use of additives, these challenges can be mitigated effectively.
Understanding the factors that contribute to their formation is crucial for developing practical strategies to avoid them.
By investing in continuous improvement and maintaining a proactive stance on quality control, manufacturers can ensure that their molded parts meet the highest standards of strength and appearance, delivering superior products to their customers.
資料ダウンロード
QCD調達購買管理クラウド「newji」は、調達購買部門で必要なQCD管理全てを備えた、現場特化型兼クラウド型の今世紀最高の購買管理システムとなります。
ユーザー登録
調達購買業務の効率化だけでなく、システムを導入することで、コスト削減や製品・資材のステータス可視化のほか、属人化していた購買情報の共有化による内部不正防止や統制にも役立ちます。
NEWJI DX
製造業に特化したデジタルトランスフォーメーション(DX)の実現を目指す請負開発型のコンサルティングサービスです。AI、iPaaS、および先端の技術を駆使して、製造プロセスの効率化、業務効率化、チームワーク強化、コスト削減、品質向上を実現します。このサービスは、製造業の課題を深く理解し、それに対する最適なデジタルソリューションを提供することで、企業が持続的な成長とイノベーションを達成できるようサポートします。
オンライン講座
製造業、主に購買・調達部門にお勤めの方々に向けた情報を配信しております。
新任の方やベテランの方、管理職を対象とした幅広いコンテンツをご用意しております。
お問い合わせ
コストダウンが利益に直結する術だと理解していても、なかなか前に進めることができない状況。そんな時は、newjiのコストダウン自動化機能で大きく利益貢献しよう!
(Β版非公開)