- お役立ち記事
- Optimizing Molding Cycles and Injection Pressure to Prevent Weld Lines
月間76,176名の
製造業ご担当者様が閲覧しています*
*2025年3月31日現在のGoogle Analyticsのデータより
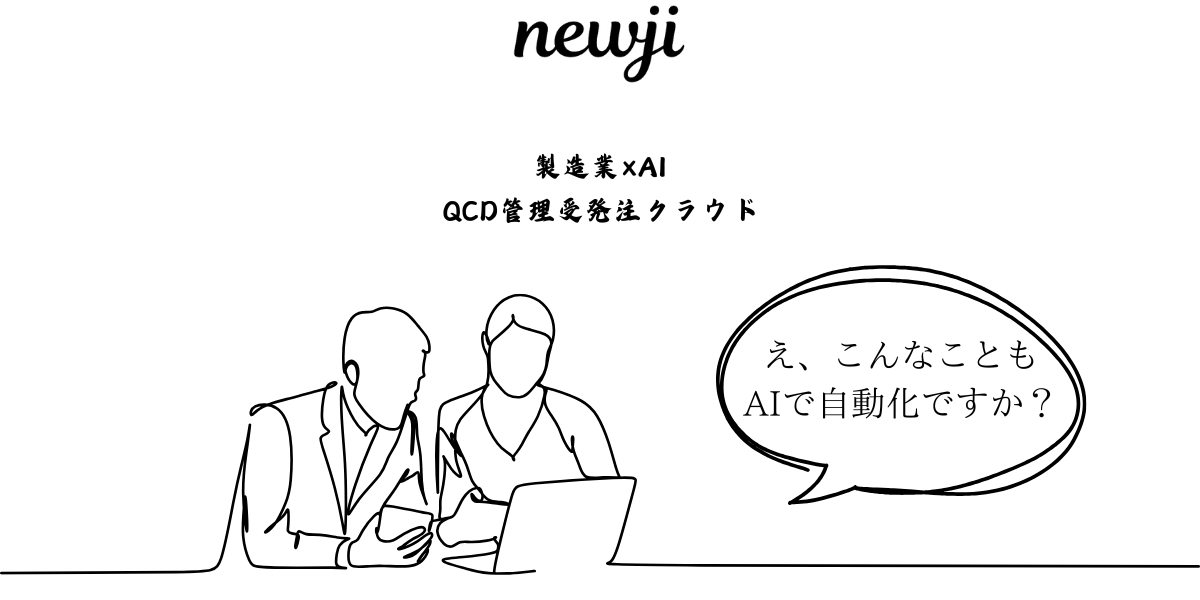
Optimizing Molding Cycles and Injection Pressure to Prevent Weld Lines
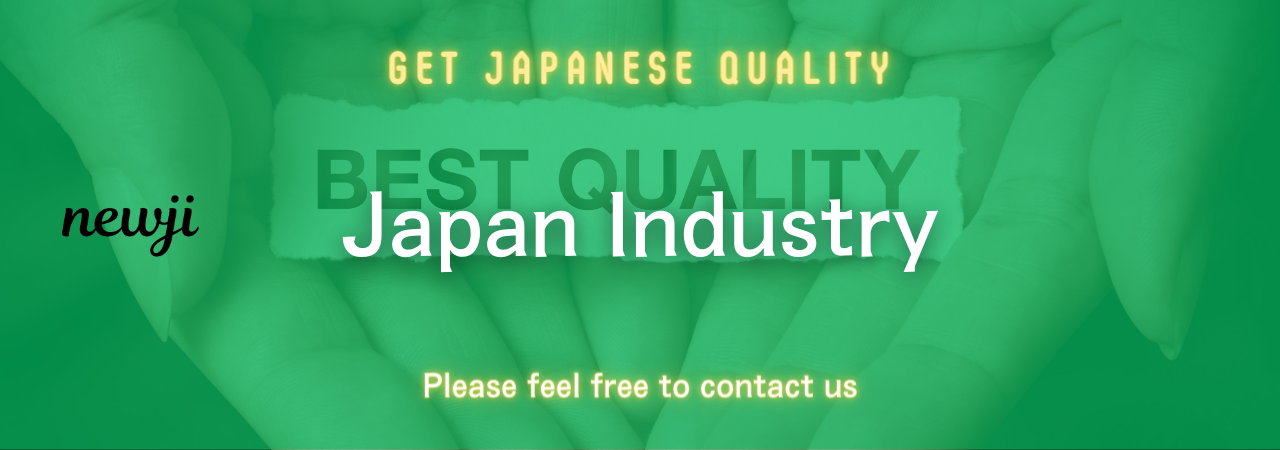
目次
Understanding Weld Lines in Injection Molding
Weld lines are a common defect in the injection molding process, which can compromise the quality and strength of the final product.
They occur when two or more flow fronts of molten plastic meet and do not fully fuse together, resulting in a visible line on the surface of the molded part.
These lines can lead to structural weaknesses, poor appearance, and reduce the mechanical properties of the component.
Understanding how to prevent these defects is crucial for producing high-quality plastic parts.
One effective method is by optimizing molding cycles and managing the injection pressure during the process.
The Importance of Molding Cycles
Molding cycles refer to the time it takes to complete one full cycle of the injection molding process, which includes injection, cooling, and ejection.
The optimization of these cycles is essential as it directly affects the efficiency, cost, and quality of the manufacturing process.
Adjusting the molding cycles can help in reducing or eliminating weld lines.
If the cycle is too short, the material may not have enough time to fill the mold properly, leading to incomplete fusion at the weld line.
Conversely, a cycle that is too long can cause excessive cooling of the molten material, resulting in weak weld lines due to inadequate bonding.
Adjusting Injection Temperature
The injection temperature plays a crucial role in managing weld lines.
Higher temperatures can improve the fluidity of the molten plastic, allowing it to meld together more completely at the weld points.
However, excessive temperatures can degrade the material, leading to other types of defects.
Therefore, it is important to find a balance that allows the plastic to remain molten enough for effective fusion without overheating.
Impact of Cooling Time
Cooling time is another vital factor to consider.
Proper cooling ensures that the molten plastic solidifies evenly and fully within the mold, reducing the risk of defects.
Adjusting the cooling time can help manage the temperature gradient across the mold, which influences the formation of weld lines.
Too short of a cooling time can lead to incomplete solidification, whereas a longer cooling time might increase the cycle time unnecessarily, affecting production efficiency.
Role of Injection Pressure
Injection pressure is a critical variable that influences the formation of weld lines.
It determines how the molten plastic flows into the mold and how well the material packs the cavity.
Insufficient pressure can result in incomplete filling, while excessive pressure can cause flash and stress within the part.
Both scenarios can lead to visible weld lines or other types of defects.
Balancing Flow Fronts
To prevent weld lines, it’s important to achieve a balanced flow front during the injection process.
This means ensuring that the molten plastic reaches all parts of the mold at the same time with equal speed and pressure.
Balancing the flow fronts prevents uneven cooling and merging of the plastic flow, reducing the risk of weld lines.
Gate Location and Design
The gate location and design also play a significant role in managing injection pressure and flow.
The gate is the part of the mold that introduces the plastic into the cavity, and its placement can affect how the plastic flows.
Strategically placing the gate can minimize the occurrence of weld lines by promoting a more controlled and even fill pattern.
Techniques to Optimize Molding Process
There are several techniques that manufacturers can employ to optimize the molding cycles and injection pressure to prevent weld lines.
These methods focus on fine-tuning various parameters to achieve the best possible molding conditions.
Simulation Software
Advanced simulation software can be used to model and predict the flow of plastic within the mold.
These tools can help in identifying potential problems related to weld lines and suggest modifications to the process parameters or mold design before actual production.
Proper Tool Maintenance
Regular maintenance of the molding tools is essential in preventing defects such as weld lines.
Ensuring that the mold surfaces are clean and free from wear or damage can help maintain the designed flow patterns and prevent irregularities during molding.
Process Monitoring and Control
Implementing real-time process monitoring and control systems allows for the detection and correction of deviations from the optimal settings.
These systems can adjust the injection pressure, temperature, and cycle times dynamically, improving the consistency and quality of the molded parts.
Conclusion
Preventing weld lines in injection molding is critical for producing high-quality plastic parts with desirable mechanical and aesthetic properties.
By optimizing molding cycles and carefully managing injection pressure, manufacturers can significantly reduce the occurrence of these defects.
Balancing injection temperature, adjusting cooling times, ensuring proper gate placement, and utilizing simulation software are effective strategies.
With continuous advancements in technology and an emphasis on precision and control, achieving weld-line-free plastic parts is a realistic and attainable goal.
資料ダウンロード
QCD管理受発注クラウド「newji」は、受発注部門で必要なQCD管理全てを備えた、現場特化型兼クラウド型の今世紀最高の受発注管理システムとなります。
ユーザー登録
受発注業務の効率化だけでなく、システムを導入することで、コスト削減や製品・資材のステータス可視化のほか、属人化していた受発注情報の共有化による内部不正防止や統制にも役立ちます。
NEWJI DX
製造業に特化したデジタルトランスフォーメーション(DX)の実現を目指す請負開発型のコンサルティングサービスです。AI、iPaaS、および先端の技術を駆使して、製造プロセスの効率化、業務効率化、チームワーク強化、コスト削減、品質向上を実現します。このサービスは、製造業の課題を深く理解し、それに対する最適なデジタルソリューションを提供することで、企業が持続的な成長とイノベーションを達成できるようサポートします。
製造業ニュース解説
製造業、主に購買・調達部門にお勤めの方々に向けた情報を配信しております。
新任の方やベテランの方、管理職を対象とした幅広いコンテンツをご用意しております。
お問い合わせ
コストダウンが利益に直結する術だと理解していても、なかなか前に進めることができない状況。そんな時は、newjiのコストダウン自動化機能で大きく利益貢献しよう!
(β版非公開)