- お役立ち記事
- Optimizing Process Control in Manufacturing with DCS (Distributed Control System)
月間77,185名の
製造業ご担当者様が閲覧しています*
*2025年2月28日現在のGoogle Analyticsのデータより
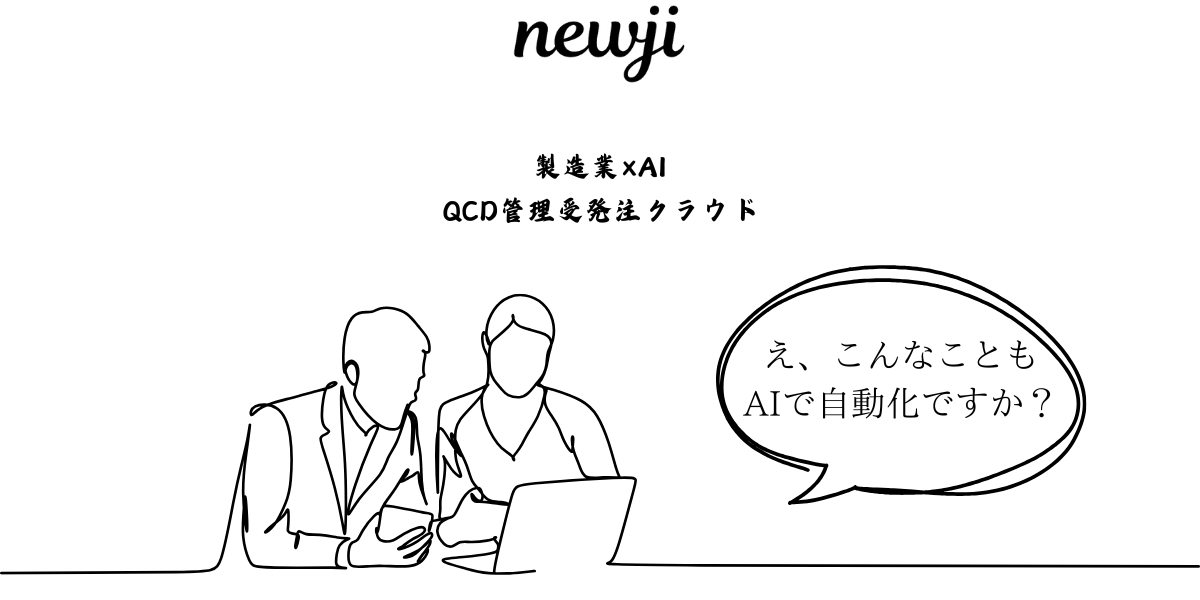
Optimizing Process Control in Manufacturing with DCS (Distributed Control System)
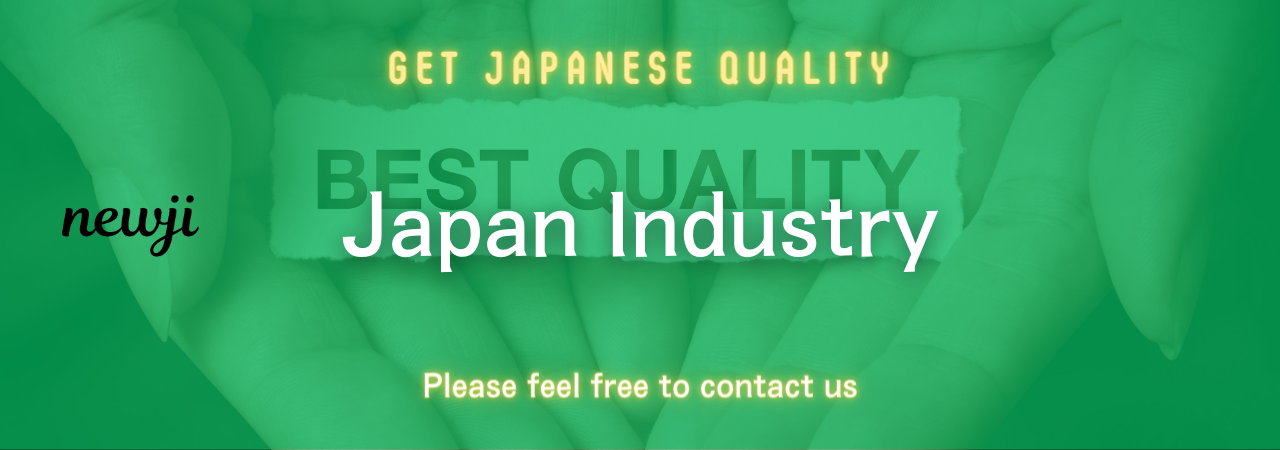
In today’s manufacturing landscape, ensuring optimal process control is crucial for maintaining efficiency, quality, and safety. One of the most effective strategies to achieve this is through the integration of DCS (Distributed Control System). This article will explore how DCS can enhance process control in manufacturing, making it easier for plants to produce high-quality products consistently.
目次
What is a Distributed Control System (DCS)?
A Distributed Control System (DCS) is an automated control system that monitors and manages various processes across a manufacturing plant. Unlike traditional centralized control systems, a DCS distributes control functions across multiple controllers. This approach provides enhanced reliability, scalability, and flexibility.
DCS systems are typically used in complex and large-scale applications such as chemical plants, oil refineries, and power generation facilities. By distributing control elements within the system, DCS minimizes the risk of total system failure since operations are not dependent on a single centralized unit.
The Core Components of a DCS
To fully understand how a DCS optimizes process control, it is essential to know its core components. A typical Distributed Control System comprises the following elements:
1. Controllers
Controllers are the brains of the DCS. They execute control algorithms and process input signals from field devices. Each controller can manage multiple loops, which allows for precise control of various process variables.
2. Human-Machine Interface (HMI)
The HMI is the interface through which operators interact with the DCS. It allows them to monitor system performance, adjust settings, and respond to alerts. A well-designed HMI is user-friendly, enabling operators to make quick and informed decisions.
3. Field Devices
Field devices include sensors, actuators, and other instruments that measure and control process variables like temperature, pressure, flow rate, and chemical concentration. These devices communicate with controllers to execute the necessary adjustments.
4. Communication Network
The communication network connects all the components of the DCS, facilitating seamless data exchange between controllers, HMIs, and field devices. A robust network ensures that information flows accurately and quickly, crucial for real-time process control.
Benefits of Implementing DCS
Several benefits make DCS a preferred choice for optimizing process control in manufacturing. These advantages collectively contribute to improved plant performance and operational efficiency.
1. Enhanced Reliability
With its decentralized architecture, DCS offers greater reliability. Even if one controller fails, the system continues to operate, minimizing the risk of downtime. This redundancy ensures continuous production.
2. Scalability
As manufacturing plants grow or diversify, their control needs may evolve. DCS is highly scalable, allowing for easy integration of new controllers and field devices. This flexibility ensures that the system can adapt to changing requirements without significant disruptions.
3. Improved Process Quality
DCS provides precise control over manufacturing processes, leading to consistent product quality. By maintaining optimal process conditions, DCS helps in reducing variations, ensuring that every batch meets the desired specifications.
4. Increased Safety
Safety is paramount in manufacturing environments. DCS enhances safety by providing real-time monitoring and alarm systems. Operators can quickly identify and address any anomalies, preventing accidents and ensuring a safe working environment.
5. Cost Efficiency
Optimized process control reduces energy consumption and minimizes waste, leading to significant cost savings. Moreover, by preventing unscheduled downtime, DCS helps avoid costly production halts and maintenance activities.
Applications of DCS in Manufacturing
DCS is versatile and can be applied across various industries to optimize process control. Here are some specific applications within manufacturing:
1. Chemical Industry
In chemical manufacturing, precise control of temperature, pressure, and chemical reactions is crucial. DCS allows for meticulous monitoring and adjustment, ensuring that chemical processes occur under optimal conditions. This not only enhances product quality but also improves safety by minimizing the risk of hazardous reactions.
2. Oil and Gas
The oil and gas industry involves complex processes such as refining and distillation. DCS helps manage these processes with high precision, ensuring efficient operation and maximizing output. It also enables real-time data analysis, facilitating predictive maintenance and reducing the likelihood of equipment failure.
3. Power Generation
Power plants require seamless integration of various subsystems to ensure reliable electricity production. DCS provides centralized control over the entire plant, optimizing performance and reducing operational costs. It also supports load shedding and demand response strategies, enhancing grid stability.
4. Food and Beverage
In the food and beverage industry, maintaining strict hygiene and quality standards is imperative. DCS ensures consistent control over temperature, flow, and pressure during production. This helps in meeting food safety regulations and producing high-quality consumables.
Implementing DCS for Optimal Results
Implementing a DCS involves careful planning and thorough understanding of the specific process requirements. Here are some steps to ensure successful DCS implementation:
1. Assess Needs
Start by assessing the specific needs of your manufacturing process. Identify the critical control points and determine the level of automation required. This will help in selecting the appropriate DCS architecture and components.
2. Design the System
Work with experts to design the DCS layout. Ensure that the system is scalable and flexible to accommodate future expansions. Consider redundancy and fail-safe mechanisms to enhance reliability.
3. Integration
Integrate the DCS with existing systems and field devices. Ensure seamless communication between all components to enable real-time data exchange. Pay attention to network security to protect against cyber threats.
4. Training
Train operators and maintenance personnel on the new system. Familiarize them with the HMI and control algorithms. Well-trained staff can leverage the full potential of the DCS, ensuring optimal process control.
5. Continuous Monitoring and Improvement
Once implemented, continuously monitor DCS performance. Use data analytics to identify areas of improvement and optimize control strategies. Regular maintenance and updates will ensure that the DCS remains efficient and reliable.
In conclusion, a Distributed Control System (DCS) is a powerful tool for optimizing process control in manufacturing. By offering enhanced reliability, scalability, and precision, DCS helps manufacturers achieve consistent product quality, increased safety, and cost efficiency. With proper implementation and continual monitoring, DCS can significantly improve the overall performance of manufacturing plants, setting the foundation for sustainable growth and innovation.
資料ダウンロード
QCD管理受発注クラウド「newji」は、受発注部門で必要なQCD管理全てを備えた、現場特化型兼クラウド型の今世紀最高の受発注管理システムとなります。
ユーザー登録
受発注業務の効率化だけでなく、システムを導入することで、コスト削減や製品・資材のステータス可視化のほか、属人化していた受発注情報の共有化による内部不正防止や統制にも役立ちます。
NEWJI DX
製造業に特化したデジタルトランスフォーメーション(DX)の実現を目指す請負開発型のコンサルティングサービスです。AI、iPaaS、および先端の技術を駆使して、製造プロセスの効率化、業務効率化、チームワーク強化、コスト削減、品質向上を実現します。このサービスは、製造業の課題を深く理解し、それに対する最適なデジタルソリューションを提供することで、企業が持続的な成長とイノベーションを達成できるようサポートします。
製造業ニュース解説
製造業、主に購買・調達部門にお勤めの方々に向けた情報を配信しております。
新任の方やベテランの方、管理職を対象とした幅広いコンテンツをご用意しております。
お問い合わせ
コストダウンが利益に直結する術だと理解していても、なかなか前に進めることができない状況。そんな時は、newjiのコストダウン自動化機能で大きく利益貢献しよう!
(β版非公開)