- お役立ち記事
- Optimizing Process Control in Manufacturing with DCS (Distributed Control System) Implementation
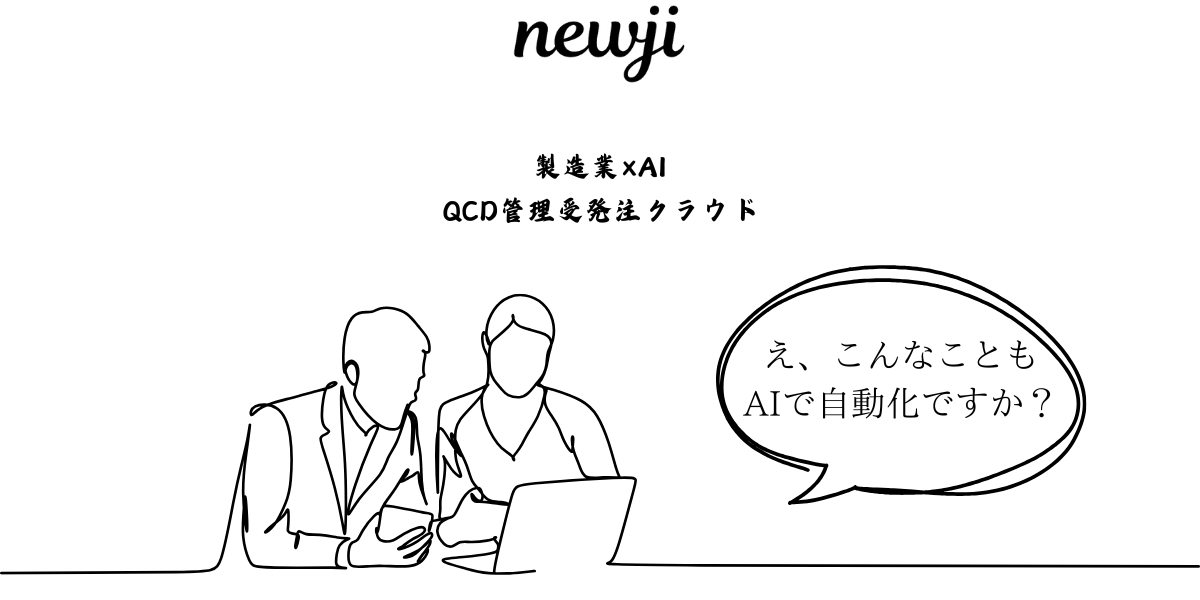
Optimizing Process Control in Manufacturing with DCS (Distributed Control System) Implementation
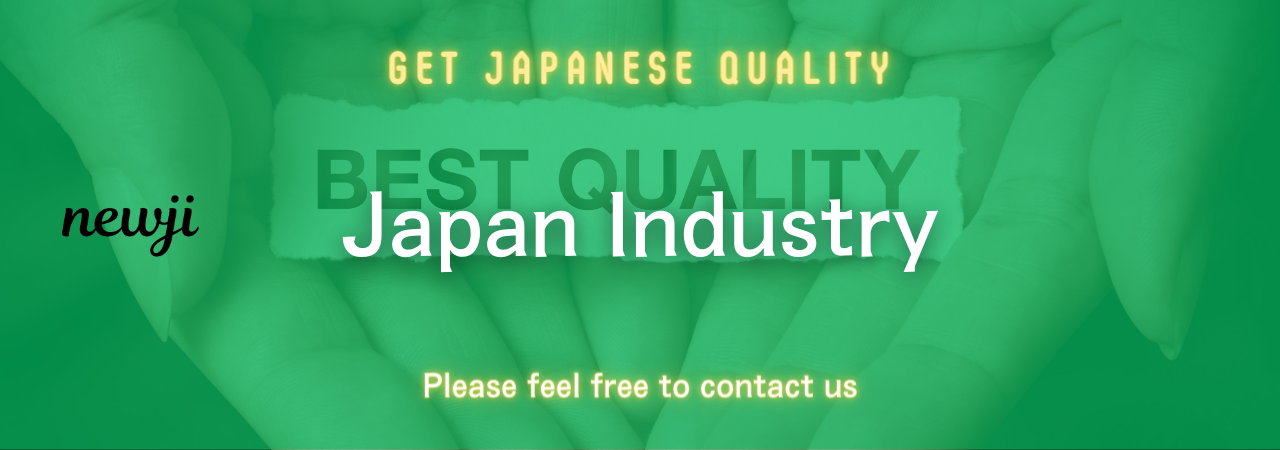
Distributed Control Systems (DCS) are playing a crucial role in modern manufacturing industries.
As technology advances, manufacturing firms consistently seek out methods to enhance their process control for optimal efficiency.
Implementing a DCS can substantially transform operations for the better, making the process smoother and more precise.
This article will explore the benefits of using a DCS in manufacturing, the key components of a DCS, and how to implement it effectively.
目次
Understanding Distributed Control Systems (DCS)
A Distributed Control System (DCS) is a type of automated control system that consists of distributed elements.
It connects various components such as controllers, sensors, and user interfaces in a manufacturing plant.
Unlike traditional control systems that rely on a single, centralized controller, a DCS uses multiple controllers.
Each of these is responsible for different processes, ensuring that even if one controller fails, the rest can continue to operate.
Advantages of Distributed Control Systems
The advantages of using a DCS in manufacturing are numerous:
1. **Increased Reliability**: By distributing control functions across several components, a DCS minimizes the risk of complete system failure.
2. **Improved Efficiency**: DCS systems can make real-time adjustments, ensuring the manufacturing process runs smoothly.
3. **Scalability**: DCS systems are easily scalable and can be expanded as the needs of the manufacturing process grow.
4. **Flexibility**: These systems are highly flexible and can be customized to suit specific manufacturing requirements.
Key Components of a DCS
A DCS consists of several core components which work together to optimize process control:
Controllers
Controllers are the brains of the system.
They collect data from sensors, process it based on set algorithms, and provide instructions to actuators or other machinery.
In a distributed system, multiple controllers ensure localized control, providing greater accuracy and reducing system overload.
Sensors
Sensors collect data from the environment or the process being controlled.
They can measure various parameters such as temperature, pressure, flow rate, and more.
This data is crucial for the controllers to make accurate decisions.
Human-Machine Interfaces (HMI)
HMIs are tools that allow operators to interact with the DCS.
They provide visual representations of the processes, making it easier to monitor and control.
Using an intuitive interface, operators can adjust settings, respond to alarms, and view real-time data.
Communication Networks
A robust communication network is essential for a DCS.
It ensures that data flows seamlessly between sensors, controllers, and HMIs.
High-speed and reliable networks are critical to handle the substantial volume of data generated and processed in real-time.
Implementing a DCS in Manufacturing
Successfully implementing a DCS in your manufacturing process requires careful planning and execution.
Here’s a guide on how to do it:
Assessment of Current Processes
Begin by thoroughly assessing your current manufacturing processes.
Identify the areas where you face the most challenges and evaluate the existing control systems.
This will help determine which parts of the process will benefit most from a DCS implementation.
Designing the System
Designing a DCS involves selecting the right controllers, sensors, and communication networks.
Work with experts to create a custom solution that meets your specific requirements.
Consider future scalability and flexibility in the design phase to ensure that the system can grow with your operations.
Installation and Integration
Once the system is designed, the next step is installation and integration.
This involves setting up sensors, controllers, and HMIs at appropriate locations within your facility.
Ensure that all components are properly integrated and communicate efficiently.
Testing the system extensively during this phase is crucial to identify and resolve any issues.
Training and Support
Training your staff is critical for the successful operation of a DCS.
Provide comprehensive training sessions on how to use the new system, interpret data, and respond to alerts.
Ongoing support and maintenance are also necessary to address any technical issues and keep the system running smoothly.
Challenges and Considerations
While the benefits of implementing a DCS are clear, there are challenges and considerations to keep in mind:
Initial Costs
Implementing a DCS can be expensive initially.
The costs of purchasing equipment, installation, and training can be significant.
However, the long-term benefits of increased efficiency and reduced downtime often outweigh these initial expenses.
Data Security
With increased connectivity and data flow, ensuring data security is paramount.
Implement robust cybersecurity measures to protect sensitive information from potential threats.
Change Management
Shifting from a traditional control system to a DCS can be a significant change.
Managing this transition carefully is essential.
Communicate the benefits clearly to all stakeholders and support them throughout the transition period.
Conclusion
Optimizing process control in manufacturing with DCS implementation is a smart move in the current technological landscape.
The increased reliability, efficiency, scalability, and flexibility of DCS make it an invaluable asset for modern manufacturing firms.
By carefully planning the implementation process, designing the system to meet specific needs, and providing comprehensive training and support, companies can reap the numerous benefits that a DCS offers.
Investing in a DCS today can lead to significant improvements in productivity and process control, positioning your manufacturing operations for future success.
資料ダウンロード
QCD調達購買管理クラウド「newji」は、調達購買部門で必要なQCD管理全てを備えた、現場特化型兼クラウド型の今世紀最高の購買管理システムとなります。
ユーザー登録
調達購買業務の効率化だけでなく、システムを導入することで、コスト削減や製品・資材のステータス可視化のほか、属人化していた購買情報の共有化による内部不正防止や統制にも役立ちます。
NEWJI DX
製造業に特化したデジタルトランスフォーメーション(DX)の実現を目指す請負開発型のコンサルティングサービスです。AI、iPaaS、および先端の技術を駆使して、製造プロセスの効率化、業務効率化、チームワーク強化、コスト削減、品質向上を実現します。このサービスは、製造業の課題を深く理解し、それに対する最適なデジタルソリューションを提供することで、企業が持続的な成長とイノベーションを達成できるようサポートします。
オンライン講座
製造業、主に購買・調達部門にお勤めの方々に向けた情報を配信しております。
新任の方やベテランの方、管理職を対象とした幅広いコンテンツをご用意しております。
お問い合わせ
コストダウンが利益に直結する術だと理解していても、なかなか前に進めることができない状況。そんな時は、newjiのコストダウン自動化機能で大きく利益貢献しよう!
(Β版非公開)