- お役立ち記事
- Optimizing Production Schedules Based on Time Analysis
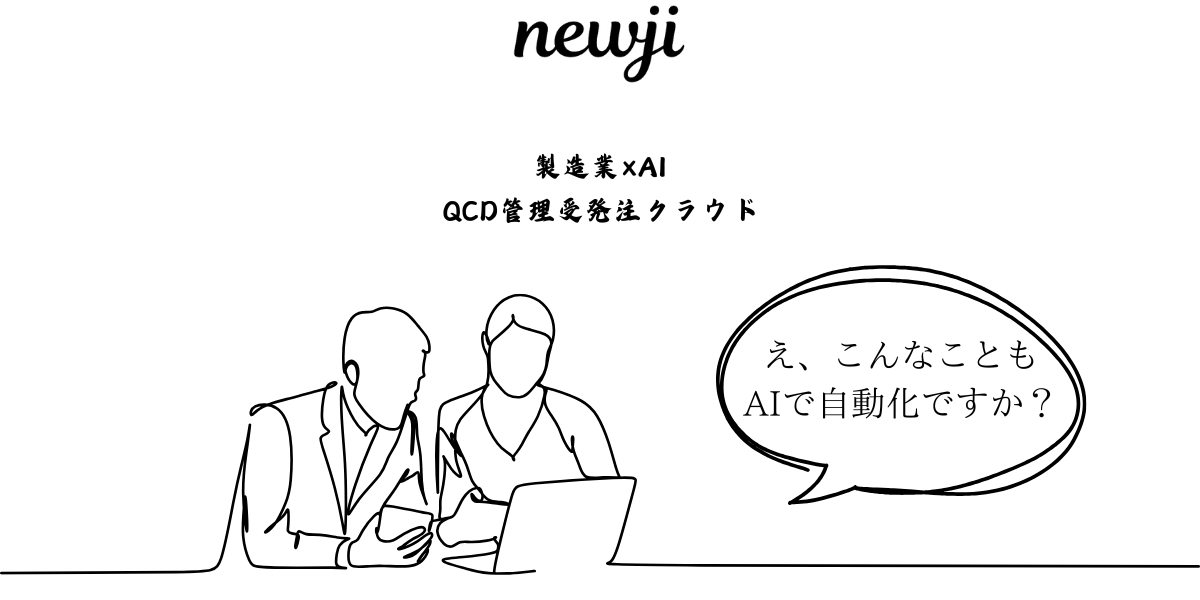
Optimizing Production Schedules Based on Time Analysis
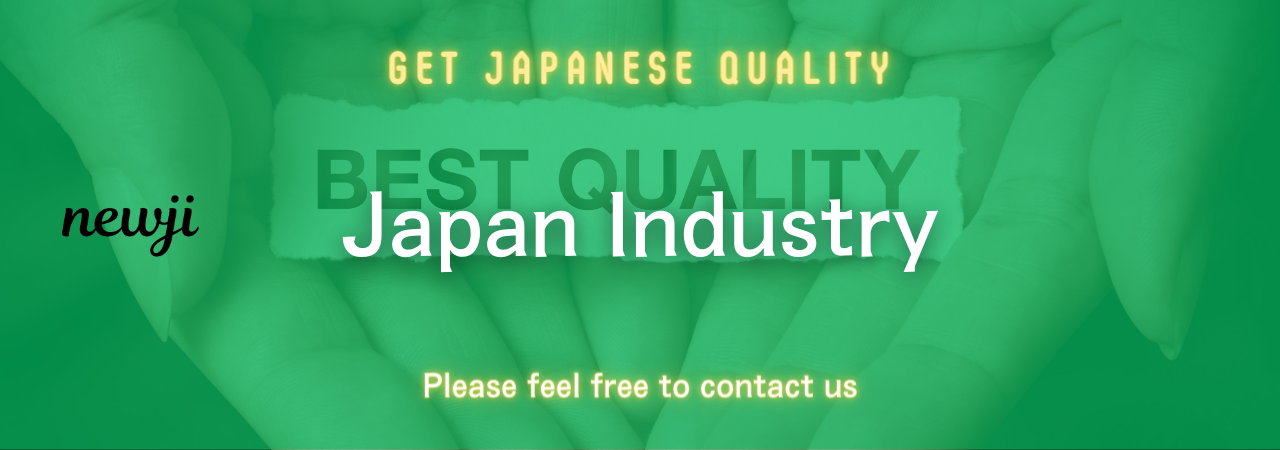
Optimizing production schedules based on time analysis plays a critical role in enhancing a company’s efficiency and profitability.
Knowing how to effectively manage time and resources ensures that production processes run smoothly, reducing delays and maximizing output.
In this article, we will delve into practical strategies for optimizing production schedules through time analysis.
目次
Understanding Time Analysis
Time analysis involves examining the various elements that make up production tasks and finding ways to streamline these processes.
A deep dive into the production timeline can reveal bottlenecks, inefficiencies, and opportunities for improvement.
This analysis helps businesses allocate resources more effectively, leading to better time management and overall productivity.
Components of Time Analysis
To optimize production schedules, it’s crucial to break down the tasks into manageable components.
Here are some elements to consider:
– Task Duration: Assess how long each task takes to complete.
– Resource Availability: Check the availability of machinery, labor, and materials.
– Task Dependency: Identify which tasks rely on the completion of others.
– Interruptions: Analyze the frequency and causes of disruptions.
Collecting Data for Time Analysis
The accuracy of your time analysis depends on the quality of data collected.
Rely on various data collection techniques for a comprehensive overview.
Methods for Data Collection
Deploy multiple methods to gather accurate data:
– Employee Feedback: Get insights from workers who are directly involved in the production process.
– Time Tracking Software: Use software tools to monitor how long tasks and projects take.
– Observational Studies: Conduct on-site observations to detect unrecorded downtime and inefficiencies.
Key Metrics to Track
Keep an eye on these crucial metrics:
– Cycle Time: The total time from the beginning to the end of a process.
– Lead Time: The duration from when an order is placed until it is fulfilled.
– Utilization Rates: The percentage of time resources are actively engaged in productive tasks.
Analyzing and Interpreting Data
Collecting data is just the first step.
The next involves analyzing this data to extract valuable insights.
Use statistical tools and software to make sense of the collected information.
Correlation analysis helps you know the relationship between different variables.
For instance, increased machine downtime might be linked to specific times of the day or certain tasks.
By identifying these relationships, you can schedule preventive maintenance during less busy times, reducing disruptions.
Identifying Bottlenecks
One of the main goals of time analysis is to identify bottlenecks.
Look for stages in the production process where tasks are frequently delayed.
Perform detailed root cause analyses to understand why these bottlenecks occur and how to address them effectively.
Implementing Optimized Production Schedules
Once you have analyzed your data, the next step is to implement optimized production schedules.
This step involves practical adjustments to the production timeline and resources.
Prioritizing Tasks
Prioritize tasks based on urgency and impact on overall production.
Use techniques such as the ABC analysis, which categorizes tasks into three groups: A (most important), B (moderately important), and C (least important).
Adjusting Resource Allocation
Allocate resources based on their availability and the demands of high-priority tasks.
Ensure that critical resources are accessible when needed to prevent delays.
Scheduling Regular Maintenance
Regular maintenance prevents unexpected breakdowns.
Schedule maintenance during off-peak hours to minimize disruptions.
Lean Manufacturing Principles
Incorporate lean manufacturing principles to eliminate waste.
Streamline processes to reduce waiting times and excessive movement.
Applying Just-in-Time (JIT) production can help in producing products only when they are needed, cutting down on overproduction.
Utilizing Technology
Technology plays a significant role in optimizing production schedules.
Utilize advanced software tools to automate scheduling and monitor progress in real time.
Production Management Software
Use production management software to create, manage, and adjust schedules efficiently.
These tools offer features like real-time tracking, resource management, and predictive analytics.
IoT and IIoT
Internet of Things (IoT) and Industrial Internet of Things (IIoT) devices can provide real-time data on machinery and processes.
Use these insights to adjust schedules on the fly and predict when maintenance is needed.
Cloud-Based Solutions
Implement cloud-based solutions for easy data access and collaboration.
These tools allow multiple teams to work together seamlessly, improving communication and coordination.
Monitoring and Continuous Improvement
The process of optimizing production schedules doesn’t end with implementation.
Continuous monitoring and regular reviews are essential.
Key Performance Indicators (KPIs)
Track KPIs to measure the effectiveness of your optimized schedules.
Important KPIs include overall equipment effectiveness (OEE), on-time delivery rate, and production cost per unit.
Regular Audits and Reviews
Conduct regular audits to ensure compliance with optimized schedules.
Reviews help in identifying any deviations and making necessary adjustments.
Feedback Mechanisms
Establish feedback mechanisms to gather input from employees.
Their on-ground insights can offer practical solutions for ongoing improvements.
The Benefits of Optimized Production Schedules
Optimizing production schedules offers numerous benefits to a business:
– Increased Efficiency: Reduce idle times and make the most of available resources.
– Cost Savings: Minimize waste and lower production costs.
– Improved Quality: Regular maintenance and streamlined processes lead to higher product quality.
– Enhanced Customer Satisfaction: Timely deliveries and high-quality products improve customer satisfaction.
By following these strategies for optimizing production schedules based on time analysis, you can ensure smoother operations and achieve better results.
資料ダウンロード
QCD調達購買管理クラウド「newji」は、調達購買部門で必要なQCD管理全てを備えた、現場特化型兼クラウド型の今世紀最高の購買管理システムとなります。
ユーザー登録
調達購買業務の効率化だけでなく、システムを導入することで、コスト削減や製品・資材のステータス可視化のほか、属人化していた購買情報の共有化による内部不正防止や統制にも役立ちます。
NEWJI DX
製造業に特化したデジタルトランスフォーメーション(DX)の実現を目指す請負開発型のコンサルティングサービスです。AI、iPaaS、および先端の技術を駆使して、製造プロセスの効率化、業務効率化、チームワーク強化、コスト削減、品質向上を実現します。このサービスは、製造業の課題を深く理解し、それに対する最適なデジタルソリューションを提供することで、企業が持続的な成長とイノベーションを達成できるようサポートします。
オンライン講座
製造業、主に購買・調達部門にお勤めの方々に向けた情報を配信しております。
新任の方やベテランの方、管理職を対象とした幅広いコンテンツをご用意しております。
お問い合わせ
コストダウンが利益に直結する術だと理解していても、なかなか前に進めることができない状況。そんな時は、newjiのコストダウン自動化機能で大きく利益貢献しよう!
(Β版非公開)