- お役立ち記事
- Optimizing Screw Design in Extrusion Molding
Optimizing Screw Design in Extrusion Molding
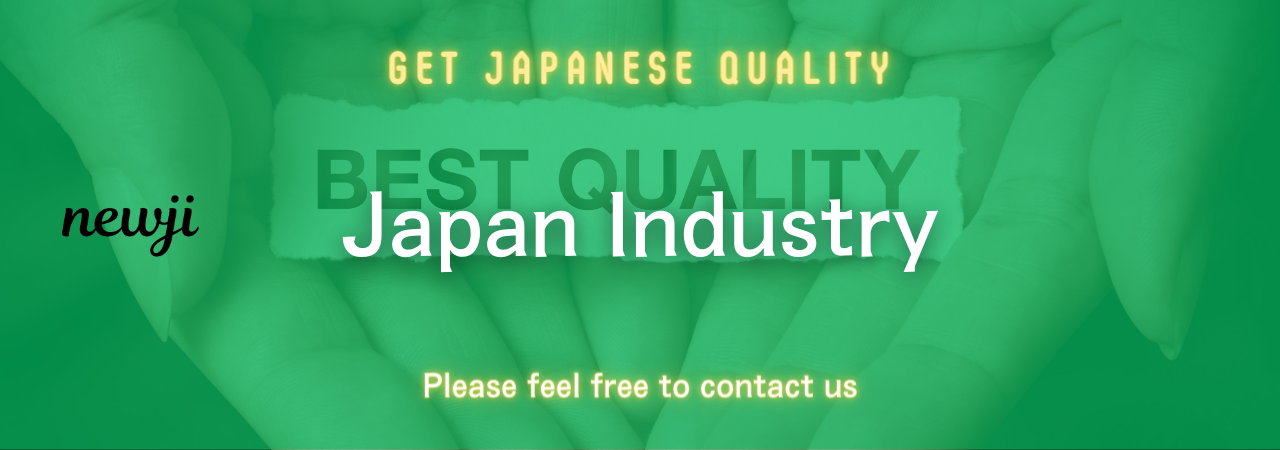
Extrusion molding is a widely used manufacturing process that forms plastic materials into continuous shapes like tubes, pipes, and profiles.
An essential element in the effectiveness of this process is the screw design.
Optimizing screw design in extrusion molding can significantly impact the efficiency, quality, and speed of production.
This article delves into the factors that contribute to an optimized screw design and how it can benefit the extrusion process.
目次
What is Extrusion Molding?
Extrusion molding is a process in which raw plastic material is melted and formed into a continuous profile.
A plastic resin is fed through a hopper into a heated barrel, where it is melted.
The melted plastic is then pushed through a die, forming a continuous shape that is cooled and cut to desired lengths.
The Importance of Screw Design in Extrusion
The screw is a critical component in the extrusion process, as it helps in the melting, mixing, and pressurizing of the plastic material.
An optimized screw design ensures efficient plasticization, uniform mixing, and consistent output.
Without an optimized screw, manufacturers may encounter issues like poor melting performance, inconsistent product quality, and reduced productivity.
Melting Performance
The screw design impacts how fast and evenly the plastic resin melts.
A well-designed screw will facilitate a homogeneous melt, reducing the chances of unmelted polymer particles that may degrade product quality.
Uniform Mixing
The screw must also efficiently mix the melted plastic to achieve uniform color and consistency.
Inadequate mixing can result in poor-quality products with visible defects.
Consistent Output
An optimized screw design ensures a consistent output of the extruded material.
This leads to a smoother production process, reducing the likelihood of machine downtime and increasing overall productivity.
Factors to Consider in Screw Design
There are several factors to consider when optimizing screw design for extrusion molding.
Understanding these factors can help in achieving the best possible performance from the extruder.
Flight Depth and Width
The flight depth and width of the screw are crucial in determining the rate of material conveyance.
The flights are the screw’s helical threads that push the plastic resin through the barrel.
Increasing the flight depth can enhance the material throughput but may also require more power.
Similarly, the width of the flight should be balanced to ensure efficient material conveyance.
Compression Ratio
The compression ratio is the ratio of the channel depth in the feed zone to the channel depth in the metering zone.
A higher compression ratio means more pressure, which aids in better melting and mixing of the plastic resin.
However, too high a compression ratio can lead to excessive shear stress, degrading the material quality.
Screw Speed
The rotational speed of the screw affects the shear rate and heat generation in the barrel.
Higher screw speeds can increase material throughput but may also lead to overheating and thermal degradation of the plastic resin.
Balancing screw speed with other design factors is essential for optimal performance.
Types of Extrusion Screws
There are various types of screws designed for specific extrusion applications.
Choosing the right type of screw can significantly enhance the efficiency and quality of the extrusion process.
Single-Flight Screws
These are the most common type of screws used in extrusion molding.
They are simple in design and generally effective for a wide range of plastic materials.
Barrier Screws
Barrier screws are designed with an additional barrier flight that separates the melted resin from unmelted particles.
This design ensures a consistent and homogeneous melt, making it ideal for processing complex and hard-to-melt materials.
Mixing Screws
Mixing screws have specialized mixing sections that enhance the blending of additives, colors, and fillers within the plastic resin.
They are particularly useful for applications requiring a high degree of material homogeneity.
Vented Screws
Vented screws have a venting section that allows trapped gases and moisture to escape from the melted plastic resin.
This design is especially useful for materials that release gases during melting, such as foamed plastics.
Benefits of Optimizing Screw Design
Optimizing screw design in extrusion molding offers several advantages that can substantially improve the production process.
Increased Efficiency
A well-optimized screw design can increase the throughput of the extruder, allowing for more efficient production cycles.
This leads to lower energy consumption and reduced production costs.
Enhanced Product Quality
An optimized screw ensures uniform melting, mixing, and pressurization of the plastic resin.
This results in higher-quality products with fewer defects and inconsistencies.
Reduced Downtime
With a consistent and efficient extrusion process, machine downtime due to clogging, inconsistencies, or poor material handling is minimized.
This leads to smoother production runs and higher overall productivity.
Versatility
Optimized screw designs can easily accommodate a wide variety of plastic materials and additives.
This versatility allows manufacturers to meet diverse production requirements without frequent screw changes.
Conclusion
Optimizing screw design in extrusion molding is crucial for achieving efficient, consistent, and high-quality production.
Key factors like flight depth, compression ratio, and screw speed play essential roles in determining the screw’s performance.
By understanding and implementing the right screw design, manufacturers can reap substantial benefits, including increased efficiency, enhanced product quality, reduced downtime, and versatile production capabilities.
Employing an optimized screw design is an investment that pays for itself many times over through improved productivity and product quality.
資料ダウンロード
QCD調達購買管理クラウド「newji」は、調達購買部門で必要なQCD管理全てを備えた、現場特化型兼クラウド型の今世紀最高の購買管理システムとなります。
ユーザー登録
調達購買業務の効率化だけでなく、システムを導入することで、コスト削減や製品・資材のステータス可視化のほか、属人化していた購買情報の共有化による内部不正防止や統制にも役立ちます。
NEWJI DX
製造業に特化したデジタルトランスフォーメーション(DX)の実現を目指す請負開発型のコンサルティングサービスです。AI、iPaaS、および先端の技術を駆使して、製造プロセスの効率化、業務効率化、チームワーク強化、コスト削減、品質向上を実現します。このサービスは、製造業の課題を深く理解し、それに対する最適なデジタルソリューションを提供することで、企業が持続的な成長とイノベーションを達成できるようサポートします。
オンライン講座
製造業、主に購買・調達部門にお勤めの方々に向けた情報を配信しております。
新任の方やベテランの方、管理職を対象とした幅広いコンテンツをご用意しております。
お問い合わせ
コストダウンが利益に直結する術だと理解していても、なかなか前に進めることができない状況。そんな時は、newjiのコストダウン自動化機能で大きく利益貢献しよう!
(Β版非公開)