- お役立ち記事
- Optimizing temperature distribution in electric furnaces and improving energy efficiency at manufacturing sites
月間77,185名の
製造業ご担当者様が閲覧しています*
*2025年2月28日現在のGoogle Analyticsのデータより
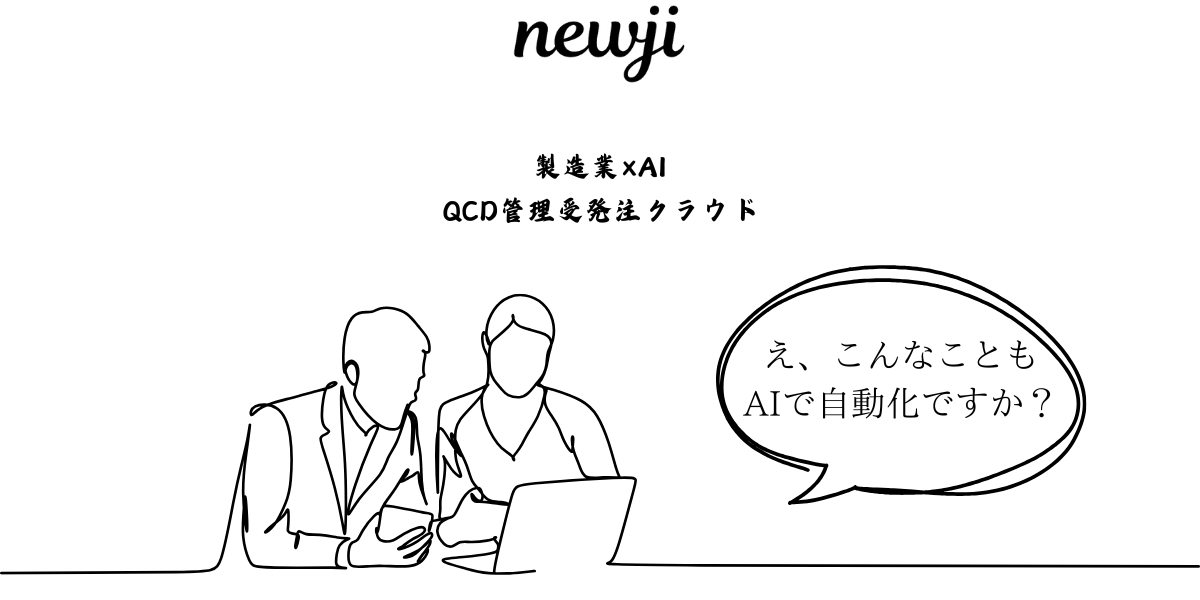
Optimizing temperature distribution in electric furnaces and improving energy efficiency at manufacturing sites
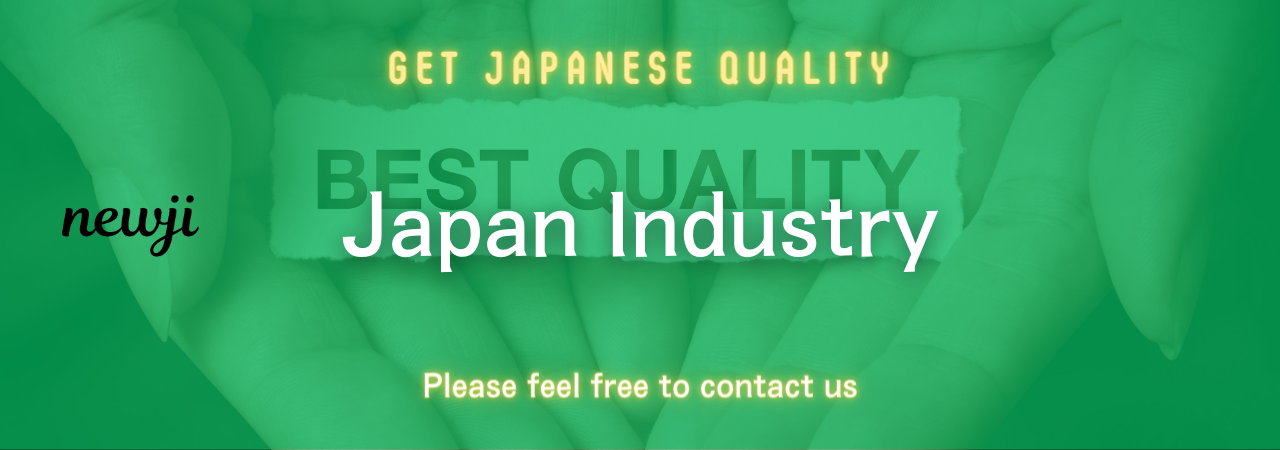
目次
The Importance of Temperature Distribution in Electric Furnaces
Electric furnaces play a crucial role in various manufacturing processes, from metal production to glassmaking.
One of the key factors that influence the quality of the output and energy consumption in these furnaces is temperature distribution.
Ensuring optimal temperature distribution is essential for improving the efficiency and effectiveness of manufacturing operations.
An even temperature distribution helps maintain consistent product quality while reducing waste and energy consumption.
The Basics of Temperature Distribution
Temperature distribution refers to how heat is distributed within an electric furnace.
Achieving an even temperature distribution ensures that the entire furnace operates uniformly, preventing hot spots or cold areas.
If the temperature is not evenly distributed, some parts of the material being processed may not reach the necessary temperature, leading to defects in the final product.
Factors Affecting Temperature Distribution
Several factors influence the temperature distribution in electric furnaces:
– **Furnace Design**: The design of the furnace, including its insulation and heating elements, plays a significant role in how heat is distributed.
A well-designed furnace will facilitate better heat circulation.
– **Material Properties**: The thermal properties of the material being processed can affect how heat is absorbed and distributed.
Different materials may require specific temperature settings and control mechanisms.
– **Heating Elements**: The type and arrangement of heating elements within the furnace can impact temperature distribution.
Uniform placement and efficient operation of these elements are crucial for balanced heat distribution.
– **Airflow and Ventilation**: Proper airflow and ventilation within the furnace ensure that heat is evenly dispersed throughout.
Any obstructions or inadequate ventilation can lead to uneven temperatures.
Improving Energy Efficiency in Electric Furnaces
Energy efficiency is a primary concern for manufacturing sites aiming to reduce operational costs and environmental impacts.
Electric furnaces can be optimized for energy efficiency through several methods.
Using Advanced Control Systems
Modern electric furnaces often incorporate advanced control systems that precisely manage and monitor temperature.
These systems can automatically adjust settings to maintain optimal conditions, ensuring energy is not wasted.
By using sensors and feedback mechanisms, these control systems help achieve consistent temperature distribution and reduce energy consumption.
Regular Maintenance and Upgrades
Regular maintenance of electric furnaces is crucial for ensuring their efficiency.
Cleaning heating elements, checking for component wear and tear, and ensuring proper insulation can significantly improve performance.
Upgrading outdated components with energy-efficient alternatives can also contribute to better energy conservation.
Insulation Improvements
Effective insulation minimizes heat loss, which is a major factor in energy efficiency.
Improving the insulation of electric furnaces helps retain heat within the chamber, reducing the energy required to maintain desired temperatures.
This leads to lower energy bills and a smaller carbon footprint.
Optimizing Operating Schedules
Aligning furnace operation schedules with production demands can enhance energy efficiency.
Running electric furnaces only when necessary and during off-peak energy times can lower energy consumption and operational costs.
Scheduling regular downtimes for inspections and maintenance can prevent unexpected breakdowns that often result in inefficient energy use.
Benefits of Optimized Temperature and Energy Efficiency
Achieving optimized temperature distribution and energy efficiency in electric furnaces offers numerous benefits:
– **Improved Product Quality**: Consistent temperature distribution leads to better product uniformity, reducing defects and enhancing quality.
– **Reduced Energy Costs**: Efficient energy use translates to lower operational costs, contributing to higher profitability.
– **Environmental Impact**: Energy-efficient operations lower the environmental footprint by reducing carbon emissions and energy waste.
– **Extended Equipment Life**: Regular maintenance and optimal operating conditions increase the lifespan of electric furnaces, saving costs on frequent replacements.
– **Competitive Advantage**: Companies that optimize their manufacturing processes can offer higher-quality products with lower production costs, gaining an edge in the market.
Conclusion
Optimizing temperature distribution and improving energy efficiency in electric furnaces are fundamental steps for any manufacturing site aiming to enhance operations.
By focusing on advanced control systems, regular maintenance, insulation improvements, and strategic operation scheduling, manufacturers can achieve significant cost savings and environmental benefits.
These improvements not only enhance product quality but also contribute to the long-term sustainability of manufacturing operations.
Implementing these strategies ensures that manufacturing sites remain competitive while aligning with global energy conservation efforts.
資料ダウンロード
QCD管理受発注クラウド「newji」は、受発注部門で必要なQCD管理全てを備えた、現場特化型兼クラウド型の今世紀最高の受発注管理システムとなります。
ユーザー登録
受発注業務の効率化だけでなく、システムを導入することで、コスト削減や製品・資材のステータス可視化のほか、属人化していた受発注情報の共有化による内部不正防止や統制にも役立ちます。
NEWJI DX
製造業に特化したデジタルトランスフォーメーション(DX)の実現を目指す請負開発型のコンサルティングサービスです。AI、iPaaS、および先端の技術を駆使して、製造プロセスの効率化、業務効率化、チームワーク強化、コスト削減、品質向上を実現します。このサービスは、製造業の課題を深く理解し、それに対する最適なデジタルソリューションを提供することで、企業が持続的な成長とイノベーションを達成できるようサポートします。
製造業ニュース解説
製造業、主に購買・調達部門にお勤めの方々に向けた情報を配信しております。
新任の方やベテランの方、管理職を対象とした幅広いコンテンツをご用意しております。
お問い合わせ
コストダウンが利益に直結する術だと理解していても、なかなか前に進めることができない状況。そんな時は、newjiのコストダウン自動化機能で大きく利益貢献しよう!
(β版非公開)