- お役立ち記事
- Optimizing the Product Development Process in Manufacturing
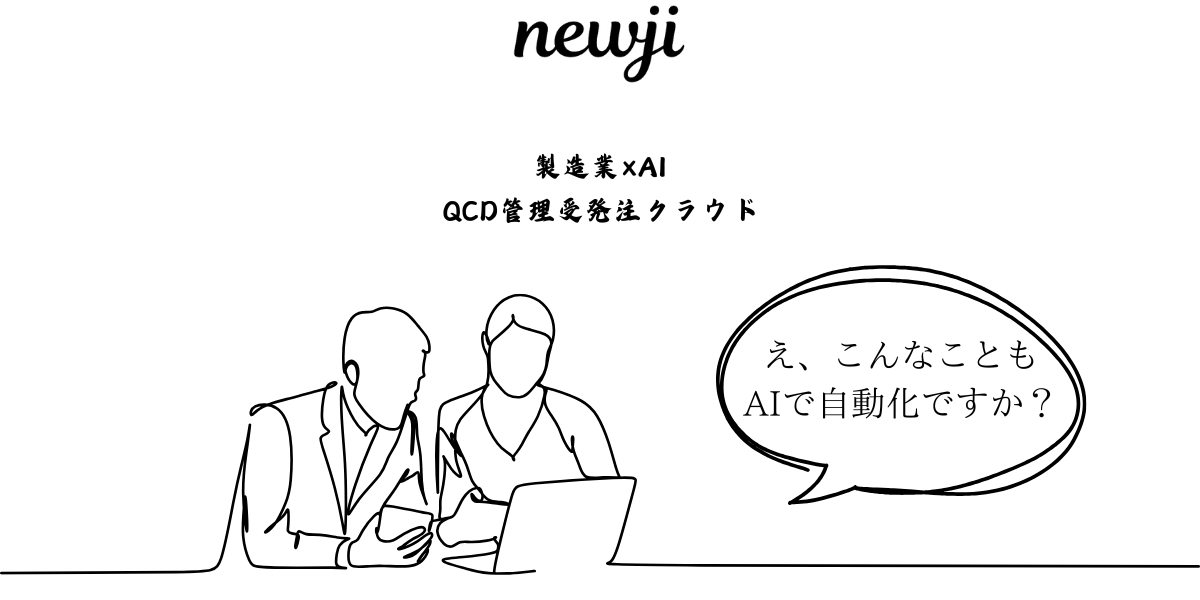
Optimizing the Product Development Process in Manufacturing
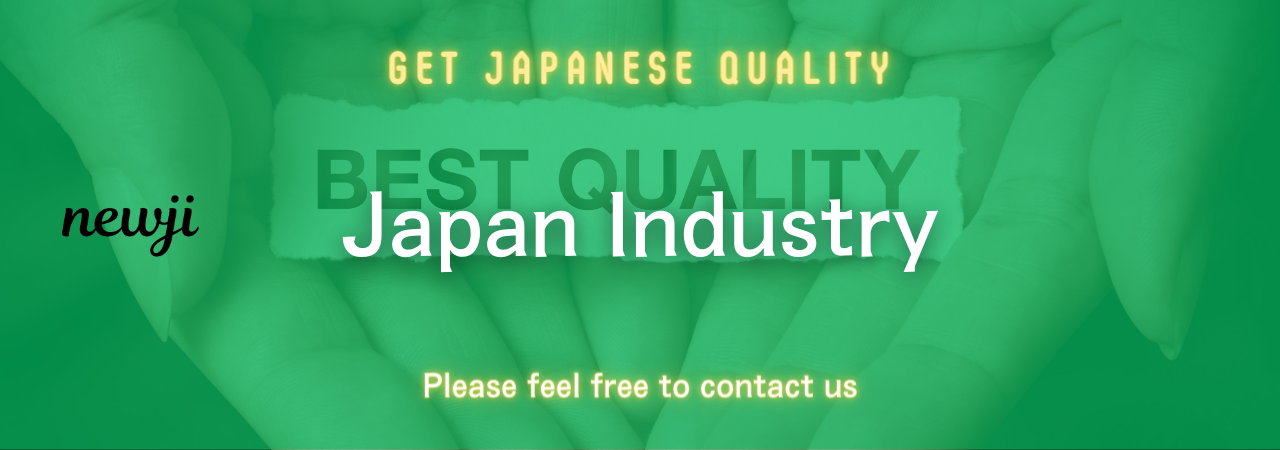
目次
Understanding Product Development in Manufacturing
The product development process in manufacturing is a crucial journey that begins with an idea and ends with the final product.
It involves multiple stages, from conceptualization to market release, each requiring careful attention and execution.
By streamlining these phases, manufacturers can enhance efficiency, reduce costs, and improve product quality.
The aim is to foster innovation while ensuring that the product meets market demands and regulatory standards.
Key Stages of the Product Development Process
1. Ideation and Conceptualization
Ideation is the first step where all potential ideas are generated.
This stage often involves brainstorming sessions and market analysis to identify gaps and opportunities.
Conceptualization follows, where viable ideas are further developed into workable concepts.
2. Feasibility Study
At this point, a feasibility study is conducted to evaluate the technical and financial aspects of the concept.
This involves assessing the resources required, potential costs, and the expected return on investment.
The goal is to determine whether the concept is viable and worth pursuing.
3. Design and Prototyping
Once a concept clears the feasibility study, the design phase begins.
Engineers and designers create detailed drawings and specifications for prototypes.
Prototyping is a critical step as it allows for testing and refinement before moving to mass production.
4. Production Planning
Production planning involves outlining the entire manufacturing process.
This includes selecting materials, defining the production timeline, and allocating resources.
Efficient planning ensures that production runs smoothly and meets deadlines.
5. Testing and Validation
Before a product is launched, it undergoes rigorous testing to ensure it meets all quality and safety standards.
This phase may include stress tests, compliance checks, and user feedback.
Validation guarantees that the product performs as expected in real-world conditions.
6. Launch and Market Introduction
The final stage is launching the product into the market.
This involves marketing strategies, distribution plans, and monitoring the product’s performance after launch.
Post-launch evaluations help identify areas for improvement and inform future product developments.
Best Practices for Optimizing Product Development
1. Collaborative Approach
Promote collaboration among different departments such as design, engineering, marketing, and finance.
This interdisciplinary approach ensures that all aspects of the product are considered, which can lead to innovative solutions and a more cohesive final product.
2. Embrace Technology
Utilize advanced technologies such as computer-aided design (CAD) and 3D printing for more efficient design and prototyping.
Automation and digital tools can significantly reduce the development time and increase accuracy.
3. Agile Methodology
Adopt an agile methodology, which focuses on iterative development and continuous feedback.
This approach allows for adjustments and improvements to be made throughout the development process rather than waiting until the end.
4. Effective Communication
Ensure clear and consistent communication among all team members.
Regular updates, meetings, and collaborative platforms can help keep everyone on the same page and reduce misunderstandings.
5. Risk Management
Identify potential risks early in the development process and devise strategies to mitigate them.
Having contingency plans in place can prevent delays and cost overruns.
The Role of Lean Manufacturing in Product Development
Lean manufacturing principles aim to minimize waste and maximize value, which can significantly benefit the product development process.
One core principle is to focus on what adds value from the customer’s perspective and eliminate anything that does not.
Continuous improvement (Kaizen) and Just-In-Time (JIT) production are key components of lean manufacturing that can increase efficiency and enhance product quality.
Applying these principles can lead to more streamlined processes and a more responsive production environment.
Case Study: Successful Product Development Optimization
Let’s look at a hypothetical example.
A company manufacturing wearable fitness devices wanted to launch a new product.
By implementing a collaborative approach and utilizing CAD software, they improved their design accuracy.
They adopted agile methodologies, allowing them to make iterative improvements based on user feedback during the prototyping phase.
By practicing effective communication and risk management, they identified potential issues early on and addressed them without significant delays.
Finally, by applying lean manufacturing principles, they reduced waste and optimized their production process.
The result was a high-quality product delivered on time and within budget.
The Impact of a Well-Optimized Product Development Process
Optimizing the product development process can have far-reaching impacts.
It can lead to faster time-to-market, which is crucial in industries where being first can provide a significant competitive advantage.
Cost savings from improved efficiency and reduced waste can increase profitability.
Moreover, high-quality products that meet or exceed customer expectations can enhance brand reputation and customer loyalty.
In essence, a well-optimized product development process can create a cycle of continuous improvement, innovation, and sustained success.
Conclusion
In the dynamic field of manufacturing, optimizing the product development process is essential for maintaining competitiveness and fostering growth.
By understanding and refining each stage, embracing technology, and staying committed to best practices, manufacturers can create superior products that resonate with the market.
The journey from idea to product is complex, but with the right strategies in place, it can be both efficient and rewarding.
資料ダウンロード
QCD調達購買管理クラウド「newji」は、調達購買部門で必要なQCD管理全てを備えた、現場特化型兼クラウド型の今世紀最高の購買管理システムとなります。
ユーザー登録
調達購買業務の効率化だけでなく、システムを導入することで、コスト削減や製品・資材のステータス可視化のほか、属人化していた購買情報の共有化による内部不正防止や統制にも役立ちます。
NEWJI DX
製造業に特化したデジタルトランスフォーメーション(DX)の実現を目指す請負開発型のコンサルティングサービスです。AI、iPaaS、および先端の技術を駆使して、製造プロセスの効率化、業務効率化、チームワーク強化、コスト削減、品質向上を実現します。このサービスは、製造業の課題を深く理解し、それに対する最適なデジタルソリューションを提供することで、企業が持続的な成長とイノベーションを達成できるようサポートします。
オンライン講座
製造業、主に購買・調達部門にお勤めの方々に向けた情報を配信しております。
新任の方やベテランの方、管理職を対象とした幅広いコンテンツをご用意しております。
お問い合わせ
コストダウンが利益に直結する術だと理解していても、なかなか前に進めることができない状況。そんな時は、newjiのコストダウン自動化機能で大きく利益貢献しよう!
(Β版非公開)