- お役立ち記事
- Optimizing the purchase order process: methods for delivery management and cost efficiency
Optimizing the purchase order process: methods for delivery management and cost efficiency
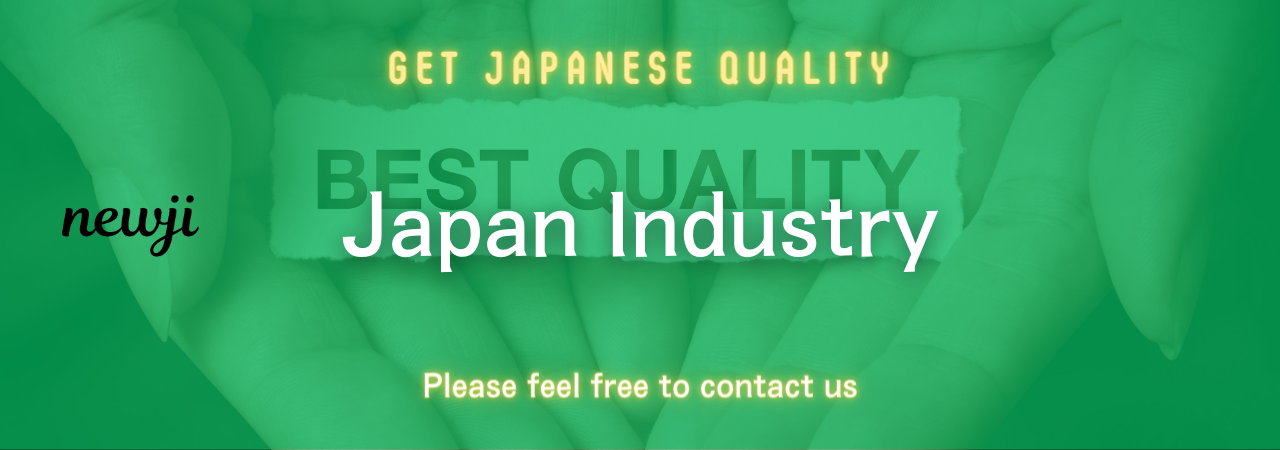
In today’s competitive business world, optimizing your purchase order process is not just important, it’s essential. Proper management of delivery times and costs can make a huge difference in the effectiveness and success of a company. This article will explore effective methods for delivery management and cost efficiency in the purchase order process.
目次
Understanding the Purchase Order Process
The purchase order process involves several steps that ensure a company acquires the goods and services it needs from suppliers.
Firstly, a requisition is made for a specific product or service.
Once approved, a purchase order is created and sent to the supplier.
The supplier then reviews and either accepts or rejects the order.
If accepted, the supplier delivers the goods or services, and an invoice is sent.
Finally, the company checks the delivery, processes the invoice, and makes a payment.
By optimizing each of these steps, businesses can enhance delivery management and achieve cost efficiency.
Methods for Effective Delivery Management
1. Choose Reliable Suppliers
Working with suppliers you can count on is crucial.
Reliable suppliers are more likely to fulfill orders on time while maintaining good quality.
Evaluate suppliers based on their delivery history, product quality, and compliance with your requirements.
2. Implement Real-Time Tracking
Real-time tracking systems offer you visibility over the entire delivery process.
By knowing the whereabouts of your orders at all times, you can provide accurate delivery times to clients and take action in case of delays.
3. Establish Clear Communication Channels
Clear communication with suppliers ensures that everyone is on the same page.
Make sure all details, such as delivery times, locations, and product specifications, are communicated clearly and in advance.
Open lines of communication help in quickly resolving any unforeseen issues.
4. Automate Inventory Management
Automation tools can help keep track of inventory levels, preventing stockouts and overstock situations.
Automated alerts can notify you when inventory levels are running low, enabling timely purchase orders and avoiding interruptions in the supply chain.
5. Use Delivery Management Software
Software solutions designed for delivery management can streamline the entire process.
These tools can help coordinate shipments, manage schedules, and track deliveries, ensuring timely execution of orders.
Methods for Achieving Cost Efficiency
1. Bulk Purchasing
Buying in bulk can lead to significant discounts from suppliers.
While it may require a larger upfront investment, the cost savings over time can be substantial.
Evaluate your usage patterns and forecast demand to take advantage of bulk purchasing.
2. Negotiate Better Terms with Suppliers
Strong negotiation skills can lead to better terms with your suppliers, such as lower prices, extended payment terms, or free shipping.
Building good relationships with suppliers can also result in additional discounts and benefits.
3. Consolidate Shipments
Consolidating shipments can reduce transportation costs significantly.
Instead of multiple smaller orders, grouping them together can maximize the use of shipping containers and reduce the per-unit cost of delivery.
4. Optimize Order Frequency
Frequent ordering can lead to higher shipping costs and processing fees.
Analyzing your order frequency and identifying the optimal schedule can help reduce unnecessary expenses.
5. Use Technology to Drive Efficiency
Leveraging technology in the purchase order process can dramatically increase efficiency.
Automation of repetitive tasks, like order entry and invoicing, saves both time and money.
Using tools for data analysis can also provide insights into spending patterns and areas for cost reduction.
The Role of Data Analytics
Data analytics can be a powerful tool in optimizing the purchase order process.
By analyzing historical data, businesses can identify trends, forecast future needs, and make informed decisions.
Using data, you can:
Identify frequently ordered products and negotiate bulk prices.
Monitor supplier performance and choose the most reliable partners.
Analyze delivery times and optimize logistics strategies.
Data-driven decision-making helps in refining both delivery management and cost efficiency strategies.
Best Practices for Continuous Improvement
1. Regularly Review and Update Processes
The purchase order process should be regularly reviewed to identify potential improvements.
Updating processes based on new technologies, market trends, or business needs can lead to better efficiency and effectiveness.
2. Train Staff
Well-trained staff are crucial for the smooth operation of the purchase order process.
Continuous training ensures that your team stays updated with the latest best practices and technological tools.
3. Measure Performance
Key performance indicators (KPIs) like order accuracy, delivery lead times, and cost savings should be tracked.
Regular monitoring of these metrics helps in assessing the effectiveness of strategies and identifying areas for improvement.
4. Foster Supplier Relationships
Strong relationships with suppliers can lead to better cooperation and enhanced performance.
Open communication, regular feedback, and mutual respect form the foundation of a fruitful supplier partnership.
5. Stay Updated with Industry Trends
The business world is constantly evolving, and staying updated with the latest trends is essential.
Keeping an eye on industry news, attending conferences, and participating in professional networks can provide valuable insights and ideas for process optimization.
Optimizing the purchase order process is a multi-step endeavor that requires careful planning and execution.
By implementing effective delivery management strategies and focusing on cost efficiency, businesses can gain a competitive edge.
Remember, continuous improvement is key to maintaining an optimized process.
Stay proactive, leverage technology, and use data-driven insights to ensure long-term success in your procurement operations.
資料ダウンロード
QCD調達購買管理クラウド「newji」は、調達購買部門で必要なQCD管理全てを備えた、現場特化型兼クラウド型の今世紀最高の購買管理システムとなります。
ユーザー登録
調達購買業務の効率化だけでなく、システムを導入することで、コスト削減や製品・資材のステータス可視化のほか、属人化していた購買情報の共有化による内部不正防止や統制にも役立ちます。
NEWJI DX
製造業に特化したデジタルトランスフォーメーション(DX)の実現を目指す請負開発型のコンサルティングサービスです。AI、iPaaS、および先端の技術を駆使して、製造プロセスの効率化、業務効率化、チームワーク強化、コスト削減、品質向上を実現します。このサービスは、製造業の課題を深く理解し、それに対する最適なデジタルソリューションを提供することで、企業が持続的な成長とイノベーションを達成できるようサポートします。
オンライン講座
製造業、主に購買・調達部門にお勤めの方々に向けた情報を配信しております。
新任の方やベテランの方、管理職を対象とした幅広いコンテンツをご用意しております。
お問い合わせ
コストダウンが利益に直結する術だと理解していても、なかなか前に進めることができない状況。そんな時は、newjiのコストダウン自動化機能で大きく利益貢献しよう!
(Β版非公開)