- お役立ち記事
- Order schedule management method to avoid supplier delivery delays
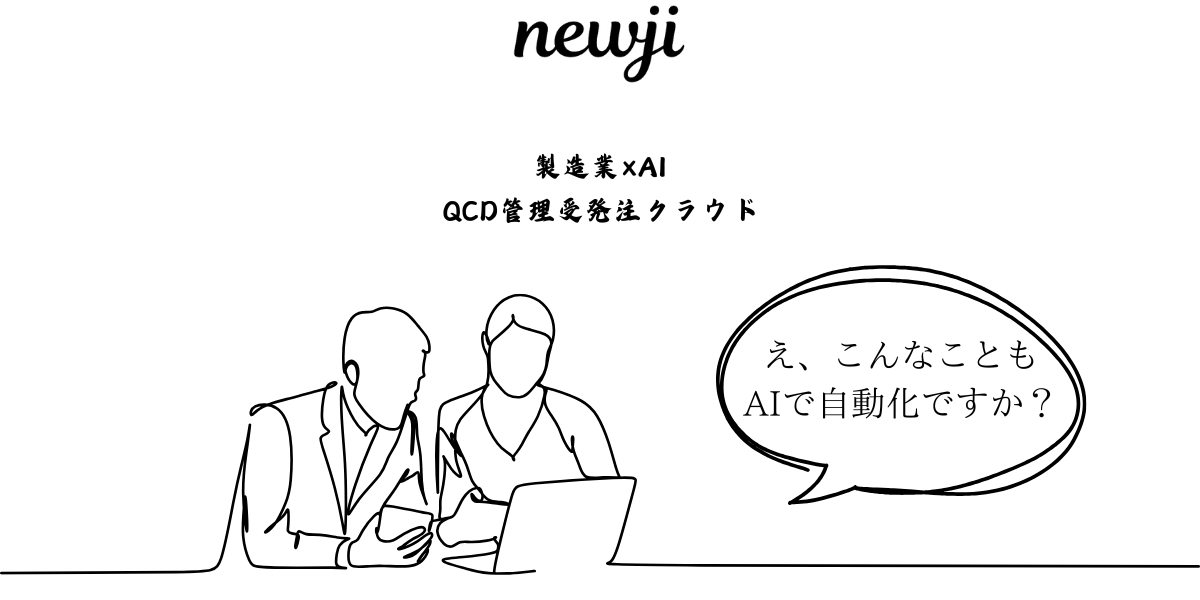
Order schedule management method to avoid supplier delivery delays
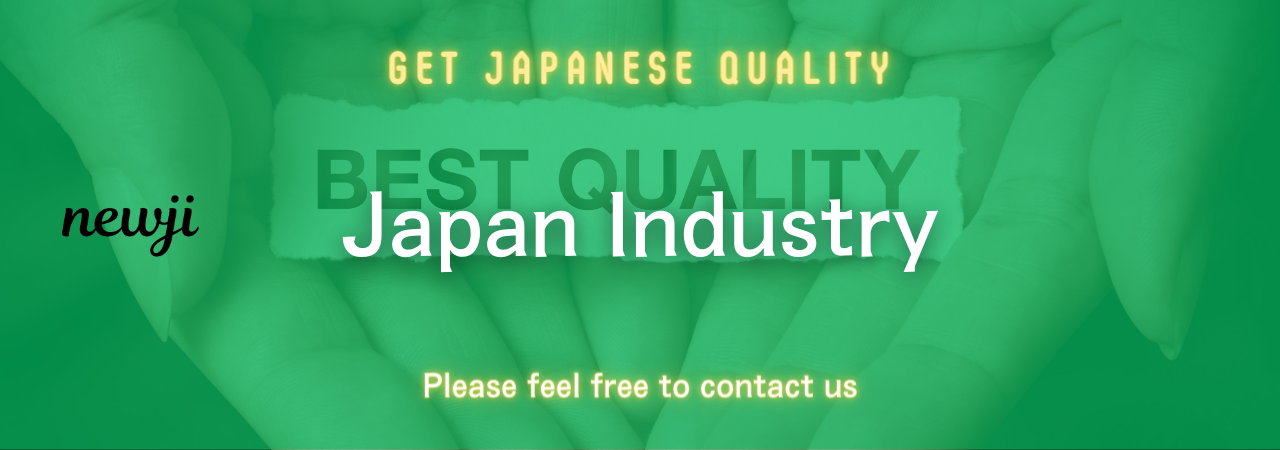
目次
Understanding the Importance of Order Schedule Management
In today’s fast-paced business environment, managing order schedules effectively is crucial to maintaining smooth operations.
An efficient order schedule management system ensures that suppliers deliver goods on time, avoiding costly delays and disruptions.
Staying on schedule is vital to maintaining positive relationships with suppliers and customers alike.
Order schedule management involves planning, coordinating, and controlling all aspects of ordering materials from suppliers.
This process requires a comprehensive understanding of the supply chain, inventory levels, and supplier capabilities.
Identifying Common Causes of Supplier Delivery Delays
To effectively manage order schedules, it is essential first to understand the common causes of supplier delivery delays.
These delays can stem from various factors, including:
Supplier Production Issues
Suppliers may encounter production issues such as machine breakdowns, labor shortages, or material shortages.
These issues can lead to delays in fulfilling orders, impacting your schedule.
Logistics and Transportation Challenges
Transportation problems, such as traffic congestion, accidents, or weather-related disruptions, can cause delays in the delivery of goods.
Additionally, logistical challenges with freight companies or shipping carriers can further exacerbate the situation.
Communication Breakdowns
Miscommunication between your company and the supplier can lead to misunderstandings about order requirements and delivery dates.
Poor communication can result in unnecessary delays and errors in the supply chain.
Demand Variability
Fluctuations in customer demand can affect order schedules.
Unanticipated increases in demand may result in suppliers being unable to fulfill orders promptly, leading to delays.
Strategies to Prevent Supplier Delivery Delays
Now that we understand the common causes of delays, let’s explore some strategies to manage order schedules effectively and prevent delivery disruptions.
Implementing Accurate Demand Forecasting
Accurate demand forecasting is vital to ensure that the right amount of inventory is ordered at the right time.
Utilize historical sales data, market trends, and customer feedback to predict future demand accurately.
By aligning your order schedules with realistic demand forecasts, you can reduce the risk of over-ordering or under-ordering, which can lead to supplier delays.
Establishing Strong Supplier Relationships
Building strong relationships with suppliers can enhance collaboration and communication.
Foster open lines of communication and maintain regular contact to address potential issues early on.
Establish clear expectations regarding delivery timelines and quality standards to ensure smooth operations.
Leveraging Technology and Automation
Modern supply chain management software and tools can optimize order schedules and monitor supplier performance.
Automate routine tasks such as order tracking and inventory management to minimize errors and improve efficiency.
Real-time data analytics can provide insights into potential bottlenecks, allowing you to address them proactively.
Developing a Contingency Plan
Preparing for unexpected disruptions is a critical aspect of order schedule management.
Develop a contingency plan that outlines alternative suppliers, transportation routes, or increased safety stock levels.
Having a backup plan in place can minimize the impact of delays and keep operations running smoothly.
Conducting Regular Performance Reviews
Regularly review supplier performance to assess their reliability and ability to meet delivery deadlines.
Use key performance indicators (KPIs) to evaluate aspects such as on-time delivery rates, order accuracy, and communication effectiveness.
Take corrective action as needed to address any consistent performance issues.
The Role of Communication in Order Schedule Management
Effective communication is at the heart of successful order schedule management.
Communicating clearly with suppliers, internal teams, and customers can prevent misunderstandings and streamline the ordering process.
Clear Order Specifications
Clearly specify order details, including product specifications, quantities, delivery dates, and any special requirements.
Detailed and unambiguous orders reduce the likelihood of errors and ensure that suppliers understand your expectations.
Regular Updates and Feedback
Provide suppliers with regular updates on order status, demand changes, and market conditions.
Solicit feedback from suppliers to identify potential issues early and collaboratively develop solutions.
Transparent and Timely Communication with Stakeholders
Keep all stakeholders informed about potential delays or changes in order schedules.
Transparent communication with customers, internal teams, and suppliers helps manage expectations and fosters trust.
Conclusion
Managing order schedules to avoid supplier delivery delays is critical to maintaining a competitive edge in today’s business landscape.
By understanding the common causes of delays, implementing preventative strategies, and fostering effective communication, businesses can enhance their supply chain efficiency and improve customer satisfaction.
An organized and proactive approach to order schedule management can significantly reduce the risk of supplier delivery delays and contribute to an overall smoother supply chain operation.
資料ダウンロード
QCD調達購買管理クラウド「newji」は、調達購買部門で必要なQCD管理全てを備えた、現場特化型兼クラウド型の今世紀最高の購買管理システムとなります。
ユーザー登録
調達購買業務の効率化だけでなく、システムを導入することで、コスト削減や製品・資材のステータス可視化のほか、属人化していた購買情報の共有化による内部不正防止や統制にも役立ちます。
NEWJI DX
製造業に特化したデジタルトランスフォーメーション(DX)の実現を目指す請負開発型のコンサルティングサービスです。AI、iPaaS、および先端の技術を駆使して、製造プロセスの効率化、業務効率化、チームワーク強化、コスト削減、品質向上を実現します。このサービスは、製造業の課題を深く理解し、それに対する最適なデジタルソリューションを提供することで、企業が持続的な成長とイノベーションを達成できるようサポートします。
オンライン講座
製造業、主に購買・調達部門にお勤めの方々に向けた情報を配信しております。
新任の方やベテランの方、管理職を対象とした幅広いコンテンツをご用意しております。
お問い合わせ
コストダウンが利益に直結する術だと理解していても、なかなか前に進めることができない状況。そんな時は、newjiのコストダウン自動化機能で大きく利益貢献しよう!
(Β版非公開)