- お役立ち記事
- Order timing adjustment and inventory control Key points for the purchasing department to cooperate with the production site
月間76,176名の
製造業ご担当者様が閲覧しています*
*2025年3月31日現在のGoogle Analyticsのデータより
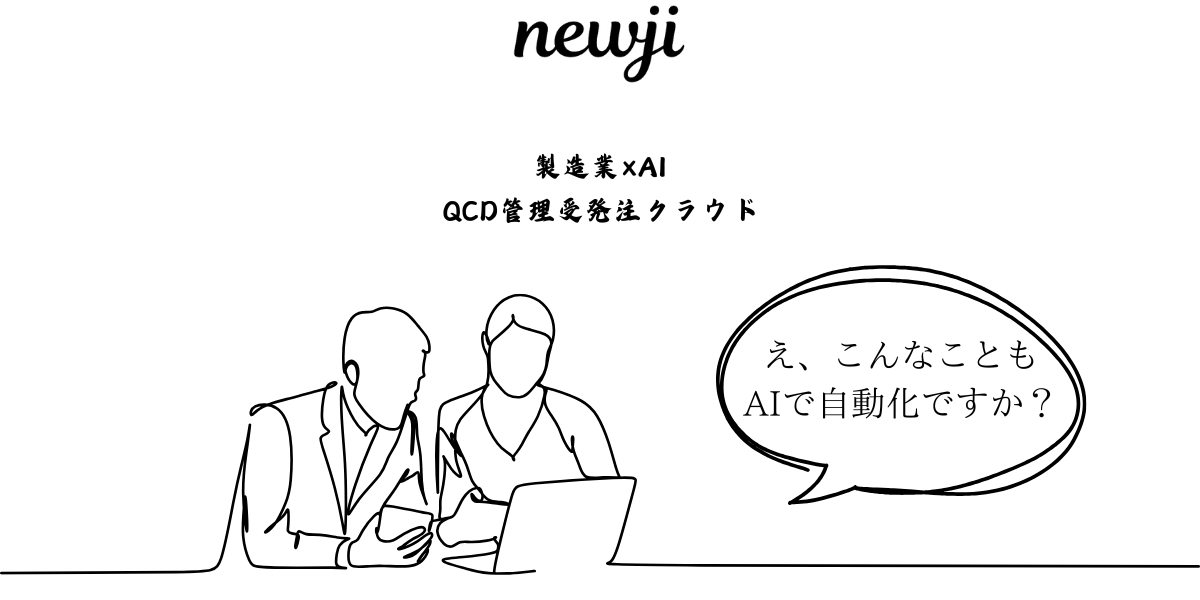
Order timing adjustment and inventory control Key points for the purchasing department to cooperate with the production site
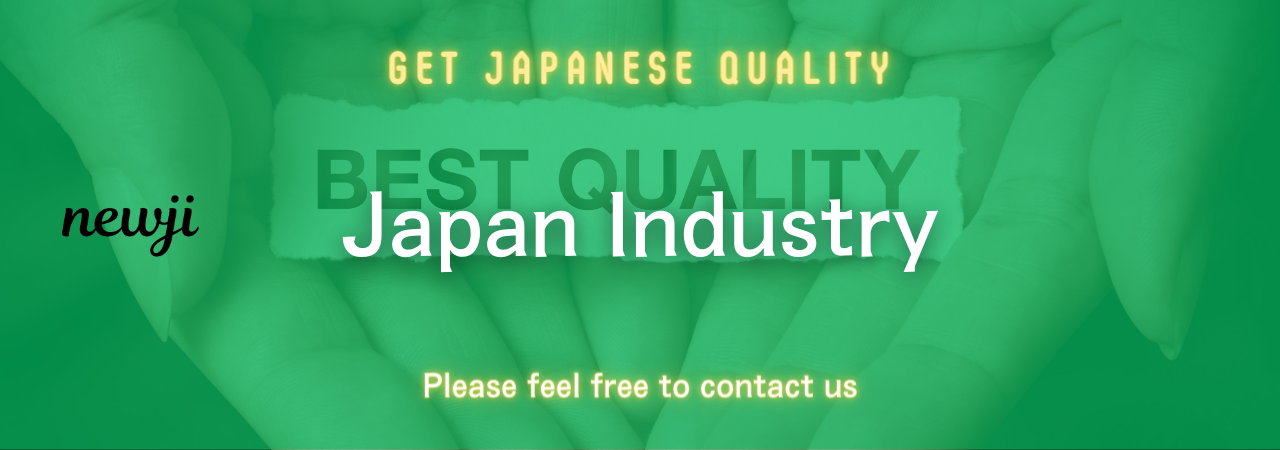
目次
Understanding Order Timing and Inventory Control
In today’s fast-paced manufacturing environment, the synergy between the purchasing department and the production site is crucial for maintaining efficiency and cost-effectiveness.
One of the key elements of this collaboration is order timing adjustment and inventory control.
By mastering these aspects, companies can ensure a smooth production schedule, minimize waste, and optimize resources.
The Role of the Purchasing Department
The purchasing department plays a vital role in ensuring that materials are available when needed, without overstocking, which ties up capital and space.
They are responsible for negotiating with suppliers, securing the best prices, and ensuring timely deliveries.
To do this effectively, they must have clear communication with the production site to understand the production schedule and inventory turnover rates.
Why Timing is Essential
Proper timing in placing orders is essential for maintaining a balanced inventory.
If orders are placed too early, excess inventory can accumulate, leading to higher storage costs and potential waste.
On the other hand, if orders are delayed, it can cause production slowdowns or halts due to a lack of necessary materials.
Thus, a synchronized schedule and accurate forecasting are necessary to ensure that the right materials arrive just in time.
Strategies for Effective Order Timing Adjustment
1. Just-in-Time (JIT) Inventory
One approach to effective inventory control is the Just-in-Time (JIT) inventory system.
This strategy focuses on receiving goods only as they are needed in the production process, thereby reducing inventory costs.
For this to work, the purchasing department must closely monitor the production schedule and ensure that suppliers are reliable and can deliver quickly.
2. Demand Forecasting
Accurate demand forecasting is another crucial strategy.
By analyzing sales data and market trends, the purchasing department can predict future material needs more accurately.
This information allows them to adjust order timing to avoid both shortages and overstock situations.
3. Supplier Relationship Management
Building strong relationships with suppliers is key to effective inventory control.
The purchasing department should work closely with suppliers to ensure they understand the company’s timing requirements and can meet them consistently.
This may involve negotiating flexible delivery schedules or setting up contracts that offer favorable terms for both parties.
The Importance of Communication
Aligning Goals and Objectives
For order timing adjustment and inventory control to be successful, the purchasing department and the production site must have aligned goals.
Both departments should work towards minimizing costs while maximizing efficiency and effectiveness.
Regular meetings and updates help both parties stay on the same page and adapt to changing circumstances quickly.
Real-Time Data Sharing
Utilizing technology to share real-time data between the purchasing department and the production site can significantly enhance communication and decision-making.
By using integrated software systems, both departments have access to up-to-date information about inventory levels, production schedules, and supplier deliveries.
This transparency allows for more accurate order timing adjustments and inventory control.
Challenges and Solutions
Overcoming Delays
Delays in supplier deliveries can cause significant disruptions to the production schedule.
To mitigate this risk, the purchasing department should have contingency plans in place, such as secondary suppliers or emergency stock.
Regular performance evaluations of suppliers can also help identify potential issues before they escalate.
Managing Inventory Costs
Maintaining an optimal inventory level is challenging, especially with fluctuating market demands.
The purchasing department must continually assess inventory turnover rates and adjust order quantities accordingly.
Using inventory management software can provide insights and analytics to aid in making informed decisions.
Navigating Fluctuating Demand
Demand fluctuations are inevitable in any business.
It is vital for the purchasing department to be agile and responsive to these changes.
Establishing flexible contracts with suppliers can offer the ability to adjust order quantities without incurring penalties.
Conclusion
Effective order timing adjustment and inventory control require meticulous planning, open communication, and a collaborative approach between the purchasing department and the production site.
By implementing strategies such as Just-in-Time inventory, demand forecasting, and strong supplier relationships, companies can enhance their operational efficiency, reduce costs, and mitigate risks associated with inventory management.
As businesses continue to face dynamic market conditions, staying adaptable and proactive will be key to sustaining success.
資料ダウンロード
QCD管理受発注クラウド「newji」は、受発注部門で必要なQCD管理全てを備えた、現場特化型兼クラウド型の今世紀最高の受発注管理システムとなります。
ユーザー登録
受発注業務の効率化だけでなく、システムを導入することで、コスト削減や製品・資材のステータス可視化のほか、属人化していた受発注情報の共有化による内部不正防止や統制にも役立ちます。
NEWJI DX
製造業に特化したデジタルトランスフォーメーション(DX)の実現を目指す請負開発型のコンサルティングサービスです。AI、iPaaS、および先端の技術を駆使して、製造プロセスの効率化、業務効率化、チームワーク強化、コスト削減、品質向上を実現します。このサービスは、製造業の課題を深く理解し、それに対する最適なデジタルソリューションを提供することで、企業が持続的な成長とイノベーションを達成できるようサポートします。
製造業ニュース解説
製造業、主に購買・調達部門にお勤めの方々に向けた情報を配信しております。
新任の方やベテランの方、管理職を対象とした幅広いコンテンツをご用意しております。
お問い合わせ
コストダウンが利益に直結する術だと理解していても、なかなか前に進めることができない状況。そんな時は、newjiのコストダウン自動化機能で大きく利益貢献しよう!
(β版非公開)