- お役立ち記事
- Oxidation Countermeasures and Management in Manufacturing
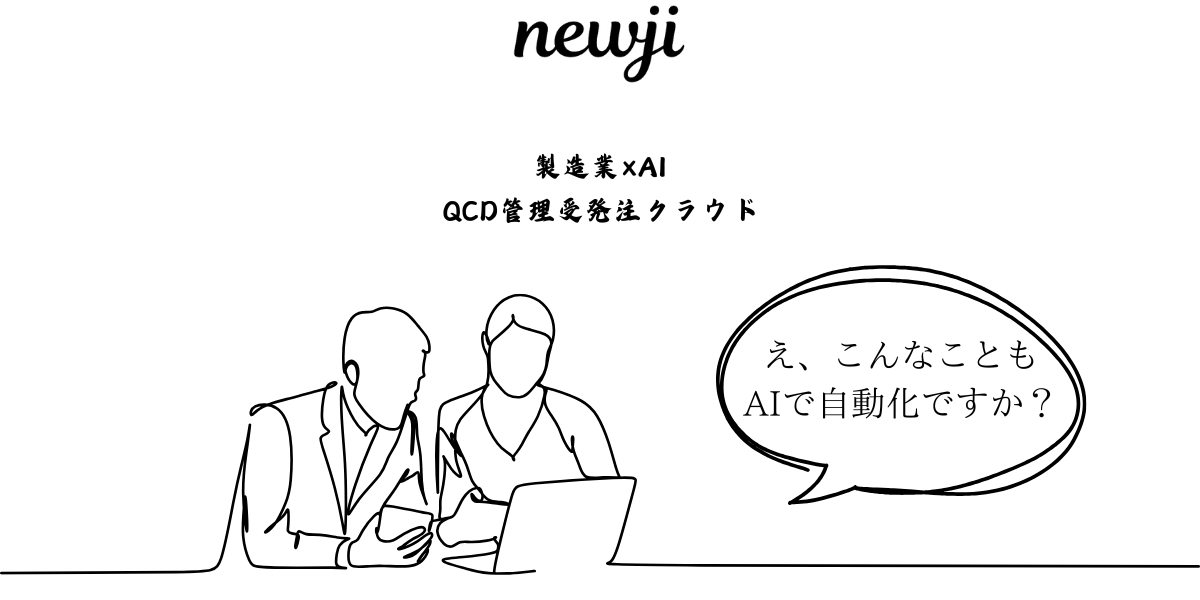
Oxidation Countermeasures and Management in Manufacturing
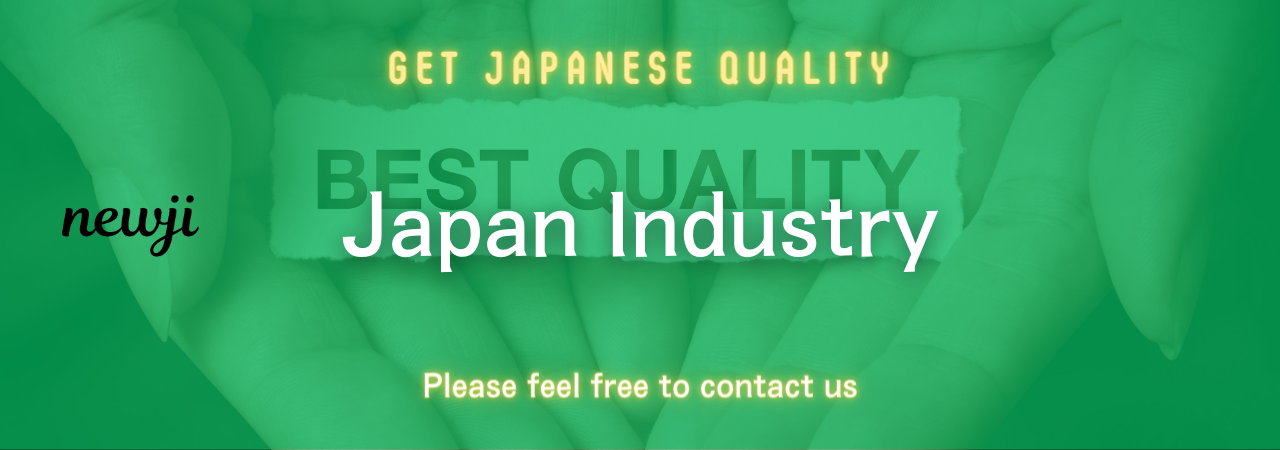
In the world of manufacturing, oxidation is a common challenge that needs to be managed effectively.
This process leads to the deterioration of materials, causing potential failures in production and end-products.
But what exactly is oxidation, and how can it be countered?
目次
What is Oxidation?
Oxidation is a chemical reaction that occurs when materials, particularly metals, react with oxygen in the environment.
This reaction leads to the formation of oxides on the surface of the material.
A familiar example is the rusting of iron.
When iron reacts with oxygen, it forms iron oxide, commonly known as rust.
While rust can sometimes be aesthetically appealing in art, it is detrimental in manufacturing and industrial applications.
Effects of Oxidation in Manufacturing
Oxidation can significantly impact the performance, appearance, and integrity of manufactured products.
Here are some common effects:
1. Material Weakening
When metals oxidize, they lose their strength.
This can compromise the structural integrity of components, making them unsafe or unusable.
2. Cosmetic Damage
Oxidation often manifests as discoloration or surface blemishes on metals and other materials.
This can negatively affect the aesthetic appeal of products, making them less attractive to consumers.
3. Electrical Conductivity
Oxidation in electrical components, such as connectors and circuit boards, can reduce conductivity.
This can lead to failures in electronic devices and systems.
Strategies to Counter Oxidation
Preventing and managing oxidation is crucial to maintaining the quality and longevity of manufactured goods.
Here are some effective strategies:
1. Protective Coatings
Applying a protective coating to materials can prevent direct exposure to oxygen.
Common coatings include paint, varnish, and specialized metal treatments like galvanization.
These barriers help to avoid or slow down the oxidation process.
2. Use of Corrosion-Resistant Materials
Selecting materials that are inherently resistant to oxidation is a proactive approach.
Stainless steel, aluminum, and certain alloys are less prone to oxidizing compared to other metals.
Incorporating these materials into manufacturing can extend the life of products.
3. Controlled Environment
In certain manufacturing processes, controlling the environment can significantly reduce oxidation.
This might involve reducing humidity levels, maintaining a specific temperature range, or using inert gases in the production area.
By minimizing the factors that contribute to oxidation, manufacturers can preserve material quality.
4. Regular Maintenance
Routine maintenance and inspection can identify early signs of oxidation.
By addressing these issues promptly, manufacturers can prevent extensive damage.
Cleaning, lubricating, and replacing affected components are key maintenance activities.
5. Anodizing
Anodizing is an electrochemical process that increases the thickness of the natural oxide layer on the surface of metals.
This process is particularly effective for aluminum and provides enhanced resistance against oxidation.
Anodized aluminum is widely used in automotive and aerospace industries due to its durability.
Implementing Oxidation Management in Manufacturing
To effectively manage oxidation, a comprehensive plan must be put in place.
This includes the following steps:
1. Assessment
Begin by assessing the current state of your materials and processes.
Identify which materials are most susceptible to oxidation and which stages of production are at the highest risk.
Understanding the problem areas will help in tailoring appropriate countermeasures.
2. Research and Procurement
Research the best materials and coatings for your specific manufacturing needs.
Procure high-quality raw materials and coatings to ensure long-lasting protection.
Consider the environmental impact and cost-effectiveness when selecting these materials.
3. Training
Train your workforce on the importance of controlling oxidation and how to implement preventative measures.
Regular training sessions can keep everyone updated on the best practices and new technologies in oxidation management.
4. Monitoring and Maintenance
Establish a routine monitoring system to regularly check for signs of oxidation.
Incorporate maintenance schedules that include cleaning, lubricating, and replacing oxidized components.
Effective monitoring and maintenance can greatly reduce the impact of oxidation on your production.
5. Continuous Improvement
Adopt a culture of continuous improvement to stay ahead of oxidation challenges.
Stay updated with advancements in materials science and surface treatment technologies.
Implementing new techniques and products as they become available can enhance your oxidation management efforts.
Future Trends in Oxidation Management
The future of oxidation management in manufacturing looks promising, with several emerging trends and technologies:
1. Nanotechnology
Nanotechnology involves manipulating materials at the atomic or molecular level.
It holds great potential in creating ultra-thin protective coatings that are more effective than traditional ones.
These nano-coatings can provide superior resistance to oxidation and other forms of corrosion.
2. Smart Coatings
Smart coatings are an innovative advancement in material science.
These coatings can change properties in response to environmental conditions.
For instance, a smart coating might tighten its structure in the presence of high humidity, preventing moisture from reaching the material beneath.
3. Advanced Surface Treatments
New surface treatments, such as laser surface modification and plasma treatment, are emerging as powerful tools against oxidation.
These treatments can enhance the surface properties of materials, making them more resistant to oxidation and wear.
Conclusion
Understanding and managing oxidation is essential for maintaining the quality and longevity of manufactured products.
By implementing protective coatings, using corrosion-resistant materials, controlling the manufacturing environment, and practicing regular maintenance, manufacturers can effectively counter oxidation.
Staying informed about future trends and continuously improving oxidation management strategies will ensure long-term success in the manufacturing industry.
資料ダウンロード
QCD調達購買管理クラウド「newji」は、調達購買部門で必要なQCD管理全てを備えた、現場特化型兼クラウド型の今世紀最高の購買管理システムとなります。
ユーザー登録
調達購買業務の効率化だけでなく、システムを導入することで、コスト削減や製品・資材のステータス可視化のほか、属人化していた購買情報の共有化による内部不正防止や統制にも役立ちます。
NEWJI DX
製造業に特化したデジタルトランスフォーメーション(DX)の実現を目指す請負開発型のコンサルティングサービスです。AI、iPaaS、および先端の技術を駆使して、製造プロセスの効率化、業務効率化、チームワーク強化、コスト削減、品質向上を実現します。このサービスは、製造業の課題を深く理解し、それに対する最適なデジタルソリューションを提供することで、企業が持続的な成長とイノベーションを達成できるようサポートします。
オンライン講座
製造業、主に購買・調達部門にお勤めの方々に向けた情報を配信しております。
新任の方やベテランの方、管理職を対象とした幅広いコンテンツをご用意しております。
お問い合わせ
コストダウンが利益に直結する術だと理解していても、なかなか前に進めることができない状況。そんな時は、newjiのコストダウン自動化機能で大きく利益貢献しよう!
(Β版非公開)