- お役立ち記事
- Paddleboard Manufacturing Process and Durability Techniques
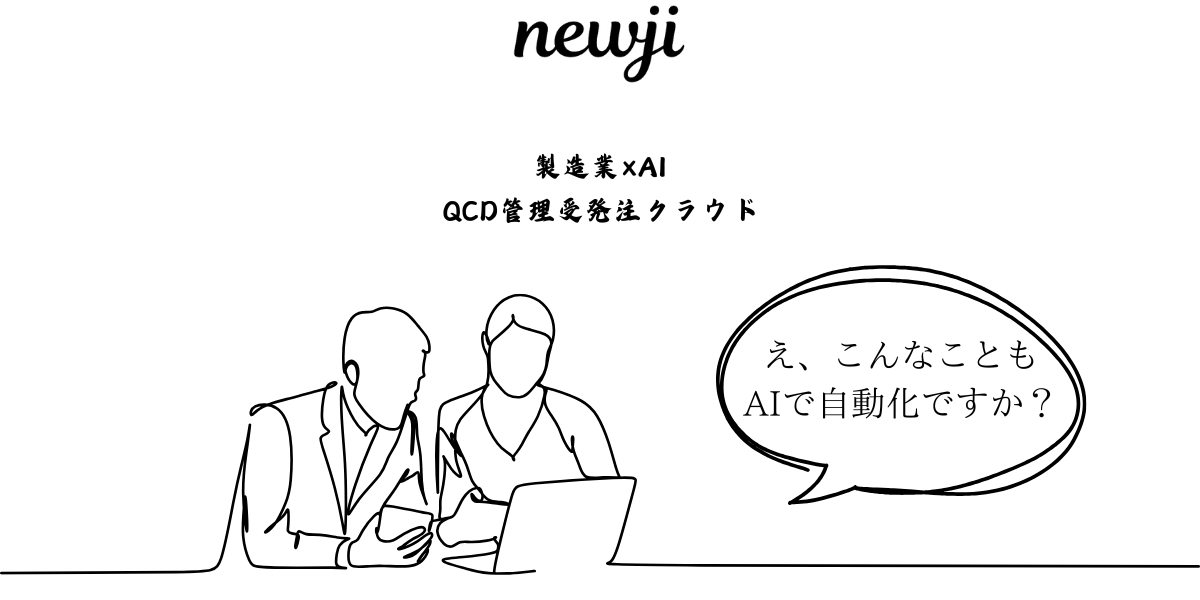
Paddleboard Manufacturing Process and Durability Techniques
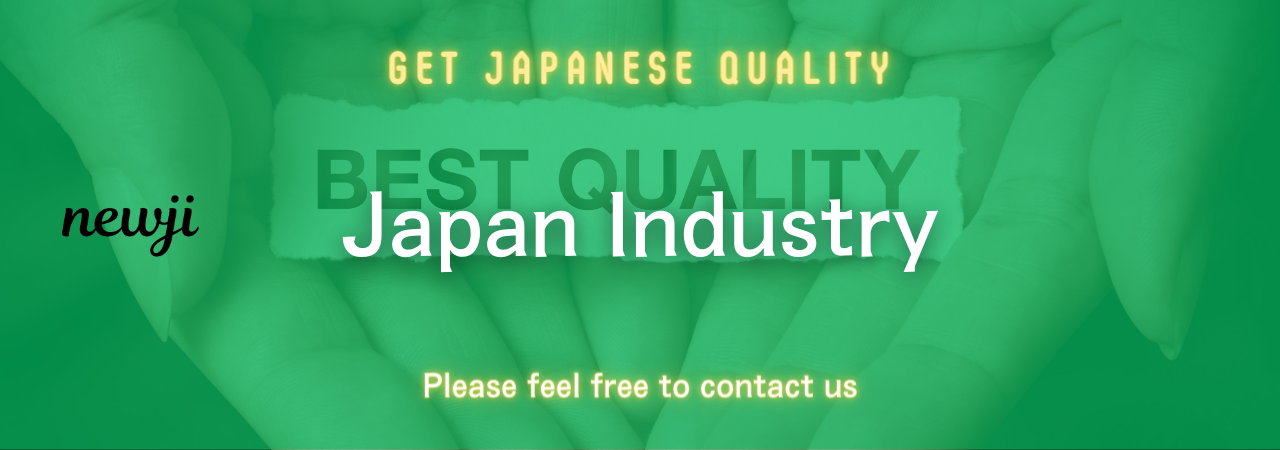
目次
Introduction to Paddleboards
Paddleboarding has become an increasingly popular water sport, drawing enthusiasts of all skill levels who enjoy the tranquility and excitement it brings.
Whether you’re paddling through calm lakes, challenging ocean waves, or peaceful rivers, the durability and quality of your paddleboard are crucial for a safe and enjoyable experience.
Understanding how paddleboards are manufactured and the techniques used to enhance their durability can empower you in making informed purchasing decisions.
Materials Used in Paddleboard Manufacturing
Paddleboards are crafted using a variety of materials, each contributing to the board’s performance and longevity.
The choice of materials significantly impacts the board’s weight, buoyancy, and susceptibility to wear and tear.
Foam Cores
The core of a paddleboard is typically made from expanded polystyrene (EPS) foam.
This material is lightweight yet strong, providing the foundational structure of the board.
EPS foam varies in density, with higher-density foams being more durable but also heavier.
The density is carefully selected to balance durability and performance, ensuring that the board remains agile while offering sufficient support.
Fiberglass Layers
To reinforce the foam core, layers of fiberglass are applied.
Fiberglass adds strength and rigidity, ensuring the board can withstand physical stress from waves and paddling.
Multiple layers are used, with varying weaves, to enhance durability without significantly increasing weight.
The fiberglass layers are laminated using epoxy resin, which hardens to form a strong, protective shell.
Epoxy Resin
Epoxy resin serves as the adhesive that binds the fiberglass layers together and secures them to the foam core.
Beyond its adhesive properties, epoxy acts as a protective coating, providing resistance to water damage and scratches.
This resin is key to creating a smooth, sleek finish that enhances the board’s hydrodynamic properties.
Carbon Fiber
For premium paddleboards, carbon fiber is often used as it offers superior strength and a lightweight profile.
Though more expensive, carbon fiber’s exceptional strength-to-weight ratio provides enhanced performance characteristics, such as faster speeds and better handling.
It is particularly favored by professional athletes and serious enthusiasts who require high-performance equipment.
The Manufacturing Process
The process of making a paddleboard is both intricate and precise, involving several stages that require expert craftsmanship and attention to detail.
Design and Shaping
The first step in manufacturing a paddleboard is designing the shape based on its intended use, such as surf, touring, or racing.
Computer-aided design (CAD) software is often used to create precise board templates.
Once the design is finalized, the EPS foam is cut and shaped according to the template.
This shaping is crucial as it determines the board’s performance characteristics like stability, speed, and maneuverability.
Laminating
After shaping, the board undergoes the laminating process where fiberglass cloth is carefully applied over the foam core.
The layers of fiberglass are then saturated with epoxy resin, which is meticulously spread to ensure even coverage and prevent air bubbles.
This step is vital in providing the board with the necessary strength and rigidity.
Curing
Once the board is laminated, it is left to cure for several hours to several days, allowing the epoxy to harden completely.
The curing time depends on factors like room temperature and humidity, influencing the resin’s properties and the final durability of the board.
Finishing Touches
After curing, excess fiberglass and resin are trimmed, and the board’s edges are smoothed for a polished appearance.
The final touch involves adding non-slip surfaces, graphics, and any additional accessories like fins or handles.
These extras enhance functionality and provide a personalized aesthetic to each board.
Durability Techniques
Paddleboard manufacturers employ several techniques to enhance the durability and lifespan of their products.
Reinforced Rails
The edges, or rails, of a paddleboard are susceptible to dings and impacts.
Reinforcement techniques, like additional layers of fiberglass or carbon fiber, help protect these vulnerable areas from damage.
These reinforcements ensure that the board can sustain the rigors of frequent use and minor collisions without significant wear.
Thermal Bonding
Thermal bonding techniques are used to improve the bond between the foam core and fiberglass layers.
This method involves applying heat during the lamination process, resulting in a stronger, more durable composite material.
Thermal bonding also helps in reducing delamination risks, where layers may peel apart due to wear or water intrusion.
Additional UV Protection
Sun exposure can degrade the materials of a paddleboard, making UV protection a critical durability factor.
UV-resistant coatings or additives in the resin provide long-lasting protection against sun damage, preserving the board’s finish and structural integrity over time.
These measures ensure that the board maintains its visual appeal and functionality even after prolonged sun exposure.
Conclusion
The manufacturing process of paddleboards combines advanced materials with precise craftsmanship to create durable, high-performing boards.
Understanding these processes and techniques can help you appreciate the craftsmanship involved and make informed choices when selecting a paddleboard.
Durability-focused innovations like reinforced rails, thermal bonding, and UV protection are essential, ensuring that paddleboards stand the test of time, allowing enthusiasts to enjoy their sport for years to come.
Whether you’re a beginner or an expert, the right paddleboard, made with care and expertise, makes all the difference in your aquatic adventures.
資料ダウンロード
QCD調達購買管理クラウド「newji」は、調達購買部門で必要なQCD管理全てを備えた、現場特化型兼クラウド型の今世紀最高の購買管理システムとなります。
ユーザー登録
調達購買業務の効率化だけでなく、システムを導入することで、コスト削減や製品・資材のステータス可視化のほか、属人化していた購買情報の共有化による内部不正防止や統制にも役立ちます。
NEWJI DX
製造業に特化したデジタルトランスフォーメーション(DX)の実現を目指す請負開発型のコンサルティングサービスです。AI、iPaaS、および先端の技術を駆使して、製造プロセスの効率化、業務効率化、チームワーク強化、コスト削減、品質向上を実現します。このサービスは、製造業の課題を深く理解し、それに対する最適なデジタルソリューションを提供することで、企業が持続的な成長とイノベーションを達成できるようサポートします。
オンライン講座
製造業、主に購買・調達部門にお勤めの方々に向けた情報を配信しております。
新任の方やベテランの方、管理職を対象とした幅広いコンテンツをご用意しております。
お問い合わせ
コストダウンが利益に直結する術だと理解していても、なかなか前に進めることができない状況。そんな時は、newjiのコストダウン自動化機能で大きく利益貢献しよう!
(Β版非公開)