- お役立ち記事
- Parts procurement strategy for production line optimization led by purchasing department
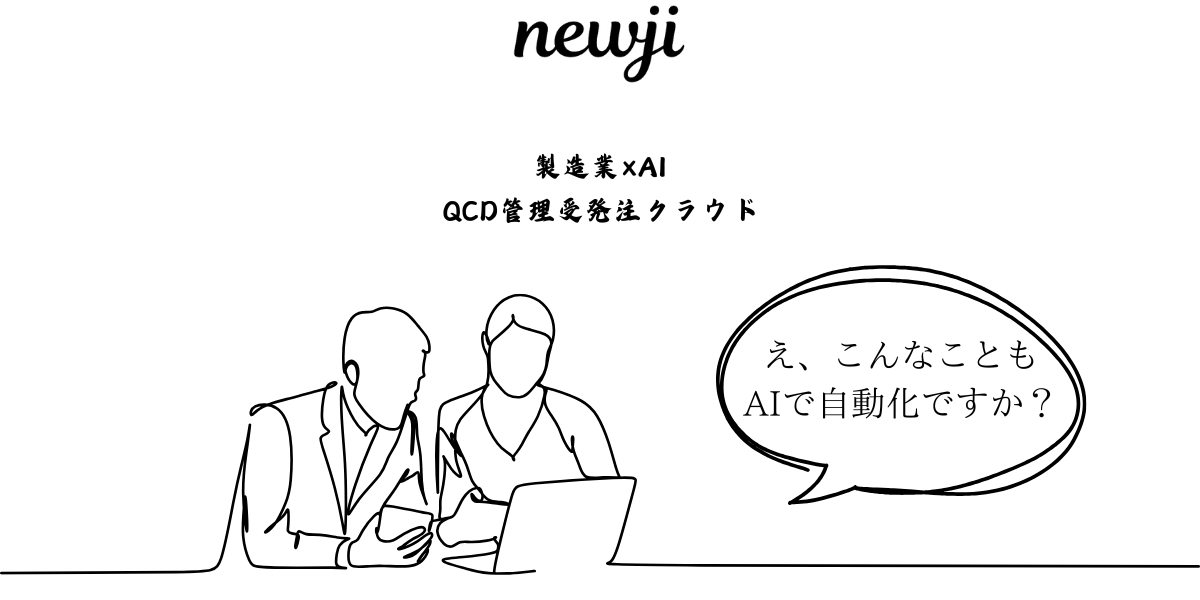
Parts procurement strategy for production line optimization led by purchasing department
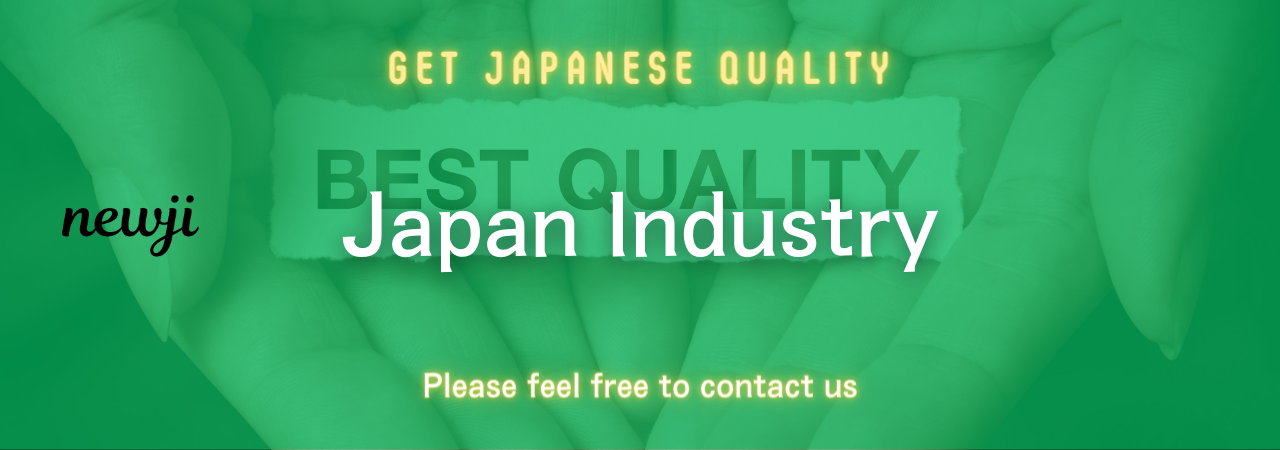
目次
Understanding the Importance of Parts Procurement
In the world of manufacturing, optimizing the production line is crucial for maintaining competitiveness and ensuring timely delivery of products.
The purchasing department plays a pivotal role in achieving this goal through effective parts procurement strategies.
Understanding the importance of parts procurement is the first step in optimizing your production line.
Parts procurement involves sourcing the necessary components required for manufacturing products.
The purchasing department must ensure a steady supply of these components to avoid production delays.
A well-organized procurement strategy helps maintain inventory levels, reduces costs, and improves overall efficiency.
Without a robust procurement strategy, the production line can suffer from bottlenecks and inefficiencies.
Challenges in Parts Procurement
Parts procurement is not without its challenges.
Fluctuating market demands, supply chain disruptions, and rising costs are just a few of the obstacles faced by the purchasing department.
To address these challenges, it’s essential to develop a flexible and adaptable procurement strategy.
Supply chain disruptions can occur due to various reasons such as natural disasters, political instability, or logistical issues.
Having multiple suppliers and maintaining strong relationships with them can mitigate these risks.
Additionally, market demands can shift rapidly, making it essential for the purchasing department to stay informed and react swiftly.
Cost management is another significant challenge in parts procurement.
Balancing cost reduction with quality assurance requires careful planning and negotiation with suppliers.
Organizations must strive to find the best value without compromising on the quality of parts.
Developing a Parts Procurement Strategy
Developing an effective parts procurement strategy involves several critical steps.
The purchasing department needs to assess the current procurement process and identify areas for improvement.
1. Supplier Evaluation and Relationship Management
Evaluating existing and potential suppliers is an important part of developing a procurement strategy.
Factors to consider include the supplier’s reliability, quality of parts, pricing, and delivery times.
Building strong relationships with key suppliers ensures a reliable supply chain and can lead to favorable negotiation terms.
2. Inventory Management
Optimizing inventory levels is another crucial aspect of an effective procurement strategy.
Excess inventory can tie up capital and create storage challenges, while insufficient inventory can lead to production delays.
Implementing just-in-time (JIT) inventory systems can help strike the right balance.
3. Cost Analysis and Negotiation
A thorough cost analysis is necessary to identify opportunities for cost reduction.
The purchasing department should negotiate with suppliers to secure the best possible prices without compromising quality.
Leverage economies of scale by consolidating orders to achieve discounts.
4. Technology Integration
Incorporating technology into the procurement process can greatly enhance its efficiency.
Utilizing procurement software for tracking orders, managing suppliers, and forecasting demand can streamline operations.
Such technology ensures accurate data management and facilitates informed decision-making.
Optimizing the Production Line
Optimizing the production line involves more than just efficient parts procurement; it requires a holistic approach.
Collaboration between the purchasing department and other departments such as production, engineering, and logistics is vital.
The production line can be optimized by implementing lean manufacturing principles, which focus on minimizing waste and maximizing efficiency.
This approach involves continually evaluating processes and eliminating non-value-adding activities.
Using cross-functional teams to identify and solve issues can enhance collaboration and improve the overall production process.
Feedback from the purchasing department regarding supplier performance can help improve quality assurance.
The Benefits of a Well-Executed Procurement Strategy
A well-executed procurement strategy leads to numerous benefits for the production line and the organization as a whole.
It ensures that production goals are met, and product delivery timelines are adhered to, thus maintaining customer satisfaction.
Cost savings achieved through effective procurement strategies can be reinvested into other areas of the business, fostering growth and innovation.
Additionally, the optimized production line enhances the company’s competitive advantage in the market.
Conclusion
The role of the purchasing department in leading parts procurement strategy for production line optimization cannot be overstated.
Through effective management of suppliers, inventory, costs, and technology, the purchasing department can significantly contribute to the overall success of the organization.
By addressing common procurement challenges and developing a comprehensive strategy, manufacturers can ensure a smooth and efficient production process.
Ultimately, a well-optimized production line will lead to increased productivity, cost savings, and customer satisfaction.
資料ダウンロード
QCD調達購買管理クラウド「newji」は、調達購買部門で必要なQCD管理全てを備えた、現場特化型兼クラウド型の今世紀最高の購買管理システムとなります。
ユーザー登録
調達購買業務の効率化だけでなく、システムを導入することで、コスト削減や製品・資材のステータス可視化のほか、属人化していた購買情報の共有化による内部不正防止や統制にも役立ちます。
NEWJI DX
製造業に特化したデジタルトランスフォーメーション(DX)の実現を目指す請負開発型のコンサルティングサービスです。AI、iPaaS、および先端の技術を駆使して、製造プロセスの効率化、業務効率化、チームワーク強化、コスト削減、品質向上を実現します。このサービスは、製造業の課題を深く理解し、それに対する最適なデジタルソリューションを提供することで、企業が持続的な成長とイノベーションを達成できるようサポートします。
オンライン講座
製造業、主に購買・調達部門にお勤めの方々に向けた情報を配信しております。
新任の方やベテランの方、管理職を対象とした幅広いコンテンツをご用意しております。
お問い合わせ
コストダウンが利益に直結する術だと理解していても、なかなか前に進めることができない状況。そんな時は、newjiのコストダウン自動化機能で大きく利益貢献しよう!
(Β版非公開)