- お役立ち記事
- PDCA cycle for improving purchasing processes that mid-level employees should know
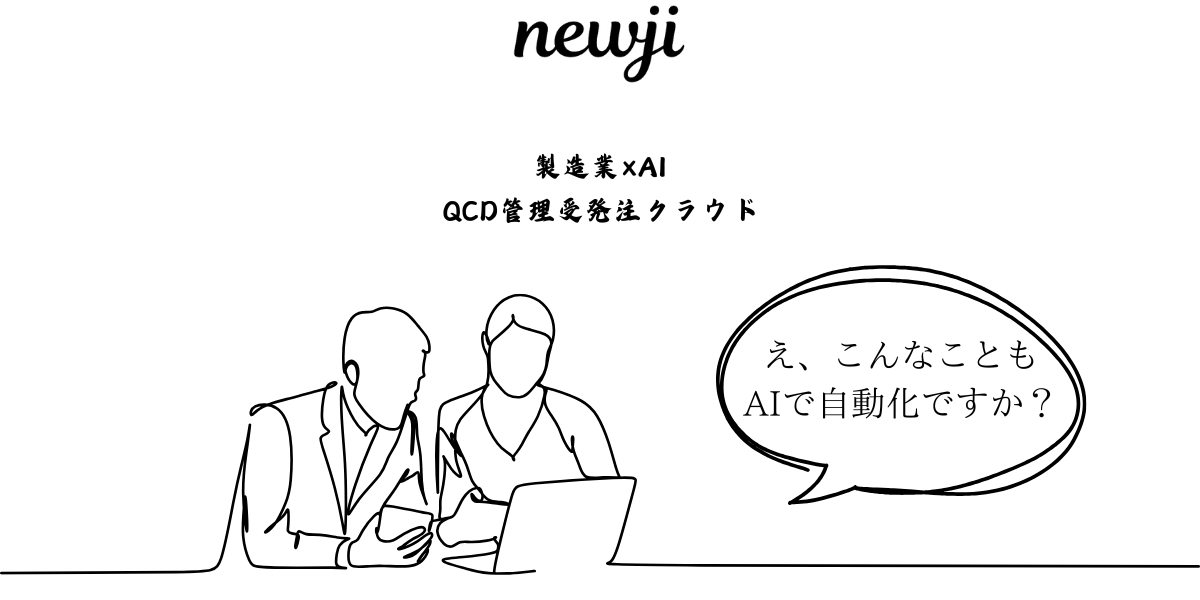
PDCA cycle for improving purchasing processes that mid-level employees should know
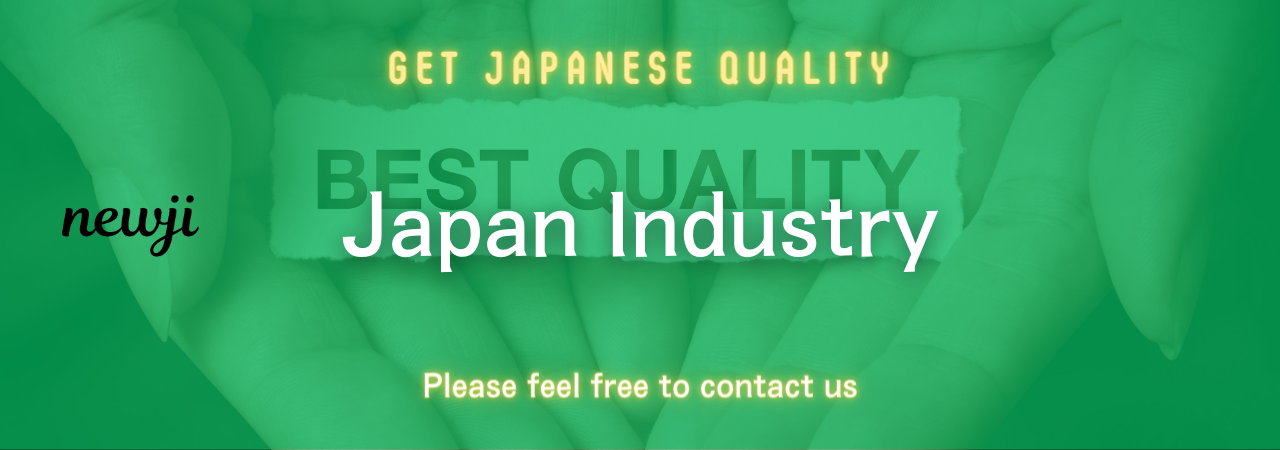
目次
Understanding the PDCA Cycle
The PDCA cycle, which stands for Plan, Do, Check, Act, is a simple yet powerful method used to enhance and control processes in various fields, including purchasing.
Its structured approach allows organizations to focus on continuous improvement by using an iterative process.
Before diving into how mid-level employees can integrate the PDCA cycle into purchasing processes, it’s essential to understand what each stage involves.
Plan
In the planning phase, you identify and understand the problem that needs attention.
This stage involves extensive research and data analysis to pinpoint the issue within the purchasing processes.
Imagine breaking down each step of your current purchasing process to understand where it can be improved.
You then set objectives for improvement and develop a plan detailing actions needed to reach these objectives.
Do
After planning, you implement the small changes on a manageable scale.
Think of this phase as a testing ground for your ideas.
Implementing these actions helps in validating hypotheses and understanding if the new approach will solve the identified issues.
It’s important to meticulously document all actions taken during this phase for further analysis.
Check
Checking is all about analyzing the results.
Measure the effectiveness of the actions taken during the Do phase.
Did you achieve the set objectives?
Use quantitative data to conduct a thorough analysis.
Compare the results against the baseline established during the planning stage to assess the improvements or need for further changes.
Act
Finally, based on the insights from the Check phase, decide whether to adopt, abandon, or modify the changes introduced.
An effective Act phase helps cement the changes or strategies into standard operational procedures if results show significant improvement.
If not, adjustments might be necessary.
This iterative approach allows for refining actions and strategies to drive better results.
Applying the PDCA Cycle to Purchasing Processes
Mid-level employees can utilize the PDCA cycle to improve purchasing processes in various effective ways.
Here are some specific strategies for these four stages when applied to purchasing.
Plan for Effective Purchasing
Start by mapping out the existing purchasing process.
Analyze where there might be bottlenecks or inefficiencies.
For example, delays might occur due to approval processes or supplier lead times.
Set realistic goals, like reducing order processing time or finding alternative suppliers.
Establish benchmarks for these goals using clear metrics to identify success after implementation.
Do: Implementing Changes in Purchasing
During the Do phase, roll out changes on a smaller scale.
This could involve automating a segment of the purchasing workflow or switching to a digital purchasing platform.
Training team members on newly implemented technologies ensures a smooth transition.
Collect data on critical indicators like processing time, cost savings, and error reduction.
Check: Evaluating Purchasing Efficiency
With data collected during the Do phase, evaluate whether the changes have positively affected the purchasing process.
Did automating the process decrease lead times?
Analyze both quantitative data and team feedback for a comprehensive overview.
Evaluate any challenges faced during the implementation phase.
It is crucial to remain objective, letting the data guide the conclusion.
Act: Adjusting and Standardizing for Improvement
Based on the evaluation, decide on the next steps.
If automation proved successful, extend it to more significant purchasing volumes.
Consider alternatives for challenges that weren’t addressed successfully in the first attempt.
Standardize any beneficial changes to ensure consistent application moving forward.
Use these standards as a benchmark for future PDCA cycles aiming for further improvements.
Benefits of Using the PDCA Cycle in Purchasing
Implementing the PDCA cycle in purchasing offers a host of benefits.
Mid-level employees adopting this approach can expect enhanced efficiency, cost savings, and better supplier relationships.
Here’s a deeper dive into these benefits:
Enhanced Efficiency
By identifying bottlenecks in the purchasing process, PDCA helps streamline operations.
Efficiency improvements can lead to faster procurement times and reduced manpower involved in routine checks.
More efficient processes result in quicker response times to market changes, allowing the organization to stay competitive.
Cost Savings
By reducing waste, over-ordering, and errors, the PDCA cycle can lead to significant cost savings.
Efficiencies gained from faster supplier negotiations and automated processes translate directly into financial benefits.
Improved cost management contributes positively to an organization’s bottom line.
Better Supplier Relationships
The cycle encourages ongoing evaluation and continuous improvement, fostering strong supplier partnerships.
It’s easier to collaborate on solutions when systems are regularly improved upon.
Engaged suppliers that grow alongside your process improvement efforts offer long-term benefits.
Conclusion: Integrating PDCA for Continuous Improvement
For mid-level employees, the PDCA cycle is an essential tool for elevating the purchasing processes.
It provides a structured approach that encourages continuous evaluation and improvements.
By addressing inefficiencies systematically through planning, implementation, evaluation, and adaptation, organizations can achieve substantial enhancements in their purchasing operations.
Successfully employing the PDCA cycle in purchasing processes not only promotes financial savings and efficiency but also supports sustained organizational success through continuous learning and improvement.
資料ダウンロード
QCD調達購買管理クラウド「newji」は、調達購買部門で必要なQCD管理全てを備えた、現場特化型兼クラウド型の今世紀最高の購買管理システムとなります。
ユーザー登録
調達購買業務の効率化だけでなく、システムを導入することで、コスト削減や製品・資材のステータス可視化のほか、属人化していた購買情報の共有化による内部不正防止や統制にも役立ちます。
NEWJI DX
製造業に特化したデジタルトランスフォーメーション(DX)の実現を目指す請負開発型のコンサルティングサービスです。AI、iPaaS、および先端の技術を駆使して、製造プロセスの効率化、業務効率化、チームワーク強化、コスト削減、品質向上を実現します。このサービスは、製造業の課題を深く理解し、それに対する最適なデジタルソリューションを提供することで、企業が持続的な成長とイノベーションを達成できるようサポートします。
オンライン講座
製造業、主に購買・調達部門にお勤めの方々に向けた情報を配信しております。
新任の方やベテランの方、管理職を対象とした幅広いコンテンツをご用意しております。
お問い合わせ
コストダウンが利益に直結する術だと理解していても、なかなか前に進めることができない状況。そんな時は、newjiのコストダウン自動化機能で大きく利益貢献しよう!
(Β版非公開)