- お役立ち記事
- Perspectives and Approaches to Solving Quality Problems
Perspectives and Approaches to Solving Quality Problems
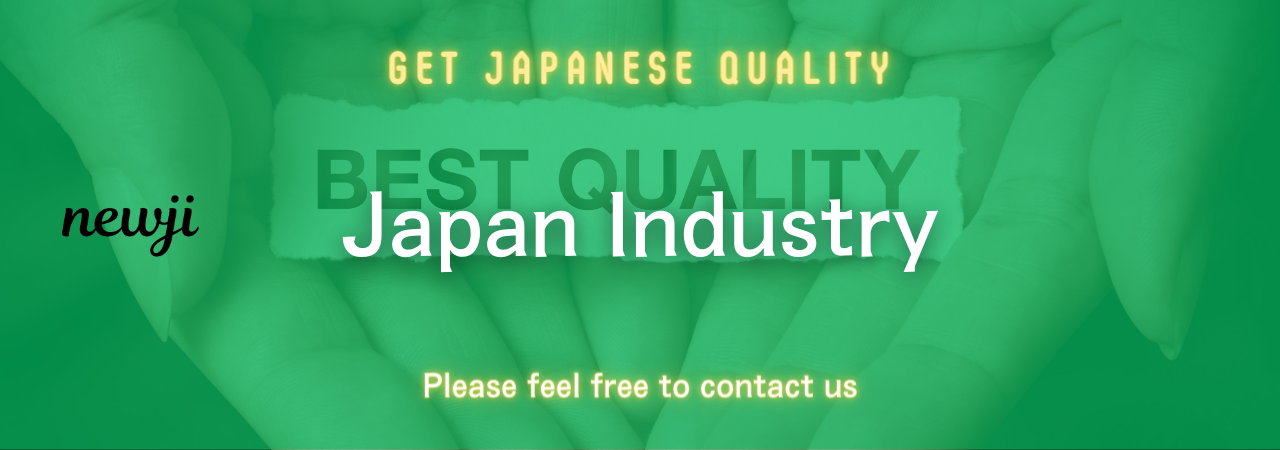
目次
Understanding Quality Problems
Quality problems can arise in various industries, affecting products, services, and overall customer satisfaction.
These issues range from production flaws, service downtimes, and even software bugs that compromise user experience.
The consequences of such problems can be detrimental to both reputation and financial health.
To effectively tackle and solve quality problems, having a clear perspective and a strategic approach is essential.
Identifying Root Causes
Gathering Data
The first step in addressing quality problems is to identify the root cause.
This starts with gathering accurate and comprehensive data.
Data collection can be performed through various methods such as customer feedback, quality control checks, and performance analytics.
By analyzing this data, teams can pinpoint patterns and anomalies that indicate underlying issues.
Using Tools for Root Cause Analysis
Several tools facilitate root cause analysis, including the Fishbone Diagram and the Five Whys technique.
The Fishbone Diagram helps visualize potential causes for a specific problem by categorizing them into different branches.
The Five Whys technique involves asking “why” multiple times until the fundamental cause is identified.
By employing these tools, organizations can move from symptoms to the core problem that needs solving.
Developing Solutions
Brainstorming Ideas
Once the root cause is identified, brainstorming sessions can help generate potential solutions.
Involve cross-functional teams to ensure diverse perspectives and expertise.
Encouraging open discussions can lead to innovative ideas that may not emerge within a siloed framework.
Evaluating Feasibility
Not all generated ideas will be practical or feasible.
It’s essential to evaluate solutions based on criteria such as cost, time, and impact.
Cost-benefit analysis and risk assessment can help narrow down the best options.
Select solutions that provide maximum benefit with the least risk.
Implementing Solutions
Planning the Implementation
Implementing solutions requires meticulous planning.
Create a detailed action plan that outlines the steps, resources, and timelines needed.
Assign responsibilities to team members and ensure they have the necessary tools and support to execute their roles.
Monitoring Progress
Monitoring is crucial to ensure that the implementation is on track.
Regular progress reviews and updates can help identify any deviations or obstacles.
Use performance metrics to track the effectiveness of the implemented solutions.
If needed, make adjustments to the action plan to address any emerging issues.
Continuous Improvement
Feedback Mechanism
Implementing a feedback mechanism helps maintain quality and encourages continuous improvement.
Collect feedback from customers, employees, and stakeholders regularly.
Analyze this feedback to identify areas for further improvement.
Adopting Best Practices
Staying abreast of industry best practices can provide insights into optimizing quality management.
Attend industry conferences, read relevant publications, and network with other professionals to learn about new techniques and tools.
Adopting these practices can help your organization remain competitive and maintain high-quality standards.
Training and Development
Equipping Staff
A well-trained staff is crucial in maintaining quality.
Regular training programs can equip employees with the skills and knowledge needed to perform their roles effectively.
Workshops, seminars, and online courses can provide continuous learning opportunities.
Promoting a Quality Culture
Promote a culture where quality is a priority.
Encourage employees to take ownership and responsibility for quality.
Recognize and reward those who contribute to quality improvements.
Fostering an environment where quality is valued can significantly reduce quality problems.
Leveraging Technology
Automation and Analytics
Technology plays a significant role in solving quality problems.
Automation can help in reducing human errors and increasing efficiency.
Analytics tools can provide in-depth insights into quality trends and pinpoint areas of concern.
By leveraging these technologies, organizations can enhance their quality control processes.
Utilizing Software Solutions
Software solutions like Quality Management Systems (QMS) can streamline processes and documentation.
These systems ensure compliance with industry standards and regulations.
They also facilitate easier tracking and resolving of quality issues.
Engaging External Expertise
Consulting Services
Sometimes, internal resources may not be sufficient to address certain quality problems.
Engaging external consultants can provide specialized expertise and fresh perspectives.
Consultants can offer tailored solutions and strategies that align with your organization’s goals.
Collaboration with Partners
Collaboration with industry partners can also be beneficial.
Sharing knowledge and resources with other organizations can lead to innovative solutions.
Partnerships can provide access to new technologies and best practices.
Conclusion
Quality problems can pose significant challenges but adopting a structured approach can lead to effective solutions.
By identifying root causes, developing feasible solutions, and implementing them systematically, organizations can enhance their quality standards.
Continuous improvement, training, technology, and external expertise further bolster these efforts.
With these approaches, quality problems can be transformed into opportunities for growth and excellence.
資料ダウンロード
QCD調達購買管理クラウド「newji」は、調達購買部門で必要なQCD管理全てを備えた、現場特化型兼クラウド型の今世紀最高の購買管理システムとなります。
ユーザー登録
調達購買業務の効率化だけでなく、システムを導入することで、コスト削減や製品・資材のステータス可視化のほか、属人化していた購買情報の共有化による内部不正防止や統制にも役立ちます。
NEWJI DX
製造業に特化したデジタルトランスフォーメーション(DX)の実現を目指す請負開発型のコンサルティングサービスです。AI、iPaaS、および先端の技術を駆使して、製造プロセスの効率化、業務効率化、チームワーク強化、コスト削減、品質向上を実現します。このサービスは、製造業の課題を深く理解し、それに対する最適なデジタルソリューションを提供することで、企業が持続的な成長とイノベーションを達成できるようサポートします。
オンライン講座
製造業、主に購買・調達部門にお勤めの方々に向けた情報を配信しております。
新任の方やベテランの方、管理職を対象とした幅広いコンテンツをご用意しております。
お問い合わせ
コストダウンが利益に直結する術だと理解していても、なかなか前に進めることができない状況。そんな時は、newjiのコストダウン自動化機能で大きく利益貢献しよう!
(Β版非公開)