- お役立ち記事
- Pick-and-Place Technology for Manufacturing Efficiency
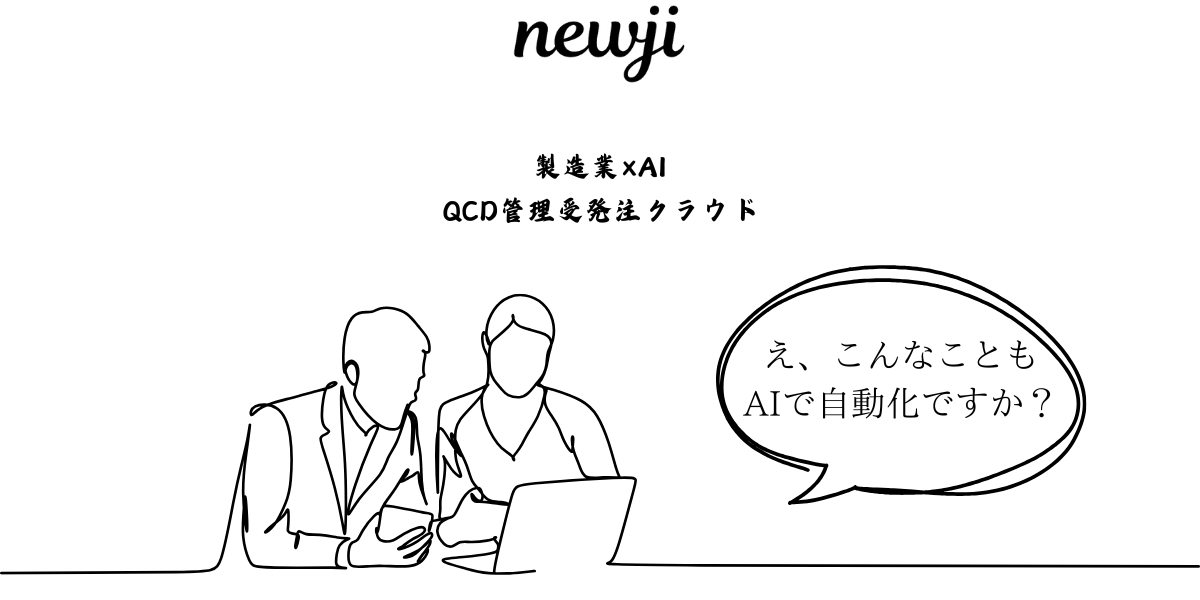
Pick-and-Place Technology for Manufacturing Efficiency
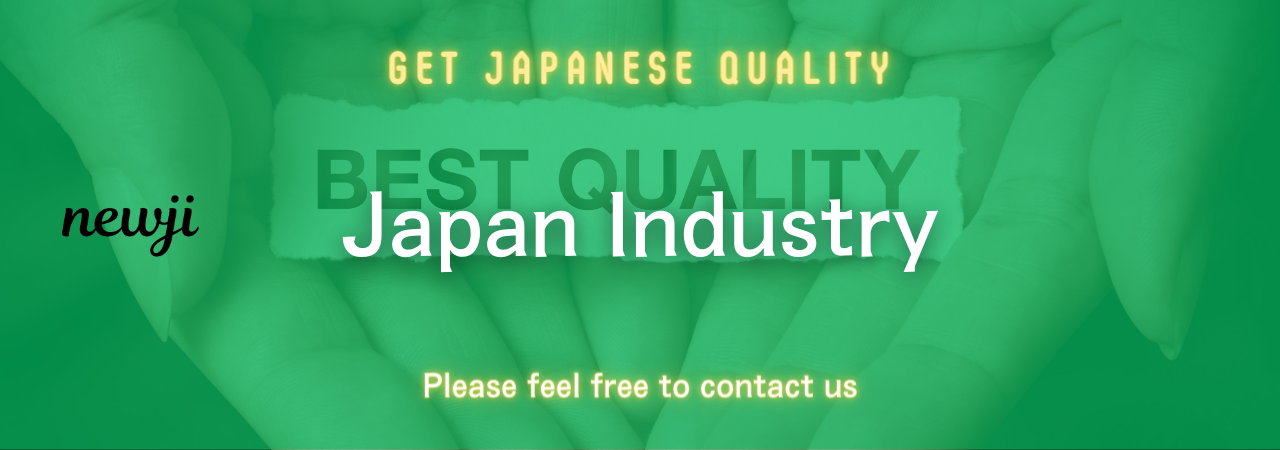
目次
What is Pick-and-Place Technology?
Pick-and-place technology is an automated manufacturing process that involves the use of robotic systems to pick up components or products and place them in designated locations accurately.
This modern technology is widely used in various industries to enhance manufacturing efficiency by reducing human error and speeding up the production process.
Robotic arms equipped with sensors and software are central to this technology, allowing precise movements and placements without human intervention.
How Does Pick-and-Place Technology Work?
The technology primarily relies on robotic arms or automated equipment that can mimic the dexterity of human hands.
These systems are programmed to perform specific tasks such as picking up parts from a conveyor belt and placing them on an assembly line or assembling parts into a final product.
The process begins with a machine vision system that identifies and locates the target objects.
This information is fed into the robot’s control system, providing the necessary data to perform precise pick-and-place actions.
The robotic arm, often equipped with suction cups, grippers, or other end-effectors, captures the object and moves it to its designated location.
The Role of Machine Vision in Pick-and-Place
Machine vision plays a crucial role in the effectiveness of pick-and-place systems.
It involves the use of cameras and sensors that enable robots to “see” and “understand” the environment.
This system captures images of the workspace, processes them, and sends the data to the robot’s control mechanisms.
With this technology, robots can identify the position, orientation, and even the quality of the components to be manipulated, ensuring precision and efficiency.
Machine vision enables robots to adapt to changes in the workspace, such as shifts in object positions or variations in size and shape, allowing for greater flexibility in operations.
Benefits of Pick-and-Place Technology
Pick-and-place technology offers several advantages that contribute to increased manufacturing efficiency.
Increased Productivity
One of the most significant benefits is the boost in productivity.
Robots can operate continuously without breaks, processing components faster than human workers.
This constant pace reduces production time and increases the output volume, allowing companies to meet higher demands with ease.
Enhanced Precision and Quality
Automated systems can achieve levels of precision that are challenging for humans to match.
Robots are programmed to follow exact pathways and exert consistent forces, resulting in accurate placements and reducing the chance of errors.
Moreover, automated systems can maintain consistent quality by adhering to set parameters, inspecting every component during processing to ensure it meets the required standards.
Cost Savings
Though the initial setup for pick-and-place systems can be costly, long-term savings are substantial.
Automation reduces the reliance on manual labor, leading to lower operational costs.
It also minimizes the waste of materials, as precise placement reduces errors and defects in the assembly process.
Additionally, automated systems tend to have lower maintenance costs due to their ability to consistently perform tasks with minimal wear and tear.
Enhanced Safety
With robots taking over tasks that are potentially hazardous for humans, workplace safety is significantly improved.
Robots can handle tasks in environments that may pose risks, such as those involving heavy lifting, toxic substances, or high temperatures.
This reduces the likelihood of workplace accidents and injuries, creating a safer work environment.
Applications of Pick-and-Place Technology
Pick-and-place technology is versatile and can be found in a variety of industries.
Electronics Manufacturing
In the electronics industry, pick-and-place machines are used for surface-mount technology (SMT) to place electronic components onto printed circuit boards (PCBs).
This application ensures the precise placement of components crucial for small-scale and intricate electronics.
Food and Beverage Industry
Robots are used to handle products on production lines, sorting and packaging them efficiently.
They can also perform quality control tasks, identifying defective products or ensuring packaging is error-free.
Automotive Industry
Pick-and-place systems assist in assembling automotive parts, which need precision due to the complexity and safety requirements of vehicle components.
Robots help in placing parts in difficult-to-reach areas and work seamlessly in synchronization with other automated systems to ensure a smooth production flow.
Pharmaceutical Industry
In pharmaceuticals, precision and hygiene are paramount.
Pick-and-place robots ensure that products are handled with care and precision while maintaining hygiene standards, essential in the production and packaging of medicines.
Challenges in Implementing Pick-and-Place Technology
While beneficial, implementing pick-and-place technology comes with challenges.
High Initial Costs
The cost of acquisition and installation of advanced robotic systems can be a barrier for smaller companies.
However, these costs can often be offset over time through gains in efficiency and productivity.
Complexity of Integration
Integrating robotic systems with existing manufacturing processes can be complex and requires technical expertise.
Firms must invest in skilled labor and training to ensure a smooth transition.
Maintenance and Upkeep
Despite being reliable, robotic systems require regular maintenance to function optimally.
This could involve retraining systems when processes change, updating software, or replacing worn parts.
The Future of Pick-and-Place Technology
As technology advances, pick-and-place systems are expected to become even more sophisticated and integrated into manufacturing processes.
Future developments may include enhanced artificial intelligence, machine learning capabilities, and improved sensors for better adaptability.
The increasing demand for customized products will likely push the development of pick-and-place technologies that can handle more complex and varied tasks with greater flexibility.
Ultimately, pick-and-place technology is poised to remain a critical component in the landscape of smart manufacturing, offering the keys to unlocking greater efficiency and competitiveness in various industries.
資料ダウンロード
QCD調達購買管理クラウド「newji」は、調達購買部門で必要なQCD管理全てを備えた、現場特化型兼クラウド型の今世紀最高の購買管理システムとなります。
ユーザー登録
調達購買業務の効率化だけでなく、システムを導入することで、コスト削減や製品・資材のステータス可視化のほか、属人化していた購買情報の共有化による内部不正防止や統制にも役立ちます。
NEWJI DX
製造業に特化したデジタルトランスフォーメーション(DX)の実現を目指す請負開発型のコンサルティングサービスです。AI、iPaaS、および先端の技術を駆使して、製造プロセスの効率化、業務効率化、チームワーク強化、コスト削減、品質向上を実現します。このサービスは、製造業の課題を深く理解し、それに対する最適なデジタルソリューションを提供することで、企業が持続的な成長とイノベーションを達成できるようサポートします。
オンライン講座
製造業、主に購買・調達部門にお勤めの方々に向けた情報を配信しております。
新任の方やベテランの方、管理職を対象とした幅広いコンテンツをご用意しております。
お問い合わせ
コストダウンが利益に直結する術だと理解していても、なかなか前に進めることができない状況。そんな時は、newjiのコストダウン自動化機能で大きく利益貢献しよう!
(Β版非公開)