- お役立ち記事
- Pioneering Precision: How Laser Welding Machines are Revolutionizing Japanese Manufacturing
Pioneering Precision: How Laser Welding Machines are Revolutionizing Japanese Manufacturing
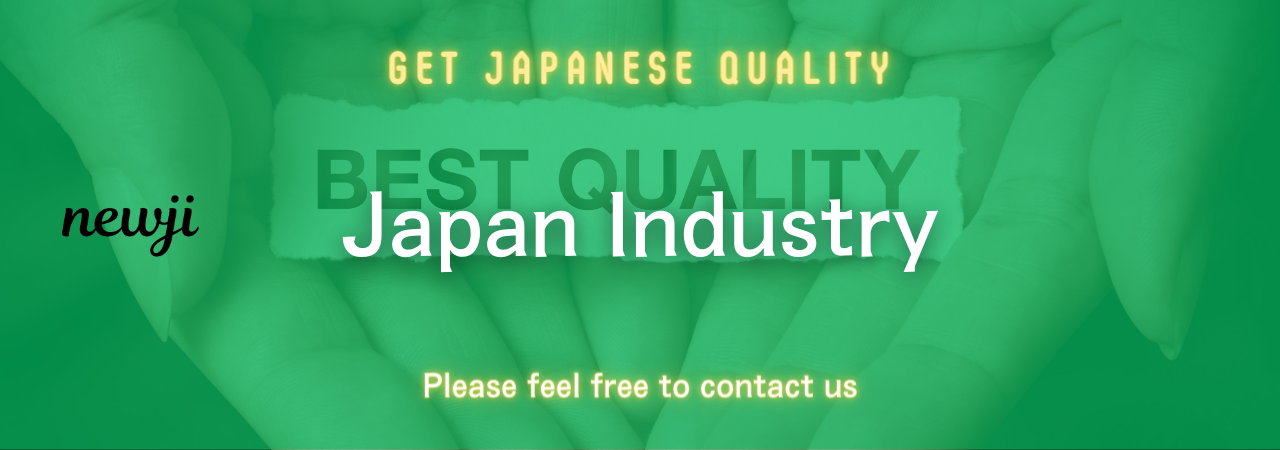
目次
Introduction to Laser Welding in Japanese Manufacturing
Laser welding technology has emerged as a pivotal innovation in Japanese manufacturing.
This advanced technique offers unparalleled precision and efficiency.
Japanese manufacturers have been at the forefront of integrating laser welding machines into their production lines.
The adoption of this technology has revolutionized various industries, from automotive to electronics.
This article explores how laser welding machines are transforming Japanese manufacturing, highlighting the benefits, challenges, and best practices associated with their implementation.
The Evolution of Laser Welding Technology
Laser welding technology has evolved significantly over the past few decades.
Initially developed for specialized applications, it has now become integral to mainstream manufacturing processes.
The continuous advancements in laser technology have enhanced beam quality, power, and control.
Japanese manufacturers have played a crucial role in this evolution, investing heavily in research and development.
Their commitment to innovation has led to the creation of highly efficient and reliable laser welding machines.
These advancements have enabled manufacturers to achieve higher precision and faster production cycles.
Key Developments in Laser Welding
Recent developments in laser welding include the introduction of fiber lasers and hybrid laser systems.
Fiber lasers offer higher beam quality and better energy efficiency compared to traditional CO2 lasers.
Hybrid systems combine laser welding with other welding methods, providing greater flexibility and control.
These advancements have expanded the applications of laser welding, making it suitable for a wider range of materials and thicknesses.
Japanese manufacturers have leveraged these developments to enhance their production capabilities and maintain a competitive edge in the global market.
Advantages of Laser Welding Machines
Laser welding machines offer numerous advantages that contribute to their widespread adoption in Japanese manufacturing.
These benefits encompass improved precision, increased speed, and enhanced versatility.
By understanding these advantages, manufacturers can make informed decisions about integrating laser welding into their production processes.
Precision and Quality
One of the most significant advantages of laser welding is its exceptional precision.
The focused laser beam allows for precise control over the welding process, ensuring accurate weld spots and minimal thermal distortion.
This precision is crucial in industries where high-quality welds are essential for product performance and safety.
Japanese manufacturers utilize this feature to produce components with tight tolerances and superior quality.
Efficiency and Speed
Laser welding machines operate at high speeds, significantly reducing production time compared to traditional welding methods.
The automation capabilities of these machines streamline the welding process, minimizing the need for manual intervention.
This efficiency leads to increased throughput and lower production costs.
In a competitive manufacturing landscape, the ability to produce high-quality products quickly is a major advantage.
Versatility and Flexibility
Laser welding is highly versatile, capable of welding various materials, including metals, plastics, and composites.
The technology can be adapted to different thicknesses and joint configurations, making it suitable for diverse applications.
Japanese manufacturers benefit from this flexibility by using laser welding machines across multiple production lines and product types.
This adaptability enhances the overall manufacturing process, allowing for quick adjustments to meet changing market demands.
Disadvantages and Challenges
While laser welding machines offer numerous benefits, they also present certain challenges that manufacturers must address.
Understanding these disadvantages is essential for effective implementation and maximizing the technology’s potential.
High Initial Investment
The acquisition of laser welding machines requires a substantial initial investment.
The cost of the equipment, installation, and training can be significant, especially for small to medium-sized enterprises.
Japanese manufacturers often mitigate this challenge by adopting phased implementation strategies and seeking financial support or incentives.
Despite the high upfront costs, the long-term benefits of increased efficiency and reduced labor costs can justify the investment.
Technical Expertise Requirement
Operating and maintaining laser welding machines demands specialized technical expertise.
Manufacturers need to invest in training their workforce to handle the intricacies of the technology.
Japanese companies typically address this by fostering a culture of continuous learning and providing extensive training programs.
The development of in-house expertise ensures the smooth operation of laser welding systems and the ability to troubleshoot issues effectively.
Maintenance and Downtime
Like any advanced machinery, laser welding machines require regular maintenance to ensure optimal performance.
Unplanned downtime due to equipment failure can disrupt production schedules and incur additional costs.
Japanese manufacturers prioritize preventive maintenance practices to minimize downtime and extend the lifespan of their laser welding machines.
Implementing robust maintenance protocols and investing in reliable equipment can help mitigate these challenges.
Supplier Negotiation Techniques for Laser Welding Machines
Effective supplier negotiation is critical for procuring laser welding machines at favorable terms.
Japanese manufacturers employ various strategies to negotiate with suppliers, ensuring they receive the best value for their investment.
Understanding Market Conditions
Before entering negotiations, it is essential to understand the current market conditions for laser welding machines.
This includes knowledge of pricing trends, availability of advanced features, and the competitive landscape.
Japanese manufacturers conduct thorough market research to gain insights into supplier offerings and identify potential negotiation leverage points.
Building Strong Relationships
Building and maintaining strong relationships with suppliers is a fundamental strategy in Japanese business culture.
Trust and mutual respect are crucial for long-term partnerships.
Manufacturers often engage in regular communication and collaborative problem-solving with suppliers, fostering a sense of partnership that can lead to more favorable negotiation outcomes.
Leveraging Volume and Long-Term Contracts
Manufacturers can negotiate better terms by committing to larger purchase volumes or long-term contracts.
Suppliers are more willing to offer discounts and favorable payment terms when there is a guarantee of sustained business.
Japanese manufacturers leverage their purchasing power and commitment to secure advantageous deals that benefit both parties.
Quality Assurance and Technical Specifications
Ensuring that the laser welding machines meet specific quality and technical specifications is a key aspect of negotiations.
Manufacturers clearly communicate their requirements and expectations to suppliers, negotiating terms that include quality guarantees and after-sales support.
This focus on quality ensures that the machines perform reliably and meet the production standards required by Japanese manufacturing processes.
Best Practices in Procuring Laser Welding Machines
Adopting best practices in procurement can enhance the efficiency and effectiveness of acquiring laser welding machines.
Japanese manufacturers implement a range of strategies to optimize their procurement processes and ensure successful integration of the technology.
Comprehensive Needs Assessment
A thorough needs assessment is the foundation of effective procurement.
Manufacturers evaluate their production requirements, identify the specific features needed in laser welding machines, and consider future scalability.
This strategic approach ensures that the selected equipment aligns with current and anticipated manufacturing needs.
Vendor Evaluation and Selection
Evaluating and selecting the right vendor is critical for successful procurement.
Japanese manufacturers assess potential suppliers based on factors such as product quality, reliability, technical support, and reputation in the industry.
Conducting site visits, reviewing customer testimonials, and comparing product specifications are common practices in the vendor selection process.
Negotiating Total Cost of Ownership
Focusing on the total cost of ownership (TCO) rather than just the purchase price is a best practice in procurement.
TCO includes not only the initial cost of the machine but also ongoing expenses such as maintenance, energy consumption, and training.
Japanese manufacturers negotiate terms that consider the long-term financial implications, ensuring a cost-effective investment.
Implementing Pilot Programs
Before full-scale implementation, manufacturers often conduct pilot programs to test the performance of laser welding machines.
Pilot programs allow for the evaluation of equipment under actual production conditions, identifying any potential issues and ensuring compatibility with existing processes.
This cautious approach minimizes risks and facilitates smoother integration of the technology into the manufacturing workflow.
Impact of Laser Welding on Production Management
Laser welding technology significantly influences production management strategies in Japanese manufacturing.
The precision and efficiency of laser welding machines enable manufacturers to optimize their production processes and enhance overall operational performance.
Streamlining Production Processes
Laser welding machines streamline production processes by reducing the number of steps required to achieve high-quality welds.
This simplification leads to shorter production cycles and increased throughput.
Manufacturers can allocate resources more effectively, focusing on other critical aspects of production without compromising quality.
Enhancing Quality Control
The consistent precision of laser welding contributes to enhanced quality control.
Manufacturers can achieve uniform welds, reducing variability and defects in the final products.
This reliability is essential for maintaining high standards and meeting the stringent quality requirements of Japanese manufacturing.
Improving Supply Chain Efficiency
By integrating laser welding machines into their production lines, manufacturers can improve supply chain efficiency.
The reduced production time and increased reliability of welds lead to more predictable production schedules.
This predictability enables better coordination with suppliers and distributors, enhancing the overall efficiency of the supply chain.
Market Conditions for Laser Welding in Japan
The market for laser welding machines in Japan is characterized by robust demand, technological innovation, and competitive dynamics.
Understanding the current market conditions is essential for manufacturers looking to invest in this technology.
Demand Drivers
Several factors drive the demand for laser welding machines in Japan.
The ongoing pursuit of high precision and quality in manufacturing, coupled with the need for increased production efficiency, fuels the adoption of laser welding technology.
Additionally, the growing demand for lightweight and durable components in industries such as automotive and aerospace further propels the market.
Competitive Landscape
The laser welding machine market in Japan is highly competitive, with numerous domestic and international players vying for market share.
Japanese manufacturers benefit from a strong network of local suppliers and a culture of continuous improvement.
This competition drives innovation and ensures that manufacturers have access to the latest technologies and advancements in laser welding.
Technological Trends
Technological trends in the laser welding market include the integration of automation and robotics, the development of hybrid laser systems, and advancements in beam control and precision.
Japanese manufacturers are quick to adopt these trends, investing in cutting-edge technologies to enhance their production capabilities and maintain their competitive edge.
Future Outlook for Laser Welding in Japanese Manufacturing
The future of laser welding in Japanese manufacturing looks promising, with continued advancements and expanding applications.
As technology evolves, laser welding machines are expected to become even more integral to manufacturing processes.
Advancements in Automation and Smart Manufacturing
The integration of laser welding with automation and smart manufacturing systems is set to enhance production efficiency and flexibility.
Japanese manufacturers are investing in smart factories where laser welding machines are seamlessly integrated into automated production lines.
This synergy between laser welding and automation technologies will lead to more agile and responsive manufacturing processes.
Expansion into New Industries
Laser welding technology is poised to expand into new industries beyond traditional sectors.
Emerging industries such as renewable energy, medical devices, and electronics present new opportunities for laser welding applications.
Japanese manufacturers are exploring these avenues, leveraging their expertise to cater to diverse market needs and drive growth.
Sustainability and Energy Efficiency
Sustainability and energy efficiency are becoming increasingly important in manufacturing.
Laser welding machines, with their high precision and reduced material waste, contribute to more sustainable production practices.
Japanese manufacturers are focusing on developing energy-efficient laser welding systems that align with global sustainability goals and reduce the environmental impact of manufacturing operations.
Conclusion
Laser welding machines are revolutionizing Japanese manufacturing by offering unparalleled precision, efficiency, and versatility.
Despite challenges such as high initial investments and the need for specialized expertise, the benefits of laser welding technology make it a valuable asset for manufacturers.
Effective supplier negotiation and adherence to best practices in procurement further enhance the successful integration of laser welding into production processes.
As the technology continues to evolve, its impact on production management and the broader manufacturing landscape in Japan will only grow.
Japanese manufacturers, known for their commitment to quality and innovation, are well-positioned to lead the way in harnessing the full potential of laser welding technology, driving advancements and maintaining their competitive edge in the global market.
資料ダウンロード
QCD調達購買管理クラウド「newji」は、調達購買部門で必要なQCD管理全てを備えた、現場特化型兼クラウド型の今世紀最高の購買管理システムとなります。
ユーザー登録
調達購買業務の効率化だけでなく、システムを導入することで、コスト削減や製品・資材のステータス可視化のほか、属人化していた購買情報の共有化による内部不正防止や統制にも役立ちます。
NEWJI DX
製造業に特化したデジタルトランスフォーメーション(DX)の実現を目指す請負開発型のコンサルティングサービスです。AI、iPaaS、および先端の技術を駆使して、製造プロセスの効率化、業務効率化、チームワーク強化、コスト削減、品質向上を実現します。このサービスは、製造業の課題を深く理解し、それに対する最適なデジタルソリューションを提供することで、企業が持続的な成長とイノベーションを達成できるようサポートします。
オンライン講座
製造業、主に購買・調達部門にお勤めの方々に向けた情報を配信しております。
新任の方やベテランの方、管理職を対象とした幅広いコンテンツをご用意しております。
お問い合わせ
コストダウンが利益に直結する術だと理解していても、なかなか前に進めることができない状況。そんな時は、newjiのコストダウン自動化機能で大きく利益貢献しよう!
(Β版非公開)