- お役立ち記事
- Pioneering the Future with Smart Factories: DX Strategies and Success Stories in Manufacturing
Pioneering the Future with Smart Factories: DX Strategies and Success Stories in Manufacturing
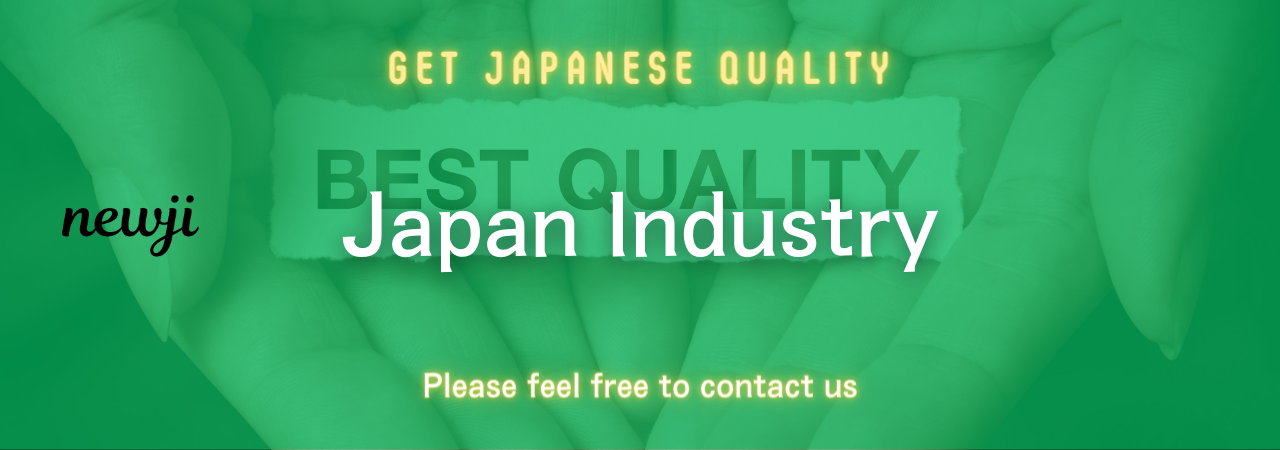
The rapid advancement of technology is revolutionizing virtually every industry, with manufacturing being one of the most transformed sectors.
Central to this transformation is the concept of “smart factories,” which represents the epitome of Digital Transformation (DX) in manufacturing.
Smart factories utilize cutting-edge technologies like the Internet of Things (IoT), Artificial Intelligence (AI), and robotics to optimize production processes, improve efficiency, and reduce operational costs.
目次
Understanding Smart Factories
What is a Smart Factory?
A smart factory is an integrated system that utilizes advanced information and manufacturing technologies like IoT, AI, and machine learning to create a highly digitized and connected production environment.
In a smart factory, machines and equipment are interconnected, enabling them to communicate and share data seamlessly.
This integration allows for real-time monitoring, predictive maintenance, and data-driven decision-making, all of which enhance overall productivity.
The Role of IoT in Smart Factories
The Internet of Things plays a crucial role in the functioning of smart factories.
By embedding sensors and devices within manufacturing equipment, companies can capture and analyze vast amounts of data.
This data provides insights into machine performance, energy consumption, and production output.
With IoT, manufacturers can predict equipment failures before they occur, leading to fewer downtimes and more efficient operations.
Key Strategies for Implementing Digital Transformation in Manufacturing
Developing a Clear Vision and Roadmap
The first step towards successful digital transformation is defining a clear vision of what the organization hopes to achieve.
This vision should align with the overall business strategy and goals.
Creating a detailed roadmap that outlines the steps, technologies, and resources required is crucial.
It ensures that every team member understands the journey’s direction and their role in it.
Investing in Technology
To build a smart factory, significant investment in the latest technologies is essential.
This includes IoT devices, AI-based systems, robotics, and advanced analytics platforms.
It’s essential to invest in scalable technologies that can grow with the business and adapt to future needs.
Partnering with technology providers can also offer the expertise and support needed to implement these solutions effectively.
Training and Upskilling Workforce
Digital transformation is not just about technology; it’s also about people.
For DX strategies to be successful, the workforce must be trained and upskilled to handle new technologies and processes.
Continuous education and training programs can help employees stay current with the latest advancements and improve their productivity.
Encouraging a culture of innovation and continuous improvement can also drive the adoption of new technologies.
Data Management and Analysis
The essence of a smart factory lies in its ability to harness data.
Effective data management and analysis are crucial for making informed decisions and optimizing operations.
Adopting advanced analytics tools can help manufacturers gain valuable insights from their data.
Implementing data governance policies ensures data accuracy, security, and compliance, which is critical for building trust and reliability in the system.
Success Stories of Smart Factories in Manufacturing
Case Study: Siemens Digital Factory
Siemens, a global leader in industrial automation, has fully embraced the concept of smart factories.
Their digital factory in Amberg, Germany, is a prime example of how DX can transform manufacturing.
By integrating IoT and AI technologies, Siemens has achieved a 99.99885% quality rate and increased productivity by 1400%.
The factory is now capable of producing more than 15 million devices per year, demonstrating the immense potential of smart factories.
Case Study: General Electric’s Brilliant Factory
General Electric (GE) has also made significant strides in implementing smart factory concepts through their “Brilliant Factory” initiative.
By leveraging IoT sensors, big data analytics, and digital twins, GE has transformed its manufacturing processes.
In their “Brilliant Factory” in Pune, India, they experienced a 20% increase in efficiency and a 10% reduction in production costs.
The ability to predict equipment failures and optimize production schedules has contributed to these impressive results.
Case Study: Bosch Industry 4.0
Bosch, a leader in engineering and electronics, has embraced the Industry 4.0 model, incorporating smart factory principles across its operations.
At their plant in Blaichach, Germany, Bosch utilized IoT and AI to achieve real-time transparency across the entire production process.
This has resulted in a significant reduction in machine downtime and enhanced productivity.
Their smart factory model is now being used as a blueprint for other Bosch plants globally, highlighting the scalability of smart factory solutions.
Challenges and Considerations
Cybersecurity Risks
With increased connectivity comes an elevated risk of cyberattacks.
Smart factories are vulnerable to various cyber threats, making it essential to implement robust cybersecurity measures.
Ensuring that all IoT devices and networks are secure is vital to prevent data breaches and protect intellectual property.
Regular security audits and updates can help mitigate these risks.
Initial Investment Costs
Implementing smart factory technologies involves substantial initial investments in equipment, software, and employee training.
While the long-term benefits are significant, the upfront costs can be a barrier for many manufacturers.
It’s crucial to develop a comprehensive financial plan that includes potential ROI to justify these investments.
Change Management
Transitioning to a smart factory model requires significant changes in processes, technologies, and culture.
Managing this change effectively is crucial to ensure smooth implementation and minimize resistance.
Developing a structured change management plan that includes clear communication, stakeholder involvement, and continuous support can ease the transition.
The Future of Smart Factories
The future of manufacturing lies in the continued evolution of smart factories.
As technologies such as IoT, AI, and machine learning continue to advance, smart factories will become even more efficient, flexible, and adaptive.
The integration of 5G technology is expected to further enhance connectivity and real-time data processing capabilities.
Moreover, the shift towards sustainability and green manufacturing will drive innovations in smart factory technologies, focusing on energy efficiency and reduced environmental impact.
In conclusion, smart factories represent the pinnacle of digital transformation in manufacturing, offering significant benefits in terms of efficiency, productivity, and cost savings.
By embracing DX strategies and learning from successful implementations, manufacturers can pioneer the future and stay competitive in the ever-evolving industrial landscape.
資料ダウンロード
QCD調達購買管理クラウド「newji」は、調達購買部門で必要なQCD管理全てを備えた、現場特化型兼クラウド型の今世紀最高の購買管理システムとなります。
ユーザー登録
調達購買業務の効率化だけでなく、システムを導入することで、コスト削減や製品・資材のステータス可視化のほか、属人化していた購買情報の共有化による内部不正防止や統制にも役立ちます。
NEWJI DX
製造業に特化したデジタルトランスフォーメーション(DX)の実現を目指す請負開発型のコンサルティングサービスです。AI、iPaaS、および先端の技術を駆使して、製造プロセスの効率化、業務効率化、チームワーク強化、コスト削減、品質向上を実現します。このサービスは、製造業の課題を深く理解し、それに対する最適なデジタルソリューションを提供することで、企業が持続的な成長とイノベーションを達成できるようサポートします。
オンライン講座
製造業、主に購買・調達部門にお勤めの方々に向けた情報を配信しております。
新任の方やベテランの方、管理職を対象とした幅広いコンテンツをご用意しております。
お問い合わせ
コストダウンが利益に直結する術だと理解していても、なかなか前に進めることができない状況。そんな時は、newjiのコストダウン自動化機能で大きく利益貢献しよう!
(Β版非公開)