- お役立ち記事
- Points for central ordering management and efficiency of factory consumables and office supplies
月間77,185名の
製造業ご担当者様が閲覧しています*
*2025年2月28日現在のGoogle Analyticsのデータより
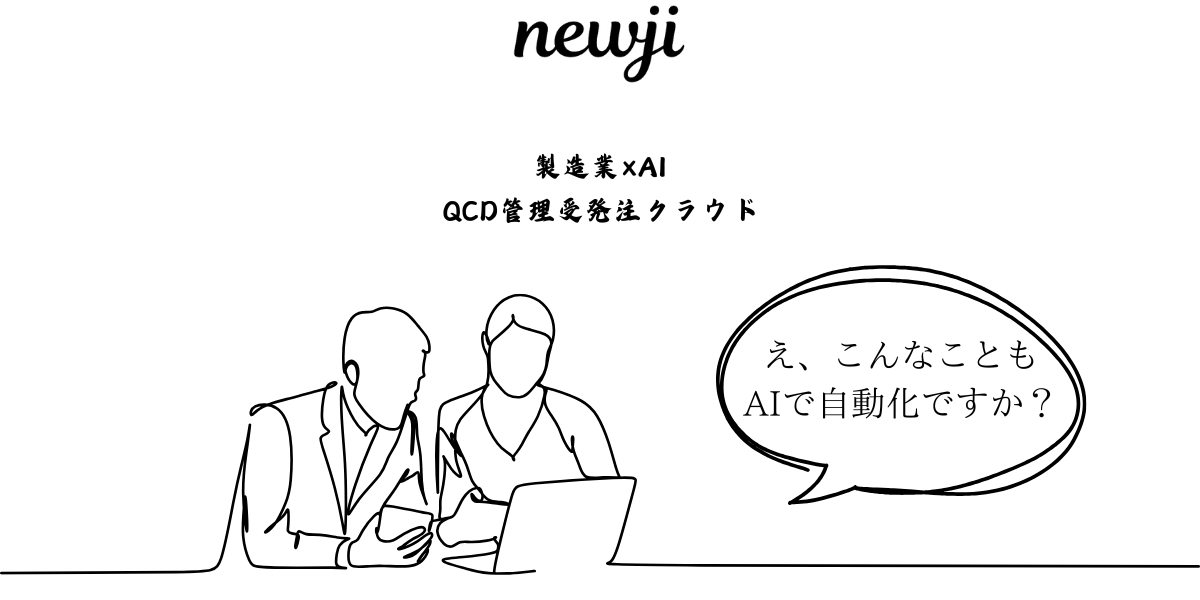
Points for central ordering management and efficiency of factory consumables and office supplies
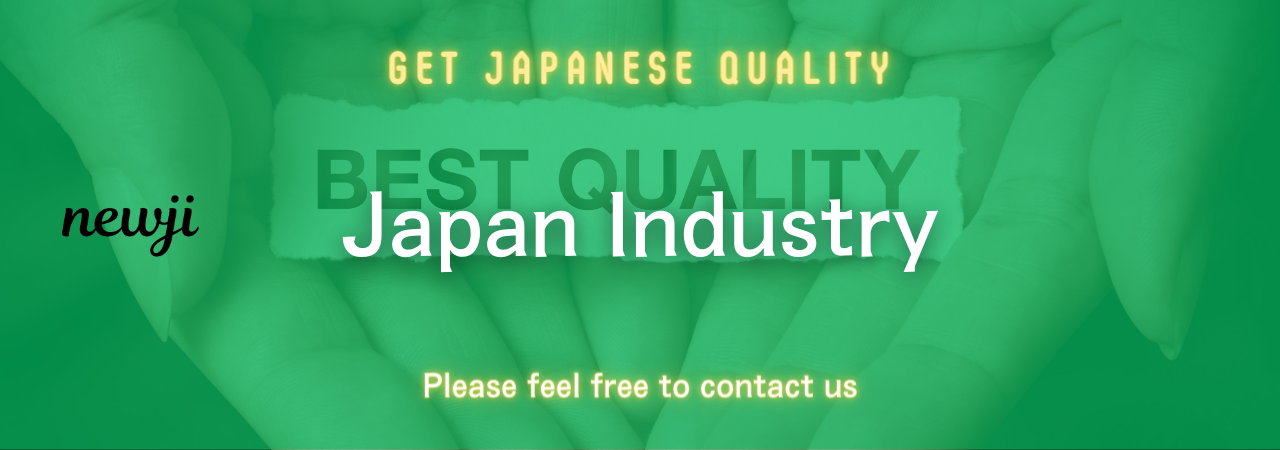
目次
Understanding Central Ordering Management
Central ordering management is an approach that aligns the procurement process in an organization, ensuring that essential materials such as factory consumables and office supplies are effectively ordered and managed from a single point within the organization.
This method is intended to streamline operations, reduce costs, and enhance efficiency.
By leveraging central ordering management, companies can better forecast needs, negotiate favorable terms with suppliers, and minimize redundancies in their supply chains.
Understanding this management approach is vital for any organization seeking to optimize their ordering processes.
In the context of both factory consumables and office supplies, central management involves creating a cohesive and unified system that manages procurement tasks and responsibilities.
This system will typically involve utilizing specialized software or platforms that allow for easier tracking of usage and supplies, submit ordering requests, and maintain communication with vendors.
Implementing a central system helps ensure that everyone in the organization follows the same procedures and protocols, thereby avoiding confusion and discrepancies.
Benefits of Central Ordering Management
One of the primary benefits of central ordering management is cost savings.
By pooling resources and ordering materials in bulk, companies can take advantage of economies of scale.
This often results in discount pricing from vendors, which reduces per-unit costs.
Additionally, with consolidated orders, companies typically incur less in shipping and delivery fees.
Another significant advantage is the enhancement of efficiency.
A central ordering system minimizes the time employees need to spend managing orders.
All requests are streamlined through a single channel, decreasing the time spent engaging with multiple suppliers, managing discrepancies, and responding to surprise shortages or overstock situations.
This streamlined approach results in employees having more time to focus on their core responsibilities.
Furthermore, central ordering management improves inventory control and forecasting.
By continually analyzing procurement data, organizations can better predict their needs based on historical consumption patterns, seasonal fluctuations, and upcoming projects.
This level of oversight also helps prevent ordering too much or too little, as the central management system provides accurate real-time data on stock levels and usage rates.
Implementing Central Ordering Management
To successfully implement a central ordering management system, an organization must first evaluate their current procurement processes.
This evaluation should identify any inefficiencies or areas where costs could be managed more effectively.
After this initial analysis, companies should then establish clear objectives, deciding whether their focus is on cost reduction, process improvement, supplier relationship enhancement, or a combination of these factors.
Next, a centralized procurement team should be appointed.
This team will be responsible for managing the procurement process, making inventory purchasing decisions, and interfacing with vendors.
They will also play a critical role in determining the new technological tools to be adopted for the new system.
The technological aspect is crucial.
Given the complexity of managing diverse materials, utilizing procurement management software can be invaluable.
These platforms often feature automated workflows, real-time data analytics, and supplier management tools, all of which make the procurement process more transparent and efficient.
Once the technological foundation is established, staff training becomes essential.
Providing adequate training ensures that all staff members are comfortable using the new systems and understand how their individual roles affect the overall procurement process.
Ongoing training and feedback can help boost engagement and adherence to the new system.
Challenges to Consider
While central ordering management holds many benefits, companies may encounter challenges during its implementation and operation.
One common issue is resistance to change.
Employees may be accustomed to sourcing their own consumables and office supplies, making them hesitant to shift to a centralized system.
To manage this, companies should highlight the benefits of the centralized approach and offer continuous support as employees transition.
Another challenge is the potential for initial costs related to software adoption, staff training, or restructuring teams.
These initial expenses should be regarded as investments that will lead to operational savings and efficiency improvements over time.
Businesses must carefully plan and allocate budgets to address these upfront costs.
Finally, choosing the right suppliers and negotiating favorable terms can be a complex task.
The centralized procurement team must consistently evaluate and establish relationships with suppliers to ensure the best quality materials at optimal costs.
Opportunities for negotiating better rates, exploring alternative supplies, or establishing vendor partnerships can greatly benefit the organization.
Maximizing Efficiency with Central Ordering
To maximize the efficiency gained through central ordering management, regular reviews and updates to policies and practices should be implemented.
A continuous review process helps in identifying new opportunities for cost-saving and more efficient processes.
Staying informed about industry trends and technological advancements also allows companies to continuously improve and upgrade their systems.
An essential aspect of maintaining efficiency is developing strong relationships with suppliers.
Good vendor relationships can lead to better product availability, pricing, and terms.
It enables high levels of communication and cooperation, allowing businesses to resolve any issues that arise quickly.
Additionally, integrating advanced technologies like artificial intelligence (AI) and machine learning can further enhance central ordering management.
These technologies can improve demand forecasting, identify purchasing patterns, and suggest reorder points automatically.
Adopting these technology-driven solutions creates a more proactive inventory management process and reduces the risks of human error.
In conclusion, the central ordering management of factory consumables and office supplies can be a game-changer for organizations looking to streamline operations and improve efficiency.
By implementing a centralized system, utilizing technology, and fostering strong supplier relationships, companies can reap benefits that positively impact their bottom line and operational effectiveness.
資料ダウンロード
QCD管理受発注クラウド「newji」は、受発注部門で必要なQCD管理全てを備えた、現場特化型兼クラウド型の今世紀最高の受発注管理システムとなります。
ユーザー登録
受発注業務の効率化だけでなく、システムを導入することで、コスト削減や製品・資材のステータス可視化のほか、属人化していた受発注情報の共有化による内部不正防止や統制にも役立ちます。
NEWJI DX
製造業に特化したデジタルトランスフォーメーション(DX)の実現を目指す請負開発型のコンサルティングサービスです。AI、iPaaS、および先端の技術を駆使して、製造プロセスの効率化、業務効率化、チームワーク強化、コスト削減、品質向上を実現します。このサービスは、製造業の課題を深く理解し、それに対する最適なデジタルソリューションを提供することで、企業が持続的な成長とイノベーションを達成できるようサポートします。
製造業ニュース解説
製造業、主に購買・調達部門にお勤めの方々に向けた情報を配信しております。
新任の方やベテランの方、管理職を対象とした幅広いコンテンツをご用意しております。
お問い合わせ
コストダウンが利益に直結する術だと理解していても、なかなか前に進めることができない状況。そんな時は、newjiのコストダウン自動化機能で大きく利益貢献しよう!
(β版非公開)