- お役立ち記事
- Points for designing and developing a production scheduling system to reduce lead time
Points for designing and developing a production scheduling system to reduce lead time
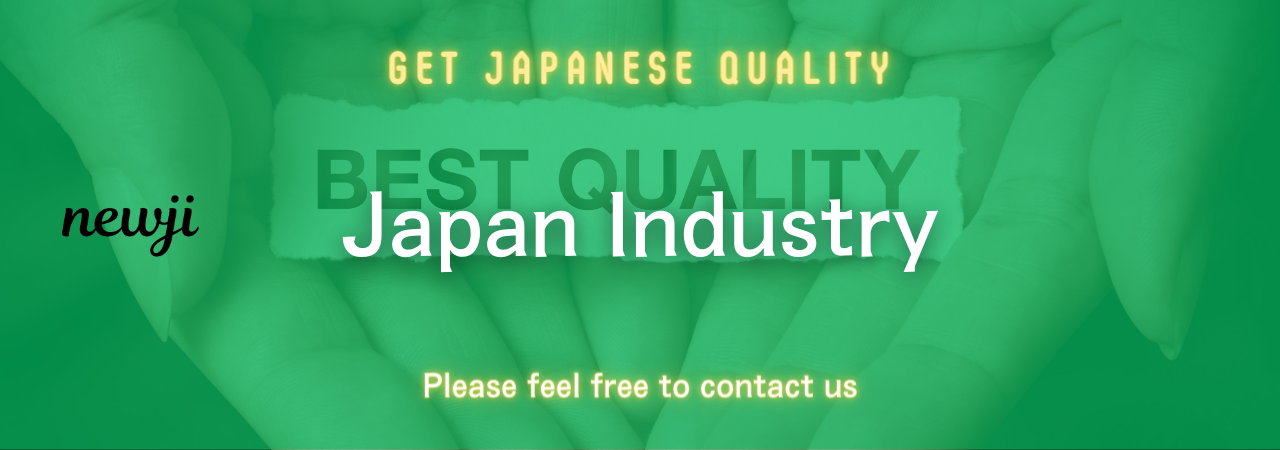
Understanding Production Scheduling Systems
Production scheduling systems are crucial for managing the complex processes involved in manufacturing.
These systems ensure that production runs smoothly by organizing work schedules, assigning tasks, and optimizing resources.
The primary goal is to reduce lead time, which is the total time from the start of a process to its completion.
Reducing lead time is essential for increasing efficiency and competitiveness in the manufacturing industry.
Identifying Key Components
To design an effective production scheduling system, it’s vital to identify the key components that will integrate seamlessly.
These components include material management, workforce scheduling, machinery allocation, and quality control.
By understanding these elements and how they interconnect, we can create a system that minimizes waste and maximizes productivity.
The Role of Technology
Technology plays a pivotal role in developing a production scheduling system.
Modern advancements, such as Artificial Intelligence (AI) and Machine Learning, can process large data sets to provide accurate forecasts and insights.
These technologies help in predicting demand, scheduling workforce efficiently, and managing inventory in real-time.
Integrating technology not only reduces lead time but also enhances the flexibility of the production processes.
Data Collection and Analysis
The foundation of a robust production scheduling system is comprehensive data collection and analysis.
Accurate data from various sources like supply chain logistics, customer demand, and production capabilities is critical.
This data allows us to build accurate models that simulate different production scenarios, identify bottlenecks, and develop strategies to overcome them.
Monitoring and analyzing this data continuously is essential for making informed decisions and adjustments swiftly.
Creating a Flexible System
Flexibility is crucial in production scheduling to adapt quickly to changes such as shifts in customer demand or supply chain disruptions.
Incorporating lean manufacturing principles can aid in creating more efficient systems.
This approach focuses on continuous improvement, eliminating waste, and ensuring all components interact effectively and are responsive to changes.
Flexibility in the system design helps businesses maintain a competitive edge by delivering products faster and responding to market needs promptly.
Developing a User-Friendly Interface
The interface of a production scheduling system should be user-friendly to enhance its effectiveness.
Operators and managers must easily interpret the data to facilitate quick decision-making.
The interface should be intuitive, providing clear visual insights such as dashboards, graphs, and alerts.
Training users on the functionalities of the system is equally important to ensure that they can leverage the system fully.
Integrating with Existing Systems
For a new production scheduling system to be successful, it should integrate seamlessly with existing systems like ERP (Enterprise Resource Planning) and MES (Manufacturing Execution Systems).
Integration ensures that all data flow smoothly across different departments, promoting collaboration and reducing redundancy.
This synchrony helps in optimizing the entire production process, from order receipt to product delivery.
Testing and Continuous Improvement
Before implementing a production scheduling system, extensive testing is essential.
Simulations can help identify potential issues and areas for improvement before live deployment.
Once in place, regular performance evaluations and updates are necessary.
Continuous improvement processes, such as gathering feedback from users and refining system algorithms, will keep the scheduling system efficient over time and further reduce lead time.
Challenges and Solutions
In designing and developing a production scheduling system, several challenges may arise.
These can include data accuracy, integration hurdles, and resistance to change from staff.
To tackle these challenges, it’s essential to establish a clear change management strategy that includes engaging stakeholders early, providing comprehensive training, and setting realistic expectations.
Additionally, leveraging cloud-based solutions can help manage data storage costs and enhance system accessibility.
Conclusion
Designing and developing an effective production scheduling system requires careful planning, the right technology, and a focus on flexibility and user experience.
By reducing lead time, businesses can improve efficiency and customer satisfaction.
Continuous monitoring and improvement will ensure that the system remains relevant and effective in meeting the evolving demands of the manufacturing industry.
By addressing potential challenges proactively, businesses can ensure a smoother transition and maximize the benefits of their production scheduling systems.
資料ダウンロード
QCD調達購買管理クラウド「newji」は、調達購買部門で必要なQCD管理全てを備えた、現場特化型兼クラウド型の今世紀最高の購買管理システムとなります。
ユーザー登録
調達購買業務の効率化だけでなく、システムを導入することで、コスト削減や製品・資材のステータス可視化のほか、属人化していた購買情報の共有化による内部不正防止や統制にも役立ちます。
NEWJI DX
製造業に特化したデジタルトランスフォーメーション(DX)の実現を目指す請負開発型のコンサルティングサービスです。AI、iPaaS、および先端の技術を駆使して、製造プロセスの効率化、業務効率化、チームワーク強化、コスト削減、品質向上を実現します。このサービスは、製造業の課題を深く理解し、それに対する最適なデジタルソリューションを提供することで、企業が持続的な成長とイノベーションを達成できるようサポートします。
オンライン講座
製造業、主に購買・調達部門にお勤めの方々に向けた情報を配信しております。
新任の方やベテランの方、管理職を対象とした幅広いコンテンツをご用意しております。
お問い合わせ
コストダウンが利益に直結する術だと理解していても、なかなか前に進めることができない状況。そんな時は、newjiのコストダウン自動化機能で大きく利益貢献しよう!
(Β版非公開)