- お役立ち記事
- Points for selecting and using materials and processing methods in product design and manufacturing
月間77,185名の
製造業ご担当者様が閲覧しています*
*2025年2月28日現在のGoogle Analyticsのデータより
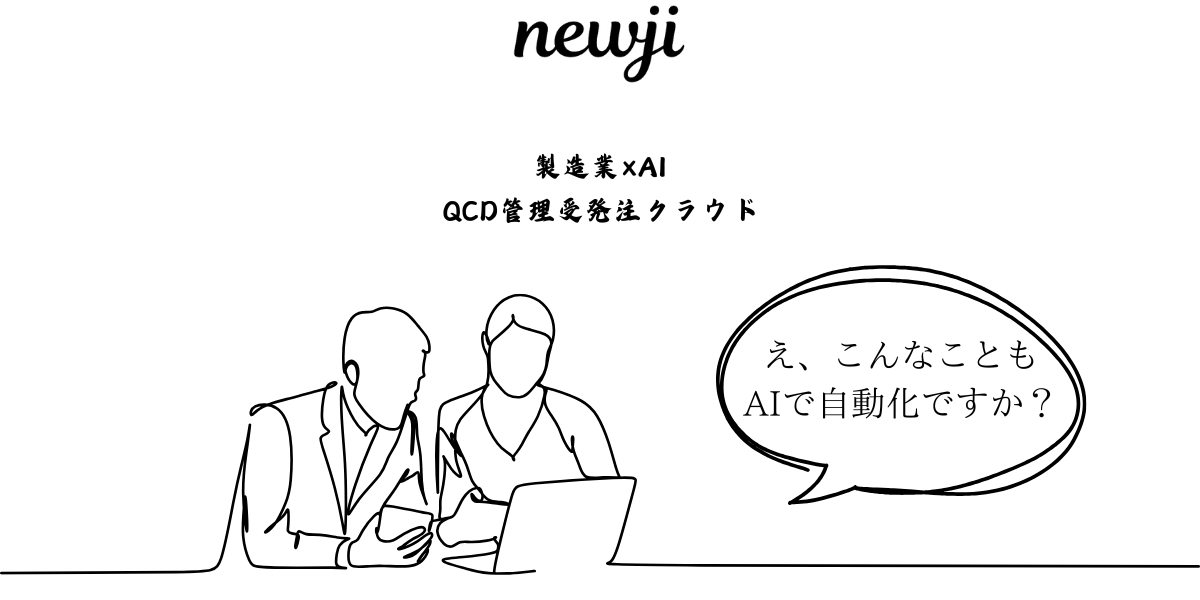
Points for selecting and using materials and processing methods in product design and manufacturing
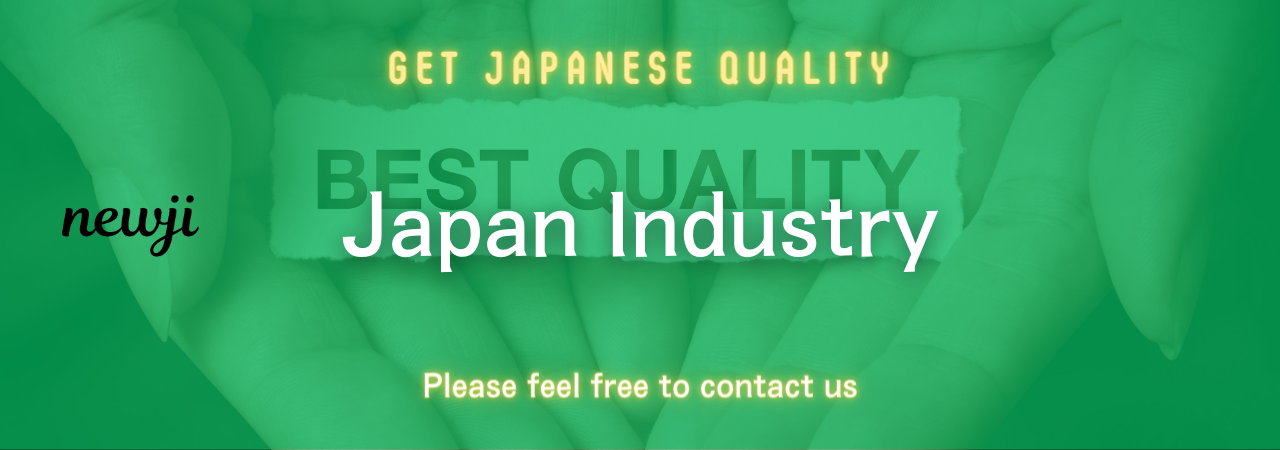
目次
Understanding Materials in Product Design
When it comes to product design and manufacturing, selecting the right materials is a crucial step.
The choice of materials affects not only the appearance and durability of the product but also its cost and environmental impact.
Understanding the properties of different materials allows designers to make informed decisions that balance aesthetics, functionality, and sustainability.
Metals, plastics, ceramics, and composites are some of the common materials used in product design.
Each of these materials has unique properties that make it suitable for specific applications.
Metals such as aluminum and steel are known for their strength and durability.
They are ideal for products that require robust structural components.
On the other hand, plastics are lightweight and versatile, making them popular for products where weight reduction is crucial, or complex shapes are needed.
Ceramics, with their heat-resistant properties, are often used in products that must withstand high temperatures.
Composites, which combine two or more materials, offer the advantage of customized properties.
They can be tailored to provide specific strengths, weights, or resistance characteristics not available in a single material.
Key Considerations for Material Selection
The primary factors to consider when choosing materials include functionality, cost, sustainability, and appearance.
**Functionality**: The material must meet the functional requirements of the product.
For example, a cookware manufacturer would prioritize materials that are heat-resistant and non-reactive.
**Cost**: Budget constraints are always part of the material selection process.
While high-performance materials may offer numerous benefits, they often come at a premium price.
The challenge is finding the right balance between performance and affordability.
**Sustainability**: With increasing environmental concerns, selecting sustainable materials has become a priority for many manufacturers.
This includes considering the material’s lifecycle, the energy required for production, and its recyclability.
**Appearance**: The aesthetics of the material can significantly impact consumer appeal.
Materials come in various colors, textures, and finishes, which can enhance the overall design of a product.
Exploring Processing Methods
Alongside material selection, choosing the right processing method is essential for successful product manufacturing.
Processing methods determine how materials are shaped, joined, and finished.
They also influence the final characteristics of the product, such as precision, strength, and appearance.
Common Processing Methods
Several processing methods are commonly used in manufacturing, each with specific benefits and limitations.
**Casting**: This process involves pouring liquid material into a mold where it solidifies.
Casting is suitable for producing complex shapes with minimal waste, making it ideal for metal and plastic components.
**Forming**: This method shapes materials by applying force, often through bending or stretching.
Forming is often used with metals to create strong, intricately shaped parts.
**Machining**: Involves removing material from a workpiece to achieve the desired shape.
CNC machines, for example, are highly precise and widely used in industries requiring tight tolerances.
**Joining**: Methods such as welding, riveting, or adhesive bonding are used to assemble different components.
Choosing the right joining technique is essential to ensure structural integrity and durability.
**Additive Manufacturing**: Often referred to as 3D printing, this method adds material layer-by-layer to create objects.
It is ideal for prototyping and complex designs that are difficult to achieve with traditional manufacturing methods.
Factors Influencing Processing Method Selection
The selection of a processing method involves considering several key factors.
**Material Compatibility**: Not all materials are suitable for every processing technique.
For example, certain plastics might be susceptible to thermal damage in some forming or machining processes.
**Production Volume**: Some methods are more cost-effective for large production runs, while others, like 3D printing, may be more suitable for small batches or custom items.
**Precision and Tolerances**: The required precision of the product can dictate the choice of processing method.
Machining, for instance, is preferred in applications requiring high precision.
**Cost**: The cost of tooling, equipment, and labor associated with a processing method is crucial in decision-making.
Initial setup costs for methods like casting can be high but become more economical with large volumes.
Integrating Material and Processing Choices
Achieving a successful product design involves the harmonious integration of material selection and processing methods.
Prototyping and Testing
Prototyping is an essential step in the integration process.
It allows designers to test material compatibility and processing capabilities.
Through this iterative process, designers can refine their choices to ensure the final product meets all design criteria.
Collaboration with Manufacturers
Early collaboration with manufacturers can provide valuable insights into material performance and processing efficiencies.
Manufacturers often have experience with various materials and can suggest alternatives or optimizations to improve the design and manufacturing process.
Evaluating Trade-offs
In many cases, selecting materials and processing methods involves evaluating trade-offs.
Prioritizing certain characteristics may mean compromising on others.
It is essential to keep the end-user in mind and to align decisions with the product’s intended purpose and market positioning.
Conclusion
Selecting the right materials and processing methods is a complex yet rewarding aspect of product design and manufacturing.
By understanding the unique properties and capabilities of various materials and processes, designers can create products that are not only functional and appealing but also cost-effective and sustainable.
Careful consideration of all these factors ensures that the final product is a perfect blend of innovation and practicality.
資料ダウンロード
QCD管理受発注クラウド「newji」は、受発注部門で必要なQCD管理全てを備えた、現場特化型兼クラウド型の今世紀最高の受発注管理システムとなります。
ユーザー登録
受発注業務の効率化だけでなく、システムを導入することで、コスト削減や製品・資材のステータス可視化のほか、属人化していた受発注情報の共有化による内部不正防止や統制にも役立ちます。
NEWJI DX
製造業に特化したデジタルトランスフォーメーション(DX)の実現を目指す請負開発型のコンサルティングサービスです。AI、iPaaS、および先端の技術を駆使して、製造プロセスの効率化、業務効率化、チームワーク強化、コスト削減、品質向上を実現します。このサービスは、製造業の課題を深く理解し、それに対する最適なデジタルソリューションを提供することで、企業が持続的な成長とイノベーションを達成できるようサポートします。
製造業ニュース解説
製造業、主に購買・調達部門にお勤めの方々に向けた情報を配信しております。
新任の方やベテランの方、管理職を対象とした幅広いコンテンツをご用意しております。
お問い合わせ
コストダウンが利益に直結する術だと理解していても、なかなか前に進めることができない状況。そんな時は、newjiのコストダウン自動化機能で大きく利益貢献しよう!
(β版非公開)