- お役立ち記事
- Points of on-site problem solving and quality assurance in the Toyota method
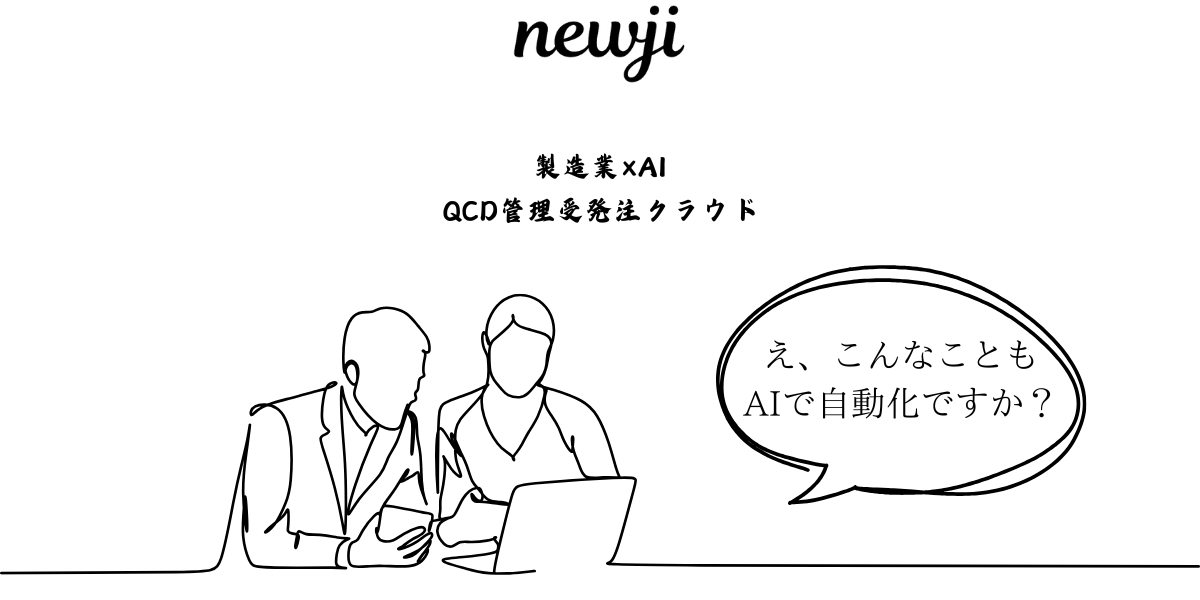
Points of on-site problem solving and quality assurance in the Toyota method
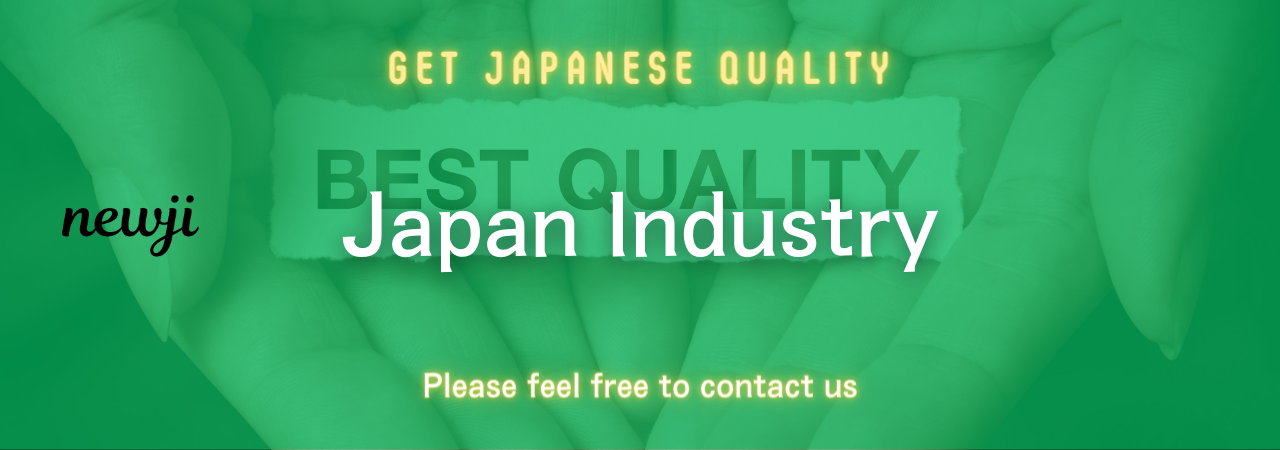
目次
Introduction to the Toyota Way
The Toyota method, often referred to as the Toyota Production System (TPS), is renowned for its focus on quality assurance and problem solving.
Originating from the automotive giant Toyota, this method has been integral in transforming the company into a leader in efficiency and quality.
The principles of the Toyota method have been adopted by numerous industries worldwide, proving their versatility and effectiveness.
In this guide, we’ll delve into the points of on-site problem solving and quality assurance within the Toyota method.
Understanding these concepts can significantly enhance the operational efficiency of any business.
Understanding the Core Principles
To fully grasp the Toyota method, one must first understand its core principles.
These principles include Kaizen, or continuous improvement, and Genchi Genbutsu, meaning “go and see.”
Both of these tenets emphasize the importance of tackling problems directly at their source.
Kaizen promotes a culture where employees at all levels are encouraged to suggest improvements, fostering an environment of constant enhancement.
On the other hand, Genchi Genbutsu encourages leaders and workers to go to the actual place, referred to as the “Gemba,” to see the real issues and gather firsthand information.
This direct approach ensures that problems are addressed accurately and effectively.
On-Site Problem Solving
The cornerstone of on-site problem solving in the Toyota method is the belief that problems must be dealt with where they actually occur.
This hands-on approach is known as Gemba, which means “the real place” in Japanese.
It involves several steps aimed at tackling issues face-to-face, ensuring no detail is overlooked.
The Role of Gemba Walks
Gemba walks are pivotal in identifying and resolving problems efficiently.
During a Gemba walk, managers and supervisors go to the production floor or the location where the work happens.
They observe processes firsthand, talk to employees, and identify any potential inefficiencies or issues.
This not only helps in gathering accurate information but also empowers workers by involving them in the problem-solving process.
Employees can offer valuable insights based on their day-to-day experiences, which are crucial for effective solutions.
The A3 Problem Solving Tool
Another vital aspect of the Toyota method’s problem-solving strategy is the use of the A3 problem-solving tool.
An A3 document is a one-page report used for storyboarding the entire problem-solving process.
It includes an explanation of the problem, an analysis of the root cause, proposed solutions, and an action plan.
This tool ensures clarity and comprehensiveness by distilling complex issues into a simple format.
It also facilitates communication among team members and stakeholders, making it easier to coordinate efforts and track progress.
Quality Assurance in the Toyota Method
Quality assurance is a fundamental component of the Toyota method, with its techniques setting high standards in the industry.
The approach emphasizes zero defects and strives for excellence at every stage of the production process.
Jidoka: Automation with a Human Touch
One of the key concepts in ensuring quality is Jidoka, which translates to “automation with a human touch.”
This means that machines are equipped to stop automatically when a defect is detected, thus preventing faulty products from advancing further along the production line.
It empowers workers to address issues immediately, reducing waste and improving efficiency.
The idea is to automate repetitive processes but retain human oversight to ensure quality control remains a priority.
The Role of Standardized Work
Standardized work is another critical element of the Toyota method’s quality assurance system.
It refers to establishing consistent and repeatable processes to maintain high-quality output.
By defining clear standards for each task, Toyota ensures that every step in the production process is conducted uniformly, minimizing variation and errors.
Standardization not only ensures quality but also facilitates continuous improvement, as it provides a benchmark against which changes can be evaluated.
This approach makes it easier to identify areas for enhancement and measure the impact of those improvements.
The Benefits of Implementing the Toyota Method
Implementing the Toyota method can lead to significant benefits for any organization.
The method’s emphasis on on-site problem solving and quality assurance helps companies achieve higher efficiency, reduced waste, and improved product quality.
Moreover, its focus on employee involvement and continuous improvement fosters a culture of teamwork and innovation.
This not only enhances job satisfaction but also contributes to the company’s overall competitiveness.
Conclusion
The Toyota method’s points on on-site problem solving and quality assurance are powerful tools for any company aiming to enhance its operations.
By implementing practices like Gemba walks, A3 problem solving, Jidoka, and standardized work, organizations can effectively address issues, ensure quality, and continuously improve processes.
The benefits of adopting these strategies are substantial, leading to a more efficient, innovative, and competitive business.
As companies across the globe continue to integrate the principles of the Toyota method, they join a legacy of operational excellence that has defined one of the most successful companies in the world.
資料ダウンロード
QCD調達購買管理クラウド「newji」は、調達購買部門で必要なQCD管理全てを備えた、現場特化型兼クラウド型の今世紀最高の購買管理システムとなります。
ユーザー登録
調達購買業務の効率化だけでなく、システムを導入することで、コスト削減や製品・資材のステータス可視化のほか、属人化していた購買情報の共有化による内部不正防止や統制にも役立ちます。
NEWJI DX
製造業に特化したデジタルトランスフォーメーション(DX)の実現を目指す請負開発型のコンサルティングサービスです。AI、iPaaS、および先端の技術を駆使して、製造プロセスの効率化、業務効率化、チームワーク強化、コスト削減、品質向上を実現します。このサービスは、製造業の課題を深く理解し、それに対する最適なデジタルソリューションを提供することで、企業が持続的な成長とイノベーションを達成できるようサポートします。
オンライン講座
製造業、主に購買・調達部門にお勤めの方々に向けた情報を配信しております。
新任の方やベテランの方、管理職を対象とした幅広いコンテンツをご用意しております。
お問い合わせ
コストダウンが利益に直結する術だと理解していても、なかなか前に進めることができない状況。そんな時は、newjiのコストダウン自動化機能で大きく利益貢献しよう!
(Β版非公開)