- お役立ち記事
- Points of on-site problem solving and quality assurance in the Toyota method
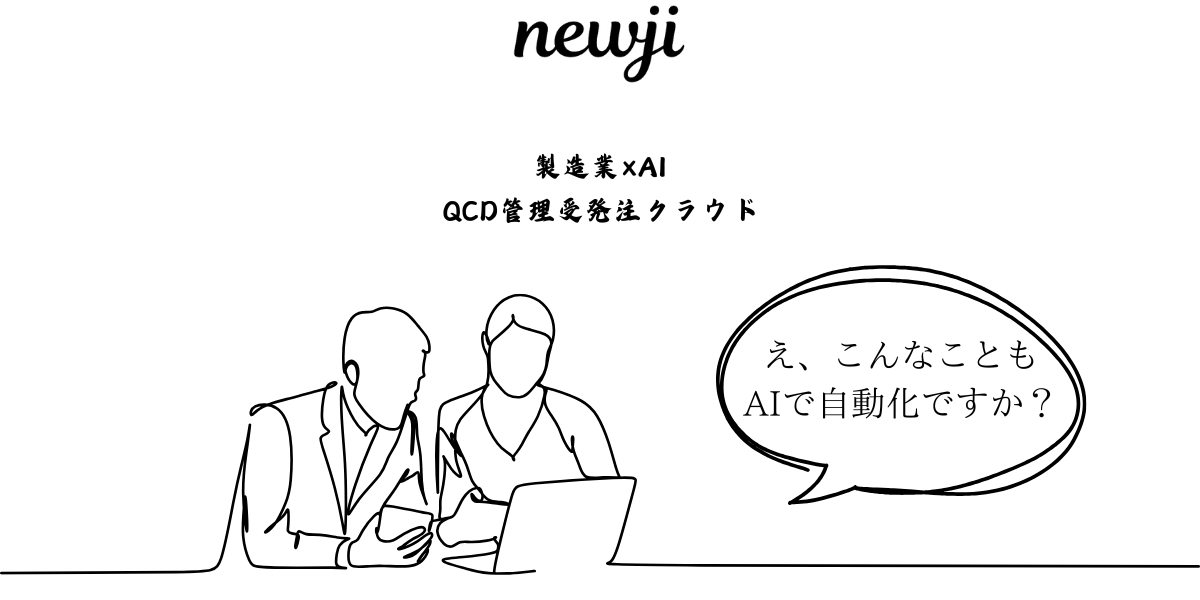
Points of on-site problem solving and quality assurance in the Toyota method
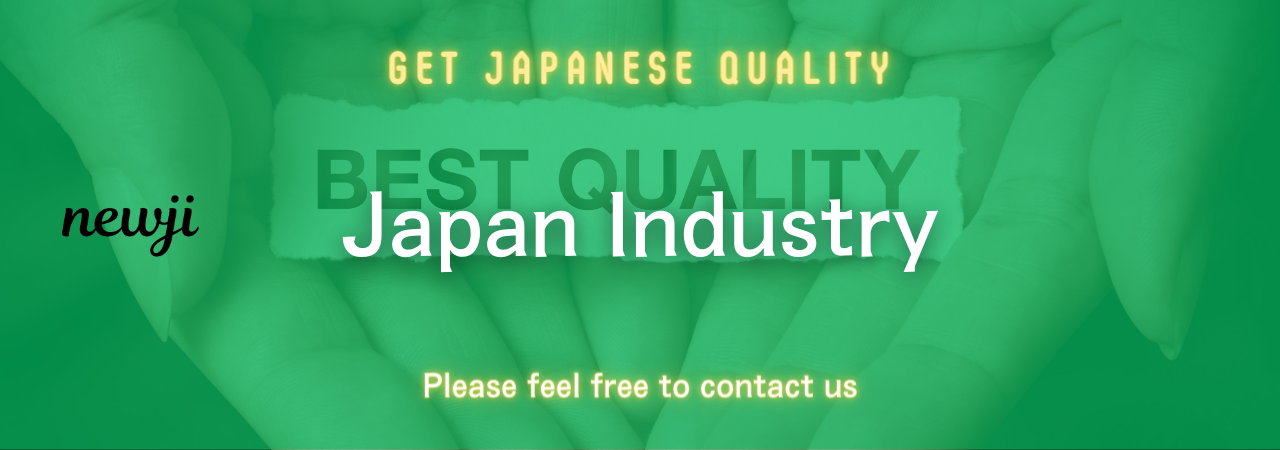
目次
Understanding the Toyota Method
The Toyota method is a renowned approach in the manufacturing world, especially when it comes to problem-solving and quality assurance.
Developed by Toyota Motor Corporation, this method has been pivotal in establishing efficient processes and maintaining exceptional quality in its products.
But what makes it so effective?
Let’s explore the core principles and practices that underline the Toyota method and how these can be applied to on-site problem-solving and quality assurance.
The Pillars of the Toyota Production System
Central to the Toyota method is the Toyota Production System (TPS), which aims to enhance both productivity and quality.
The key pillars of TPS include “Just-in-Time,” maintaining inventory levels only as needed, and “Jidoka,” which ensures automatic detection of problems with immediate stopping in case of anomalies.
These principles facilitate a smooth flow of the production process while empowering workers to stop production to correct errors immediately.
This results in fewer defects and improved efficiency.
Embracing Kaizen for Continuous Improvement
Kaizen, meaning “continuous improvement,” is a fundamental concept in the Toyota method.
It advocates incremental changes, encouraging every employee, from the factory floor to management, to suggest improvements.
Through Kaizen, Toyota fosters an environment where everyone is involved in suggesting improvements and innovations.
This culture of continuous improvement not only enhances quality but also leads to cost reduction and customer satisfaction.
Problem Solving with the Toyota Method
The 5 Whys Technique
One of the most effective problem-solving tools in the Toyota method is the “5 Whys” technique.
This involves asking “Why?” multiple times until the root cause of a problem is identified.
For instance, if a machine stops working, one might ask, “Why did the machine stop?” and continue to delve deeper with subsequent questions until reaching the fundamental cause.
This systematic approach ensures that problems are not just superficially treated but are addressed at their core, preventing recurrence.
Genchi Genbutsu: Going to the Source
Genchi Genbutsu, meaning “go and see,” emphasizes the importance of direct observation of the problem site.
By visiting the workplace and seeing the problem firsthand, employees gain a deeper understanding, leading to practical solutions.
This approach prevents assumptions and ensures that solutions are grounded in reality, contributing significantly to solving problems effectively and efficiently.
Ensuring Quality with the Toyota Method
The Role of Quality Circles
Quality circles are small groups of employees who regularly meet to discuss and solve work-related problems.
In the Toyota method, these circles play a crucial role in establishing and maintaining high quality standards.
Employees from various levels work collaboratively, utilizing their unique perspectives and experiences to address issues affecting quality.
This collective effort leads to innovative solutions and improvements, enhancing overall quality assurance.
Standardized Work: Maintaining Consistency
Standardized work is another essential element of the Toyota method, which ensures consistency and efficiency in production.
By documenting best practices, it provides a clear, detailed guide for carrying out tasks.
This reduces variability, ensures quality, and identifies areas for improvement.
When deviations occur, they are quickly noticed and addressed, maintaining production standards and enhancing overall quality assurance.
Implementing the Toyota Method in Your Organization
Cultivating a Culture of Play
To successfully implement the Toyota method, cultivating a culture of involvement and engagement is crucial.
Encourage employees at all levels to participate in problem-solving and quality assurance activities.
Provide the tools and training necessary for them to contribute meaningfully.
Create an environment where suggestions for improvement are welcomed and acted upon.
Over time, this approach will lead to a more dynamic, efficient, and quality-driven workplace.
Adapting the Principles to Your Needs
While the Toyota method is highly effective, it’s important to adapt its principles to fit your organization’s specific needs and context.
Assess your current processes and identify areas where these principles can be incorporated or modified for better results.
Customization is key to ensuring that the method works effectively in your unique business environment.
Keep evaluating and adjusting the approach as needed, ensuring continuous improvement.
Conclusion: Harnessing the Power of the Toyota Method
The Toyota method offers valuable insights and proven strategies for on-site problem solving and quality assurance.
From the 5 Whys technique to the concept of Genchi Genbutsu, each aspect is designed to enhance efficiency and quality systematically.
By implementing these principles and fostering a collaborative culture, organizations can achieve lasting improvements in their processes and products.
The key lies in embracing continuous improvement and customizing the approach to meet specific organizational needs.
In harnessing the power of the Toyota method, your organization can not only optimize operations but also maintain an edge in today’s competitive marketplace.
資料ダウンロード
QCD調達購買管理クラウド「newji」は、調達購買部門で必要なQCD管理全てを備えた、現場特化型兼クラウド型の今世紀最高の購買管理システムとなります。
ユーザー登録
調達購買業務の効率化だけでなく、システムを導入することで、コスト削減や製品・資材のステータス可視化のほか、属人化していた購買情報の共有化による内部不正防止や統制にも役立ちます。
NEWJI DX
製造業に特化したデジタルトランスフォーメーション(DX)の実現を目指す請負開発型のコンサルティングサービスです。AI、iPaaS、および先端の技術を駆使して、製造プロセスの効率化、業務効率化、チームワーク強化、コスト削減、品質向上を実現します。このサービスは、製造業の課題を深く理解し、それに対する最適なデジタルソリューションを提供することで、企業が持続的な成長とイノベーションを達成できるようサポートします。
オンライン講座
製造業、主に購買・調達部門にお勤めの方々に向けた情報を配信しております。
新任の方やベテランの方、管理職を対象とした幅広いコンテンツをご用意しております。
お問い合わせ
コストダウンが利益に直結する術だと理解していても、なかなか前に進めることができない状況。そんな時は、newjiのコストダウン自動化機能で大きく利益貢献しよう!
(Β版非公開)