- お役立ち記事
- Points that the purchasing department should keep in mind when checking the quality of imported products
Points that the purchasing department should keep in mind when checking the quality of imported products
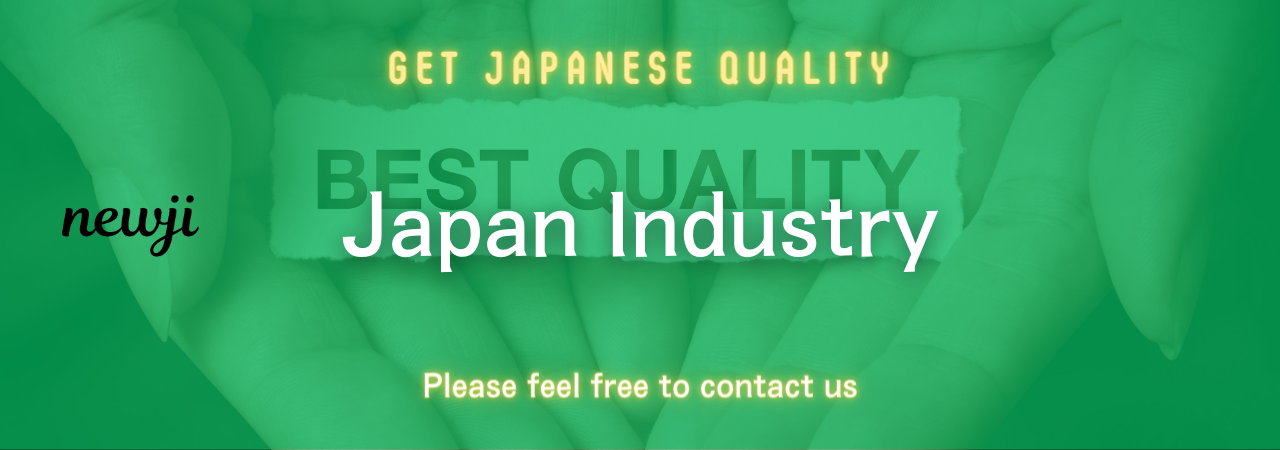
目次
Introduction to Quality Checking for Imported Products
When it comes to importing products, ensuring quality is crucial for sustaining customer satisfaction and maintaining brand reputation.
The purchasing department plays a vital role in this process, as they are on the frontline of guaranteeing that imported goods meet predetermined quality standards.
Attention to detail and a comprehensive understanding of quality assurance processes are essential for the purchasing department to execute their responsibilities effectively.
In this article, we will discuss the important points that the purchasing department should keep in mind when checking the quality of imported products.
Understanding Quality Standards
International Quality Standards
Before diving into the specifics of quality checking, it is important to acknowledge the international quality standards relevant to the products being imported.
Countries around the world have established different quality standards, such as ISO (International Organization for Standardization), which serve as benchmarks for determining the acceptable quality of various products.
The purchasing department should be well-versed in these standards to ensure compliance and avoid potential legal and financial consequences.
Product-Specific Regulations
Different products are subject to specific regulations and standards depending on their category and intended use.
For instance, electronic devices might need to adhere to safety standards that differ from those applicable to food products.
Knowing these regulations is crucial for the purchasing department to ensure that imported products meet safety and performance criteria.
Key Steps in Quality Checking
Supplier Evaluation
One of the first steps in ensuring the quality of imported products is conducting a thorough evaluation of suppliers.
The purchasing department should assess factors such as the supplier’s track record, certifications, and reputation in the industry.
An effective supplier evaluation process will help in establishing a trustworthy partnership, reducing the risk of receiving products that fail to meet quality standards.
Sampling and Testing
Sampling and testing are integral components of the quality checking process.
The purchasing department should implement a systematic approach to select samples from shipments and conduct tests to evaluate quality.
Testing methods may vary based on the product type and can include visual inspections, chemical analyses, and performance assessments.
Reliable sampling and testing help in identifying quality issues early and prevent large-scale quality failures.
Documentation and Record Keeping
Proper documentation and record keeping are critical when it comes to quality checking imported products.
Ensuring that all test results, quality reports, and compliance certificates are well-documented supports transparency and accountability.
It also allows for efficient communication between the purchasing department and suppliers, as well as aids in making informed decisions in the event of disputes or quality issues.
Handling Quality Issues
Non-Conformance Management
Despite preventive measures, there may be instances when imported products do not meet the expected quality standards.
Non-conformance management involves identifying and addressing such quality issues effectively.
The purchasing department should have a clear protocol for managing non-conformances, which includes documenting the issue, communicating with the supplier, and implementing corrective actions.
Continuous Improvement
Quality checking isn’t just about identifying defects; it’s also about continually improving processes.
The purchasing department should actively seek feedback from customers and integrate these insights into their quality assurance strategies.
They should collaborate with suppliers to identify areas for improvement and work toward enhancing overall product quality.
Building Strong Supplier Relationships
Communication and Collaboration
Effective communication with suppliers is essential for ensuring product quality.
The purchasing department should foster open lines of communication to discuss quality expectations and address any concerns promptly.
Collaborative efforts with suppliers can result in mutual benefits, such as reduced errors, improved quality, and enhanced efficiency.
Supplier Development Programs
Investing in supplier development programs can significantly contribute to maintaining product quality.
The purchasing department may consider conducting training sessions and workshops for suppliers to align them with the organization’s quality standards and expectations.
Such initiatives not only improve quality but also build stronger partnerships with suppliers.
Embracing Technological Solutions
Quality Management Systems
Adopting a robust quality management system (QMS) can streamline the entire process of quality checking.
These systems provide tools for tracking product quality, managing documentation, and facilitating compliance with standards.
A QMS can help the purchasing department identify quality trends, automate testing procedures, and enhance overall efficiency.
Data Analytics in Quality Assurance
Data analytics can play a significant role in enhancing quality assurance processes.
By analyzing historical data related to quality issues, the purchasing department can identify patterns and anticipate potential quality risks.
Insights derived from data analytics can guide decision-making and improve supplier selection, product testing, and process enhancements.
Conclusion
Checking the quality of imported products is a multi-faceted process that requires the purchasing department’s active involvement and attention to detail.
By understanding international quality standards, evaluating suppliers, implementing effective sampling and testing, and managing quality issues efficiently, the purchasing department can ensure that imported products meet the organization’s quality expectations.
With a commitment to continuous improvement and collaboration with suppliers, purchasing departments can enhance product quality, safeguard customer satisfaction, and uphold their company’s reputation in the global market.
資料ダウンロード
QCD調達購買管理クラウド「newji」は、調達購買部門で必要なQCD管理全てを備えた、現場特化型兼クラウド型の今世紀最高の購買管理システムとなります。
ユーザー登録
調達購買業務の効率化だけでなく、システムを導入することで、コスト削減や製品・資材のステータス可視化のほか、属人化していた購買情報の共有化による内部不正防止や統制にも役立ちます。
NEWJI DX
製造業に特化したデジタルトランスフォーメーション(DX)の実現を目指す請負開発型のコンサルティングサービスです。AI、iPaaS、および先端の技術を駆使して、製造プロセスの効率化、業務効率化、チームワーク強化、コスト削減、品質向上を実現します。このサービスは、製造業の課題を深く理解し、それに対する最適なデジタルソリューションを提供することで、企業が持続的な成長とイノベーションを達成できるようサポートします。
オンライン講座
製造業、主に購買・調達部門にお勤めの方々に向けた情報を配信しております。
新任の方やベテランの方、管理職を対象とした幅広いコンテンツをご用意しております。
お問い合わせ
コストダウンが利益に直結する術だと理解していても、なかなか前に進めることができない状況。そんな時は、newjiのコストダウン自動化機能で大きく利益貢献しよう!
(Β版非公開)