- お役立ち記事
- Points to comprehensively promote Q/C/D management
月間77,185名の
製造業ご担当者様が閲覧しています*
*2025年2月28日現在のGoogle Analyticsのデータより
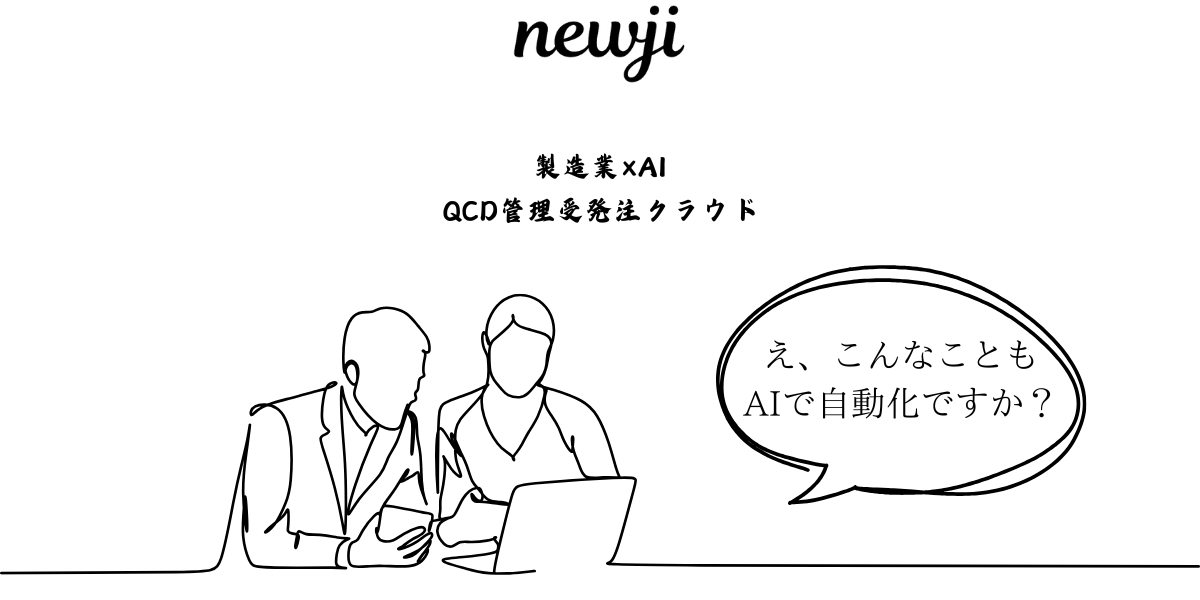
Points to comprehensively promote Q/C/D management
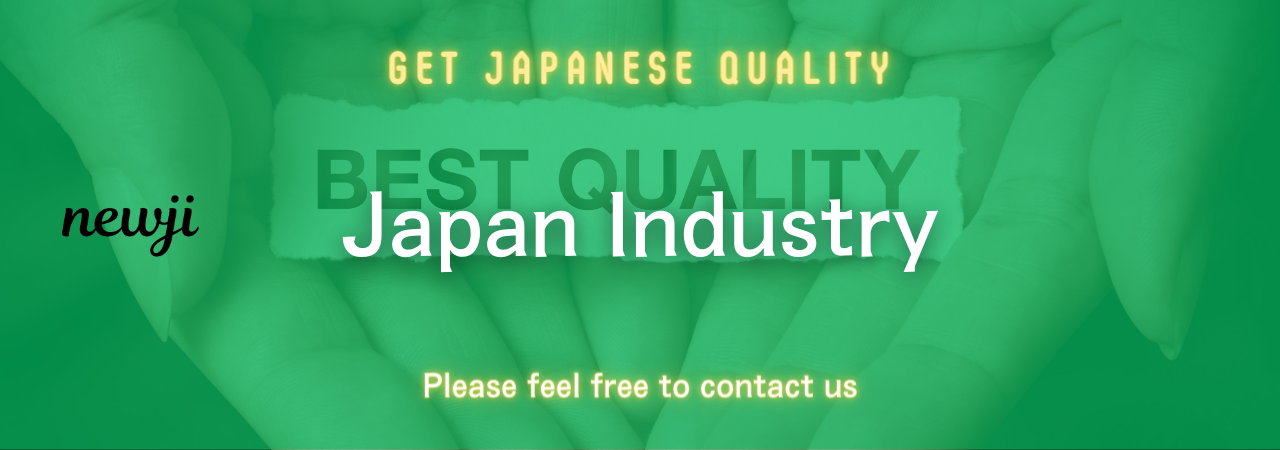
Understanding Q/C/D Management
Q/C/D management is an acronym that stands for Quality, Cost, and Delivery management.
These are three crucial pillars in any production or service process.
Keeping a keen eye on these areas ensures that businesses can provide their customers with high-quality products and services, at competitive costs, and within a timely manner.
Effectively promoting Q/C/D management can lead to increased customer satisfaction, improved efficiency, and better market positioning.
Quality: The Bedrock of Q/C/D Management
Quality is at the heart of any good manufacturing or service process.
It refers to the degree of excellence in goods or services, meeting customer expectations and regulatory requirements.
Without a consistent focus on quality, businesses run the risk of losing customer trust, which can lead to reduced sales and diminished brand reputation.
Promoting quality starts with understanding customer needs and expectations.
Regularly soliciting feedback can provide valuable insights into areas of improvement.
Quality control processes, such as regular inspections and testing, can help identify defects or areas where quality may be slipping.
This proactive approach allows for quick corrections and adjustments, preventing minor defects from becoming significant issues.
Implementing a robust quality management system (QMS) can support these efforts.
QMS provides a framework for standardizing processes and continually improving quality.
Total Quality Management (TQM) and Six Sigma are popular methodologies used to enhance quality by reducing defects and variations in production processes.
Cost Management: Balancing Quality and Profitability
Cost management involves controlling expenses to maintain profitability without compromising on quality.
In the competitive market landscape, maintaining a balance between cost and quality is critical.
Cost management requires a detailed analysis of all expenses and finding areas where efficiencies can be achieved.
This may include negotiating better rates with suppliers, reducing waste, or streamlining processes to cut unnecessary expenditures.
One approach to managing costs effectively is through Lean Management, which emphasizes reducing waste and improving efficiencies.
Lean processes aim to produce more with less—less time, less space, and fewer resources—without compromising quality.
Monitoring key performance indicators (KPIs) related to costs can help identify trends and areas for potential savings.
Adopting technology solutions like automated systems and data analytics can also lead to significant cost reductions by minimizing errors and optimizing resource allocation.
Delivery: Ensuring Timely Fulfillment
Delivery in Q/C/D management refers to the timely provision of goods and services to meet customer demands.
Effective delivery management ensures that products arrive as expected, which is crucial in maintaining customer satisfaction and loyalty.
Late deliveries can disrupt customer operations and lead to a loss of trust and potential sales.
Optimizing delivery involves several strategic activities, including supply chain management, inventory control, and demand planning.
A well-structured supply chain can enhance delivery efficiency, ensuring materials and products move smoothly from supplier to customer.
Technology plays a pivotal role in optimizing delivery processes.
Tools such as enterprise resource planning (ERP) systems and logistics software can streamline operations, improve communication between departments, and enhance tracking capabilities.
Demand planning is another critical component of effective delivery management.
By accurately forecasting customer needs, businesses can adjust their production and inventory levels to align with demand, minimizing overstock or stockouts.
Integrating Q/C/D Management for Comprehensive Success
While each component of Q/C/D management is vital on its own, integrating all three effectively results in comprehensive success for an organization.
Each pillar supports the others, resulting in a harmonious balance that benefits both the business and its customers.
For instance, maintaining high quality often supports higher customer satisfaction, which can justify premium pricing, balancing cost concerns.
Similarly, efficient cost management aids in allocating resources to enhance quality and speed up delivery processes.
Interdepartmental collaboration is essential for integrating Q/C/D management elements effectively.
Teams must communicate challenges and success to eliminate silos, allowing for a continuous flow of information throughout the organization.
A holistic approach to training and development ensures that employees across all levels understand the importance of Q/C/D management and possess the necessary skills to contribute to its success.
Regular performance reviews and audits provide feedback on areas that need improvement and celebrate successes, fostering a culture of continuous improvement.
Conclusion: The Path to Excellence
Promoting Q/C/D management comprehensively is a pathway to excellence for any organization.
Quality, cost, and delivery are interlinked, and addressing them together leads to maximizing business potential and satisfying customer demands.
Achieving a balance between these three components leads to a strong market position and resilience in a competitive and ever-changing business landscape.
Implementing these practices may require time and effort, but the results will ultimately be rewarding, driving both short-term success and long-term growth.
In summary, focusing on quality ensures product or service standards meet and exceed customer expectations.
Proper cost management allows businesses to maintain profitability, while thorough delivery processes guarantee timely fulfillment.
Together, these make Q/C/D management essential for businesses aiming to achieve sustainable growth and a loyal customer base.
資料ダウンロード
QCD管理受発注クラウド「newji」は、受発注部門で必要なQCD管理全てを備えた、現場特化型兼クラウド型の今世紀最高の受発注管理システムとなります。
ユーザー登録
受発注業務の効率化だけでなく、システムを導入することで、コスト削減や製品・資材のステータス可視化のほか、属人化していた受発注情報の共有化による内部不正防止や統制にも役立ちます。
NEWJI DX
製造業に特化したデジタルトランスフォーメーション(DX)の実現を目指す請負開発型のコンサルティングサービスです。AI、iPaaS、および先端の技術を駆使して、製造プロセスの効率化、業務効率化、チームワーク強化、コスト削減、品質向上を実現します。このサービスは、製造業の課題を深く理解し、それに対する最適なデジタルソリューションを提供することで、企業が持続的な成長とイノベーションを達成できるようサポートします。
製造業ニュース解説
製造業、主に購買・調達部門にお勤めの方々に向けた情報を配信しております。
新任の方やベテランの方、管理職を対象とした幅広いコンテンツをご用意しております。
お問い合わせ
コストダウンが利益に直結する術だと理解していても、なかなか前に進めることができない状況。そんな時は、newjiのコストダウン自動化機能で大きく利益貢献しよう!
(β版非公開)