- お役立ち記事
- Points to consider when selecting supply chain risk management tools for purchasing departments
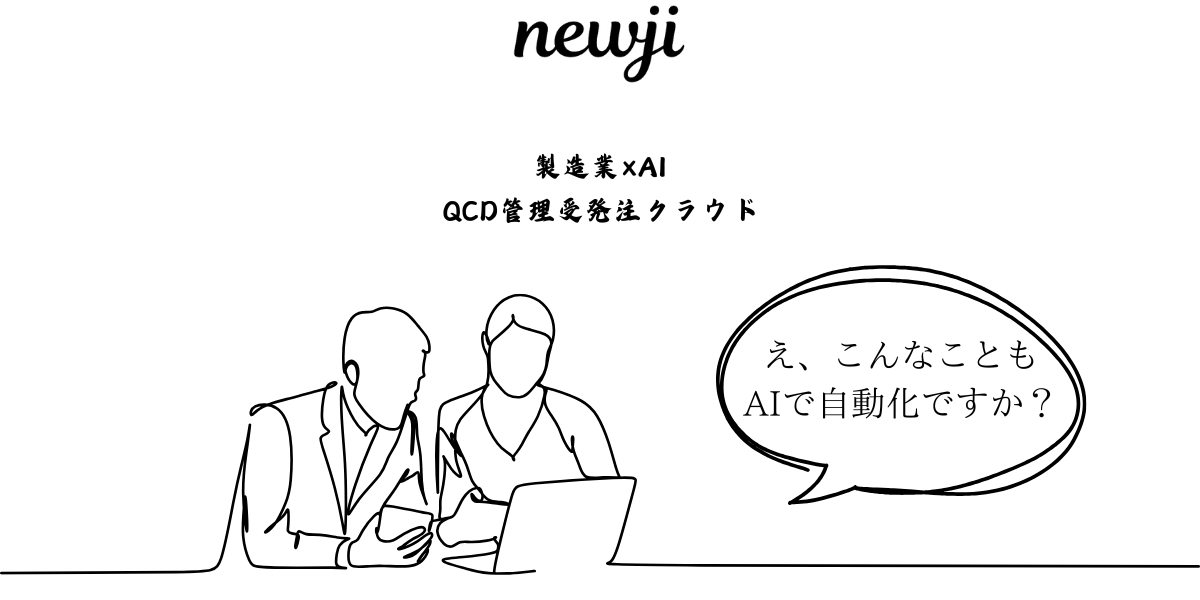
Points to consider when selecting supply chain risk management tools for purchasing departments
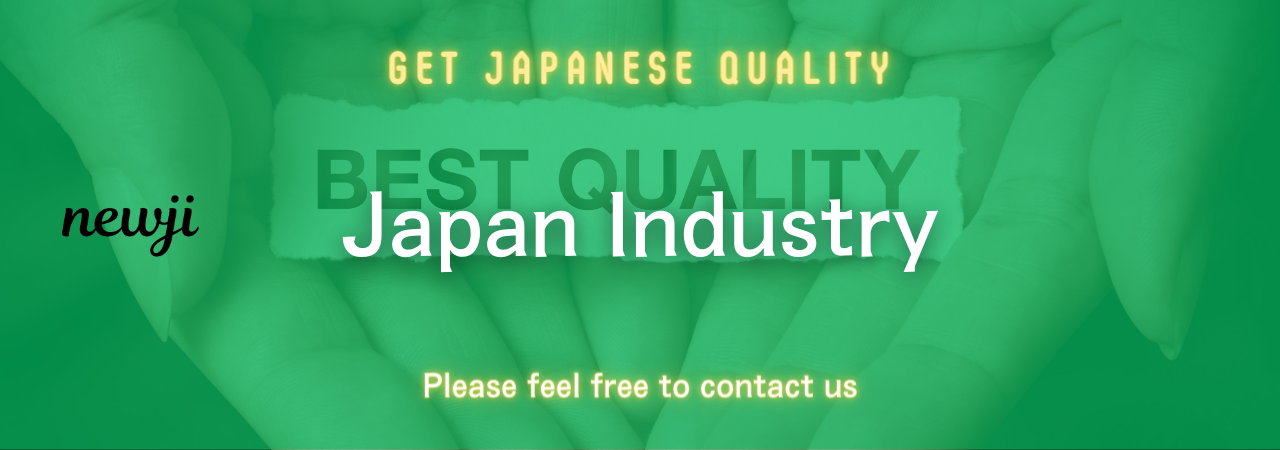
目次
Understanding Supply Chain Risk Management
In today’s globalized market, managing the risks associated with supply chains is more crucial than ever for purchasing departments.
Supply chain risk management involves identifying, assessing, and mitigating risks that can disrupt the flow of goods and services.
From natural disasters and political instability to cyber threats and supplier failures, these risks can significantly impact a company’s operations and profitability.
Hence, selecting the right tools for supply chain risk management is essential for ensuring the resilience and efficiency of purchasing departments.
Key Features to Look for in Supply Chain Risk Management Tools
When selecting supply chain risk management tools for purchasing departments, it’s important to consider several key features.
These features will help ensure that your department can effectively manage and mitigate risks within the supply chain.
Comprehensive Risk Identification
The tool should have the capability to identify a wide range of risks, from financial and operational to environmental and geopolitical.
It should provide a comprehensive view, allowing you to understand both the internal and external threats that could affect the supply chain.
Real-Time Risk Monitoring
Real-time monitoring is essential, as it enables purchasing departments to respond quickly to emerging risks.
The tool should continuously gather data from various sources, offering timely alerts and updates.
This feature helps in making informed decisions that could prevent potential disruptions.
Risk Assessment and Analysis
A good risk management tool should include robust assessment and analysis capabilities.
It should provide insights into the likelihood and impact of risks, helping you prioritize which risks to address first.
Advanced analytical tools may also use algorithms and AI to predict future risks based on historical data and trends.
Scenario Planning and Simulation
Scenario planning allows purchasing departments to prepare for various potential risk situations.
The tool should offer simulation capabilities, enabling you to test different strategies and understand how they might affect the supply chain.
This feature is crucial for developing contingency plans and ensuring your department is ready for unexpected events.
Integration Capabilities
The supply chain risk management tool should easily integrate with existing systems and databases.
Seamless integration ensures that data flows smoothly across different platforms, allowing for more comprehensive risk analysis and improved decision-making.
Considerations Specific to Purchasing Departments
While general features are essential, purchasing departments have specific needs when it comes to selecting supply chain risk management tools.
Supplier Risk Management
Purchasing departments must focus heavily on supplier-related risks.
The tool should provide detailed insights into supplier performance and financial stability.
It should also help identify potential risks related to supplier locations, such as geopolitical issues or natural disaster zones.
Cost-Effectiveness
Budget constraints are a reality for most purchasing departments.
The tool should offer a balance between cost and functionality, ensuring that it delivers the necessary features without overspending.
Consideration of total cost of ownership, including initial purchase price, implementation costs, and ongoing maintenance, is key.
User-Friendly Interface
A straightforward, easy-to-navigate interface is important for encouraging widespread use within the department.
Team members should be able to easily access and utilize the tool’s various functions without requiring extensive training or support.
Regulatory Compliance
The tool should assist in ensuring compliance with relevant industry regulations and standards.
It should provide features that help in tracking and documenting compliance efforts, thus avoiding potential legal issues.
Evaluating and Selecting the Right Tool
The process of selecting a supply chain risk management tool involves careful evaluation.
Define Your Objectives
Start by identifying the specific risks that your purchasing department faces and what objectives you hope to achieve by implementing the tool.
Defining clear goals will help in narrowing down your options and selecting a tool that meets your needs.
Research Available Options
Conduct thorough research on the various tools available in the market.
Look for reviews and case studies to understand how others in your industry are using these tools and what benefits they have achieved.
This research phase is essential to comprehending the strengths and weaknesses of each option.
Request Demos and Trials
Before making a decision, request demos and trials from providers.
Hands-on experience with the tool will give you a better understanding of its capabilities and ease of use.
Involve key stakeholders in this testing phase to gather diverse feedback.
Assess Support and Training Options
Evaluate the support and training options offered by the tool provider.
Adequate support ensures that any issues you encounter can be resolved quickly, while comprehensive training helps your team make the most of the tool’s features.
Conclusion
Selecting the right supply chain risk management tool is a critical decision for purchasing departments.
By focusing on comprehensive risk identification, real-time monitoring, and easy integration, among other features, you can ensure that your department is well-equipped to manage and mitigate supply chain risks.
Consider specific needs, such as supplier risk and cost-effectiveness, to find a tool that aligns with your department’s objectives.
With careful evaluation and selection, purchasing departments can build a resilient supply chain that sustains operations and supports the organization’s overall goals.
資料ダウンロード
QCD調達購買管理クラウド「newji」は、調達購買部門で必要なQCD管理全てを備えた、現場特化型兼クラウド型の今世紀最高の購買管理システムとなります。
ユーザー登録
調達購買業務の効率化だけでなく、システムを導入することで、コスト削減や製品・資材のステータス可視化のほか、属人化していた購買情報の共有化による内部不正防止や統制にも役立ちます。
NEWJI DX
製造業に特化したデジタルトランスフォーメーション(DX)の実現を目指す請負開発型のコンサルティングサービスです。AI、iPaaS、および先端の技術を駆使して、製造プロセスの効率化、業務効率化、チームワーク強化、コスト削減、品質向上を実現します。このサービスは、製造業の課題を深く理解し、それに対する最適なデジタルソリューションを提供することで、企業が持続的な成長とイノベーションを達成できるようサポートします。
オンライン講座
製造業、主に購買・調達部門にお勤めの方々に向けた情報を配信しております。
新任の方やベテランの方、管理職を対象とした幅広いコンテンツをご用意しております。
お問い合わせ
コストダウンが利益に直結する術だと理解していても、なかなか前に進めることができない状況。そんな時は、newjiのコストダウン自動化機能で大きく利益貢献しよう!
(Β版非公開)