- お役立ち記事
- Points to keep in mind when managing material receipts for purchasing leaders
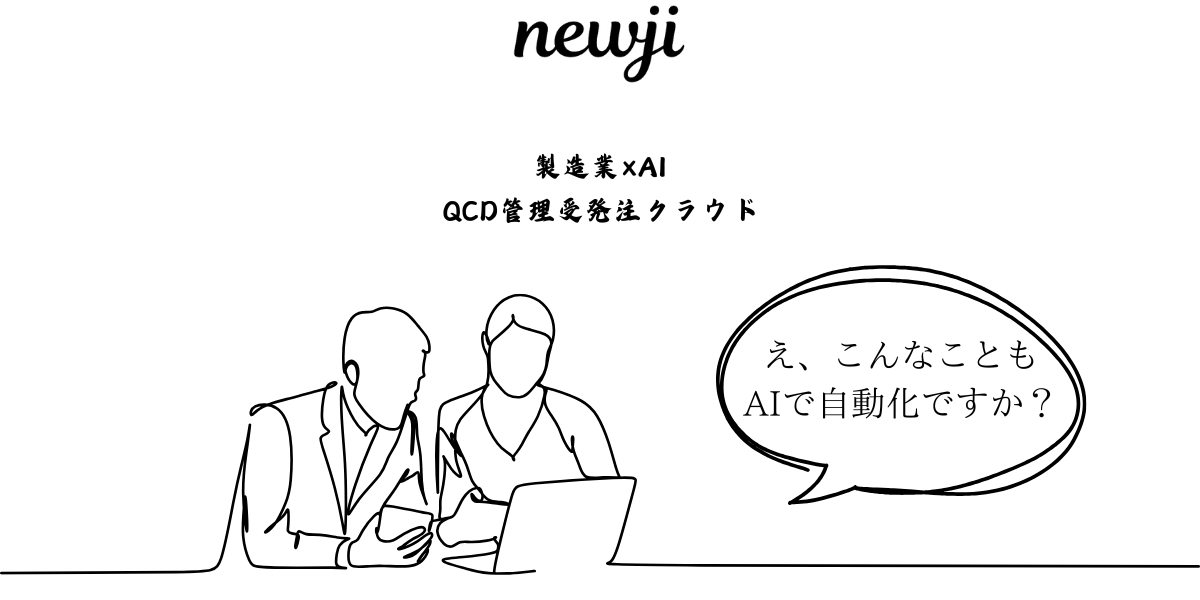
Points to keep in mind when managing material receipts for purchasing leaders
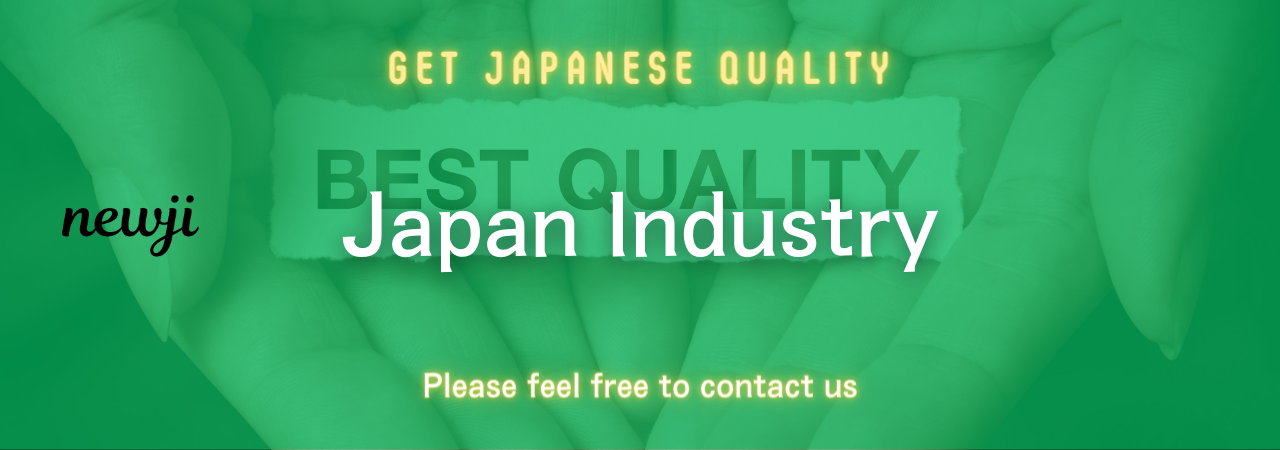
目次
Understanding Material Receipts in Purchasing
In the realm of procurement, managing material receipts effectively is crucial for purchasing leaders.
Material receipts are the documentation and process of acknowledging the receipt of goods that have been ordered.
It signifies that the goods have arrived and are in satisfactory condition.
This action plays a significant role in inventory management, financial accounting, and supply chain efficiency.
Ensuring accuracy in this process is vital as it affects inventory levels, cost management, and vendor relationships.
With accurate material receipt management, you can avoid pitfalls such as discrepancies in inventory, financial losses, and strained supplier relationships.
Importance of Timely Processing
One of the key points to keep in mind is to process material receipts promptly.
When materials arrive, it is essential to inspect and verify them immediately.
Timely processing ensures that any discrepancies or damages are addressed quickly, maintaining the integrity of the supply chain.
Delays in processing can result in stock shortages, impacting production and sales.
Rapid processing also aids in improving cash flow management.
Once materials are verified and the receipt is acknowledged, payments can be processed timely, maintaining good relationships with suppliers.
Moreover, it helps in preventing bottlenecks that may develop from a backlog of unprocessed receipts.
Verification and Documentation
Verification is a critical step in the management of material receipts.
Ensure that received materials match the purchase order in terms of quantity, quality, and specifications.
Discrepancies must be promptly recorded and communicated to the supplier to facilitate swift resolution.
Documenting this process is equally important.
Maintain accurate records of each transaction, including the purchase order, delivery note, and any communication regarding discrepancies.
This documentation serves as a vital reference for auditing and troubleshooting any issues that may arise in the future.
Utilizing Technology for Efficiency
Incorporating technology into managing material receipts can significantly enhance accuracy and efficiency.
Utilize inventory management software to automate the receipt process.
These digital tools can streamline operations by automatically updating inventory records and facilitating real-time tracking of goods.
Moreover, electronic data interchange (EDI) systems can be employed to seamlessly communicate with suppliers and reduce the reliance on manual paper-based systems.
These technologies not only reduce the chance of human error but also increase the speed at which information is processed.
Training and Empowering Staff
While technology plays a vital role, well-trained personnel are equally important in managing material receipts.
Ensure that staff involved in this process are well trained in the procedures and the use of technological tools.
Empower them with the authority to address and resolve discrepancies as they arise.
Continuous training programs should be implemented to keep the team updated on best practices and new technologies.
By empowering your team with knowledge and skills, you enhance the overall efficiency and reliability of the material receipt process.
Fostering Supplier Relationships
Effective management of material receipts is integral to maintaining strong supplier relationships.
Ensuring accurate and timely receipts can boost trust and collaboration between your organization and suppliers.
Communicate openly with suppliers regarding receipt expectations and any issues that arise.
Participate in regular reviews with your suppliers to discuss performance and explore ways to improve delivery accuracy.
Strong relationships with suppliers can lead to better negotiation terms, priority service, and critical support during supply chain disruptions.
Improving Inventory Accuracy
Proper management of material receipts directly impacts inventory accuracy.
Each receipt should be meticulously logged, ensuring that inventory levels are up-to-date and reflect the actual stock on hand.
Accurate inventory data is essential for demand planning and ensuring that orders are placed in a timely manner to prevent stockouts.
Regular audits should be conducted to ensure that receipts align with inventory levels.
Any discrepancies found during audits should be quickly investigated and addressed to maintain data integrity.
Conclusion
Managing material receipts effectively is a fundamental aspect of purchasing that requires attention to detail, efficiency, and effective communication.
By focusing on timely processing, thorough verification, utilizing technology, empowering staff, fostering supplier relationships, and maintaining inventory accuracy, purchasing leaders can ensure a smooth and reliable procurement process.
These efforts not only enhance the operational efficiency of the organization but also contribute to long-term strategic goals.
資料ダウンロード
QCD調達購買管理クラウド「newji」は、調達購買部門で必要なQCD管理全てを備えた、現場特化型兼クラウド型の今世紀最高の購買管理システムとなります。
ユーザー登録
調達購買業務の効率化だけでなく、システムを導入することで、コスト削減や製品・資材のステータス可視化のほか、属人化していた購買情報の共有化による内部不正防止や統制にも役立ちます。
NEWJI DX
製造業に特化したデジタルトランスフォーメーション(DX)の実現を目指す請負開発型のコンサルティングサービスです。AI、iPaaS、および先端の技術を駆使して、製造プロセスの効率化、業務効率化、チームワーク強化、コスト削減、品質向上を実現します。このサービスは、製造業の課題を深く理解し、それに対する最適なデジタルソリューションを提供することで、企業が持続的な成長とイノベーションを達成できるようサポートします。
オンライン講座
製造業、主に購買・調達部門にお勤めの方々に向けた情報を配信しております。
新任の方やベテランの方、管理職を対象とした幅広いコンテンツをご用意しております。
お問い合わせ
コストダウンが利益に直結する術だと理解していても、なかなか前に進めることができない状況。そんな時は、newjiのコストダウン自動化機能で大きく利益貢献しよう!
(Β版非公開)