- お役立ち記事
- Points to note when purchasing departments promote long-term contracts with suppliers
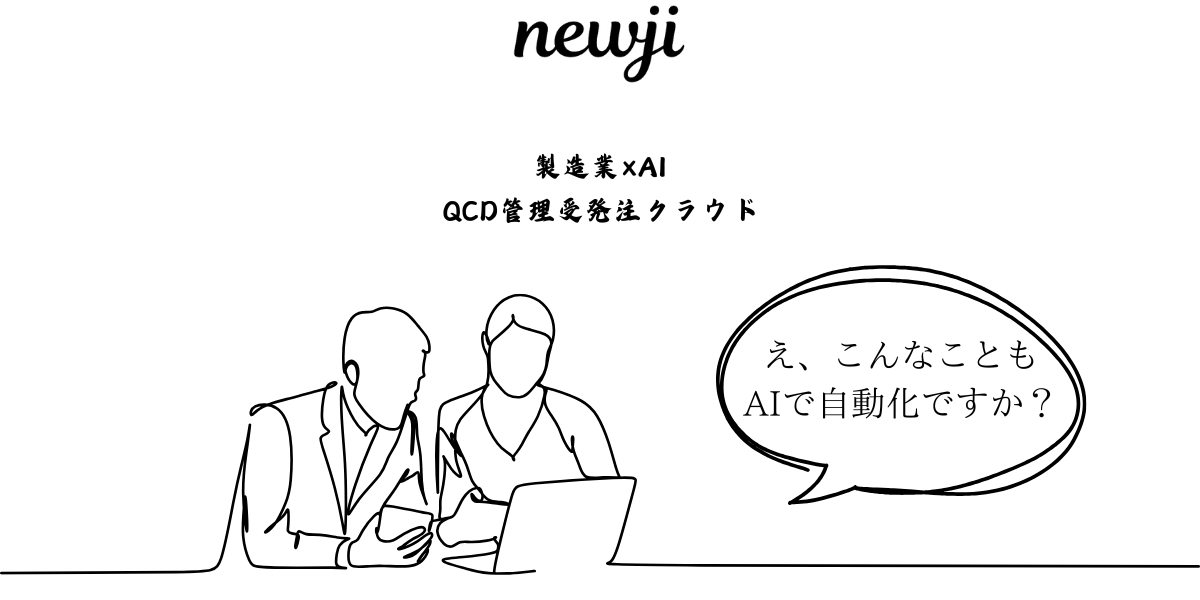
Points to note when purchasing departments promote long-term contracts with suppliers
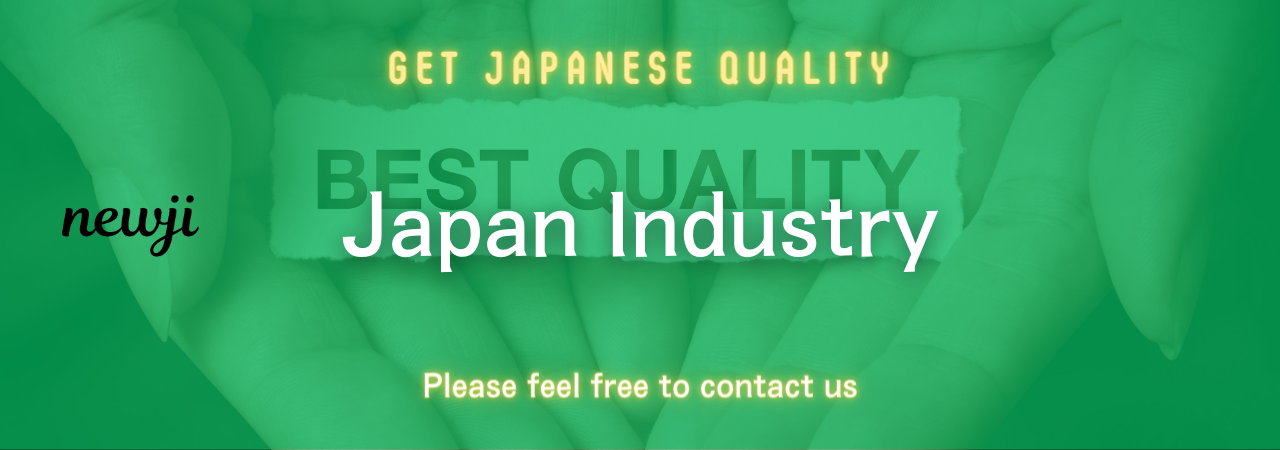
目次
Understanding Long-term Contracts
When purchasing departments consider entering long-term contracts with suppliers, it’s important to understand what these agreements entail.
A long-term contract typically spans several years and may cover a wide range of goods or services.
Such agreements provide stability and predictability for both parties.
For purchasing departments, they offer the security of knowing that supplies will be available at predetermined prices over an extended period.
However, these contracts also come with challenges.
It’s crucial to find a balance between commitment and flexibility.
This involves considering how market conditions might change over the term of the contract and how these changes might affect the agreement.
Advantages of Long-term Contracts
There are several benefits to promoting long-term agreements with suppliers.
Price Stability
One of the most significant advantages is price stability.
By locking in prices for a set period, a purchasing department can avoid the fluctuations of the market.
This stability allows for better budgeting and financial management.
Guaranteed Supply
Long-term contracts ensure a steady supply of goods.
In industries where supply chain disruptions can cause major issues, this guarantee is invaluable.
Purchasing departments can plan effectively without the constant concern of shortages.
Strong Supplier Relationships
Entering a long-term contract often fosters stronger relationships with suppliers.
These alliances encourage better communication, leading to improved service and product quality.
Suppliers are more likely to invest in technology and processes that benefit your business when they have the assurance of a long-term partnership.
Potential Drawbacks
Despite these benefits, there are potential downsides to long-term contracts that purchasing departments need to consider.
Lack of Flexibility
Committing to long-term contracts can limit a company’s flexibility to switch suppliers if better options become available.
This inflexibility might result in missed opportunities for cost savings or improved products.
Market Changes
Economic conditions, such as inflation or supply chain disruptions, can affect the terms and viability of a contract over time.
Fixed prices might not match the market rates after several years, potentially leading to financial disadvantages.
Vendor Dependency
Relying on a single supplier for long periods can create dependency issues.
If a vendor faces operational challenges or goes out of business, it can leave the purchasing department scrambling for alternatives.
Key Considerations
To mitigate the potential downsides and maximize the benefits of long-term agreements, purchasing departments should consider the following factors.
Comprehensive Market Research
Before entering a long-term contract, thorough market research is essential.
Understanding industry trends, competitor pricing, and potential technological advancements can provide insights into the contract’s long-term feasibility.
Contract Terms and Conditions
Ensure the contract includes flexible terms and conditions.
Clauses for price adjustments, technology upgrades, and quality improvements are essential to accommodate future changes.
Including exit strategies in the contract can also provide an out if unexpected circumstances arise.
Supplier Evaluation
A comprehensive supplier evaluation process should be in place.
Assess the supplier’s financial health, production capacity, and market reputation.
Ensuring that the supplier can meet long-term commitments is crucial for a successful partnership.
Regular Performance Reviews
Schedule regular reviews with the supplier to evaluate performance against the contract terms.
These reviews offer a chance to address any issues and ensure continuous alignment with business objectives.
Navigating Supplier Negotiations
Effective negotiation is critical in setting up a successful long-term contract.
Define Clear Objectives
Before entering negotiations, clearly define what your company aims to achieve with the contract.
Identify your priorities such as price, quality, delivery timelines, and additional services.
Build a Negotiation Team
Form a negotiation team that combines expertise from different departments like procurement, finance, and legal.
This team approach can help address various aspects of the contract comprehensively.
Foster Collaborative Relationships
Negotiations should not be adversarial.
Approach them as opportunities to build mutually beneficial partnerships.
Open communication and a willingness to compromise can lead to agreements that satisfy both parties.
Implementing Effective Management Strategies
Once a long-term contract is in place, effective management strategies are vital for ensuring ongoing success.
Relationship Management
Maintain strong relationships with suppliers by promoting open communication and transparency.
Regular interactions can help preempt challenges and foster a collaborative atmosphere.
Monitoring Market Conditions
Stay informed about market conditions to anticipate changes that could impact the contract.
Having contingency plans in place can help navigate unexpected events.
Internal Alignment
Ensure internal stakeholders are aligned with the contract terms and objectives.
Regular updates and communication across departments can help in aligning efforts and expectations.
Understanding and navigating the complexities of long-term contracts require careful consideration and strategic planning.
By weighing the benefits and potential drawbacks, addressing key factors, and fostering strong supplier relationships, purchasing departments can promote successful long-term contracts that drive business value.
資料ダウンロード
QCD調達購買管理クラウド「newji」は、調達購買部門で必要なQCD管理全てを備えた、現場特化型兼クラウド型の今世紀最高の購買管理システムとなります。
ユーザー登録
調達購買業務の効率化だけでなく、システムを導入することで、コスト削減や製品・資材のステータス可視化のほか、属人化していた購買情報の共有化による内部不正防止や統制にも役立ちます。
NEWJI DX
製造業に特化したデジタルトランスフォーメーション(DX)の実現を目指す請負開発型のコンサルティングサービスです。AI、iPaaS、および先端の技術を駆使して、製造プロセスの効率化、業務効率化、チームワーク強化、コスト削減、品質向上を実現します。このサービスは、製造業の課題を深く理解し、それに対する最適なデジタルソリューションを提供することで、企業が持続的な成長とイノベーションを達成できるようサポートします。
オンライン講座
製造業、主に購買・調達部門にお勤めの方々に向けた情報を配信しております。
新任の方やベテランの方、管理職を対象とした幅広いコンテンツをご用意しております。
お問い合わせ
コストダウンが利益に直結する術だと理解していても、なかなか前に進めることができない状況。そんな時は、newjiのコストダウン自動化機能で大きく利益貢献しよう!
(Β版非公開)