- お役立ち記事
- Polypropylene Processing Techniques Update for SMEs
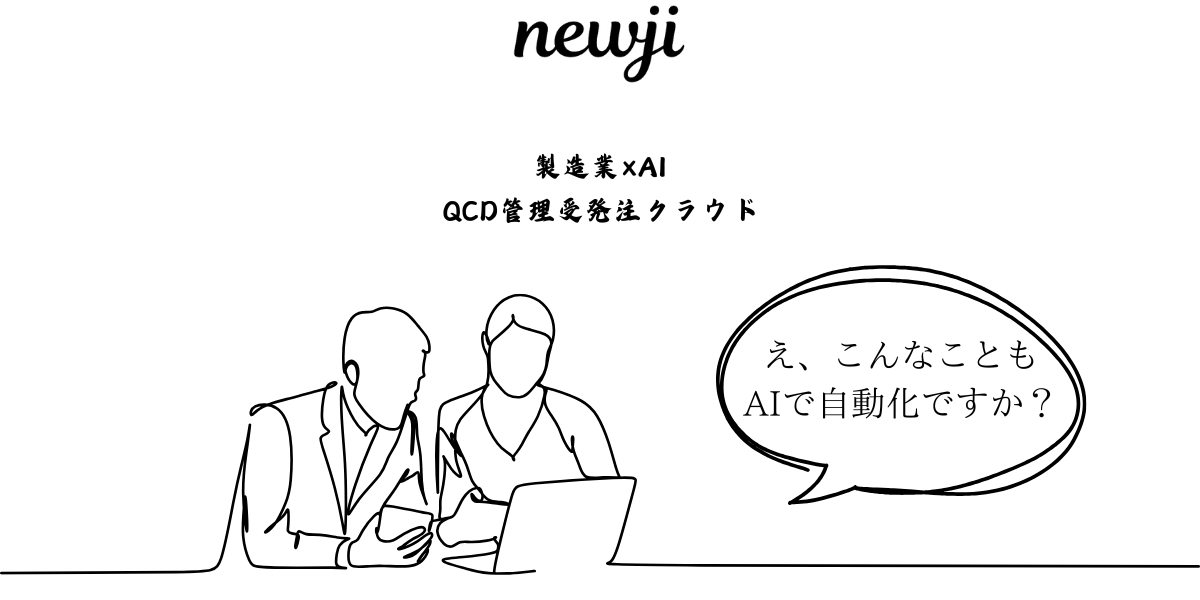
Polypropylene Processing Techniques Update for SMEs
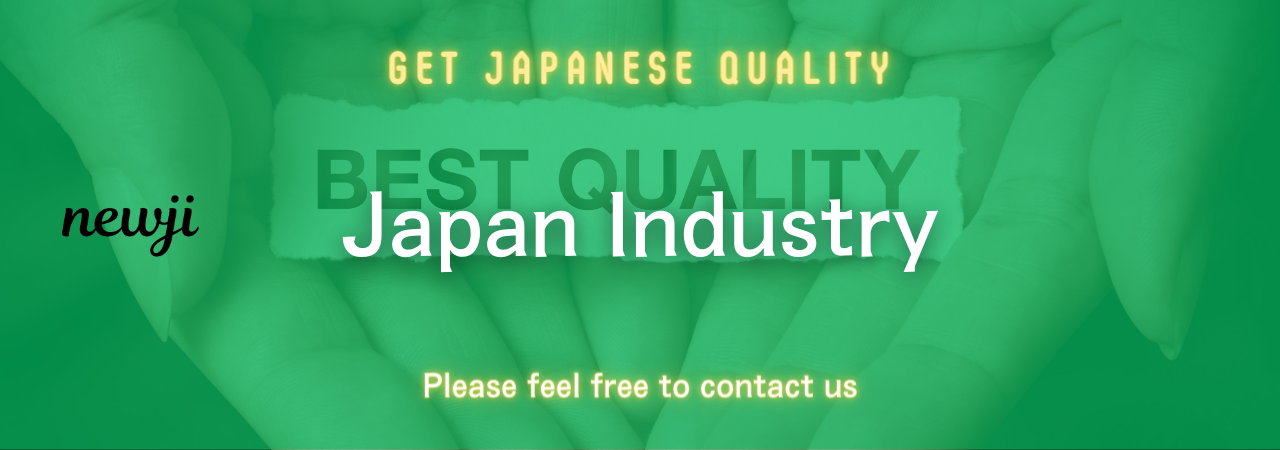
目次
Understanding Polypropylene
Polypropylene is a versatile thermoplastic polymer widely used in various industries due to its unique properties.
It is a type of plastic known for being lightweight, durable, and resistant to various chemical solvents, acids, and bases.
This makes it ideal for a wide range of applications, from automotive parts to food containers.
For small and medium-sized enterprises (SMEs) looking to utilize polypropylene, it is essential to understand its processing techniques to optimize production and ensure high-quality results.
Injection Molding
One of the most common methods for processing polypropylene is injection molding.
In this process, the polypropylene is heated until it becomes molten, then injected into a mold under high pressure.
As the material cools, it hardens into the shape of the mold.
This technique is favored for its ability to produce complex shapes with high precision and consistency.
It’s also highly efficient for mass production runs, making it an excellent choice for SMEs aiming to scale up quickly.
Benefits of Injection Molding
– **Efficiency**: High-speed production capabilities make it cost-effective for producing large quantities.
– **Precision**: Capable of creating detailed and intricate parts with minimal error.
– **Material Utilization**: Minimizes waste as excess material can often be recycled and reused.
Extrusion Molding
Extrusion molding is another prevalent technique used in polypropylene processing.
This method involves forcing molten polypropylene through a die to create continuous shapes, such as sheets, tubes, or films.
Once extruded, the material cools and takes on a solid form.
Extrusion is particularly well-suited for products that require uniform cross-sections and long lengths.
Advantages of Extrusion Molding
– **Consistency**: Produces uniform products with excellent consistency in shape and size.
– **Versatility**: Can produce a wide range of products with different profiles.
– **Customization**: Allows for easy changes in color, texture, and size.
Blow Molding
Blow molding is a technique primarily used for creating hollow objects like bottles and containers.
The process involves blowing air into heated plastic to form it against the contours of a mold.
Polypropylene’s lightweight and durable nature makes it an ideal candidate for blow molding in the production of containers that are both robust and light.
Why Choose Blow Molding?
– **Efficiency**: Ideal for producing a large volume of hollow items quickly.
– **Cost-Effective**: Lower tooling costs compared to other molding techniques.
– **Versatility**: Suitable for a variety of shapes and sizes.
Thermoforming
Thermoforming is a process where a sheet of polypropylene is heated until pliable and then formed over a mold.
Once cooled, it hardens into the desired shape, making it perfect for creating large surface area parts such as panels or lids.
This technique is often used for packaging applications, where thin-walled, flexible, yet durable parts are required.
Key Benefits of Thermoforming
– **Cost Efficiency**: Lower costs due to inexpensive tooling and fast production cycles.
– **Flexibility**: Easily accommodates design changes and accommodates complex shapes.
– **Material Savings**: Reduces waste by utilizing thin sheets of polypropylene.
Challenges in Polypropylene Processing
While there are several benefits to using polypropylene, there are also some challenges associated with its processing.
One major challenge is its high thermal expansion, which can lead to warping and dimensional instability.
Another issue is the material’s sensitivity to UV light, which can cause degradation over time.
To mitigate these challenges, SMEs can consider additives that enhance UV resistance or employ post-processing techniques such as annealing to stabilize dimensions.
Innovations in Polypropylene Processing
The landscape of polypropylene processing is constantly evolving with new technologies and techniques emerging.
For instance, computer-aided design (CAD) and simulation tools are significantly improving the accuracy and efficiency of mold design and development.
Additionally, advancements in automation are streamlining production processes, reducing costs and increasing throughput.
SMEs can leverage these innovations to remain competitive, enhance product quality, and reduce production costs.
Conclusion
Polypropylene processing offers a multitude of techniques and benefits for small and medium-sized enterprises.
Understanding and employing the right processing methods can greatly enhance product quality and manufacturing efficiency.
By staying informed about the latest advancements and challenges in polypropylene processing, SMEs can position themselves for success in the competitive market.
Whether it’s injection molding, blow molding, extrusion, or thermoforming, each technique has its unique advantages and challenges.
Careful consideration and application of these methods can lead to a sustainable and profitable operation.
As technology continues to evolve, SMEs will find more opportunities to innovate and improve their polypropylene processing capabilities.
資料ダウンロード
QCD調達購買管理クラウド「newji」は、調達購買部門で必要なQCD管理全てを備えた、現場特化型兼クラウド型の今世紀最高の購買管理システムとなります。
ユーザー登録
調達購買業務の効率化だけでなく、システムを導入することで、コスト削減や製品・資材のステータス可視化のほか、属人化していた購買情報の共有化による内部不正防止や統制にも役立ちます。
NEWJI DX
製造業に特化したデジタルトランスフォーメーション(DX)の実現を目指す請負開発型のコンサルティングサービスです。AI、iPaaS、および先端の技術を駆使して、製造プロセスの効率化、業務効率化、チームワーク強化、コスト削減、品質向上を実現します。このサービスは、製造業の課題を深く理解し、それに対する最適なデジタルソリューションを提供することで、企業が持続的な成長とイノベーションを達成できるようサポートします。
オンライン講座
製造業、主に購買・調達部門にお勤めの方々に向けた情報を配信しております。
新任の方やベテランの方、管理職を対象とした幅広いコンテンツをご用意しております。
お問い合わせ
コストダウンが利益に直結する術だと理解していても、なかなか前に進めることができない状況。そんな時は、newjiのコストダウン自動化機能で大きく利益貢献しよう!
(Β版非公開)