- お役立ち記事
- Polypropylene Processing Tips and Precautions for Small Manufacturers
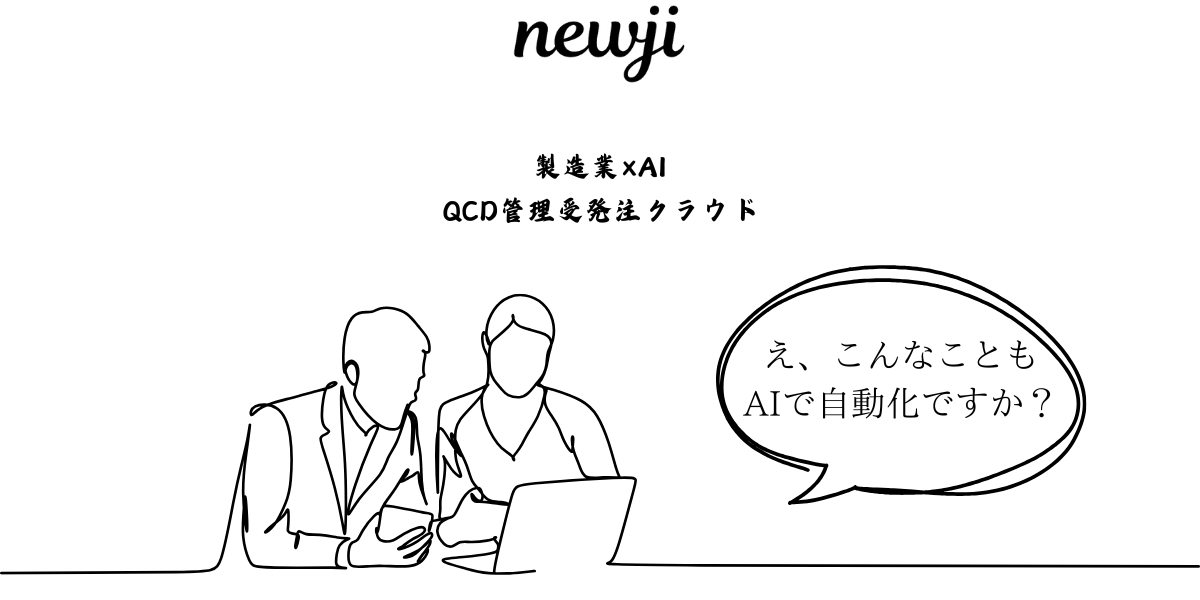
Polypropylene Processing Tips and Precautions for Small Manufacturers
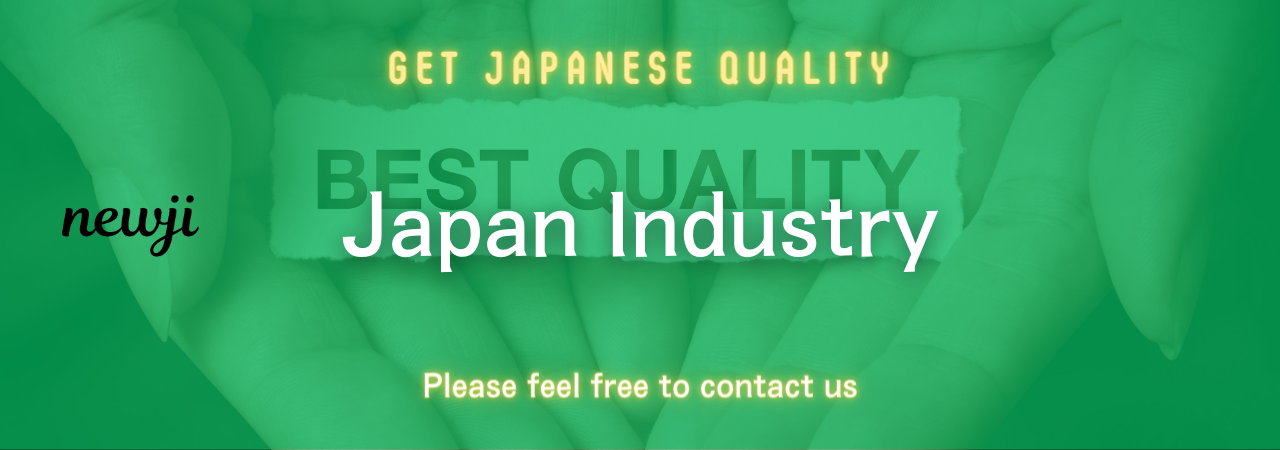
目次
Understanding Polypropylene
Polypropylene is a versatile thermoplastic polymer widely used in various industries due to its robust physical properties and affordability.
It is commonly found in packaging materials, textiles, automotive parts, and household goods.
Its resistance to heat, chemicals, and fatigue makes it a preferred choice for small manufacturers aiming to produce cost-effective and durable products.
Key Characteristics of Polypropylene
Polypropylene is known for its low density, which contributes to its lightweight nature.
This property makes it ideal for applications where weight is a critical factor, such as in automotive components or consumer goods.
Additionally, its high resistance to chemical attack ensures durability in harsh environments.
Polypropylene is also resistant to moisture absorption, further enhancing its suitability for applications like food packaging.
The material has excellent dielectric properties, making it an ideal choice for use in electrical components.
Moreover, it is fully recyclable, which aligns well with sustainable manufacturing practices.
Processing Techniques for Polypropylene
Understanding the correct processing techniques is crucial for small manufacturers to achieve optimal quality and efficiency when working with polypropylene.
There are several common methods utilized for polypropylene processing.
Injection Molding
Injection molding is a widely used process for creating polypropylene products.
In this method, melted polypropylene is injected into a mold cavity, where it cools and solidifies to form the desired shape.
For optimal results, it is important to control the temperature and pressure parameters closely.
Maintaining a consistent temperature throughout the mold ensures uniform flow and reduces the risk of defects such as warping or incomplete filling.
Extrusion
Extrusion involves heating polypropylene and pushing it through a die to produce long shapes like pipes, sheets, or films.
Careful monitoring of extrusion speed and cooling rates is essential to avoid variations in thickness and surface imperfections.
Small manufacturers should invest in high-quality dies to ensure precision and reduce the need for post-processing corrections.
Blow Molding
Blow molding is commonly used to produce hollow objects like bottles and containers.
In this process, a heated plastic parison (a tube-like piece of plastic) is inflated within a mold using compressed air.
Ensuring uniform wall thickness is key in blow molding, requiring precise control of air pressure and mold temperature.
Precautions for Processing Polypropylene
Working with polypropylene requires certain precautions to guarantee the safety, quality, and efficiency of manufacturing processes.
Temperature Management
Polypropylene has a relatively high melting point, so maintaining an appropriate temperature range during processing is crucial.
Overheating can lead to material degradation, affecting the mechanical properties and appearance of the final product.
It is vital to calibrate equipment regularly and monitor temperatures closely to prevent such issues.
Static Electricity Consideration
Polypropylene can generate static electricity during processing, which may lead to dust attraction or even equipment malfunction.
Integrating anti-static agents or grounding systems can help mitigate these effects, ensuring a smoother production process.
Environmental Concerns
When processing polypropylene, it is important to adhere to environmental regulations and sustainability practices.
Proper disposal of waste materials and emissions control measures should be part of the overall production strategy.
Exploring recycling options not only helps in reducing environmental impact but also in cutting down material costs.
Quality Control and Troubleshooting
Implementing effective quality control measures is essential to ensure that the finished polypropylene products meet the desired specifications.
Regular inspection and testing can help identify potential issues before they escalate.
Common Issues in Polypropylene Processing
One common issue is the presence of surface defects such as scratches or blemishes.
These can result from improper mold design or insufficient maintenance of equipment.
Another potential problem is warping or deformation, often caused by uneven cooling or inconsistent wall thickness.
By closely monitoring the process parameters and promptly addressing variations, manufacturers can minimize defects and achieve consistent quality.
Final Thoughts
For small manufacturers, understanding the intricacies of polypropylene processing is key to leveraging its advantages fully.
By employing proper techniques and adhering to precautions, manufacturers can produce high-quality products efficiently and sustainably.
Regular training and updates on industry best practices are also beneficial to keep up with technological advances and maintain competitive edge.
Investing in reliable equipment and fostering a culture of innovation and environmental responsibility can further enhance success in working with polypropylene.
With careful planning and execution, small manufacturers can harness the potential of this versatile material to support their growth and development.
資料ダウンロード
QCD調達購買管理クラウド「newji」は、調達購買部門で必要なQCD管理全てを備えた、現場特化型兼クラウド型の今世紀最高の購買管理システムとなります。
ユーザー登録
調達購買業務の効率化だけでなく、システムを導入することで、コスト削減や製品・資材のステータス可視化のほか、属人化していた購買情報の共有化による内部不正防止や統制にも役立ちます。
NEWJI DX
製造業に特化したデジタルトランスフォーメーション(DX)の実現を目指す請負開発型のコンサルティングサービスです。AI、iPaaS、および先端の技術を駆使して、製造プロセスの効率化、業務効率化、チームワーク強化、コスト削減、品質向上を実現します。このサービスは、製造業の課題を深く理解し、それに対する最適なデジタルソリューションを提供することで、企業が持続的な成長とイノベーションを達成できるようサポートします。
オンライン講座
製造業、主に購買・調達部門にお勤めの方々に向けた情報を配信しております。
新任の方やベテランの方、管理職を対象とした幅広いコンテンツをご用意しております。
お問い合わせ
コストダウンが利益に直結する術だと理解していても、なかなか前に進めることができない状況。そんな時は、newjiのコストダウン自動化機能で大きく利益貢献しよう!
(Β版非公開)