- お役立ち記事
- Portable Electric Can Opener Manufacturing Process and Torque Control Technology Enhancement
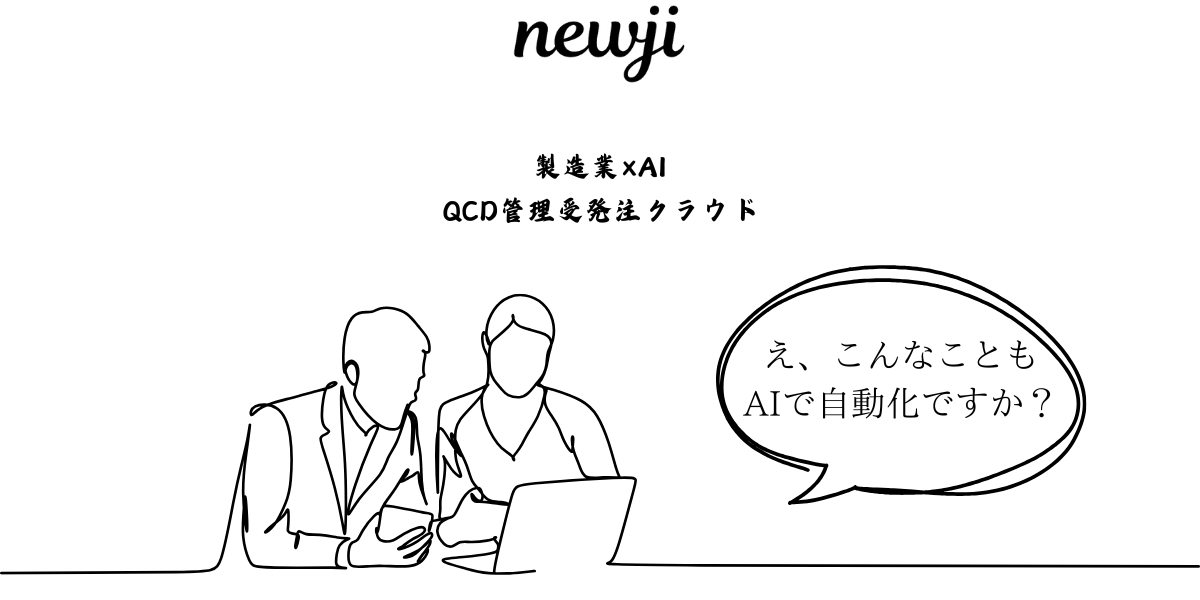
Portable Electric Can Opener Manufacturing Process and Torque Control Technology Enhancement
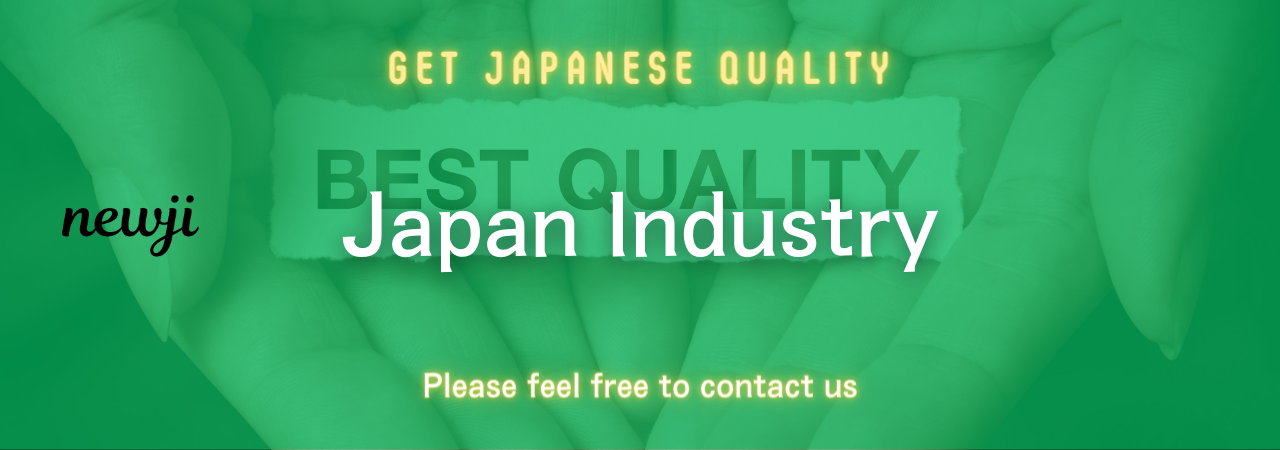
Electric can openers have become valuable tools in modern kitchens, simplifying the process of opening cans with just the press of a button.
Have you ever wondered how these handy devices are made?
Let’s dive into the manufacturing process and discover how torque control technology enhances their efficiency and reliability.
目次
Understanding the Basics: What is a Portable Electric Can Opener?
Before dissecting the manufacturing process, it’s essential to understand what a portable electric can opener is.
These devices are compact, battery-operated tools designed to easily open metal cans without manual effort.
They typically consist of a motor, a cutting mechanism, and a housing unit.
The primary advantage of these openers is their portability, making them ideal for home kitchens, camping trips, and even in settings where traditional can openers might be inconvenient.
Step-by-Step Manufacturing Process
1. Design and Planning
The manufacturing process begins with the design phase.
Engineers and designers collaborate to create a blueprint of the can opener, taking into account factors such as size, shape, weight, and ergonomic design.
Computer-aided design (CAD) software is often used to create 3D models and simulations.
These models help in visualizing how the components fit together and function.
2. Material Selection
Selecting the right materials is crucial for the durability and functionality of the can opener.
The primary materials used are typically plastic for the housing and metal for the internal components like the cutting blade and motor.
The choice of materials directly impacts the product’s weight, durability, and overall performance.
3. Component Manufacturing
Once the design and materials are finalized, the manufacturing of individual components begins.
Plastic parts are usually produced using injection molding, a process that involves injecting molten plastic into a mold cavity.
Metal parts, on the other hand, are typically fabricated using stamping or cutting techniques.
The motor is procured from specialized manufacturers and is designed to meet specific torque and power requirements.
4. Assembly
The assembly process involves putting together the various components to form the final product.
This step is often carried out on an assembly line to ensure consistency and efficiency.
First, the motor is fitted into the housing, followed by the installation of the cutting mechanism.
Wiring is then added to connect the motor to the power source (usually a battery compartment).
Finally, the housing is sealed, often using screws or ultrasonic welding, to secure all internal components.
5. Quality Control
Quality control is a critical part of the manufacturing process.
Each can opener undergoes rigorous testing to ensure it meets safety and performance standards.
Tests include running the motor, checking the sharpness and alignment of the cutting blade, and verifying the integrity of the housing.
Only products that pass these tests are sent for packaging and distribution.
Enhancing Efficiency with Torque Control Technology
Torque control is a crucial aspect of the functionality of electric can openers.
Torque refers to the rotational force generated by the motor to turn the cutting blade.
Effective torque control ensures that the can opener can effortlessly cut through the metal lid, without stalling or causing damage.
1. Importance of Torque Control
Torque control technology ensures that the motor delivers consistent power, regardless of the can material or thickness.
This consistency helps in achieving a smooth and clean cut every time.
Moreover, effective torque control minimizes wear and tear on the motor and cutting blade, thereby extending the product’s lifespan.
2. Incorporating Advanced Sensors
Modern portable electric can openers are equipped with advanced sensors that monitor the torque in real time.
These sensors communicate with the motor’s control unit to adjust the power output dynamically.
For instance, if the sensor detects increased resistance while cutting a particularly thick can, it instructs the motor to ramp up the power.
Conversely, if the resistance decreases, the motor reduces power to conserve energy.
3. Software Integration
Besides hardware improvements, software plays a pivotal role in torque control.
Embedded software algorithms analyze data from the sensors and make instantaneous adjustments to the motor’s operation.
This integration ensures that the can opener operates at optimal efficiency, regardless of varying conditions.
4. Battery Efficiency
Torque control technology also contributes to better battery management.
By adjusting the motor’s power based on the task at hand, the can opener uses only the necessary amount of energy.
This efficient power usage translates to longer battery life, making the device more convenient for users who rely on its portability.
Challenges and Future Directions
While torque control technology has significantly improved the performance of portable electric can openers, there are still challenges to address.
One major issue is the balance between power and safety.
Enhancing the motor’s torque without compromising safety features such as auto-shutoff is a continual concern for manufacturers.
Future advancements may include more refined sensors and AI integration for even smarter torque control.
These improvements could lead to can openers that not only adjust power levels but also predict when maintenance is needed, ultimately offering better user experiences.
In summary, the journey of a portable electric can opener from concept to kitchen is a fascinating blend of engineering, design, and technology.
By focusing on efficient manufacturing processes and incorporating advanced torque control technology, manufacturers can produce reliable and user-friendly can openers that simplify one of the most mundane kitchen tasks.
資料ダウンロード
QCD調達購買管理クラウド「newji」は、調達購買部門で必要なQCD管理全てを備えた、現場特化型兼クラウド型の今世紀最高の購買管理システムとなります。
ユーザー登録
調達購買業務の効率化だけでなく、システムを導入することで、コスト削減や製品・資材のステータス可視化のほか、属人化していた購買情報の共有化による内部不正防止や統制にも役立ちます。
NEWJI DX
製造業に特化したデジタルトランスフォーメーション(DX)の実現を目指す請負開発型のコンサルティングサービスです。AI、iPaaS、および先端の技術を駆使して、製造プロセスの効率化、業務効率化、チームワーク強化、コスト削減、品質向上を実現します。このサービスは、製造業の課題を深く理解し、それに対する最適なデジタルソリューションを提供することで、企業が持続的な成長とイノベーションを達成できるようサポートします。
オンライン講座
製造業、主に購買・調達部門にお勤めの方々に向けた情報を配信しております。
新任の方やベテランの方、管理職を対象とした幅広いコンテンツをご用意しております。
お問い合わせ
コストダウンが利益に直結する術だと理解していても、なかなか前に進めることができない状況。そんな時は、newjiのコストダウン自動化機能で大きく利益貢献しよう!
(Β版非公開)