- お役立ち記事
- Portable Projector Tripod Manufacturing Process and Stability Reinforcement
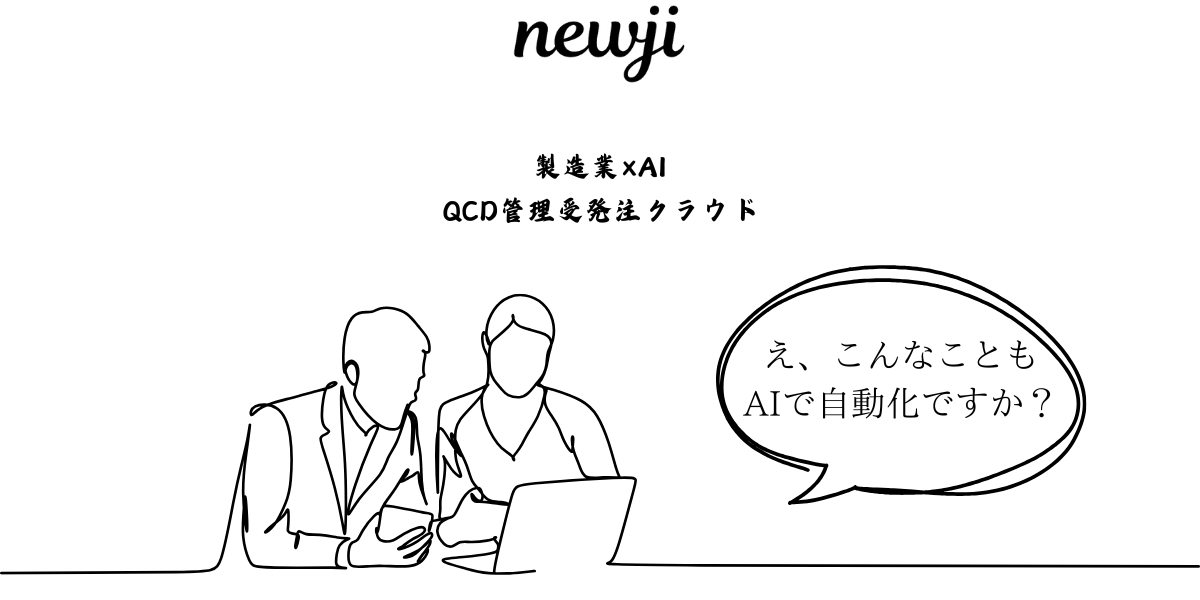
Portable Projector Tripod Manufacturing Process and Stability Reinforcement
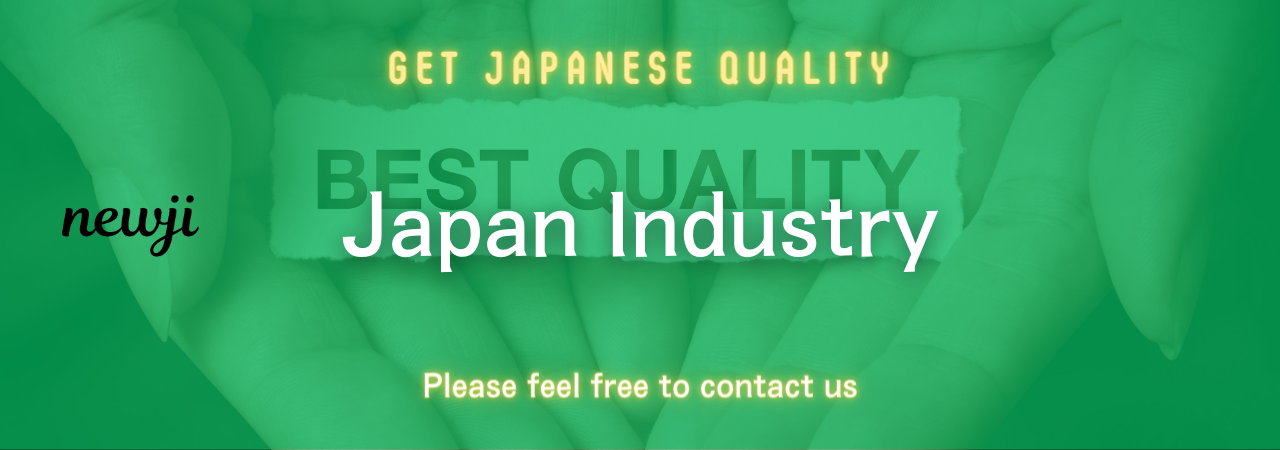
目次
Introduction to Portable Projector Tripods
Portable projectors have become increasingly popular for both personal and professional use, enabling presentations, movie screenings, and more, anywhere with ease.
A critical component that enhances their functionality is the portable projector tripod.
These tripods ensure stability and provide flexibility, making them an essential accessory for a seamless projection experience.
Understanding the manufacturing process and the methods used to reinforce their stability can provide valuable insights into selecting the right tripod for your needs.
The Importance of a Stable Tripod
The stability of a projector tripod is crucial for a smooth, uninterrupted viewing experience.
A wobbly or an unstable tripod can result in shaky images, disrupted presentations, and frustration for users.
To prevent such issues, manufacturers focus on creating tripods that provide reliable support, even on uneven surfaces.
The Manufacturing Process of Portable Projector Tripods
Manufacturing a portable projector tripod involves several precise steps to ensure quality and durability.
Let’s break down each stage of the process.
Design and Material Selection
The process begins with designing the tripod.
Engineers work to develop a model that combines lightweight properties with maximum strength.
Material selection is pivotal, with a focus on alloys such as aluminum or carbon fiber, which offer excellent strength-to-weight ratios.
The design phase also includes determining the number of legs and their adjustability, ergonomics, and compatibility with various projector models.
Prototype Development and Testing
Once the design is finalized, a prototype is developed.
The prototype undergoes rigorous testing to assess its stability, weight-bearing capacity, and ease of use.
Tests are conducted under different environmental conditions to ensure the tripod’s adaptability.
Precision Manufacturing
With successful testing, the manufacturing proceeds to the precision machining of parts.
Components such as the legs, central column, and head mount are crafted using CNC machines to ensure high precision.
Quality control measures are integrated at this stage, with parts inspected for any defects or discrepancies from design specifications.
Assembly and Adjustment Mechanisms
After machining, the components are assembled.
This process involves fitting together the central column with the legs and the head mount.
Special attention is given to the adjustment mechanisms such as locks and hinges, ensuring they operate smoothly and can sustain repeated use.
The assembly phase is also when non-slip rubber feet are attached to the tripod legs for added stability.
Final Testing and Quality Assurance
After assembly, the complete tripod undergoes final testing.
This includes load testing to confirm it can support the designated projector weight and stability tests on different surfaces.
Quality assurance teams check for proper functioning of adjustment features, overall strength, and durability.
This phase ensures that the final product meets all safety standards before it enters the market.
Techniques for Stability Reinforcement
Enhancing the stability of a portable projector tripod is vital to ensure user satisfaction.
Several techniques are employed during manufacturing and post-production to achieve this objective.
Structural Reinforcement
Structural reinforcement methods include using thicker materials in high-stress areas and incorporating cross-bracing into the design.
These techniques enhance the tripod’s ability to withstand lateral forces, maintaining balance even if accidentally nudged.
Wide Base and Weight Distribution
Designing a wide base with significant weight distribution helps in minimizing shifts and wobbles.
Tripods may include telescoping legs that allow for a broad foundation to enhance stability.
Center of Gravity Optimization
Ensuring the projector is centered over the tripod’s legs can dramatically enhance stability.
Adjustable head mounts allow precise positioning of the projector’s center of gravity, reducing the risk of tipping over.
Advanced Locking Mechanisms
High-quality locking mechanisms on the legs and head mount prevent slippage during use.
These locks can include twist locks or lever locks, each tested for endurance and grip.
Material Innovations
Material innovations such as anti-shock composites and vibration dampening technology can also improve stability.
These materials absorb minor vibrations that can affect image clarity, particularly in outdoor environments.
Conclusion
The manufacturing process and stability reinforcement of portable projector tripods are crucial to delivering a smooth and reliable user experience.
From design and material selection to final quality assurance, each production step is optimized to produce high-quality tripods.
Through structural enhancements, weight distribution strategies, and innovative materials, manufacturers continue to improve the stability and functionality of these essential devices.
Understanding this process helps consumers make informed decisions, ensuring their projector setup is secure and efficient.
資料ダウンロード
QCD調達購買管理クラウド「newji」は、調達購買部門で必要なQCD管理全てを備えた、現場特化型兼クラウド型の今世紀最高の購買管理システムとなります。
ユーザー登録
調達購買業務の効率化だけでなく、システムを導入することで、コスト削減や製品・資材のステータス可視化のほか、属人化していた購買情報の共有化による内部不正防止や統制にも役立ちます。
NEWJI DX
製造業に特化したデジタルトランスフォーメーション(DX)の実現を目指す請負開発型のコンサルティングサービスです。AI、iPaaS、および先端の技術を駆使して、製造プロセスの効率化、業務効率化、チームワーク強化、コスト削減、品質向上を実現します。このサービスは、製造業の課題を深く理解し、それに対する最適なデジタルソリューションを提供することで、企業が持続的な成長とイノベーションを達成できるようサポートします。
オンライン講座
製造業、主に購買・調達部門にお勤めの方々に向けた情報を配信しております。
新任の方やベテランの方、管理職を対象とした幅広いコンテンツをご用意しております。
お問い合わせ
コストダウンが利益に直結する術だと理解していても、なかなか前に進めることができない状況。そんな時は、newjiのコストダウン自動化機能で大きく利益貢献しよう!
(Β版非公開)