- お役立ち記事
- Potential issues in logistics efficiency projects from the perspective of the purchasing department
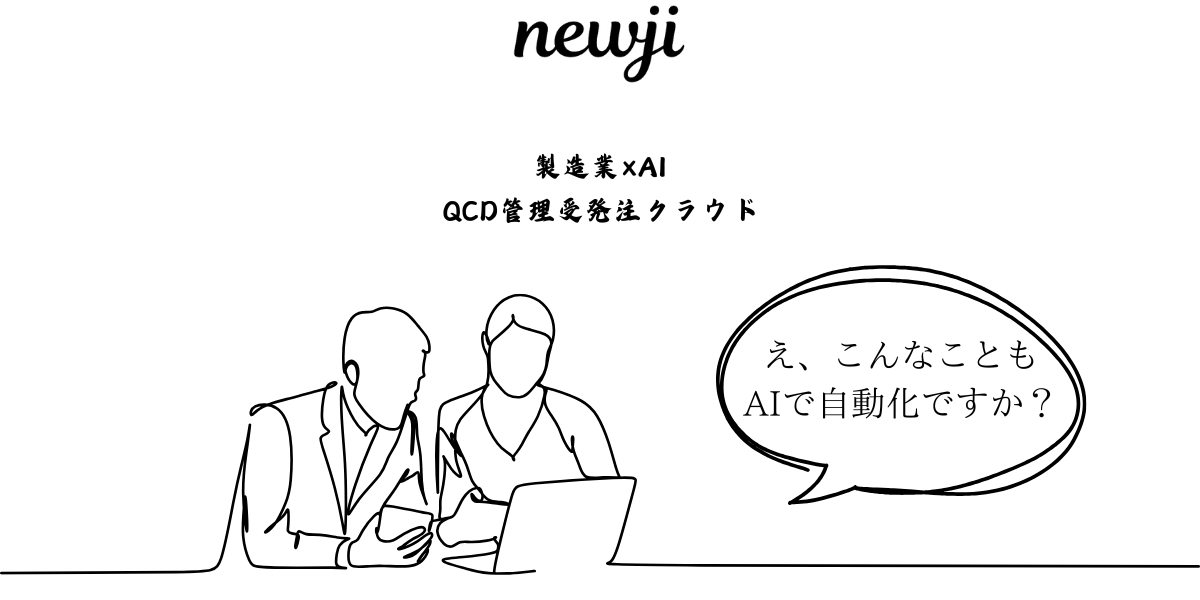
Potential issues in logistics efficiency projects from the perspective of the purchasing department
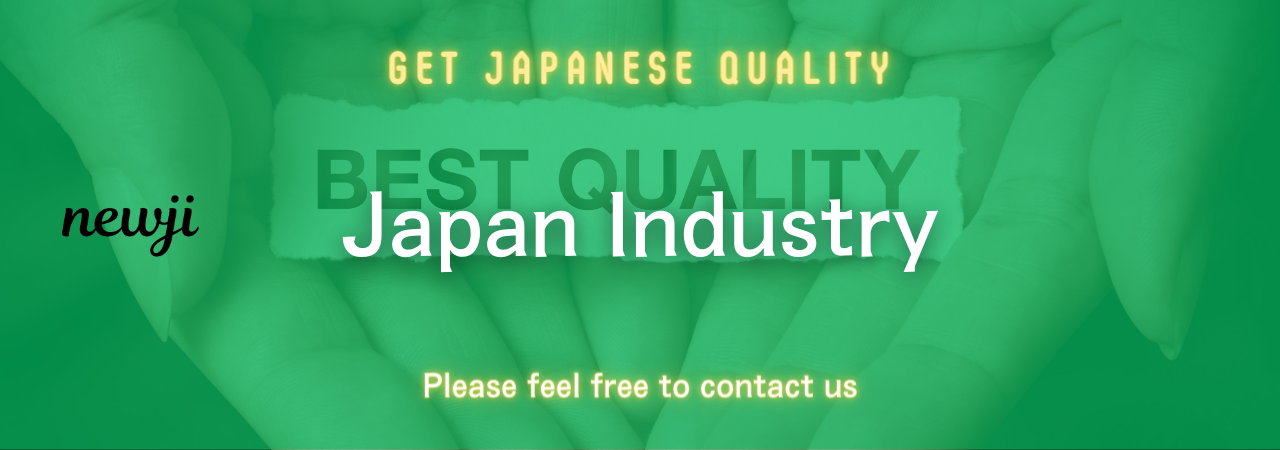
目次
Understanding Logistics Efficiency Projects
Logistics efficiency projects are initiatives designed to optimize the supply chain and make the movement of goods more streamlined and cost-effective.
These projects aim to reduce delays, cut costs, and improve service delivery by reorganizing logistics processes, adopting new technologies, or implementing advanced analytics.
However, these efficiency projects can present several challenges when viewed from the perspective of the purchasing department.
The Role of the Purchasing Department
The purchasing department plays a crucial role in any organization.
It is responsible for acquiring the goods and services that the company needs to carry out its business operations.
This includes everything from raw materials to office supplies.
In the context of logistics efficiency projects, the purchasing department is a vital player.
It must ensure that the inputs required for the projects are bought at the best possible price and quality.
This task becomes increasingly challenging when logistics processes are altered or updated.
Maintaining Cost Control
One of the main goals of logistics efficiency projects is to reduce costs.
However, this can sometimes have an unintended effect on the purchasing department’s ability to maintain cost control.
Changes in logistics processes might require the acquisition of new materials or services, and these may not have been anticipated in the initial budget.
As a result, purchasing managers must be vigilant in adjusting their strategies to accommodate unexpected expenses, such as new vendor contracts or increased transportation fees.
Additionally, the shift to new suppliers as part of a logistics efficiency project can further complicate negotiations and cost assessments.
Supplier Relationship Management
Logistics efficiency projects may lead to changing supplier relationships, which can pose a significant challenge to the purchasing department.
The introduction of new technologies or processes might necessitate sourcing from different suppliers than those traditionally used.
Building new supplier relationships takes time and effort and requires due diligence to ensure reliability and compatibility with the company’s needs.
Moreover, long-standing suppliers might feel sidelined if they are not included in the new process, potentially leading to a degradation in cooperation or disruptions in supply.
Impact on Inventory Management
Efficient logistics projects can significantly impact how inventory is managed within an organization.
The purchasing department must be agile in understanding and reacting to these changes to ensure inventory levels are optimized.
Balancing Just-In-Time Services
A popular strategy in logistics efficiency is the implementation of just-in-time (JIT) inventory systems, which aim to reduce inventory carrying costs by aligning orders with production schedules.
While this can enhance efficiency, it also places additional pressure on the purchasing department to manage precise delivery schedules.
The increased need for coordination with manufacturers and suppliers can lead to higher transactional complexities and requires robust communication channels to prevent delays.
Addressing Technology Integration
New technologies introduced during logistics projects can change inventory tracking and management systems.
For purchasing departments, this implies adapting to or acquiring new software solutions and ensuring these systems are compatible with existing processes.
Implementing and training staff on new inventory management systems can involve additional costs and time, impacting the overall productivity until the transition is complete.
Communication and Collaboration Challenges
Effective communication across multiple departments is critical for the success of logistics efficiency projects.
The purchasing department, in particular, must effectively communicate its needs and constraints to other teams to ensure that efficiency gains do not lead to inefficiencies elsewhere.
Aligning Department Goals
Logistics projects often require a coordination of objectives between different departments.
Misalignment may occur when the purchasing department’s goal of securing materials at the lowest cost conflicts with other departments’ priorities, such as seeking sustainable or ethically sourced products.
Ensuring that all department goals are aligned requires careful planning and ongoing dialogue, which can sometimes be a complex process.
Ensuring Stakeholder Involvement
For logistics projects to truly succeed, stakeholder involvement is essential.
This means that the purchasing department should have adequate representation in project planning stages.
Failing to involve purchasing early might lead to overlooked insights or project requirements, risking inefficiencies post-implementation.
Continual updates and feedback mechanisms should be in place to foster a collaborative environment and ensure the success of logistics projects.
Conclusion: Balancing Efficiency and Functionality
Logistics efficiency projects offer tremendous potential in terms of cost savings and service improvements.
However, from the purchasing department’s perspective, these projects can introduce new challenges in cost management, supplier relations, inventory control, and cross-departmental collaboration.
By anticipating these potential issues and maintaining a proactive and communicative approach, purchasing managers can successfully navigate the complexities of logistics efficiency projects.
Fostering a culture of adaptability and continuous improvement will enable the department to balance logistical efficiency with the functional needs of the business, leading to sustained operational success.
資料ダウンロード
QCD調達購買管理クラウド「newji」は、調達購買部門で必要なQCD管理全てを備えた、現場特化型兼クラウド型の今世紀最高の購買管理システムとなります。
ユーザー登録
調達購買業務の効率化だけでなく、システムを導入することで、コスト削減や製品・資材のステータス可視化のほか、属人化していた購買情報の共有化による内部不正防止や統制にも役立ちます。
NEWJI DX
製造業に特化したデジタルトランスフォーメーション(DX)の実現を目指す請負開発型のコンサルティングサービスです。AI、iPaaS、および先端の技術を駆使して、製造プロセスの効率化、業務効率化、チームワーク強化、コスト削減、品質向上を実現します。このサービスは、製造業の課題を深く理解し、それに対する最適なデジタルソリューションを提供することで、企業が持続的な成長とイノベーションを達成できるようサポートします。
オンライン講座
製造業、主に購買・調達部門にお勤めの方々に向けた情報を配信しております。
新任の方やベテランの方、管理職を対象とした幅広いコンテンツをご用意しております。
お問い合わせ
コストダウンが利益に直結する術だと理解していても、なかなか前に進めることができない状況。そんな時は、newjiのコストダウン自動化機能で大きく利益貢献しよう!
(Β版非公開)