- お役立ち記事
- “Powering Innovation: How ACDC Principles and Japanese Manufacturing Electrify the Future”
“Powering Innovation: How ACDC Principles and Japanese Manufacturing Electrify the Future”
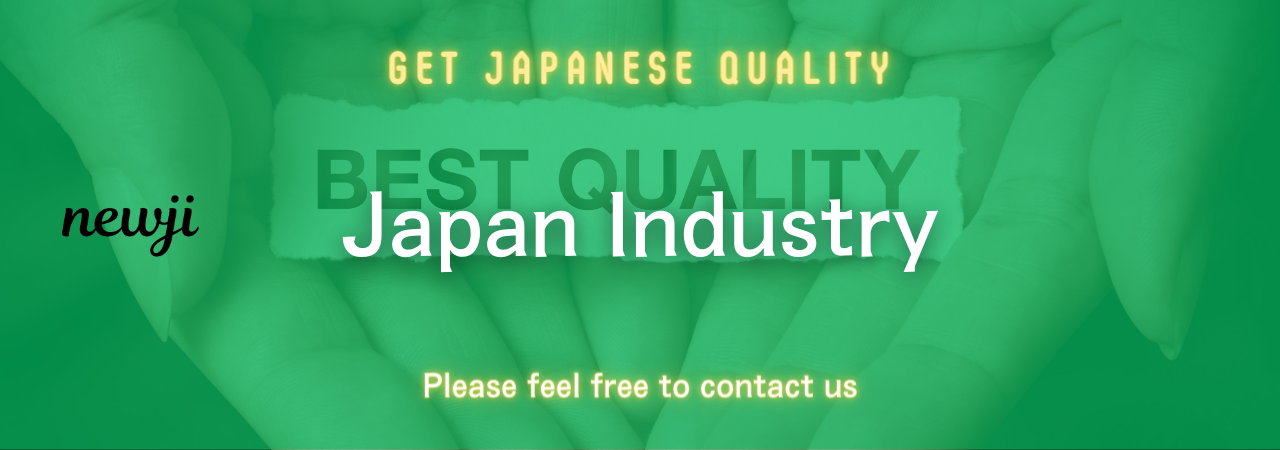
目次
A New Frontier in Manufacturing: The Intersection of ACDC Principles and Japanese Craftsmanship
In today’s competitive global market, manufacturers are constantly seeking methods to improve efficiency, quality, and innovation. The ACDC principles—Automation, Connectivity, Digitalization, and Collaboration—are proving to be transformative in various sectors. When these principles are combined with the meticulous craftsmanship of Japanese manufacturing, the results can be extraordinary.
The Essence of ACDC Principles
1. Automation
Automation involves the use of advanced machinery and software to perform tasks that were traditionally completed by human workers. The primary objective is to enhance efficiency, reduce human error, and improve production speed.
2. Connectivity
Connectivity refers to the interlinking of systems, machines, and even factories to ensure seamless communication and data sharing. This connectivity promotes quicker decision-making and more cohesive operations across the supply chain.
3. Digitalization
Digitalization involves converting processes and data into a digital format. It enables real-time monitoring, predictive maintenance, and data analytics, transforming raw data into actionable insights.
4. Collaboration
Collaboration emphasizes the importance of teamwork and synergy among different departments, suppliers, and even countries. It fosters an environment where innovation can thrive through shared knowledge and resources.
The Unique Strengths of Japanese Manufacturing
Kaizen: The Path to Continuous Improvement
The philosophy of Kaizen, or continuous improvement, is a cornerstone of Japanese manufacturing. It focuses on incremental changes and improving work processes to enhance efficiency and quality. This principle encourages a culture of sustained excellence.
Quality Control
Japanese manufacturers are renowned for their rigorous quality control processes. From the procurement of raw materials to the final stages of production, every step undergoes meticulous scrutiny. This attention to detail ensures that products meet the highest standards.
Lean Manufacturing
Lean manufacturing aims to minimize waste without sacrificing productivity. This methodology, which originated in Japan, streamlines production processes, reduces costs, and boosts overall efficiency. Concepts like Just-In-Time (JIT) and 5S are integral components of this system.
Combining ACDC Principles with Japanese Manufacturing
Automation and Lean Manufacturing
By integrating advanced automation technologies with lean manufacturing principles, companies can significantly enhance their production capabilities. Automated systems can handle repetitive tasks more efficiently, allowing human workers to focus on more complex and value-added activities. Robotics play a crucial role here, taking on monotonous or hazardous tasks and ensuring that production lines are both safe and efficient.
Digitalization and Quality Control
Digitalization has the potential to revolutionize quality control processes in Japanese manufacturing. Real-time data collection and analysis ensure that any deviations from quality standards are immediately identified and rectified. This minimizes defects, reduces waste, and promotes a culture of continuous improvement.
Connectivity and Kaizen
Connectivity enhances the practice of Kaizen by promoting the seamless exchange of information across different stages of the manufacturing process. By sharing data and insights, teams can collaborate more effectively to identify areas for improvement. IoT (Internet of Things) devices and sensors can monitor every aspect of production, providing valuable feedback that drives continuous improvement.
Collaboration and Supplier Relationships
Incorporating collaboration into supplier relationships can lead to benefits for all parties involved. Japanese manufacturers often engage in long-term relationships with their suppliers, fostering a sense of mutual trust and shared goals. Collaborative efforts in R&D, production planning, and logistics can result in innovative solutions that benefit both the manufacturer and the supplier.
Practical Insights from International Procurement
Negotiating with Japanese Suppliers
Negotiating with Japanese suppliers requires an understanding of cultural nuances and business practices. Patience, respect, and long-term relationship-building are crucial. It is essential to approach negotiations with a win-win mindset, emphasizing the mutual benefits of the partnership. Establishing clear communication channels and setting realistic expectations can pave the way for successful negotiations.
Overcoming Language Barriers
Language barriers can pose challenges in international procurement. Engaging professional translators and ensuring that documentation is available in both languages can mitigate misunderstandings. Additionally, building a team that includes bilingual members who understand both the language and cultural context can be highly beneficial.
Ensuring Compliance and Regulatory Standards
Japanese manufacturers adhere to stringent compliance and regulatory standards. When engaging with Japanese suppliers, it is vital to ensure that all products and processes align with international regulations. This might involve independent audits and certifications to maintain trust and compliance.
The Advantages and Disadvantages of Sourcing from Japan
Advantages
**High Quality Standards:** Japanese manufacturers are known for their uncompromising quality standards. Products sourced from Japan are often superior in terms of durability and performance.
**Innovation and Technology:** Japan is a global leader in technological advancements. By sourcing from Japanese suppliers, companies can access cutting-edge technology and innovative solutions.
**Reliability:** Japanese manufacturers are recognized for their reliability and punctual delivery. This ensures a smoother supply chain with fewer disruptions.
Disadvantages
**Cost:** High quality and innovation often come at a higher cost. Products from Japanese suppliers may be more expensive compared to those from other regions.
**Cultural Differences:** Navigating cultural differences can be challenging. Misunderstandings and miscommunications can arise if not managed properly.
**Lead Time:** Due to geographical distance and meticulous quality control procedures, lead times for products sourced from Japan might be longer.
Market Conditions and Emerging Trends
Shift Toward Sustainable Practices
Sustainability is becoming a major focus in manufacturing. Japanese companies are increasingly adopting eco-friendly practices, such as reducing carbon emissions and utilizing recyclable materials. This shift aligns with global trends toward environmental responsibility and offers a competitive edge.
Adoption of Smart Manufacturing
Smart manufacturing, which integrates ACDC principles, is gaining traction. Through the use of IoT, AI, and advanced analytics, manufacturers can optimize production processes, enhance product quality, and improve overall efficiency. Japanese manufacturers are at the forefront of adopting these smart manufacturing practices.
Increased Focus on Resilience
Recent global disruptions have highlighted the importance of supply chain resilience. Japanese manufacturers are investing in strategies to mitigate risks, such as diversifying supply sources, enhancing inventory management, and leveraging digital tools to predict and respond to disruptions.
Best Practices for Successful Procurement and Purchasing
Build Strong Relationships
Spend time cultivating robust relationships with Japanese suppliers. Regular communication, visits, and openness to cultural exchange can strengthen these partnerships.
Embrace Technology
Leverage advanced digital tools to enhance procurement processes. Use software for real-time tracking, predictive analytics for demand forecasting, and blockchain for transparency and traceability.
Focus on Total Cost of Ownership (TCO)
Evaluate the total cost of ownership rather than just the initial purchase price. Consider factors like quality, reliability, and long-term performance, which can impact overall costs.
Engage in Continuous Learning
Stay updated with the latest trends and technologies in the manufacturing sector. Continuous learning and adaptation are essential for maintaining a competitive edge.
Conclusion: Powering Innovation for the Future
Combining the ACDC principles with Japanese manufacturing techniques creates a powerful synergy that can drive significant advancements in the manufacturing sector. By embracing automation, connectivity, digitalization, and collaboration, companies can achieve new levels of efficiency and innovation.
Japanese manufacturing’s commitment to quality, lean practices, and continuous improvement provides an excellent foundation for these principles to flourish. Understanding the intricacies of international procurement, from effective negotiation strategies to overcoming cultural barriers, is critical for harnessing the full potential of Japanese suppliers.
As market conditions evolve, adopting sustainable practices and smart manufacturing technologies will be vital. Companies that successfully integrate these elements into their procurement and purchasing strategies will be well-positioned to lead in the competitive global landscape.
The path to powering innovation is clear. By embracing the best of both worlds, manufacturers can electrify the future and set new standards of excellence in the industry.
資料ダウンロード
QCD調達購買管理クラウド「newji」は、調達購買部門で必要なQCD管理全てを備えた、現場特化型兼クラウド型の今世紀最高の購買管理システムとなります。
ユーザー登録
調達購買業務の効率化だけでなく、システムを導入することで、コスト削減や製品・資材のステータス可視化のほか、属人化していた購買情報の共有化による内部不正防止や統制にも役立ちます。
NEWJI DX
製造業に特化したデジタルトランスフォーメーション(DX)の実現を目指す請負開発型のコンサルティングサービスです。AI、iPaaS、および先端の技術を駆使して、製造プロセスの効率化、業務効率化、チームワーク強化、コスト削減、品質向上を実現します。このサービスは、製造業の課題を深く理解し、それに対する最適なデジタルソリューションを提供することで、企業が持続的な成長とイノベーションを達成できるようサポートします。
オンライン講座
製造業、主に購買・調達部門にお勤めの方々に向けた情報を配信しております。
新任の方やベテランの方、管理職を対象とした幅広いコンテンツをご用意しております。
お問い合わせ
コストダウンが利益に直結する術だと理解していても、なかなか前に進めることができない状況。そんな時は、newjiのコストダウン自動化機能で大きく利益貢献しよう!
(Β版非公開)