- お役立ち記事
- Powering Japan: The Future of Manufacturing with Direct Current Innovation
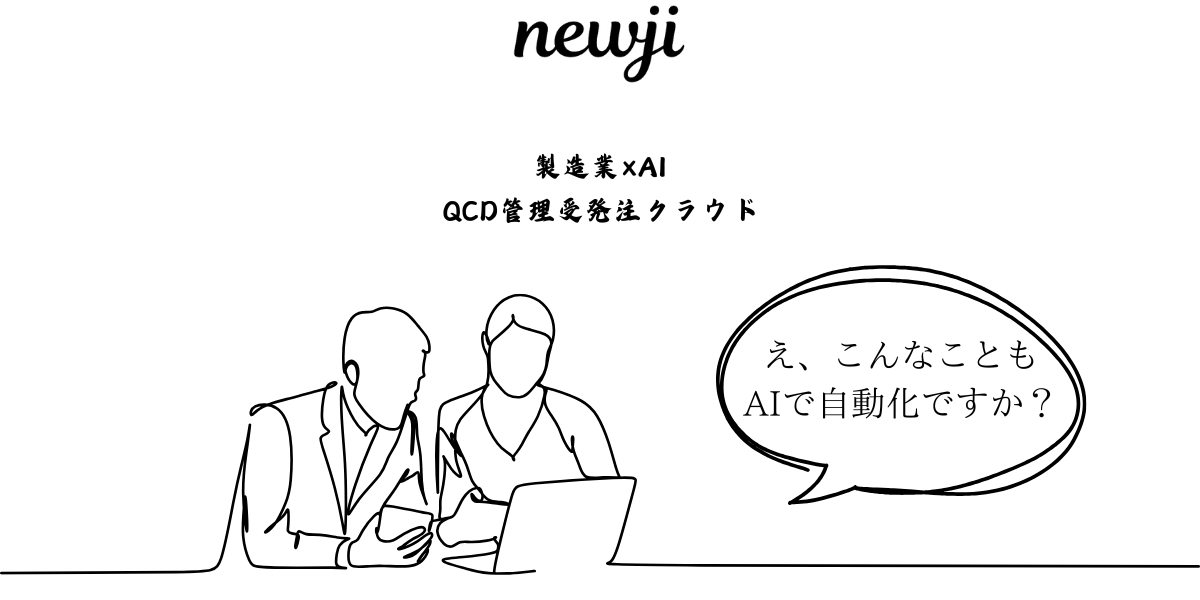
Powering Japan: The Future of Manufacturing with Direct Current Innovation
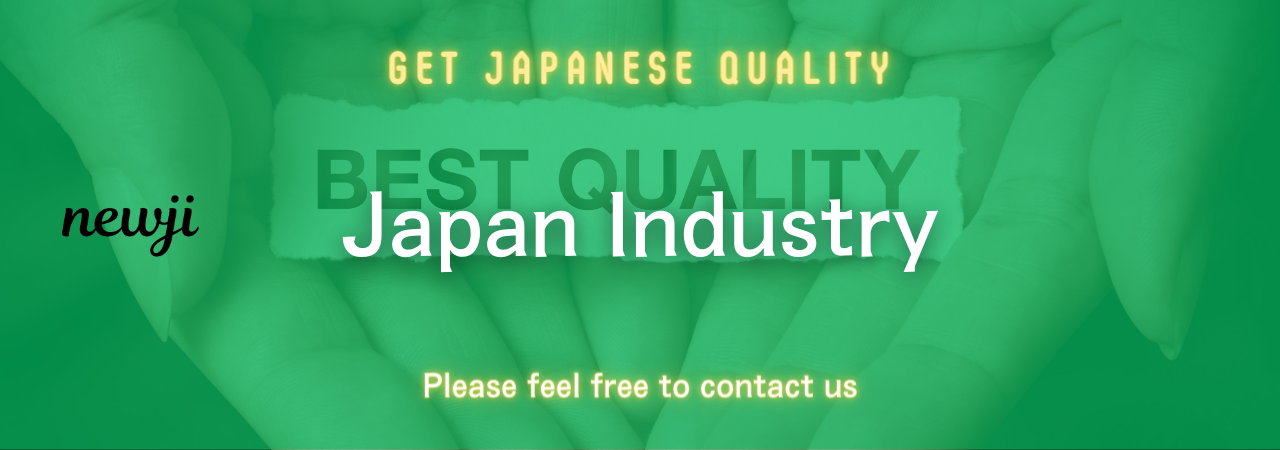
目次
The Rise of Direct Current Innovation in Japanese Manufacturing
In recent years, the manufacturing landscape in Japan has undergone significant transformation.
Direct current (DC) innovation has emerged as a pivotal force driving this evolution.
Japanese manufacturers are at the forefront of integrating DC technologies into their production processes.
This shift is not only enhancing efficiency but also setting new standards for quality and sustainability in the industry.
The adoption of DC systems marks a departure from traditional alternating current (AC) methodologies, offering unique advantages that align with the demands of modern manufacturing.
As global competition intensifies, Japanese companies are leveraging DC innovations to maintain their competitive edge and meet the increasing expectations of consumers worldwide.
Advantages of Direct Current in Manufacturing Processes
Direct current technology offers a myriad of benefits that make it an attractive option for manufacturers.
These advantages extend beyond mere energy efficiency, encompassing aspects such as precision, control, and environmental sustainability.
Understanding these benefits is crucial for procurement and purchasing professionals who play a vital role in integrating DC systems into manufacturing operations.
Energy Efficiency and Cost Savings
One of the most significant advantages of direct current is its superior energy efficiency compared to alternating current systems.
DC power eliminates energy losses associated with frequency conversion, resulting in lower operational costs.
Manufacturers can achieve substantial savings on energy bills by adopting DC technologies, making it a financially sound investment.
Moreover, the consistent power flow of DC systems reduces the wear and tear on machinery, leading to extended equipment lifespan and reduced maintenance expenses.
Enhanced Precision and Control
Direct current provides manufacturers with greater precision and control over the manufacturing process.
DC-powered machinery and equipment offer finer adjustments and smoother operations, which are essential for high-precision industries such as electronics and automotive manufacturing.
This enhanced control leads to improved product quality, reduced defect rates, and increased customer satisfaction.
Furthermore, the ability to precisely regulate power input allows for better synchronization of production processes, enhancing overall operational efficiency.
Environmental Benefits
The adoption of direct current technology contributes to environmental sustainability, a key consideration for modern manufacturers.
DC systems are inherently more energy-efficient, reducing the overall carbon footprint of manufacturing operations.
Additionally, the integration of renewable energy sources, such as solar panels, is more seamless with DC power, promoting the use of clean energy in production.
These environmental benefits not only align with global sustainability goals but also enhance the corporate reputation of manufacturers committed to green practices.
Challenges and Considerations in Implementing Direct Current Systems
While the benefits of direct current are compelling, manufacturers must navigate several challenges when implementing DC systems.
Addressing these challenges is essential to ensure a smooth transition and maximize the potential of DC innovations.
Initial Investment and Infrastructure
The initial cost of transitioning to direct current systems can be high, encompassing expenses related to new equipment, infrastructure upgrades, and potential downtime during installation.
Manufacturers must carefully evaluate the long-term cost savings against these upfront investments.
Strategic financial planning and phased implementation approaches can help mitigate the financial burden associated with adopting DC technologies.
Technical Expertise and Training
Implementing DC systems requires specialized technical knowledge and skills that may not be readily available within the existing workforce.
Training programs and partnerships with technology providers are essential to equip employees with the necessary expertise.
Investing in workforce development ensures that manufacturers can effectively operate and maintain DC systems, thereby maximizing their benefits.
Integration with Existing Systems
Integrating direct current technologies with legacy AC systems poses technical challenges that require careful planning and execution.
Compatibility issues, retrofitting requirements, and potential disruptions to ongoing operations must be addressed to ensure seamless integration.
Collaborating with experienced suppliers and engineering partners can facilitate the integration process and minimize operational disruptions.
Procurement and Purchasing Strategies for Direct Current Technologies
Effective procurement and purchasing strategies are critical for successfully adopting direct current innovations in manufacturing.
These strategies encompass supplier selection, negotiation techniques, and evaluation of supplier capabilities to ensure the best outcomes.
Selecting the Right Japanese Suppliers
Japanese suppliers are renowned for their technological expertise and commitment to quality, making them ideal partners for DC innovations.
When selecting suppliers, procurement professionals should assess factors such as technical capabilities, production capacity, and track record in delivering DC solutions.
Building a shortlist of potential suppliers based on these criteria facilitates informed decision-making and fosters successful partnerships.
Negotiation Techniques with Japanese Manufacturers
Negotiating with Japanese suppliers requires cultural sensitivity and an understanding of Japanese business practices.
Building trust and establishing long-term relationships are paramount, as Japanese companies prioritize mutual respect and collaboration.
Effective negotiation techniques include clear communication of requirements, willingness to engage in open dialogues, and flexibility in negotiations to accommodate the supplier’s perspectives.
Patience and persistence are key, as negotiations may take longer compared to other markets due to the thorough decision-making processes inherent in Japanese business culture.
Evaluating Supplier Reliability and Quality
Ensuring supplier reliability and product quality is essential when procuring direct current technologies.
Procurement professionals should conduct thorough assessments, including site visits, quality audits, and performance evaluations, to verify the capabilities of potential suppliers.
Leveraging certifications such as ISO and industry-specific standards can provide additional assurance of a supplier’s commitment to quality.
Establishing clear quality expectations and monitoring mechanisms ensures that suppliers can consistently meet the manufacturing requirements.
Market Conditions and Trends in Direct Current Manufacturing
Understanding the current market landscape and emerging trends is crucial for procurement professionals seeking to capitalize on DC innovations in Japanese manufacturing.
Current Market Landscape
The direct current manufacturing market in Japan is characterized by rapid technological advancements and strong demand for energy-efficient solutions.
Japanese manufacturers are investing heavily in research and development to pioneer innovative DC applications across various industries.
Competitive pressures and the need for sustainable production practices are driving the adoption of DC systems, creating a robust market environment for DC technologies.
Future Projections and Innovation
The future of direct current manufacturing in Japan is poised for continued growth and innovation.
Advancements in DC power electronics, energy storage solutions, and smart manufacturing technologies are expected to further enhance the capabilities of DC systems.
The integration of artificial intelligence and IoT with DC manufacturing processes will enable greater automation, predictive maintenance, and real-time optimization, propelling the industry toward unprecedented levels of efficiency and productivity.
Best Practices for Successful Procurement of DC Innovations
Implementing direct current innovations successfully requires adherence to best practices that encompass strategic planning, supplier management, and continuous improvement.
Building Strong Supplier Relationships
Strong relationships with suppliers are foundational to successful procurement.
Collaborative partnerships foster open communication, mutual trust, and shared objectives, facilitating innovation and problem-solving.
Regular engagement with suppliers through meetings, joint development projects, and feedback sessions ensures alignment and fosters a sense of partnership that can lead to long-term success.
Ensuring Quality Control and Compliance
Maintaining strict quality control and compliance with industry standards is essential.
Implementing comprehensive quality management systems, conducting regular audits, and enforcing adherence to regulatory requirements ensures that DC technologies meet the necessary performance and safety standards.
Proactive quality assurance practices minimize defects, reduce risks, and enhance the reliability of manufacturing processes.
Leveraging Technology for Optimal Procurement
Utilizing advanced procurement technologies can streamline processes and improve efficiency.
Digital procurement platforms, data analytics, and supply chain management tools enable better decision-making, enhance transparency, and facilitate real-time tracking of orders and inventory.
Embracing these technologies empowers procurement professionals to optimize sourcing strategies, reduce costs, and respond swiftly to changing market dynamics.
Case Studies: Successful Implementation of Direct Current in Japanese Manufacturing
Examining real-world examples provides valuable insights into the practical applications and benefits of direct current innovations in Japanese manufacturing.
Case Study 1: Automotive Industry
A leading Japanese automotive manufacturer integrated DC-powered assembly lines to enhance production efficiency and reduce energy consumption.
The implementation of DC systems facilitated precise control of assembly robots, resulting in increased accuracy and reduced cycle times.
Energy savings from DC-powered operations contributed to significant cost reductions, while the improved efficiency led to higher production volumes and better product quality.
This transformation underscored the strategic advantage of adopting DC technologies in the highly competitive automotive sector.
Case Study 2: Electronics Manufacturing
A prominent Japanese electronics company adopted direct current innovations to streamline its manufacturing processes.
DC-powered equipment enabled more consistent and stable power supply, crucial for assembling sensitive electronic components.
The enhanced control and precision of DC systems reduced defect rates and improved overall product reliability.
Additionally, energy efficiency gains from DC adoption aligned with the company’s sustainability goals, reinforcing its commitment to environmentally responsible manufacturing practices.
Conclusion
Direct current innovation is revolutionizing the manufacturing sector in Japan, offering substantial benefits in terms of energy efficiency, precision, and sustainability.
For procurement and purchasing professionals, understanding the advantages and challenges of DC systems is essential for successful integration.
Strategic selection of Japanese suppliers, effective negotiation, and adherence to best practices are critical components in harnessing the full potential of DC technologies.
As the market continues to evolve, ongoing investment in research, supplier relationships, and workforce training will be pivotal in maintaining Japan’s leadership in manufacturing excellence.
Embracing direct current innovations not only drives operational efficiency but also positions manufacturers to meet the future demands of a dynamic global market.
資料ダウンロード
QCD調達購買管理クラウド「newji」は、調達購買部門で必要なQCD管理全てを備えた、現場特化型兼クラウド型の今世紀最高の購買管理システムとなります。
ユーザー登録
調達購買業務の効率化だけでなく、システムを導入することで、コスト削減や製品・資材のステータス可視化のほか、属人化していた購買情報の共有化による内部不正防止や統制にも役立ちます。
NEWJI DX
製造業に特化したデジタルトランスフォーメーション(DX)の実現を目指す請負開発型のコンサルティングサービスです。AI、iPaaS、および先端の技術を駆使して、製造プロセスの効率化、業務効率化、チームワーク強化、コスト削減、品質向上を実現します。このサービスは、製造業の課題を深く理解し、それに対する最適なデジタルソリューションを提供することで、企業が持続的な成長とイノベーションを達成できるようサポートします。
オンライン講座
製造業、主に購買・調達部門にお勤めの方々に向けた情報を配信しております。
新任の方やベテランの方、管理職を対象とした幅広いコンテンツをご用意しております。
お問い合わせ
コストダウンが利益に直結する術だと理解していても、なかなか前に進めることができない状況。そんな時は、newjiのコストダウン自動化機能で大きく利益貢献しよう!
(Β版非公開)