- お役立ち記事
- Practical application of impact analysis using dynamic finite element method
月間76,176名の
製造業ご担当者様が閲覧しています*
*2025年3月31日現在のGoogle Analyticsのデータより
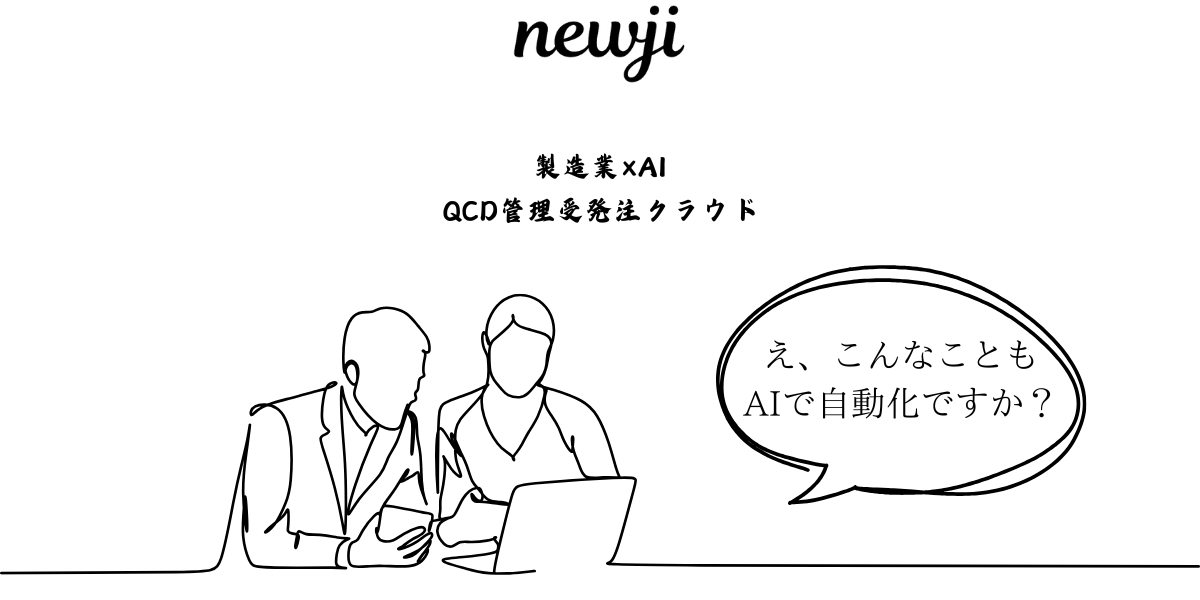
Practical application of impact analysis using dynamic finite element method
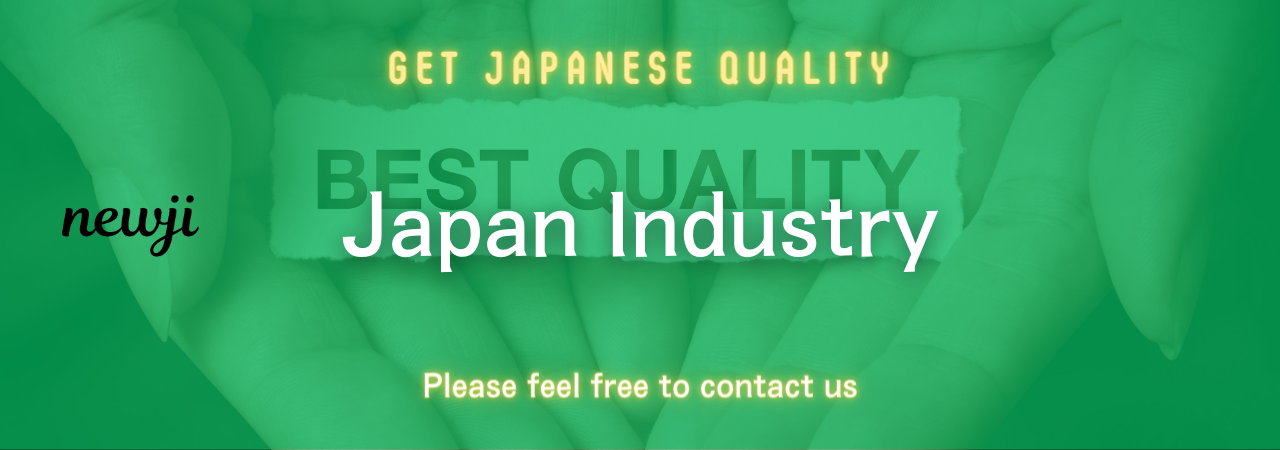
目次
Understanding the Dynamic Finite Element Method
The dynamic finite element method (DFEM) is a powerful tool used in engineering and material sciences to study how structures respond to dynamic loads.
It’s a computational technique that helps predict the behavior of components when subjected to various forces, such as impacts, vibrations, or seismic activity.
By breaking down complex structures into smaller, manageable elements, engineers can analyze and predict how these elements will perform under specified conditions.
The beauty of DFEM lies in its ability to handle both time-dependent and spatial changes in materials.
This method uses mathematical equations and algorithms to simulate real-world physical conditions, making it possible to foresee potential failures or improvements in design before they are physically constructed.
This predictive capability is crucial in industries where safety and reliability are paramount, such as automotive, aerospace, and civil engineering.
Key Components of DFEM
At its core, the DFEM revolves around a few key components:
Meshing
Meshing is one of the first and vital steps in the finite element analysis process.
It involves dividing the structure into smaller, manageable elements or nodes.
The precision of the analysis often depends on the quality of the mesh; a finer mesh typically yields more accurate results.
However, it also requires more computational resources.
Material Properties
The material properties of the elements are essential for accurate simulations.
These properties generally include density, elasticity, damping, and plasticity, which dictate how a material will behave under load.
Understanding and applying correct material properties is crucial for ensuring realistic results from the analysis.
Boundary Conditions
Boundary conditions define how the structure interacts with its surroundings.
They can include constraints like fixed supports or loads like pressure and forces.
Setting appropriate boundary conditions is necessary to replicate real-world scenarios accurately.
Time Integration
Since DFEM deals with dynamic analysis, time integration is crucial for simulating how structures respond over time.
Various methods, such as implicit and explicit time integration, are used depending on the needs of the analysis and available computational resources.
Applications of DFEM in Impact Analysis
Impact analysis is a significant application of the dynamic finite element method.
This analysis helps predict how a structure will respond to sudden forces, such as collisions or falls, which is critical in designing safer and more resilient products.
Automotive Industry
In the automotive sector, DFEM is extensively used to enhance vehicle safety.
Through impact analysis, engineers can simulate crash tests, analyze the effects of collisions, and improve the design of safety features like airbags, seatbelts, and crumple zones.
These simulations help optimize the structural integrity of vehicles, protecting passengers during accidents.
Aerospace Sector
For aerospace, ensuring the strength and reliability of aircraft structures under various dynamic loads is paramount.
DFEM helps in evaluating the impact of bird strikes, rapid depressurization, and extreme weather conditions.
By analyzing these scenarios, manufacturers can enhance the safety and performance of aircraft.
Civil Engineering
In civil engineering, DFEM plays a pivotal role in designing structures like bridges, buildings, and dams that can withstand dynamic forces such as earthquakes and wind loads.
Impact analysis aids in assessing the resilience of these structures, ensuring they remain functional and safe throughout their lifespan.
Challenges in Implementing DFEM
While DFEM offers numerous benefits, there are challenges associated with its implementation.
Computational Demand
DFEM simulations require considerable computational power and resources, especially for large and complex structures.
The need for high-performance computing systems can be a barrier for some organizations, making it essential to balance the level of detail with available resources.
Model Validation
Ensuring that the simulation results accurately reflect real-world behavior is critical.
This requires thorough validation processes, comparing simulation results with experimental data or historical performance.
Accurate validation increases confidence in the predictions made by the DFEM.
Expertise Requirement
Performing DFEM analysis requires a high level of expertise and understanding of both the method and the domain of application.
Training and experience are crucial for professionals to correctly set up and interpret simulations, making it a specialized field.
Future Prospects of DFEM in Impact Analysis
As technology advances, so does the potential of DFEM.
The ongoing development of more powerful computing systems and algorithms promises faster and more accurate simulations.
Integration with Machine Learning
The future may see the integration of DFEM with machine learning techniques to optimize simulations further.
Such integration can help in predicting outcomes more efficiently and identifying patterns or anomalies in data that might not be evident through traditional methods.
Real-time Monitoring
Advances in sensor technologies can complement DFEM by providing real-time data inputs, allowing for dynamic adjustments of models.
Such capabilities could revolutionize fields like automotive and aerospace, where real-time feedback loops could significantly enhance safety features.
Conclusion
The practical application of impact analysis using the dynamic finite element method offers profound insights and improvements in various engineering fields.
Despite its challenges, DFEM remains a crucial tool for developing safer, more resilient structures.
As computational capabilities and integration with other technologies advance, the potential of DFEM in impact analysis will continue to grow, opening new possibilities for innovation and safety in engineering designs.
資料ダウンロード
QCD管理受発注クラウド「newji」は、受発注部門で必要なQCD管理全てを備えた、現場特化型兼クラウド型の今世紀最高の受発注管理システムとなります。
ユーザー登録
受発注業務の効率化だけでなく、システムを導入することで、コスト削減や製品・資材のステータス可視化のほか、属人化していた受発注情報の共有化による内部不正防止や統制にも役立ちます。
NEWJI DX
製造業に特化したデジタルトランスフォーメーション(DX)の実現を目指す請負開発型のコンサルティングサービスです。AI、iPaaS、および先端の技術を駆使して、製造プロセスの効率化、業務効率化、チームワーク強化、コスト削減、品質向上を実現します。このサービスは、製造業の課題を深く理解し、それに対する最適なデジタルソリューションを提供することで、企業が持続的な成長とイノベーションを達成できるようサポートします。
製造業ニュース解説
製造業、主に購買・調達部門にお勤めの方々に向けた情報を配信しております。
新任の方やベテランの方、管理職を対象とした幅広いコンテンツをご用意しております。
お問い合わせ
コストダウンが利益に直結する術だと理解していても、なかなか前に進めることができない状況。そんな時は、newjiのコストダウン自動化機能で大きく利益貢献しよう!
(β版非公開)