- お役立ち記事
- Practical Approaches for SMEs to Increase Efficiency in Bending Processes
Practical Approaches for SMEs to Increase Efficiency in Bending Processes
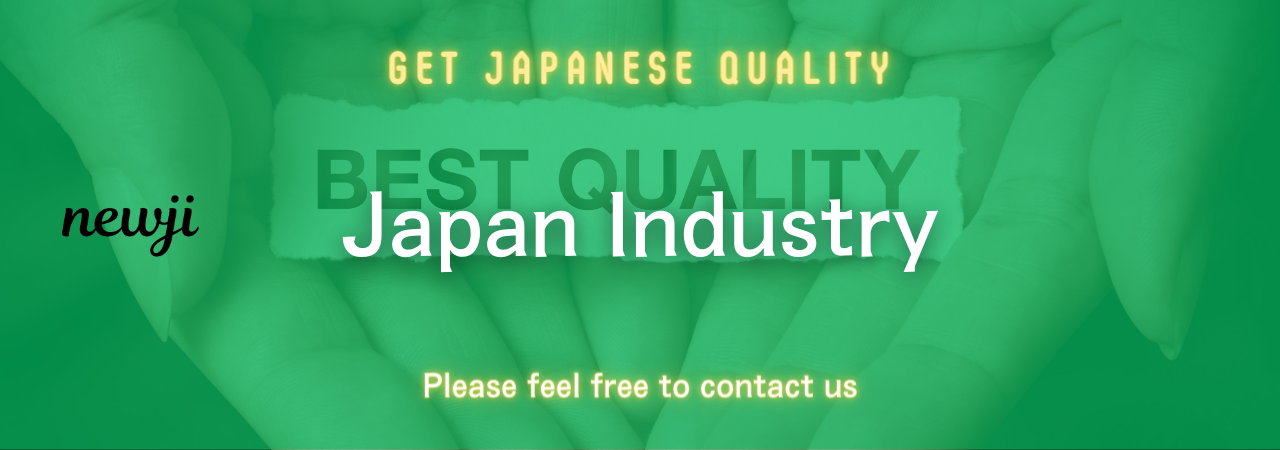
Small and medium-sized enterprises (SMEs) form the backbone of many economies worldwide.
One of the critical areas where these businesses often seek efficiency is in their manufacturing processes, particularly in bending processes.
Improving efficiency in bending operations can enhance productivity, reduce costs, and ultimately boost the bottom line.
This article will discuss practical approaches for SMEs to increase efficiency in bending processes.
From adopting advanced technologies to optimizing workflow, these strategies can make a significant difference.
目次
Understanding Bending Processes
Bending processes are fundamental in many manufacturing sectors.
They involve deforming materials, usually metals, into desired shapes, often for parts in larger assemblies.
There are various types of bending processes, such as air bending, bottoming, and coining, each serving distinct purposes and materials.
Air Bending
Air bending is a widely-used technique where the material is bent by pressing a punch into the material, allowing it to “float” in the air as it bends.
This method provides flexibility, accommodating different tooling needs with minimal adjustments.
Bottoming
In bottoming, the material is pressed into a die to conform to its shape, offering more precision than air bending.
This technique is ideal for high-volume production with consistent results.
Coining
Coining uses extreme pressure to create precise bends, especially for small, intricate designs.
While providing high accuracy, coining can be more time-consuming and requires significant force.
Investing in Advanced Technology
For SMEs, investing in advanced technologies can revolutionize bending processes.
Automation and modern machinery reduce manual errors and increase precision.
Automated Bending Machines
Automated bending machines perform operations with reduced human intervention, ensuring consistent quality.
Although the initial investment may seem substantial, the long-term benefits usually justify the expenditure due to increased throughput and reduced labor costs.
Computer Numerical Control (CNC) Machines
CNC machines offer precision and repeatability, essential for maintaining consistent quality in high-volume production.
By programming these machines, SMEs can produce complex shapes with minimal waste.
Robotics Integration
Integrating robotics into bending processes can further streamline operations.
Robots can handle repetitive tasks, allowing human workers to focus on more skilled activities, enhancing overall productivity.
Streamlining Workflow
Streamlining workflow involves reorganizing processes to eliminate unnecessary steps and improve efficiency.
This can be achieved through the following methods:
Lean Manufacturing Principles
Adopting lean manufacturing principles helps reduce waste and optimize resource use.
Focus on continuous improvement (Kaizen), just-in-time production, and reducing downtime can lead to more efficient bending processes.
Value Stream Mapping
Value stream mapping identifies every step in the manufacturing process, from material sourcing to final product delivery.
By mapping these steps, SMEs can pinpoint inefficiencies and areas for improvement, ensuring that every stage of the bending process adds value.
Effective Training and Skill Development
Even with the best technology and workflows in place, a skilled workforce is crucial for efficiency in bending processes.
Continuous Training
Regular training ensures that workers stay updated with the latest technologies and techniques.
Training programs should cover safety protocols, machine operation, and maintenance practices to minimize downtime and enhance productivity.
Cross-Training
Cross-training employees in multiple skills allows for more flexibility in operations.
Workers can fill in for one another when needed, preventing bottlenecks and maintaining steady production flow.
Implementing Preventive Maintenance
Proper maintenance is essential for keeping machines running smoothly and preventing unexpected breakdowns.
Scheduled Maintenance
Implementing scheduled maintenance programs ensures that machines receive regular check-ups and necessary repairs.
This practice minimizes downtime and prolongs equipment lifespan, contributing to continuous, efficient operations.
Real-Time Monitoring
Using sensors and monitoring systems helps track machine performance in real-time.
Early detection of potential issues allows for timely interventions and reduces the risk of major disruptions.
Material Optimization
Optimizing material usage is another key factor in enhancing bending process efficiency.
Material Selection
Selecting the right material for each bending project can save time and reduce waste.
Consider the material’s properties, such as tensile strength and ductility, to ensure it meets the specific requirements of the bending process.
Nesting Techniques
Nesting techniques involve strategically arranging part shapes on the material sheet to minimize scrap.
Effective nesting software can optimize this layout, ensuring maximum material utilization and reducing costs.
Data-Driven Decision Making
Utilizing data analytics can provide valuable insights into bending process performance.
Performance Metrics
Tracking key performance metrics, such as cycle time, throughput, and scrap rates, helps identify areas for improvement.
Regularly reviewing these metrics enables SMEs to make informed decisions and implement changes that enhance efficiency.
Predictive Analytics
Predictive analytics uses historical data to forecast future performance and potential issues.
Implementing predictive maintenance, for example, can prevent breakdowns and reduce unplanned downtime.
Conclusion
Increasing efficiency in bending processes is crucial for SMEs looking to remain competitive and profitable.
Investing in advanced technologies, streamlining workflows, training employees, maintaining equipment, optimizing materials, and leveraging data analytics are all practical approaches to achieving this goal.
By implementing these strategies, SMEs can enhance their bending operations, reduce costs, and improve overall productivity.
With the right combination of technology, processes, and skilled workforce, SMEs can thrive in today’s demanding manufacturing landscape.
資料ダウンロード
QCD調達購買管理クラウド「newji」は、調達購買部門で必要なQCD管理全てを備えた、現場特化型兼クラウド型の今世紀最高の購買管理システムとなります。
ユーザー登録
調達購買業務の効率化だけでなく、システムを導入することで、コスト削減や製品・資材のステータス可視化のほか、属人化していた購買情報の共有化による内部不正防止や統制にも役立ちます。
NEWJI DX
製造業に特化したデジタルトランスフォーメーション(DX)の実現を目指す請負開発型のコンサルティングサービスです。AI、iPaaS、および先端の技術を駆使して、製造プロセスの効率化、業務効率化、チームワーク強化、コスト削減、品質向上を実現します。このサービスは、製造業の課題を深く理解し、それに対する最適なデジタルソリューションを提供することで、企業が持続的な成長とイノベーションを達成できるようサポートします。
オンライン講座
製造業、主に購買・調達部門にお勤めの方々に向けた情報を配信しております。
新任の方やベテランの方、管理職を対象とした幅広いコンテンツをご用意しております。
お問い合わせ
コストダウンが利益に直結する術だと理解していても、なかなか前に進めることができない状況。そんな時は、newjiのコストダウン自動化機能で大きく利益貢献しよう!
(Β版非公開)