- お役立ち記事
- Practical Approaches to Achieving Zero Contaminants
Practical Approaches to Achieving Zero Contaminants
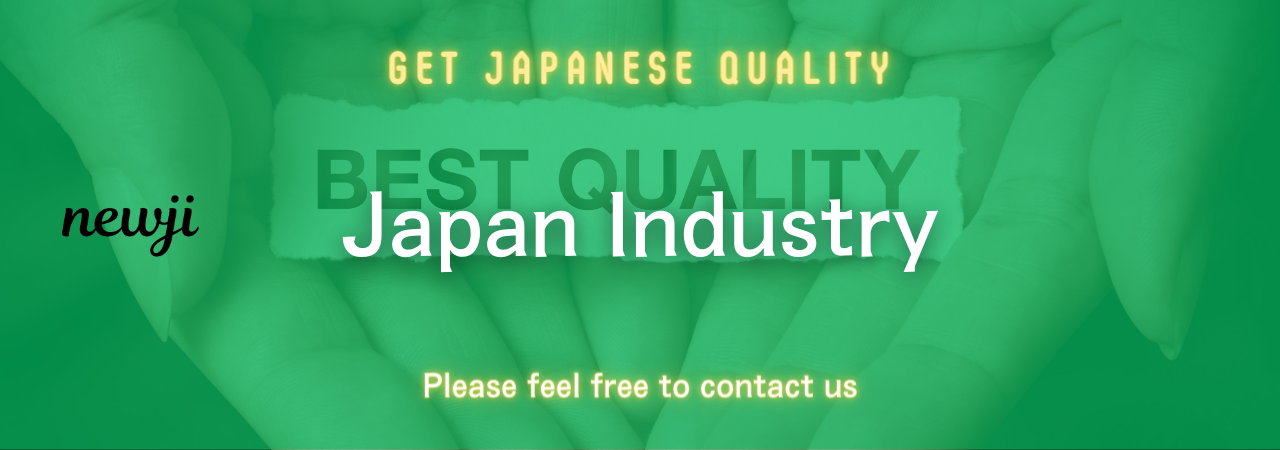
In recent years, ensuring zero contaminants in various environments has become a significant concern.
From industrial settings to food production, the goal is to achieve a contaminant-free state that promises safety and quality.
Contaminants, whether biological, chemical, or physical, can pose serious health and economic risks.
Understanding the approaches to achieving zero contaminants is vital for anyone invested in maintaining hygienic and safe conditions.
目次
Understanding Contaminants
Before diving into practical approaches, it is essential to comprehend what contaminants are.
Contaminants refer to any substance that makes a product or environment impure or unsafe.
They can be of various types:
Biological Contaminants
Biological contaminants include bacteria, viruses, and fungi that can contaminate food, water, and surfaces.
These microorganisms can lead to diseases and spoilage.
Chemical Contaminants
Chemical contaminants are harmful substances like pesticides, heavy metals, and pollutants.
They can enter food and water supplies or be released into the environment through industrial processes.
Physical Contaminants
Physical contaminants are foreign objects like metal shavings, glass pieces, or plastic fragments that can accidentally enter products during production or packaging.
Practical Strategies for Zero Contaminants
Achieving zero contaminants requires a multifaceted approach that includes stringent practices, advanced technology, and continual monitoring.
Implementing Good Manufacturing Practices (GMP)
Good Manufacturing Practices (GMP) are a set of guidelines designed to ensure products are consistently produced and controlled according to quality standards.
Implementing GMP is crucial in preventing contamination in manufacturing processes.
This includes regular equipment maintenance, employee hygiene training, and employing sanitary design in production facilities.
Adopting Hazard Analysis and Critical Control Points (HACCP)
HACCP is a systematic approach to identifying and controlling hazards in food production processes.
It involves assessing potential hazards, determining critical control points, establishing preventive measures, and implementing monitoring procedures.
By adopting HACCP, companies can better manage and eliminate risks associated with contaminants.
Utilizing Advanced Filtration Systems
In industries where clean air and water are essential, advanced filtration systems play a critical role in eliminating contaminants.
For example, HEPA filters in air handling units can trap particles as small as 0.3 microns, effectively reducing airborne contaminants.
Similarly, water filtration systems employing reverse osmosis and UV sterilization can ensure that water is free from pathogens and chemicals.
Embracing Automation and Robotics
Automation and robotics can significantly reduce human error, which is often a significant source of contamination.
Automated systems can perform tasks with high precision, ensuring consistent quality and cleanliness.
Robotics can also handle dangerous or sensitive materials, minimizing the risk of contamination from human interaction.
Regular Cleaning and Sanitation
Maintaining a regular cleaning and sanitation schedule is vital.
Surfaces, equipment, and work areas should be cleaned and sanitized frequently to prevent the buildup of contaminants.
Using appropriate cleaning agents and disinfectants that target specific contaminants can further enhance effectiveness.
Strict Monitoring and Testing
Continual monitoring and testing are necessary to ensure that environments remain contaminant-free.
This includes routine sampling and laboratory analysis to detect any presence of contaminants.
Real-time monitoring systems can provide immediate alerts to any deviations from established safety parameters.
Personal Protective Equipment (PPE) and Hygiene
Using personal protective equipment (PPE) such as gloves, masks, and gowns can prevent the spread of contaminants, especially in sensitive environments like healthcare and food production.
Additionally, promoting good personal hygiene practices among employees, such as regular handwashing and use of sanitizers, can significantly reduce contamination risks.
The Role of Education and Training
Education and training are critical components in the quest for zero contaminants.
Employees should be well-trained in contamination-control protocols and understand the importance of maintaining a contaminant-free environment.
Regular workshops and training sessions can update staff on new techniques and reinforce existing practices.
Innovations in Contaminant Detection
Emerging technologies are continually improving our ability to detect and eliminate contaminants.
For instance, advanced sensors and IoT (Internet of Things) devices can monitor environmental conditions in real-time and provide data for predictive analysis.
Additionally, innovations in pathogen detection technologies, like rapid DNA sequencing, allow for quicker identification and response to biological contaminants.
Collaboration and Compliance
Achieving zero contaminants often requires collaboration across various sectors.
Government agencies, industry bodies, and academic institutions need to work together to establish and enforce stringent regulations.
Compliance with these regulations ensures a standardized approach to contamination control across all levels of production and handling.
Conclusion
Achieving zero contaminants is an ongoing process that demands diligence, innovation, and commitment.
By understanding the types of contaminants and adopting comprehensive strategies to control them, environments can remain safe and clean.
Implementing GMP, HACCP, advanced filtration, automation, regular sanitation, and rigorous training are all essential elements in this endeavor.
With continual monitoring and the adoption of new technologies, the goal of zero contaminants can be met, ensuring a safer and healthier environment for all.
資料ダウンロード
QCD調達購買管理クラウド「newji」は、調達購買部門で必要なQCD管理全てを備えた、現場特化型兼クラウド型の今世紀最高の購買管理システムとなります。
ユーザー登録
調達購買業務の効率化だけでなく、システムを導入することで、コスト削減や製品・資材のステータス可視化のほか、属人化していた購買情報の共有化による内部不正防止や統制にも役立ちます。
NEWJI DX
製造業に特化したデジタルトランスフォーメーション(DX)の実現を目指す請負開発型のコンサルティングサービスです。AI、iPaaS、および先端の技術を駆使して、製造プロセスの効率化、業務効率化、チームワーク強化、コスト削減、品質向上を実現します。このサービスは、製造業の課題を深く理解し、それに対する最適なデジタルソリューションを提供することで、企業が持続的な成長とイノベーションを達成できるようサポートします。
オンライン講座
製造業、主に購買・調達部門にお勤めの方々に向けた情報を配信しております。
新任の方やベテランの方、管理職を対象とした幅広いコンテンツをご用意しております。
お問い合わせ
コストダウンが利益に直結する術だと理解していても、なかなか前に進めることができない状況。そんな時は、newjiのコストダウン自動化機能で大きく利益貢献しよう!
(Β版非公開)