- お役立ち記事
- Practical Approaches to Product Cost Management
Practical Approaches to Product Cost Management
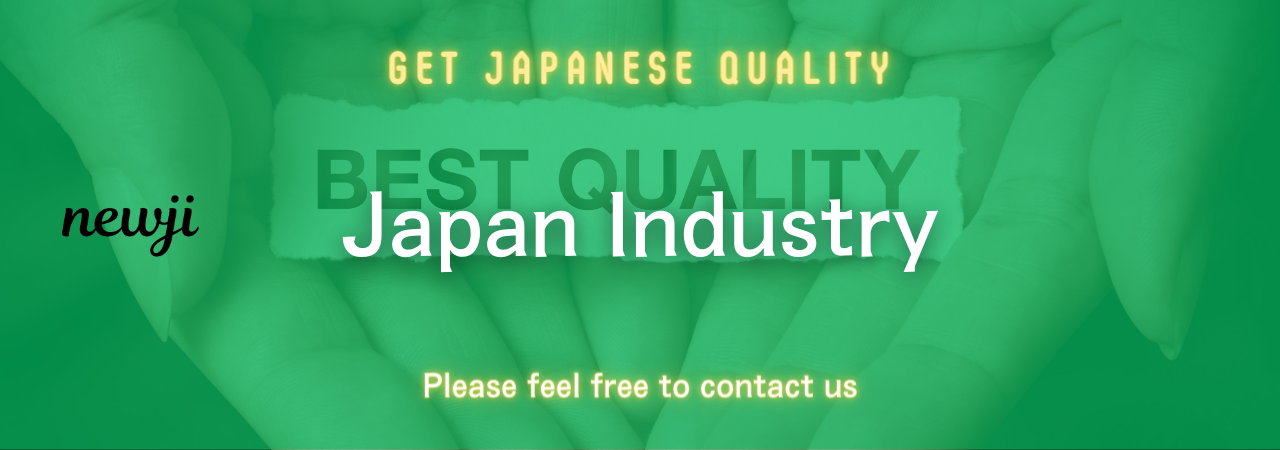
Product cost management is a crucial aspect for any business seeking to enhance profitability and maintain competitiveness.
By effectively controlling product costs, companies can improve their margins, deliver better value to customers, and reinvest savings into growth initiatives.
This article delves into practical approaches to product cost management, providing actionable insights for businesses of all sizes.
目次
Understanding Product Cost Management
Effective product cost management encompasses a series of strategies aimed at minimizing production and operational expenses.
The goal is to achieve cost efficiency without compromising product quality.
It involves a detailed examination of costs associated with the entire lifecycle of a product, from raw materials to distribution.
Key Components of Product Cost Management
Product cost management can be divided into several key components:
1. **Cost Analysis**: The process involves identifying and analyzing all costs related to the production and delivery of a product.
2. **Cost Reduction**: Implementing strategies and practices to reduce unnecessary costs.
3. **Cost Control**: Monitoring and managing expenses to ensure they do not exceed budgeted levels.
4. **Cost Allocation**: Accurately assigning costs to different products, services, or departments to better understand profitability.
Effective Approaches to Product Cost Management
1. Implementing Lean Manufacturing
Lean manufacturing is an approach focused on reducing waste while ensuring quality and efficiency.
By adopting lean principles, businesses can streamline production processes, reduce inventory costs, and eliminate non-value-added activities.
Key elements of lean manufacturing include:
– **Continuous Improvement (Kaizen)**: Encouraging small, incremental changes to enhance productivity and reduce costs.
– **Just-in-Time (JIT) Production**: Producing only what is needed, when it is needed, thereby minimizing inventory costs.
– **Value Stream Mapping**: Analyzing all steps in the production process to identify and eliminate waste.
2. Conducting a Thorough Cost-Benefit Analysis
A cost-benefit analysis helps businesses make informed decisions by comparing the costs and benefits of different actions.
This approach ensures that resources are allocated efficiently and that the most cost-effective strategies are implemented.
Steps to conduct a cost-benefit analysis include:
– Identifying all costs and benefits associated with a decision.
– Quantifying costs and benefits in monetary terms.
– Comparing the total costs and benefits to determine the net gain or loss.
3. Strategic Sourcing and Supplier Negotiation
Effective procurement practices are critical for managing product costs.
Strategic sourcing involves evaluating and selecting suppliers based on their ability to deliver high-quality materials at competitive prices.
Negotiating favorable terms with suppliers can lead to significant cost savings.
Key tactics include:
– Requesting quotes from multiple suppliers to ensure competitive pricing.
– Building long-term relationships with reliable suppliers to secure better rates.
– Identifying opportunities for bulk purchasing to benefit from volume discounts.
4. Utilizing Technology and Automation
Technology and automation play a pivotal role in modern product cost management.
By leveraging advanced software and machinery, businesses can enhance accuracy, reduce labor costs, and increase operational efficiency.
Examples of technology-driven cost management include:
– **Enterprise Resource Planning (ERP) Systems**: Integrating all business processes to provide a unified view of operations, facilitating better cost control.
– **Automation Robotics**: Implementing automated machines to perform repetitive tasks, reducing the need for manual labor.
– **Advanced Data Analytics**: Utilizing data analysis tools to gain insights into cost trends and identify areas for improvement.
5. Focusing on Product Design and Development
The design and development phase significantly impacts the overall cost of a product.
By adopting a cost-conscious approach during this stage, businesses can reduce production expenses and improve profitability.
Effective strategies include:
– **Design for Manufacturability (DFM)**: Designing products in a way that simplifies production processes and lowers costs.
– **Standardization**: Using standard components and materials to benefit from economies of scale.
– **Value Engineering**: Systematically evaluating product functions to identify opportunities for cost reduction without sacrificing quality.
6. Monitoring and Controlling Overhead Costs
Overhead costs, such as utilities, rent, and administrative expenses, can significantly impact overall product costs.
Businesses should implement measures to monitor and control these expenses effectively.
Practical techniques include:
– **Regular Audits**: Conducting periodic reviews of overhead costs to identify inefficiencies and areas for savings.
– **Energy Efficiency**: Investing in energy-efficient equipment and practices to reduce utility costs.
– **Outsourcing Non-Core Activities**: Partnering with third-party providers for tasks like payroll, IT, and maintenance to lower overhead expenses.
Conclusion
Product cost management is an ongoing process that requires a strategic approach and continuous effort.
By implementing these practical approaches, businesses can effectively manage product costs, enhance profitability, and remain competitive in the market.
From lean manufacturing and strategic sourcing to technology utilization and cost control, each strategy plays a vital role in achieving cost efficiency.
Ultimately, the key to successful product cost management lies in a comprehensive understanding of costs and a commitment to continuous improvement.
資料ダウンロード
QCD調達購買管理クラウド「newji」は、調達購買部門で必要なQCD管理全てを備えた、現場特化型兼クラウド型の今世紀最高の購買管理システムとなります。
ユーザー登録
調達購買業務の効率化だけでなく、システムを導入することで、コスト削減や製品・資材のステータス可視化のほか、属人化していた購買情報の共有化による内部不正防止や統制にも役立ちます。
NEWJI DX
製造業に特化したデジタルトランスフォーメーション(DX)の実現を目指す請負開発型のコンサルティングサービスです。AI、iPaaS、および先端の技術を駆使して、製造プロセスの効率化、業務効率化、チームワーク強化、コスト削減、品質向上を実現します。このサービスは、製造業の課題を深く理解し、それに対する最適なデジタルソリューションを提供することで、企業が持続的な成長とイノベーションを達成できるようサポートします。
オンライン講座
製造業、主に購買・調達部門にお勤めの方々に向けた情報を配信しております。
新任の方やベテランの方、管理職を対象とした幅広いコンテンツをご用意しております。
お問い合わせ
コストダウンが利益に直結する術だと理解していても、なかなか前に進めることができない状況。そんな時は、newjiのコストダウン自動化機能で大きく利益貢献しよう!
(Β版非公開)