- お役立ち記事
- Practical design standardization methods and know-how for creating design procedure manuals
月間76,176名の
製造業ご担当者様が閲覧しています*
*2025年3月31日現在のGoogle Analyticsのデータより
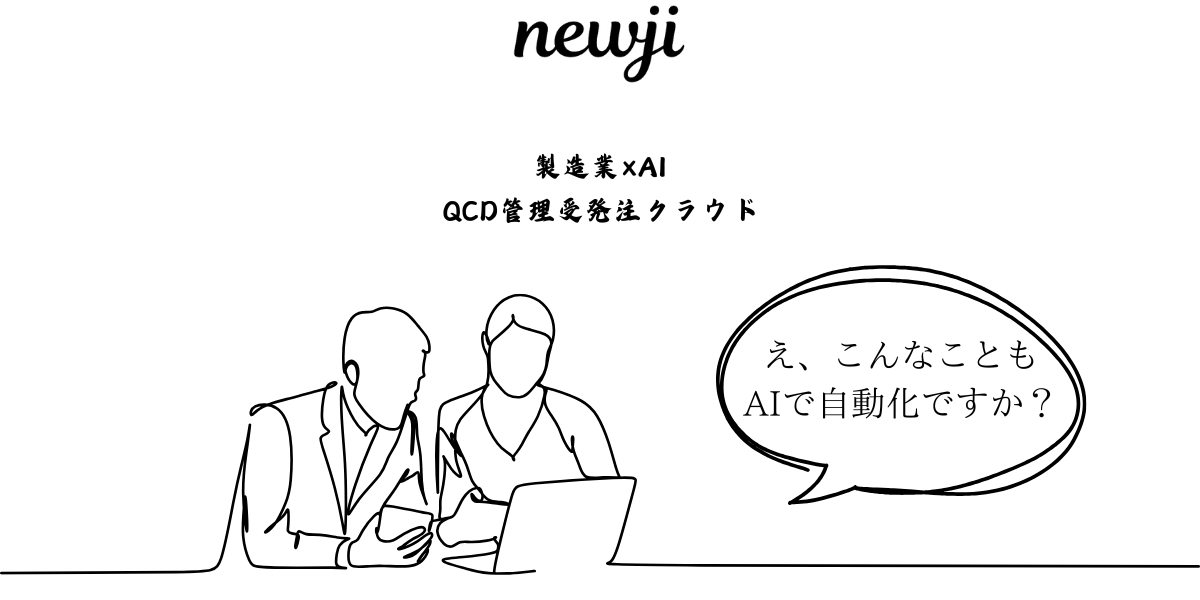
Practical design standardization methods and know-how for creating design procedure manuals
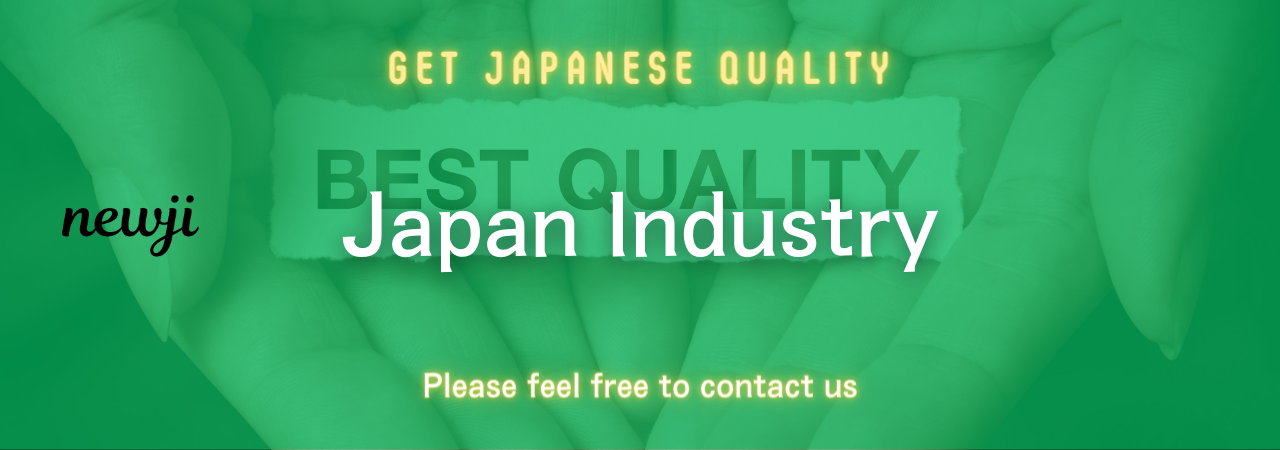
目次
Understanding Design Standardization
Design standardization is a crucial aspect of modern design practices, where uniformity and consistency are key to ensuring quality and efficiency in production.
It involves setting guidelines, creating templates, and streamlining processes to maintain the same quality across different products or services.
By implementing design standards, companies can save time, reduce costs, and improve overall productivity.
Standardization is not only beneficial for the organization but also for the consumers, as it guarantees consistent user experiences across various platforms.
Creating a design procedure manual is a comprehensive approach to standardizing design processes and can be an invaluable tool for any design-oriented company.
Such manuals provide detailed instructions and guidelines for design tasks, aiding in maintaining consistency and quality in the final output.
Benefits of Design Standardization
Implementing design standardization comes with a host of benefits that can significantly enhance the operations of any business.
One of the primary advantages is improved efficiency.
Standardized procedures reduce the probability of errors, rework, and miscommunication, enabling faster turnaround times.
Consistency in design also contributes to brand recognition.
When consumers encounter a product that appears consistent in design and function with previous experiences, it fosters trust and loyalty.
Cost reduction is another significant benefit, as standardization eliminates the need for redundant design efforts and minimizes material wastage.
Moreover, it facilitates easier training and onboarding of new staff members, as standardized procedures are easier to understand and follow.
Steps for Creating a Design Procedure Manual
Crafting a design procedure manual involves several key steps, each critical in ensuring that the final document is practical and comprehensive.
Identify Key Design Processes
Before creating a procedure manual, it is essential to identify the key design processes that require standardization.
Analyze current workflows and pinpoint areas that would benefit most from consistency.
This can include branding guidelines, layout templates, typography rules, color schemes, and more.
Engage With Stakeholders
Collaborating with stakeholders is a vital step in the creation of an effective design procedure manual.
These stakeholders could include designers, project managers, product developers, and even clients.
Their insights and feedback can provide valuable perspectives on what processes need attention and how best to go about standardizing them.
Develop a Clear Structure
The design procedure manual should have a clear and logical structure.
Begin with an introduction that outlines the purpose and scope of the document.
Follow up with sections that define each design process in detail, including objectives, necessary materials, and step-by-step instructions.
Additionally, include visuals and examples to illustrate each point clearly.
Document Procedures in Detail
When documenting procedures, it is essential to provide detailed information that leaves no room for doubt.
This includes specifying software to be used, file formats, naming conventions, and timelines.
By doing so, you create a tool that guides designers through each stage of their tasks effectively, reducing the risk of errors or misinterpretations.
Test and Revise
Once a draft of the design procedure manual is ready, it should be tested under real-world conditions.
Collect feedback from users and revise the document accordingly.
This iterative process will help fine-tune the procedures and ensure that the manual is practical and user-friendly.
Know-How for Effective Design Standardization
Beyond just creating a manual, there are essential know-how and tips that can make design standardization efforts more effective.
Embrace Flexibility
While standardization aims for uniformity, it is important to allow some degree of flexibility to accommodate creative processes and innovation.
Allowing designers to adapt the guidelines to fit unique projects can lead to more innovative solutions.
Continuous Improvement
A successful design standardization process requires continuous updates and improvements.
Regularly review and update the design procedure manual to reflect changes in technology, industry standards, or company goals.
Training and Communication
Provide training for designers on how to use the procedure manual and emphasize its importance.
Foster open communication to encourage feedback and suggestions for improvements.
Regular discussions about design processes can also lead to new insights and innovative approaches.
Measure Success
Implement metrics to measure the success of standardization efforts.
This could include tracking time savings, reduction in errors, or consistency in branding across channels.
Analyzing these metrics can provide valuable data to support the continuation and refinement of design standardization initiatives.
Cultural Benefits of Design Standardization
Design standardization also brings about cultural benefits that resonate throughout an organization.
It creates a shared understanding and language among team members, which boosts collaboration and unity.
When everyone is on the same page concerning design expectations, it minimizes conflict and enhances teamwork.
Moreover, standardized processes empower employees by providing clear expectations and guidelines.
This clarity can lead to increased job satisfaction, as team members have the resources and guidance they need to succeed in their roles.
Conclusion
Design standardization is a powerful strategy that, when executed effectively, brings about numerous advantages.
From enhancing efficiency and reducing costs to improving brand consistency and fostering a unified company culture, the benefits are manifold.
Creating a comprehensive design procedure manual is an integral part of this strategy, along with embracing best practices and adapting to ongoing changes.
By doing so, organizations can ensure that their design processes are as smooth, consistent, and effective as possible.
資料ダウンロード
QCD管理受発注クラウド「newji」は、受発注部門で必要なQCD管理全てを備えた、現場特化型兼クラウド型の今世紀最高の受発注管理システムとなります。
ユーザー登録
受発注業務の効率化だけでなく、システムを導入することで、コスト削減や製品・資材のステータス可視化のほか、属人化していた受発注情報の共有化による内部不正防止や統制にも役立ちます。
NEWJI DX
製造業に特化したデジタルトランスフォーメーション(DX)の実現を目指す請負開発型のコンサルティングサービスです。AI、iPaaS、および先端の技術を駆使して、製造プロセスの効率化、業務効率化、チームワーク強化、コスト削減、品質向上を実現します。このサービスは、製造業の課題を深く理解し、それに対する最適なデジタルソリューションを提供することで、企業が持続的な成長とイノベーションを達成できるようサポートします。
製造業ニュース解説
製造業、主に購買・調達部門にお勤めの方々に向けた情報を配信しております。
新任の方やベテランの方、管理職を対象とした幅広いコンテンツをご用意しております。
お問い合わせ
コストダウンが利益に直結する術だと理解していても、なかなか前に進めることができない状況。そんな時は、newjiのコストダウン自動化機能で大きく利益貢献しよう!
(β版非公開)