- お役立ち記事
- Practical error management course: Root cause analysis of accidents and troubles and application to preventive measures
月間77,185名の
製造業ご担当者様が閲覧しています*
*2025年2月28日現在のGoogle Analyticsのデータより
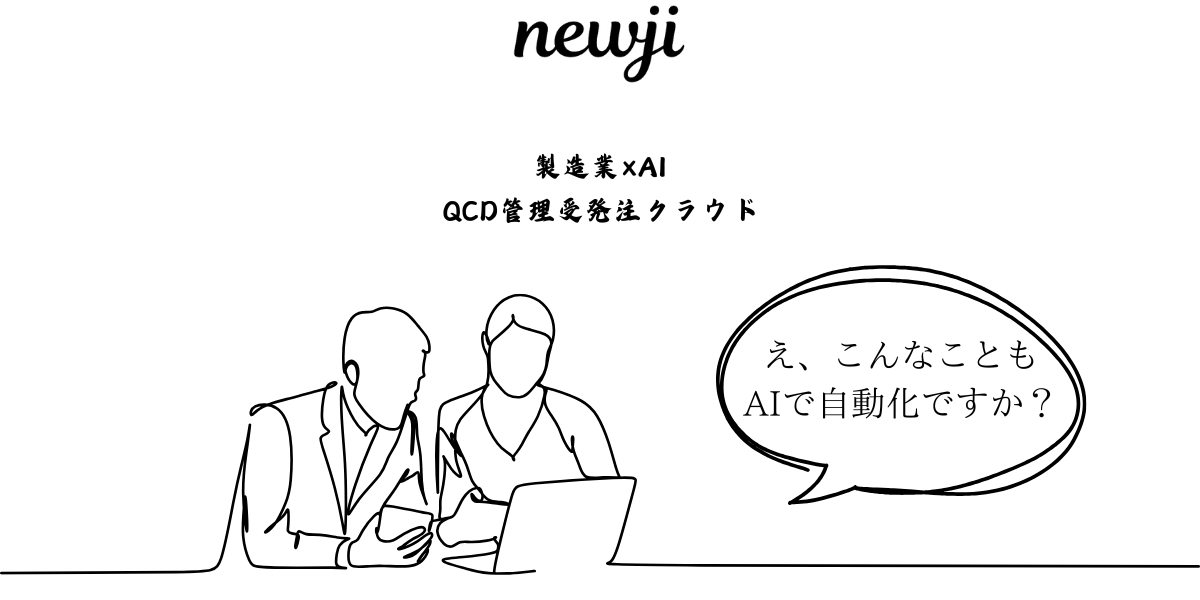
Practical error management course: Root cause analysis of accidents and troubles and application to preventive measures
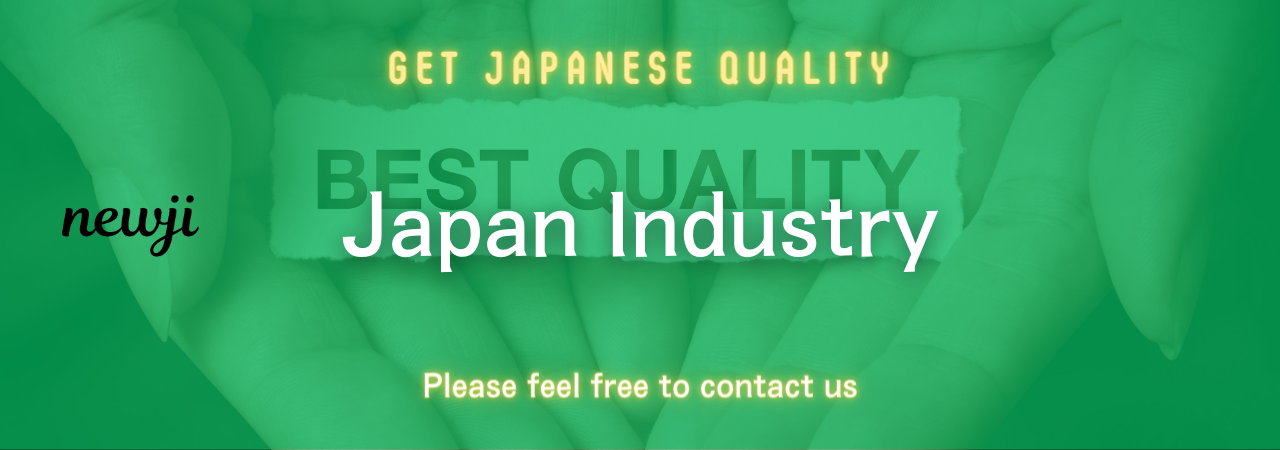
Understanding the importance of error management and learning how to conduct root cause analysis can significantly enhance safety and efficiency in any organization. This specialized field focuses on identifying, understanding, and mitigating the causes of accidents and troubles, thereby preventing future occurrences.
目次
What is Error Management?
Error management refers to the systematic approach of recognizing, identifying, and correcting errors to improve safety and reliability. In various industries, especially those that are high-risk such as aviation, healthcare, and manufacturing, effective error management is crucial.
By understanding the underlying causes of errors or accidents, organizations can develop strategies to minimize the recurrence of such issues. This involves not just fixing the immediate problem but understanding the deeper, systemic issues that contribute to these events.
The Role of Root Cause Analysis
Root cause analysis (RCA) is a key component of error management. It is a method used to determine the fundamental causes of a problem. When correctly applied, RCA helps prevent the recurrence of errors by addressing the root reasons rather than the symptoms.
1. Identifying the Problem
The first step in RCA is to clearly identify the problem. This involves gathering detailed information about the incident, understanding what happened, and documenting the outcomes. Accurate identification is critical as it sets the course for the entire analysis process.
2. Collecting Data
After defining the problem, the next step is data collection. During this phase, information regarding the circumstances that led to the error is gathered. This includes examining the processes involved, interviewing personnel, and reviewing documentation. The goal is to develop a comprehensive understanding of the situation.
3. Determining Possible Causes
Once data is collected, the analysis process begins with identifying all possible causes of the error. This often involves the use of tools such as the “5 Whys” technique, which prompts analysts to ask “why” repeatedly to drill down into the root cause of the problem. Other methods include fishbone diagrams and failure mode and effects analysis (FMEA).
4. Identifying the Root Cause
With potential causes identified, the next step is to pinpoint the root cause. This involves evaluating the evidence and determining which cause, if addressed, will prevent the issue from recurring. This step is critical, as success in solving the problem is greatly dependent on accurately identifying the root cause.
5. Implementing Solutions
Once the root cause is identified, solutions can be implemented. The goal is to address the systemic issues that led to the error. This can involve changes to processes, technologies, or training to ensure that similar problems do not arise in the future. The solutions should be practical and sustainable over the long term.
6. Monitoring and Review
The final step in the RCA process is monitoring the implemented solutions. This ensures that the changes made are effective and that the issue does not recur. Regular reviews and audits of the processes involved can help to ensure continuous improvement and maintain safety standards.
Applying Root Cause Analysis to Preventive Measures
Once root causes are correctly identified and addressed, the insights gained can be applied to develop preventive measures. These measures can proactively manage risks and prevent potential issues before they arise.
Proactive Risk Assessment
Conducting regular risk assessments is crucial. These assessments help identify potential errors or hazards that could lead to accidents. By understanding potential risks, organizations can implement safeguards and mitigate those risks proactively.
Developing a Safety Culture
Beyond technical interventions, building a safety-oriented culture within the organization is crucial. This involves creating an environment where safety and error management are part of the organizational ethos. This includes encouraging open communication about safety concerns and continuously educating employees on best practices.
Continuous Improvement
Organizations should foster an environment of continuous improvement. By regularly updating and reviewing safety protocols and procedures, businesses can maintain high safety standards. Continuous learning from past incidents and near-misses can also inform better preventive measures.
Conclusion
Effective error management, skilled root cause analysis, and comprehensive preventive measures are integral to ensuring safety and reliability within any organization.
These steps not only help solve existing problems but also prevent future incidents, promoting a more efficient and safe operational environment.
By prioritizing these techniques, organizations can adapt, learn, and thrive even in high-risk industries, safeguarding their personnel, assets, and reputation.
資料ダウンロード
QCD管理受発注クラウド「newji」は、受発注部門で必要なQCD管理全てを備えた、現場特化型兼クラウド型の今世紀最高の受発注管理システムとなります。
ユーザー登録
受発注業務の効率化だけでなく、システムを導入することで、コスト削減や製品・資材のステータス可視化のほか、属人化していた受発注情報の共有化による内部不正防止や統制にも役立ちます。
NEWJI DX
製造業に特化したデジタルトランスフォーメーション(DX)の実現を目指す請負開発型のコンサルティングサービスです。AI、iPaaS、および先端の技術を駆使して、製造プロセスの効率化、業務効率化、チームワーク強化、コスト削減、品質向上を実現します。このサービスは、製造業の課題を深く理解し、それに対する最適なデジタルソリューションを提供することで、企業が持続的な成長とイノベーションを達成できるようサポートします。
製造業ニュース解説
製造業、主に購買・調達部門にお勤めの方々に向けた情報を配信しております。
新任の方やベテランの方、管理職を対象とした幅広いコンテンツをご用意しております。
お問い合わせ
コストダウンが利益に直結する術だと理解していても、なかなか前に進めることができない状況。そんな時は、newjiのコストダウン自動化機能で大きく利益貢献しよう!
(β版非公開)